Konieczne kompromisy, z jakimi trzeba się godzić w trakcie projektowania konwerterów DC-DC, znacznie by się uprościłyby, gdy indukcyjność wbudować do wnętrza układu scalonego w układzie sterującym zasilaniem. W niniejszym artykule skupiono się na zagadnieniach projektowania, które upraszczają się przez włączenie indukcyjności do układu scalonego. Projektowanie indukcyjności uznano za szczególnie uciążliwe, ponieważ wpływa na sprawność, stabilność i zaburzenia elektromagnetyczne (EMI), a także rozmieszczenie elementów układu i powierzchnię, jaką zajmuje on na płytce. Wreszcie scalenie indukcyjności gwarantuje parametry systemu, ułatwiając pracę projektantom systemów.
Brak norm
Nie ma żadnych norm, które regulowałyby lub narzucały jednolite parametry cewek i dławików indukcyjnych. Każdy z producentów na rdzenie używa własnych materiałów magnetycznych o unikalnym składzie, własnej techniki nawijania, rodzaju drutu nawojowego, kształtu i geometrii wyprowadzeń itp. Stan ten silnie kontrastuje z kondensatorami na przykład MLC, w których własności dielektryka, wytrzymałość napięciowa, czy rozmiary fizyczne są znormalizowane. Gdy kupuje się kondensator MLC 1206, 10μF X5R na 10V, od dowolnego producenta, podstawowe parametry kondensatora będą takie same. Jedyne różnice będą dotyczyły zastępczej rezystancji szeregowej (ESR), czy zastępczej indukcyjności szeregowej (ESL). Takich norm, a więc takiego ujednolicenia dla cewek nie ma. Dla określonej indukcyjności projektant spotyka się z mnóstwem możliwości w zakresie strat stałoprądowych, strat zmiennoprądowych, parametrów sygnałów małej amplitudy, prądu nasycenia, rozmiarów fizycznych itp. Przy wyborze cewki lub dławika istnieje wiele stopni swobody, z których każdy wpływa na jej właściwości. Zrozumienia wpływu każdego z kompromisów trzeba się uczyć latami metodą prób i błędów.
Wpływ temperatury
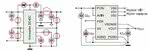
Rys. 1. Konieczne elementy zewnętrzne typowego przetwornika obniżającego z indukcyjnością zewnętrzną (po lewej) w porównaniu do odpowiadającego mu przetwornika scalonego z indukcyjnością (po prawej).
Szczególną cechą cewek i dławików z rdzeniem ferrytowym jest stosunkowo znaczny wpływ temperatury na ich liczne parametry. Straty stałoprądowe ze wzrostem temperatury wzrastają. Straty zmiennoprądowe w przypadku niektórych materiałów magnetycznych zależą od temperatury, a dla różnych ich odmian osiągają minima przy różnych temperaturach. W przypadku innych materiałów są nie są od temperatury zależne.
Główną przyczyną temperaturowej zależności strat stałoprądowych jest wzrost rezystancji drutu nawojowego ze wzrostem temperatury. Rezystancja miedzi wzrasta o 0,393%/ºC, aluminium i srebra podobnie. Rezystancja uzwojenia przy 75ºC będzie o 20% wyższa niż przy 25ºC. W tym samym stopniu, przy niezmienionym natężeniu prądu stałego, wzrośnie wydzielanie ciepła.
Straty zmiennoprądowe w cewce powstają i w uzwojeniu i w materiale magnetycznym rdzenia. Straty w przewodach są wywoływane przez kombinację efektu naskórkowego i efektu bliskości. Oba te rodzaje strat zmniejszają się ze wzrostem temperatury. Dzieje się tak dlatego, że gdy wzrasta rezystancja, głębokość naskórkowości również wzrasta, proporcjonalnie do pierwiastka kwadratowego zmiany rezystancji. Straty zmiennoprądowe w niektórych magnetycznych materiałach rdzenia, jak sproszkowane żelazo, alsifer i blachy, praktycznie nie zależą od temperatury, w przeciwieństwie do takich jak NiZn lub MnZn. Minima strat w tych materiałach, zależnie od ich składu, mogą się znaleźć między 25ºC a 120ºC.
