Wydaje się intuicyjne, że wszystkie nadrukowane punkty poprzez szablon będą mieć taką samą wysokość, która jest w przybliżeniu równa grubości szablonu. W rzeczywistości kształt otworu wpływa na wysokość kropli kleju, która może być powyżej lub poniżej grubości szablonu (rys. 1). Zjawisko nadruku punktów kleju o różnych wysokościach szablonem o jednakowej grubości jest kluczem do zrozumienia procesu nadruku kleju.
Zjawisko to występuje, ponieważ w przeciwieństwie do pasty, klej nie jest całkowicie uwalniany z otworów szablonu. W większości przypadków więcej kleju pozostaje w otworze szablonu niż na powierzchni płytki. Punkty kleju mniejsze niż grubość szablonu powstają na skutek wykonania zbyt małych otworów w szablonie. Jeżeli powierzchnia wewnętrznej ścianki otworu jest większa od powierzchni podłoża, to tylko niewielka część kleju zostanie na podłożu, podczas gdy reszta pozostanie w otworze szablonu (rys. 2).
Kształt takich punktów kleju jest zbliżony do tych, jakie uzyskujemy z dyspensera. Wraz ze wzrostem średnicy otworu, punkty kleju stają się coraz szersze i wyższe, aż ostatecznie przekraczają grubość szablonu. Najwyższe punkty kleju uzyskujemy z otworów, w których stosunek powierzchni otworu do powierzchni podłoża wynosi 1:1. Jeśli powierzchnia podłoża jest znacznie większa niż otworu, to otrzymane punkty kleju będą stosunkowo płaskie, a ich wysokość będzie w przybliżeniu równa grubości szablonu.
Wysokość punktu kleju jest tylko jednym z elementów procesu nakładania kleju, który wpływa na poprawność nanoszenia kleju. Powodzenie procesu nadruku uzależnione jest również od własności kleju, prawidłowo zaprojektowanego szablonu i odpowiedniej drukarki z możliwością separacji pionowej płytki od szablonu (najlepiej z regulacją prędkości) oraz z możliwością ustalenia przerwy pomiędzy płytką a szablonem.
Projektowanie szablonu
Stal nierdzewna jest jednym z najpowszechniej stosowanych materiałów na szablony przeznaczone do kleju. Grubość takich szablonów wynosi od 150 do 1000 μm w zależności od elementów, które mają być położone. Kształt, wielkość i liczba otworów w szablonie przeznaczonym do nakładania kleju jest uzależniona od zastosowanych komponentów. Dla elementów SMD w obudowach typu RC najczęściej wykorzystuje się dwa otwory w kształcie okręgu, rzadziej jeden w kształcie wydłużonej elipsy (rys. 3).
Pojedyncze punkty kleju umieszczamy dla elementów o wymiarach obudowy 0402 i mniejszych. Dla elementów o wymiarach obudowy 0603 i większych stosuje się dwa punkty lub elipsę. Dla elementów w obudowach typu SOT wykonuje się zazwyczaj tylko dwa otwory w kształcie okręgu. Powszechność stosowania dwóch okrągłych otworów wynika z faktu, że przede wszystkim mamy możliwość wpływania na wysokość punktu kleju poprzez dobór odpowiedniej średnicy otworu szablonu.
Równocześnie im większa jest masa komponentu, tym większa powinna być powierzchnia pokryta klejem, ponieważ siła przylegania kleju jest wprost proporcjonalna do jego powierzchni. Dodatkowo punkty kleju nie mogą być za duże, żeby nie zalewały pól lutowniczych. Dla elementów SMD w obudowach typu "SO", w których odległość między obudową układu a płytką jest mniejsza od 0,2mm, stosujemy otwory umieszczone w rzędach (rys. 4). Dla układów o szerszej obudowie np. SOIC używamy otworów w kilku rzędach.
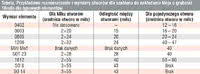
Tabela. Przykładowe rozmieszczenie i wymiary otworów dla szablonu do nakładania kleju o grubości 10mils dla typowych elementów
Wyjątkiem jest tylko układ SO4, dla którego otwory pod klej rozmieszone powinny być na kształcie rombu (rys. 4). W przypadku kiedy odległość między obudową układu a płytką jest większa lub równa 0,2mm, stosujemy otwory w kształcie koniczyny (rys. 5), co pozwala na uzyskanie wyższej kropli kleju. Dla elementów SMD w obudowach typu "QFP" używamy otwory umieszczone na przekątnych układu (rys. 6), a dla elementów w obudowach typu "melf" stosujemy dwa otwory przesunięte względem osi elementu (rys. 7).
Takie rozmieszczenie otworów przede wszystkim zapobiega przesunięciu się elementu podczas montażu. Optymalne wymiary oraz położenie otworów zostały zdefiniowane w normie IPC-7525. Otwory na klej powinny być umieszczone na środku pomiędzy polami lutowniczymi. Szerokość otworu (średnica) jest określana jako 1/3 odległości pomiędzy polami lutowniczymi, natomiast szerokość otworu W - jako 110% szerokości obudowy elementu (rys. 8). Typowa grubość szablonu powinna zawierać się pomiędzy 0,150 - 0,200mm (5,9 - 7,9 milsów).
Piotr Ciszewski
Semicon
www.semicon.com.pl