Rezystory nawet jeżeli wyglądają podobnie, mogą się znacznie różnić, na przykład pod względem technologii produkcji, materiałów i konstrukcji. W zależności od tego, jakim procesom poddawany jest materiał rezystancyjny w czasie produkcji podlega on różnym naprężeniom powodującym odkształcenia zmieniające właściwości oporników, głównie ich parametry elektryczne.
Naprężenia występują też w czasie użytkowania rezystorów, głównie wskutek rozszerzania i kurczenia się elementów ich konstrukcji z powodu zmian temperatury otoczenia i w efekcie wydzielania ciepła przy przepływie prądu elektrycznego.
Idealny rezystor powinien być tak skonstruowany, by takie sytuacje zarówno na etapie produkcji, jak i w czasie użytkowania nie wpływały na jego parametry. W praktyce tak się jednak nie dzieje, a niektóre typy są bardziej wytrzymałe od innych. W artykule scharakteryzujemy pod tym względem cztery najpopularniejsze rodzaje rezystorów: precyzyjne drutowe, cienkowarstwowe, grubowarstwowe i foliowe.
Rezystory drutowe
Oporniki tego typu wykonuje się z drutu rezystancyjnego nawijanego na korpus z tworzywa sztucznego lub materiału ceramicznego. Końcówki drutu są punktowo mocowane do zewnętrznych wyprowadzeń rezystora. Dla zabezpieczenia przed wpływem otoczenia drut izoluje się w obudowie. Już sam proces nawijania drutu na korpus powoduje jego trwałe odkształcenia. Dodatkowo przed zamknięciem w obudowie drut jest też odpowiednio skracany i ścierany, w celu uzyskania określonej długości i średnicy, a dzięki temu konkretnej wartości rezystancji.
Obie te operacje powodują defekty drutu zmniejszające dokładność rezystora. Co więcej, nadmiernie zeszlifowany drut łatwiej może się przerwać, gdy w rezystorze wydzieli się zbyt dużo ciepła lub gdy pracuje on w wysokiej temperaturze. Drut może też przez to szybciej pękać także na skutek zużycia. Mimo że proces produkcji rezystorów drutowych nie należy do najbardziej finezyjnych, komponenty te charakteryzują parametry porównywalne, a nawet lepsze niż w przypadku oporników innych typów.
Są to m.in. duża wytrzymałość na wyładowania elektrostatyczne, duża stabilność rezystancji w czasie, a także tolerancja, która może osiągać wartość nawet ±0,005% oraz mała wartość temperaturowego współczynnika rezystancji (TWR). Ten ostatni parametr, który określa, jak zmienia się rezystancja przy zmianie temperatury w przypadku rezystorów drutowych, wynosi typowo od kilku do kilkunastu pmm/ °C, jedynie w przypadku małych wartości rezystancji wzrastając do dwudziestu kilku pmm/°C.
Niestety ze względu na sposób nawinięcia drutu na korpus oporniki tego typu oprócz rezystancji charakteryzują też pasożytnicze parametry: indukcyjność i pojemność elektryczna. W efekcie ich impedancja zmienia się w zakresie większych częstotliwości, zwłaszcza powyżej 50 kHz. Problemem w przypadku rezystorów drutowych są także trudności w zapewnieniu powtarzalności parametrów poszczególnych komponentów.
Ze względu na specyfikę procesu produkcyjnego nie można bowiem zagwarantować, że ich właściwości w określonych warunkach, np. stabilność rezystancji w danym przedziale temperatur, będą zmieniać się tak samo, nawet jeżeli rezystory mają identyczną nominalną rezystancję. Jest to jeszcze mniej pewne w przypadku rezystorów o różnych rezystancjach, bo generalnie im większa jest różnica między wartościami rezystancji oporników, tym większa różnica w zakresie ich konstrukcji, np. pod względem liczby zwojów lub rozmiaru rdzenia.
Rezystory cienkowarstwowe
Rezystory cienkowarstwowe produkuje się, nanosząc cienkie, o grubości kilku mikrometrów, jednolite powłoki rezystancyjne na podłoże ceramiczne lub szklane. Realizuje się to na przykład w procesie naparowywania próżniowego lub napylania. Warstwy są nanoszone w postaci konkretnego wzoru lub powłoki, w której później trawiony jest odpowiedni wzór. W porównaniu na przykład do rezystorów drutowych metodą cienkowarstwową uzyskać można większą wartość rezystancji w przeliczeniu na jednostkę powierzchni.
