Obwody drukowane w branży motoryzacyjnej - wymagania, normy jakości, problemy przy wysokich temperaturach oraz zalecenia
| Prezentacje firmowe ArtykułyW ostatnich latach liczba urządzeń elektronicznych w pojazdach mechanicznych znacząco wzrosła. Dotyczy to niemal każdej części pojazdów, od udoskonalenia zwykłych części mechanicznych w napędach, poprzez inteligentną aparaturę dostarczającą wszelkiego rodzaju informacji, systemy bezpieczeństwa, po zaawansowane urządzenia sterujące. Już teraz szacuje się, że wartość elektroniki stanowi ok. 30% całkowitej wartości pojazdu.
Podstawą każdego układu elektronicznego zamontowanego w pojeździe są obwody drukowane, przy czym są też najmniej ustandaryzowaną jego częścią.
Poza koniecznością dostosowania ich do wymogów projektu, płytki PCB muszą spełniać szereg wymagań dotyczących niezawodności, wytrzymałości mechanicznej, wytrzymałości na wysokie temperatury (płytki w częściach silnika lub skrzyni biegów muszą wytrzymać temperatury powyżej 150°C), kompatybilności elektromagnetycznej czy też takiej kwestii jak nieszkodliwość dla środowiska naturalnego. Nie każdy producent obwodów drukowanych jest w stanie spełnić zaostrzone wymogi stawiane przez branżę motoryzacyjną.
Wymagania i normy jakości
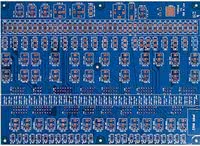
Fot. 2. Przykładowa płytka dla branży motoryzacyjnej: materiał: FR4 Tg170°C, grubość: 3,2 mm, liczba warstw 8, grubość miedzi: 105 μm dla warstw wewn. i zewn, wykończenie: cyna chemiczna
Wysokie wymagania branży motoryzacyjnej wymusiły stworzenie szeregu norm celem lepszej kontroli procesów produkcyjnych i testowania gotowych wyrobów. Jednym z ważniejszych dokumentów jest specyfikacja techniczna ISO/TS 16949. Łączy w sobie wiele międzynarodowych standardów i została stworzona na podstawie normy jakościowej ISO:9001, wzbogacając ją o wymagania techniczne dla branży motoryzacyjnej. Zawarte są w niej wytyczne dotyczące takich obszarów jak: planowanie jakości, dokumentacja techniczna, audyty, analiza systemów pomiarowych, zakupy czy badanie wyrobu niespełniającego wymagań.
System zarządzania jakością według ISO/ TS 16949 nie jest obligatoryjny, jednak staje się niezbędny dla tych przedsiębiorstw przemysłu samochodowego, które stawiają sobie za cel zwiększenie konkurencyjności na rynku zarówno krajowym, jak i zagranicznym.
Wdrożony system przynosi wiele korzyści, tj. elastyczne dopasowanie do wymagań koncernów branży motoryzacyjnej, zredukowanie strat w łańcuchu dostaw, zmniejszenie kosztów ponoszonych z tytułu reklamacji konsumenckich oraz awarii, skuteczne identyfikowanie produktów/usług niezgodnych oraz możliwość podjęcia szybkich procesów naprawczych.
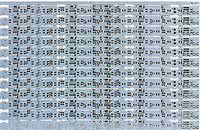
Fot. 3. Przykładowa płytka dla branży motoryzacyjnej do aplikacji LED: materiał: FR-4, grubość: 1,6 mm, liczba warstw: 4, grubość miedzi: 35 μm, wykończenie: HAL PbF
Producentom nie udało się uzyskać zgodności co do wielu punktów normy TS. Tam gdzie było to możliwe, wymagania zostały precyzyjnie sformułowane. W innych punktach norma odwołuje się do wymagań klienta. Organizacja wdrażająca ISO/TS 16949:2009 musi być świadoma faktu, że klient może domagać się spełnienia wymagań dodatkowych.
Dla obwodów drukowanych stworzono szereg norm IPC:
- IPC-A-600 - dopuszczalność obwodów drukowanych,
- IPC-4101 - specyfikacja dla materiałów bazowych obwodów sztywnych i wielowarstwowych,
- IPC-2221 - ogólne standardy dla obwodów drukowanych,
- IPC-2222 - standardy projektowania dla obwodów sztywnych,
- IPC-TM-650 - testowanie obwodów drukowanych.
Na podstawie powyższych norm możliwe jest zaprojektowanie i stworzenie płytek spełniających wysokie wymagania branży motoryzacyjnej, aczkolwiek niezbędne może być wdrożenie systemu ISO/TS 16949.