Gęstość nasycenia strumienia magnetycznego w rdzeniu z niektórych materiałów maleje ze wzrostem temperatury w jej normalnym przedziale. Oznacza to, że jeśli konwerter tak został zaprojektowany, że rdzeń pracuje blisko nasycenia w temperaturze pokojowej (prąd nasycenia jest zwykle podawany dla temperatury 25ºC), to podczas pracy w wyższej temperaturze rdzeń się nasyci, skutkiem czego przez stosunkowo niską impedancję cewki będzie płynął duży prąd szczytowy. Wywoła on wzrost skutecznego natężenia prądu, powodując zwiększone ponad oczekiwania straty przewodzenia w cewce. Do prawidłowego projektowania potrzebne są parametry materiałów w wyższych temperaturach, nie zawsze podawane przez wytwórców.
Temperaturowo nieprzewidywalne otoczenie
Oprócz oczywistych czynników temperaturowych są jeszcze dwa, z pozoru nie oczywiste.
Pierwszy bierze się z faktu, że od producentów cewek bardzo trudno uzyskuje się ich szczegółowe parametry termiczne. W wielu przypadkach sami wytwórcy nie mają tak szczegółowej wiedzy. Ale wpływ tych parametrów na projektowane zasilacze jest ogromny.
Drugim czynnikiem, tak samo o ile nie bardziej ważnym, jest brak wiedzy projektanta o termicznym otoczeniu konwertera, w którym indukcyjność ma pracować. Lokalna temperatura może być całkiem wysoka, jeśli na przykład zasilacz jest umieszczony w pobliżu radiatora. Także duży ASIC w bliskim sąsiedztwie może nagrzewać powierzchnię masy pod cewką. Obliczanie wzrostu temperatury cewki może więc mieć niewielkie znaczenie, jeżeli znaczna część tego wzrostu jest skutkiem przewodzenia lub promieniowania ciepła z zewnątrz.
Czułość na rozmieszczenie
Po omówieniu parametrów cewki lub dławika można przejść do lepiej poznanych właściwości tego podzespołu – czułości na jego położenie na płytce drukowanej. Podczas projektowania trzeba wiele uwagi poświęcić generacji zaburzeń przez element przełączający, aby uniknąć indukowania prądów zakłócających w płytce drukowanej. Umiejscowienie cewki ma duży wpływ na wejściową i wyjściową pętlę zmiennoprądowego sprzężenia zwrotnego, są one bowiem głównymi źródłami promieniowania zaburzeń EMI. Są one zarówno przewodzone jak i promieniowane, mogą sprząc się z obwodami sprzężenia zwrotnego i pogorszyć stabilność pętli sprzężenia zwrotnego. Niewłaściwe rozmieszczenie komponentów często prowadzi do kłopotów z zakłóceniami i stabilnością pracy zasilaczy.
Napięcie w węźle przełączania, wspólnym punkcie MOSFET-ów mocy, górnego i dolnego, przerzuca się od poziomu napięcia wejściowego do poziomu masy. Szybkie przerzuty w tym punkcie indukują w płytce drukowanej w bezpośredniej bliskości węzła siłę elektromotoryczną (SEM). Pasożytnicze pojemności pomiędzy węzłem i innymi węzłami na płytce mogą wywoływać niepożądane prądy, prowadzące do problemów z EMI.
Głównymi źródłami promieniowania zakłócającego są w przetworniku wejściowa i wyjściowa pętla prądowa. Projektanci doświadczeni w projektowaniu układów w.cz znają oddziaływanie tych prądów, płynących w antenach pętlowych. Sprawność promieniowania takich anten zależy od stosunku ich rozmiarów do częstotliwości. W celu obniżenia ich sprawności trzeba się starać w możliwie największym stopniu zmniejszać rozmiary tych pętli. Na wejściową pętlę prądową pozycja cewki nie ma w zasadzie wpływu, chyba że układ scalony sterownika jest źle zaprojektowany, czy gęstość układów scalonych na płytce wymusza nieoptymalne rozmieszczenie komponentów. Jednakże na wyjściową pętlę zmiennoprądową cewka wpływa bezpośrednio. Należy zatem zwrócić baczną uwagę na pozycję cewki i kondensatora wyjściowego, aby możliwie zmniejszyć tę pętlę i nie dopuścić do powstania efektów pasożytniczych w ścieżce powrotnej prądu zmiennego.