Rezystory cienkowarstwowe są też tańsze. Dlatego są one optymalnym rozwiązaniem, gdy priorytetem nie jest dokładność, a ważniejszy jest mały rozmiar i niska cena. Z drugiej strony ze względu na specyfikę tej technologii charakteryzuje je duży rozrzut parametrów, bo w zależności od grubości powłoki oporniki te mogą być mniej lub bardziej wytrzymałe oraz starzeć się wolniej lub szybciej.
Na przykład w przypadku dużych rezystancji, które wymagają wytworzenia bardzo cienkich warstw rezystancyjnych, problemem staje się zapewnienie ich jednorodności, a zwłaszcza ograniczenie powstawania defektów, przerw i pęcherzyków gazów w sieci krystalicznej. Ważne jest również dokładne zabezpieczanie tych warstw przed wpływem otoczenia, a zwłaszcza wilgocią i zanieczyszczeniami osadzającymi się w sieci krystalicznej. Cienkie warstwy są też bardziej podatne na utlenianie oraz wrażliwsze na wyładowania elektrostatyczne.
Rezystory grubowarstwowe
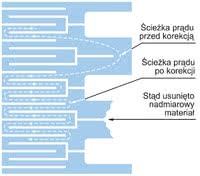
Rys. 2. By uzyskać dokładną wartość rezystancji ze struktury opornika foliowego usuwa się laserem odcinki materiału zwierające ścieżki
Rezystory grubowarstwowe wykonuje się, nanosząc pasty rezystywne stanowiące połączenie materiału ceramicznego z drobinami metalu na podłoże ceramiczne w procesie sitodruku. Tak przygotowane powłoki następnie utwardza się, spiekając je jednocześnie z podłożem. Komponenty konstruowane w ten sposób są wytrzymałe, np. w porównaniu do rezystorów cienkowarstwowych są też odporniejsze na wpływ wilgoci. Jest to również jeden z najtańszych typów obecnie dostępnych rezystorów.
W porównaniu do najczęściej z nimi porównywanych oporników cienkowarstwowych rezystory grubowarstwowe dostępne są w większym zakresie rezystancji. Niestety jednocześnie charakteryzuje je stosunkowo mała stabilność rezystancji w czasie oraz przy zmianie temperatury w porównaniu do rezystorów cienkowarstwowych, foliowych i drutowych, a także duże szumy.
Wadą oporników grubowarstwowych jest też to, że nie są dostępne w małych tolerancjach (standardowe tolerancje rezystorów tego typu do 1% i 5%). Charakteryzuje je też stosunkowo duża wartość współczynnika TWR, typowo wynosząca od 50 ppm/°C do nawet 400ppm/°C.
Rezystory foliowe
Rezystory tego typu wykonuje się, nanosząc folię ze stopu Ni/Cr z domieszkami na podłoże ceramiczne (rys. 1). Następnie wzór ścieżek rezystancyjnych jest wycinany w procesie fotolitografii, dzięki czemu unika się naprężeń mechanicznych. By uzyskać dokładną wartość rezystancji, strukturę później koryguje się laserowo, usuwając odcinki materiału zwierające ścieżki (rys. 2).
Dzięki temu, że materiał rezystancyjny nie jest poddawany mechanicznej obróbce w takim stopniu jak np. w przypadku rezystorów drutowych, oporniki foliowe w czasie produkcji zachowują wszystkie swoje początkowe parametry elektryczne i mechaniczne.
W efekcie otrzymuje się rezystory, które charakteryzuje mała wartość współczynnika TWR, duża stabilność rezystancji, brak indukcyjności pasożytniczej, duża odporność na wyładowania elektrostatyczne, mała wartość pojemności elektrycznej oraz małe szumy. W ramach podsumowania w tabeli 1 przestawiono porównanie wybranych parametrów wszystkich omówionych technologii rezystorów.
Podsumowanie
Wybierając konkretny typ opornika, warto pamiętać, że nie zawsze wykorzystanie rezystorów o najwyższych parametrach jest opłacalne, na przykład gdy bez strat dla jakości całego projektu można je zastąpić rezystorami o nieco słabszej specyfikacji. Warto to rozważyć, zwłaszcza jeżeli opracowujemy projekt urządzenia elektroniki użytkowej.
Zawyżając koszt z powodu zbyt drogich komponentów występujących w urządzeniu bardzo licznie, można osiągnąć efekt odwrotny od zamierzonego, bo w rezultacie nasz produkt nie zyska popularności na rynku. Z drugiej strony w przypadku obwodów, w których jeden lub kilka oporników powinno charakteryzować się większą precyzją, tańszym rozwiązaniem może być właśnie zastosowanie takiego komponentu niż na przykład skonstruowanie dodatkowego obwodu kompensującego.
Monika Jaworowska