Projektowanie interfejsów użytkownika z sensorami pojemnościowymi
| TechnikaInterfejsy użytkownika z czujnikami pojemnościowymi są coraz częściej montowane, już nie tylko w elektronice użytkowej i sprzęcie AGD, ale również m.in. w urządzeniach pomiarowych oraz medycznych. Dzięki wyeliminowaniu podzespołów mechanicznych charakteryzuje je niezawodność oraz długa żywotność. Ponadto uatrakcyjniają one wygląd urządzenia oraz upraszczają jego obsługę.
Projektowanie przycisków
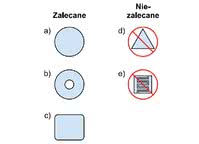
Rys. 5. Wybór kształtu sensora dotykowego nie jest wyłącznie kwestią estetyki. Możliwe rozwiązania to: a) przycisk okrągły, b) przycisk z otworem na diodę w środku c) przycisk z zaokrąglonymi rogami, d) przycisk, którego brzegi tworzą kąty mniejsze niż 90°, e) struktura grzebieniowa
Najpopularniejsze są przyciski okrągłe lub kwadratowe. Szczególnie polecane są zwłaszcza te pierwsze, ponieważ unikać należy ostrych rogów. Ze względu na ich większą czułość charakterystyka przetwarzania sensora nie będzie bowiem liniowa. Z tego powodu aby ograniczyć emisję zaburzeń elektromagnetycznych, narożniki takie należy zaokrąglać. Na rysunku 5 przedstawiono przykłady zalecanych i niepolecanych kształtów przycisków.
Aby uzyskać jak największy stosunek sygnału do szumu, pojemność CF powinna mieć możliwie największą wartość. Wpływ ma na to pole powierzchni sensora. Im jest ono większe, tym większa jest wartość CF.
Pamiętać przy tym należy, że zwiększenie tego pierwszego powyżej pola powierzchni palca przeciętnego człowieka nie przyniesie żadnego efektu. Ponadto ponieważ wpływ na CF ma także m.in. grubość warstwy ochronnej oraz użyte materiały, jej wartość mieści się z reguły w zakresie od 0,1 pF do 1 pF. Zależność między pojemnością CF a średnicą przycisku oraz grubością warstwy ochronnej przedstawiono na rysunku 6.
Slidery
Często wykorzystywanym typem przycisków są również slidery liniowe (rys. 7). Przykładem ich zastosowania jest regulacja głośności lub jasności wyświetlacza. W praktyce taki przycisk stanowi zestaw wielu, niezależnych sensorów umieszczonych w swoim bezpośrednim sąsiedztwie.
Gdy użytkownik dotyka jednego z czujników, jednocześnie aktywowane są również sensory po obu jego stronach. Za aktualną pozycję slidera uznawany jest wówczas środkowy spośród wszystkich wybranych przycisków. Aby można było zrealizować odczyt wskazania użytkownika w ten sposób, sąsiednie czujniki powinny być odpowiednio wąskie.
Dlatego aby uzyskać wymaganą długość slidera, trzeba wykorzystać znaczną liczbę pojedynczych czujników. Sposobem na jej zmniejszenie jest ułożenie sensorów we wzór jak na rysunku 7b. Zaletą tego rozwiązania jest możliwość wykorzystania większych segmentów, a jednocześnie dotknięcie jednego z nich nadal będzie aktywować dwa sąsiednie.
Podobną funkcję spełniają slidery koliste. Najważniejszą różnicą między przyciskami obu tych typów oprócz kształtu jest konieczność implementacji innego algorytmu obliczeniowego w kontrolerze slidera okrągłego. Wynika to stąd, że w tych przyciskach nie jest wyróżniony punkt początkowy ani końcowy.
Czujniki zbliżeniowe
Czujniki pojemnościowe są również używane do budowy sensorów zbliżeniowych. Przykładem ich zastosowania jest podświetlanie przycisków interfejsu w momencie, gdy użytkownik zbliży dłoń do urządzenia. Aby oszczędzić energię w urządzeniach zasilanych bateryjnie, takie rozwiązanie można też wykorzystywać do aktywacji czujników, całkowicie wyłączanych przy braku aktywności użytkowników.
Innym przykładem jest blokowanie przycisków klawiatury telefonu podczas rozmowy, gdy słuchawka przykładana jest do ucha. Pozwala to uniknąć ich przypadkowego wybrania. Przyciski są w takim wypadku odblokowywane, gdy tylko telefon znajdzie się w odpowiedniej odległości od twarzy.
W wypadku czujników zbliżeniowych bezpośredni kontakt między palcem a powierzchnią sensora nie jest wymagany, ponieważ charakteryzuje je znacznie większa czułość niż przyciski dotykowe. Przykład realizacji takiego czujnika z wykorzystaniem ścieżki PCB poprowadzonej wokół przycisków interfejsu przedstawiono na rysunku 8a.
Aby uzyskać większy zasięg detekcji ruchu, pole powierzchni pętli tworzonej przez ścieżkę powinno być jak największe. Równocześnie im ścieżka jest dłuższa, tym większa jest pojemność CP sensora. W rezultacie wymagany jest dłuższy czas skanowania, co z kolei zwiększa pobór mocy i wydłuża czas reakcji. Aby zmniejszyć CP można wykorzystać elektrodę ekranującą jak na rysunku 8b.