Ratunek w scaleniu
Scalenie indukcyjności w układzie scalonym skutecznie usuwa trudności z tym komponentem z listy kłopotów projektanta. W rezultacie otrzymuje się układ o najmniejszej możliwej powierzchni montażowej, najmniejszej liczbie elementów, gwarantujący optymalne parametry. A z perspektywy projektanta scalenie indukcyjności ułatwia projektowanie zasilacza i upodobnia je do projektowania liniowego stabilizatora.
Kompletna charakterystyka
Scalenie indukcyjności zdejmuje też z projektanta ciężar odszukiwania jej licznych właściwości i związaną z nim zmienność i przerzuca go na barki producenta półprzewodników i daje szansę, aby cewka scalona z układem zasilacza została zaprojektowana optymalnie w całym zakresie warunków działania, napięć wejściowych i wyjściowych, częstotliwości pracy, prądu obciążenia, strat stałoprądowych i zmiennoprądowych, zależności termicznych, wzrostu temperatury, prądu nasycenia i dopuszczalnego upływu strumienia magnetycznego. Ponieważ producent półprzewodnika zna także lepiej właściwości krzemu, niż dostępne w publikacjach, możliwa jest optymalizacja przetwornika. Rezultat jest przewidywalny we wszystkich aspektach, elektrycznych, termicznych i zakłóceniowych (EMI).
Optymalne rozmieszczenie w obudowie
Wprowadzenie indukcyjności do wnętrza obudowy układu pozwala zoptymalizować pozycję tego podzespołu względem źródła zaburzeń EMI. Rozmieszczenia wyprowadzeń wejścia i wyjścia względem masy zostają starannie dobrane. Umożliwia to uzyskanie możliwie najmniejszych wejściowej i wyjściowej pętli zmiennoprądowych. Impedancja pomiędzy zakłócającym węzłem przełączania i cewką jest kontrolowana, pozwalając na redukcję emisji zakłóceń.
W wielu dostępnych na rynku przetwornikach większość obwodów kompensacyjnych mieści się na zewnątrz stabilizatora. Jest to konieczne z powodu znacznej zmienności charakterystyk cewki indukcyjnej i niemożności ich zoptymalizowania w szerokim zakresie warunków pracy. Rys. 1 pokazuje typowe rozwiązanie takiego układu z indukcyjnością umieszczoną na zewnątrz, w porównaniu z układem w pełni scalonym. W tym pierwszym przypadku poza układem znajdują się kondensatory wejściowy i wyjściowy, kondensator analogowego filtra wejściowego, liczne elementy obwodów kompensacyjnych, obwód bootstrapu górnego MOSFET-a i oczywiście cewka lub dławik. W sumie jest to 14 elementów zewnętrznych. Trzeba pamiętać, że układ ten zawiera scalone MOSFET-y. Gdyby ich nie zawierał, liczba elementów byłaby jeszcze większa, więcej byłoby także potencjalnych zmiennych.
Scalenie indukcyjności zapewnia wyższy stopień kontroli nad projektowanym przetwornikiem. Kompletna charakterystyka cewki pozwala na zoptymalizowanie układu dla wymaganych warunków pracy. Po scaleniu indukcyjności liczba 14 elementów zewnętrznych zmniejszyła się do jedynie 3. W przypadku układów z wewnętrznym obwodem płynnego rozruchu liczba ta maleje do 2.
Redukcja zajmowanej powierzchni
Bardzo ważnym skutkiem scalenia jest znaczna redukcja powierzchni zajmowanej przez układ na płytce drukowanej, a także jego wysokości. Ponieważ praktycznie wszystkie komponenty przetwornika mieszczą się w jego obudowie, gęstość upakowania jest bardzo duża. Najlepsze w swojej klasie rozwiązanie z cewką zewnętrzną zajmuje powierzchnię około 550mm2 przy mocy 10W, czyli 1,8W/cm2 (12W/cal2). Odpowiadające mu rozwiązanie ze scaloną indukcyjnością zajmuje 180mm2, czyli 5,5W/cm2 (36W/cal2). Z tych liczb wynika, że gęstość wzrasta trzykrotnie, a zajmowana powierzchnia też trzykrotnie maleje.