Problemy z PCB przy wysokich temperaturach
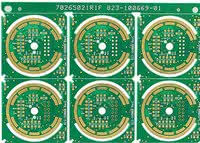
Fot. 4. Przykładowa płytka systemu zasilania szyberdachu: materiał: CEM-3 CTI (600 V), grubość: 1,6 mm, liczba warstw: 2, grubość miedzi: 35 μm, wykończenie: złoto chemiczne 3u
Jak wspomniano wyżej, płytki PCB w urządzeniach pracujących w pojazdach mechanicznych narażone są na działanie wysokich temperatur. Pod wpływem wysokiej temperatury laminat zmienia swój stan struktury ze szklistego (twardego) do plastycznego (miękkiego), przy równoczesnym gwałtownym wzroście jego rozszerzalności w kierunku osi Z.
Temperaturę tę określa się jako temperaturę zeszklenia TG, natomiast rozszerzalność termiczna laminatu określana jest przez współczynnik CTE (Coefficient of Thermal Expansion). Rozszerzanie się laminatu w kierunku osi Z powoduje naprężenia przewodnika w przelotkach, co skutkuje tzw. zjawiskiem podnoszenia padów oraz pękaniem przelotek na krawędziach lub na ściankach otworów.
W wysokich temperaturach może nastąpić rozkład chemiczny substancji, z których składają się obwody. Parametrem określającym taką sytuację jest temperatura rozkładu TD, przy której laminat traci 5% swojej wagi bazowej.
Przy wystawieniu laminatu na ciągłe działanie wysokiej temperatury może on się rozwarstwiać. Do dokładnego określenia tej sytuacji stosuje się wskaźniki T260/T288, czyli czas do delaminacji po wystawieniu na temperaturę odpowiednio 260°C (min. 60 minut) oraz 288°C (min. 30 minut).
Zalecenia przy produkcji płytek dla branży motoryzacyjnej
- wszystkie ścieżki powinny znajdować się na tej samej warstwie,
- ścieżki niezwiązane z urządzeniami wejścia/wyjścia nie powinny znajdować się pomiędzy złączami tych portów i urządzeniami wysyłającymi i odbierającymi korzystającymi z tych złączy,
- sieci ładowane pojemnościowo powinny mieć całkowitą impedancję źródła większą lub równą 1 impedancji charakterystycznej linii,
- do izolacji sieci szybkich od sieci portów wejść/wyjść powinno się stosować ścieżki ochronne,
- sieci ochronne powinny być połączone z uziemieniem poprzez przelotki zlokalizowane w odległości mniej niż 1 długości fali dla najwyższych częstotliwości,
- wszelkie ścieżki zasilające i uziemiające powinny być przynajmniej trzykrotnie szersze niż nominalne ścieżki sygnałowe (nie dotyczy to ścieżek ochronnych),
- kluczowe sieci połączeń powinny znajdować się w odległości przynajmniej dwukrotnej szerokości ścieżki od krawędzi płytki,
- długość ścieżek w sieciach o wysokiej częstotliwości powinny zostać zminimalizowane,
- liczba przelotek w sieciach o wysokiej częstotliwości powinna zostać zminimalizowana,
- należy stosować laminaty o wysokim współczynniku zeszklenia Tg (dla bardzo wysokich temperatur laminaty CEM-3 lub ceramiczne).
Podsumowanie
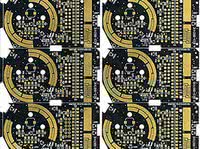
Fot. 5. Aplikacja przełącznika przednich świateł: materiał: CEM-3 CTI (600 V), grubość: 1,6 mm, liczba warstw: 2, grubość miedzi: 35 μm, wykończenie: złoto chemiczne 3u
Zaprojektowanie i wyprodukowanie obwodów drukowanych dla branży motoryzacyjnej niesie ze sobą wiele trudności. Dobór odpowiedniego materiału bazowego oraz prawidłowe rozłożenie elementów i ścieżek na laminacie wymaga sporego doświadczenia, na co należy zwrócić szczególną uwagę podczas wybierania dostawcy płytek.
Produkcja obwodów spełniających wysokie wymagania klienta powinna odbywać się w zgodzie z normami jakościowymi ISO oraz IPC. Dlatego też nie każdy producent może dostarczać swoje wyroby do branży motoryzacyjnej, a jedynie ci, którzy utrzymują w swej działalności bardzo wysokie standardy.
W celu uzyskania dalszych informacji zapraszamy do kontaktu. Posiadamy wieloletnie doświadczenie w dostarczaniu obwodów drukowanych dla branży motoryzacyjnej i innych
Karol Liguz
Elhurt
www.elhurt.com.pl