Projektowanie PCB
Projektując PCB, należy dopilnować, aby równolegle do ścieżek sensorów nie były prowadzone ścieżki sygnałowe. Zaburzenia emitowane przez te ostatnie będą bowiem zakłócać sygnał pomiarowy z czujników. Można tego uniknąć na kilka sposobów.
W wypadku płytek wielowarstwowych na jednej z warstw można rozmieścić wyłącznie ścieżki sensorów, a na pozostałych poprowadzić inne. Dobrze, jeżeli warstwy te będą oddzielone płaszczyzną masy albo zasilania. Takie rozplanowanie będzie łatwiejsze, jeżeli komponenty zostaną pogrupowane w taki sposób, aby czujniki były podłączone do zacisków po przeciwnej stronie mikrokontrolera, niż inne elementy (na przykład sygnalizacyjne diody LED).
Wówczas uzyska się też odpowiednio duże odległości między torami sygnałowymi czujników a pozostałymi. Jeżeli nie można ani wykorzystać PCB o liczbie warstw większej niż dwie, ani pogrupować komponentów obwodu, należy ekranować ścieżki czujników ścieżkami masy. W ostateczności można również poprowadzić ścieżki sygnałowe prostopadle do tych z sygnałem pomiarowym.
Masa
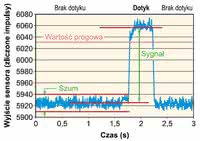
Rys. 9. Wartość progowa sygnału wyjściowego układu pomiarowego powinna wynosić co najmniej 65% - 80% sygnału generowanego podczas dotknięcia czujnika w kontrolowanych warunkach
Kilka zasad projektowych dotyczy również realizacji płaszczyzny masy. Pamiętać należy o tym, że zwiększa ona pojemność CP sensora, co nie jest pożądane. Można ten wpływ zmniejszyć, wykonując masę w formie siatki. Efektem ubocznym takiego rozwiązania jest mniejsza skuteczność ekranowania.
Ważną kwestią jest również odległość przycisk-masa. Przyjmuje się, że w wypadku zastosowania akrylowej warstwy ochronnej odstęp ten powinien być równy grubości tej powłoki, mieszcząc się równocześnie w przedziale od 0,5 do 2 mm. Dopilnować należy również, aby masa wokół sensora była połączona z masą mikrokontrolera. Dzięki temu unika się powstania pętli prądowych, które negatywnie wpływają na kompatybilność elektromagnetyczną urządzenia.
Parametry pracy
To, czy projektowany interfejs będzie działał szybko, poprawnie oraz niezawodnie w różnych warunkach otoczenia, zależy przede wszystkim od doboru trzech parametrów: stosunku sygnału do szumu, czasu skanowania oraz wartości progowej zmiany pojemności, przekroczenie której jest uznawane za potwierdzenie dotknięcia czujnika.
Przy określaniu optymalnej wartości SNR za sygnał uznać należy sygnał wyjściowy układu pomiarowego w momencie dotknięcia sensora. Szum to z kolei wartość zmian sygnału wyjściowego układu pomiarowego, które występują samoistnie. Przyjmuje się, że minimalna zalecana wartość SNR powinna wynosić 5:1. Z kolei im krótszy jest czas skanowania, tym mniejszy SNR.
Niestety, jeżeli będzie on zbyt długi, wydłuży się czas reakcji interfejsu na dotyk, wzrośnie także pobór mocy. Wartość progowa zmiany pojemności powinna natomiast mieścić się w przedziale od 65-80% wartości zmierzonej w czasie dotknięcia czujnika podczas testów (rys. 9).
Kolejne etapy wyznaczania opisanych parametrów przedstawiono na schemacie blokowym na rysunku 10. Wynika z niego, że jest to proces czasochłonny i pracochłonny, którego kolejne kroki trzeba wielokrotnie powtarzać, zwłaszcza gdy wprowadzane są jakiekolwiek zmiany, przykładowo w projekcie PCB.
Dostrajanie
Ponadto w czasie produkcji oraz eksploatacji różne czynniki mogą powodować, że zmieni się m.in. pojemność sensora. W rezultacie parametry określone na etapie projektu w gotowym produkcie nie będą już optymalne. Największy wpływ na to wywierają: zmiana typu lub producenta laminatu PCB, zmiany w procesie produkcyjnym, zmiana grubości warstwy ochronnej lub typu materiału, z jakiego ją wykonano oraz warunki otoczenia, głównie wahania temperatury oraz wilgotności.
Dlatego dobrze, jeżeli układ nadzorujący pracę interfejsu potrafi w miarę potrzeby skorygować kluczowe parametry w czasie jego użytkowania, tak by skompensować wpływ wymienionych czynników. Przykładowo po włączeniu zasilania częstotliwość przełączania w układzie z rysunku 4a powinna być dostosowana do aktualnej pojemności sensora - jeżeli ta ostatnia wzrosła, parametr ten należy zmniejszyć.
Z kolei w czasie pracy regulacji wymagają zwykle: czas skanowania oraz wartość progowa pojemności. Tę ostatnią należy stale aktualizować w zależności od szumów otoczenia, które są czynnikiem zmiennym oraz całkowicie nieprzewidywalnym.
Monika Jaworowska