Gwarantowane parametry systemu
Jedną z uprzednio wspominanych wad rozwiązania z zewnętrzną cewką jest nieprzewidywalność termiczna otoczenia, ogromnie utrudniająca przewidywanie parametrów przetwornika. Indukcyjność mieszcząca się w obudowie jest termicznie izolowana od otoczenia przez jej plastykowy materiał. Termiczne właściwości wnętrza obudowy układu scalonego są doskonale znane, są przewidywalne i mogą zostać uwzględnione przy projektowaniu przetwornika.
Drugim ważnym skutkiem scalenia jest gwarancja jakości całego systemu zasilania. Jak już wspomniano, scalenie zapewnia zoptymalizowanie całości od początku do końca, opierające się na kompletnej znajomości właściwości cewki i krzemu w całym zakresie spodziewanych warunków działania. Kompensacja jest dokładnie dostosowana do cewki, MOSFET-a i pasożytniczych elementów połączeń, w innych warunkach niemożliwych do rozpoznania. Po zaprojektowaniu przetwornik wraz z indukcyjnością jest testowany jako całość. Optymalizacja w połączeniu z wynikami końcowego testu gwarantuje wszystkie właściwości przetwornika DC-DC.
Konwertery z wbudowaną indukcyjnością – oferta rynkuEnpirion EN5311Q to jeden z kilku 1-amperowych konwerterów DC-DC, w którym cewka indukcyjna została wbudowana do wnętrza obudowy układu scalonego, dostępny jest na rynku od 2006 roku. Obudowa o wymiarach 4x4x1,1mm kryje funkcjonalny sterownik PWM wraz z kompletem obwodów zabezpieczających, driver stopnia mocy i dwa tranzystory przełączające MOSFET. Nad strukturą umieszczono planarną cewkę powietrzną. Układ pracuje na częstotliwości 4MHz i akceptuje napięcie wejściowe w zakresie 2,4-5,5V. Napięcie wyjściowe może być ustalane na jednej z typowych wartości za pomocą trzech końcówek sterujących w zakresie 0,8-5V. Układ charakteryzuje się sprawnością przetwarzania do 95% i pobiera jedynie 1µA prądu w stanie standby. Enpirion oferuje także układy przetworników drugiej generacji o prądzie wyjściowym dochodzącym do 3A EN533x i 6A EN536x. Ceny tych ostatnich układów dla partii 1000 sztuk wynoszą odpowiednio 2,94 dol. i 4,36 dol. |
Układ przykładowy
Do zilustrowania procesu projektowania wybrano jednoamperowy przetwornik DC-DC firmy Enpirion EN5311Q. Rozmieszczenie jego wyprowadzeń jest dostosowane do optymalnych pozycji kondensatorów wejściowego i wyjściowego. Dla masy wejściowej i masy wyjściowej przeznaczono osobne wyprowadzenia. W tym układzie scalonym zastosowano trójwyprowadzeniową konfigurację napięcia ID czyli VID, do wyboru napięcia wyjściowego. Pozwala ona projektantowi wybrać jedno z siedmiu z góry ustalonych napięć wyjściowych, albo posłużyć się w tym celu zewnętrznym dzielnikiem napięcia.
Prawidłowe zaprojektowanie przetwornika DC-DC ze scaloną indukcyjnością jest bardzo łatwe. Jak zawsze w przypadku układów w.cz. trzeba uważać z rozmieszczaniem powierzchni masy. Wejście i wyjście zasilania, oraz płaszczyzny masy, powinny być tak rozmieszczone, aby kondensatory wejściowy i wyjściowy można było umieścić jak najbliżej układu scalonego. Na rys. 2 pokazano taką konfigurację płaszczyzn. Do wejściowej i wyjściowej sekcji filtra powinny zostać użyte osobne płaszczyzny masy. Odprowadzenia masy powinny być możliwie najgrubsze, ale nie powinny się ze sobą stykać. Wejściowa płaszczyzna masy powinna zostać użyta do połączenia końcówki masy kondensatora wejściowego z wejściowym wyprowadzeniem masy układu scalonego. Masa ta nie powinna się łączyć z żadnym innym układem, za wyjątkiem małych przelotek pomiędzy wejściową płaszczyzną masy a masą systemu. Dzięki temu zostaną zredukowane tętnienia wejściowe, wywołane wysokoczęstotliwościowymi składowymi przerzutów przebiegu przełączania. Kilka małych przelotek powinno łączyć wyjściową płaszczyznę masy z masą systemu. Redukuje to tętnienia wyjściowe, wywołane impulsami przełączania. (KKP)