Posługiwanie się elektromagnesem prądu stałego w pętli sprzężenia sterującego nie jest łatwe, pomimo że jest to urządzenie proste. W licznych zastosowaniach musi on być wzbudzany wiele razy w ciągu sekundy, szczególnie gdy pętla sterująca służy do regulowania przepływu cieczy przez zawór. Rozpowszechnienie układów cyfrowych może kusić do posługiwania się zaworami elektromagnetycznymi tak jak przekaźnikami, czyli sterowania ich z wyjścia układu cyfrowego za pośrednictwem tranzystora.
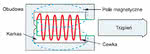
Rys. 1. Elektromagnes składa się z uzwojenia nawiniętego na plastykowym, ceramicznym lub mosiężnym karkasie, umieszczonym w żelaznej obudowie z żelaznym trzpieniem
W wielu aplikacjach jest to jednak podejście błędne. Często układy zasilające muszą dysponować odpowiednią nadwyżką napięcia zasilania. Nawet jeśli średnia moc zasilania nie jest duża, to impuls pobieranego z baterii prądu może powodować zbyt duży spadek napięcia, zwłaszcza gdy bateria jest bliska wyczerpania. Z kolei zbyt wysokie napięcie, a w konsekwencji zbyt duży prąd przepływający przez elektromagnes może spowodować jego przegrzanie.
Kłopoty mogą powstawać także w stanie spoczynkowym elektromagnesu, gdy jego wzbudzenie jest utrudnione lub gdy czasy uruchomienia i uwolnienia są zbyt długie. Jeżeli elektromagnes jest objęty pętlą sterowania, pętla może stać się niestabilna i uszkodzić elektromagnes. Metoda kontroli prądu wzbudzenia w pętli sterowania zawsze musi zostać wybrana starannie. Elektromagnes składa się z uzwojenia nawiniętego na plastikowym, ceramicznym lub mosiężnym karkasie oraz żelaznej obudowy (rys. 1).
Obudowa jest jarzmem przejmującym pole magnetyczne, wzbudzane przez prąd płynący w cewce. Ruchomy trzpień żelazny zamyka pole. Cewka może również służyć za łożysko trzpienia. W miarę, jak zmniejsza się szczelina powietrzna pomiędzy trzpieniem i jarzmem, natężenie pola magnetycznego w rdzeniu rośnie, a wraz z nim siła wywierana przez trzpień na obciążenie. Gdy trzpień całkowicie zagłębi się w cewkę, oba jego końce domykają szczeliny powietrzne.
Początkowo indukcyjność cewki jest mała z powodu dużych szczelin powietrznych. Ponieważ pole magnetyczne w powietrzu rozprzestrzenia się gorzej niż w żelazie, do wytworzenia pola o sile wystarczającej do poruszenia trzpienia początkowo jest potrzebne większe natężenie prądu w cewce elektromagnesu. Po zagłębieniu się trzpienia w cewce i domknięciu obwodu magnetycznego, do utrzymywania elektromagnesu w stanie zamkniętym wystarcza mniejsze natężenie prądu.
Przekaźnik elektromagnetyczny jest urządzeniem czynnym, używanym do uruchamiania styków przełącznika. Elektronicznie zarówno elektromagnes, jak i przekaźnik są podobne, ponieważ można je traktować jak indukcyjności. Na tym jednak ich podobieństwo się kończy. Pod względem funkcjonalnym elektromagnes bardziej przypomina silnik niż przekaźnik. Używa się go do zamiany energii, zwykle elektrycznej w mechaniczną. Ruch elektromagnesu jest zwykle jednokierunkowy, a powrót do położenia spoczynkowego zapewnia sprężyna.
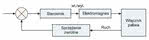
Rys. 2. Elektromagnes wchodzi w skład systemu sterującego ze sprzężeniem zwrotnym, który kontroluje dopływ paliwa do zaworu pędnika
Istnieją elektromagnesy dwukierunkowe, wymagające zastosowania dwóch obwodów sterujących. Czas pozostawania w stanie wzbudzonym powinien być ograniczony ze względu na możliwość uszkodzenia wydzielającym się w uzwojeniu ciepłem. Jednym ze sposobów ograniczania emisji ciepła jest obniżanie prądu po wzbudzeniu elektromagnesu. Na rysunku 2 przedstawiono elektromagnes jako element wykonawczy, objęty pętlą sprzężenia zwrotnego.
Sterownik wysyła polecenia uruchomienia elektromagnesu sterującego procesem, w tym przypadku zaworu dozującego, który reguluje dopływ paliwa do pędnika. Elektromagnes otwiera zawór, a sprężyna go zamyka. Wymagania dla elektromagnesu specyfikują czasy uruchomienia i zwolnienia, maksymalny i minimalny czas otwarcia, cykl roboczy i powtarzalność. W przykładzie przedstawiono dwie metody sterowania: z zamkniętą i otwartą pętlą sprzężenia.
Intuicyjnie najlepszym sposobem sterowania elektromagnesu wydaje się użycie przełączanego obwodu tranzystorowego sterowanego z wyjścia logicznego, pracujących w otwartej pętli napięciowej. Układ taki mógłby działać poprawnie w warunkach stabilnego zasilania. Ale stabilny zasilacz nie jest jedynym czynnikiem wyznaczającym metodę sterowania. Trudności może sprawiać zmienność działania elektromagnesu. Czasy włączania i wyłączania są zależne od zmian napięcia i rezystancji cewki.
W tym przykładzie źródłem zasilania jest bateria, w której zmiany napięcia podczas pracy dochodzą do 10V. W konfiguracji otwartej pętli trzeba zapewnić działanie elektromagnesu przy minimalnym napięciu – w warunkach wyczerpania pojemności baterii. Natomiast zamknięta pętla prądowa wymaga więcej komponentów, a jej działanie nie może kolidować z działaniem sterownika procesowego. Do wyboru metody sterowania konieczne jest dokładne zrozumienie charakterystyki obciążenia elektromagnesu i parametrów kontrolowanego przez niego procesu.
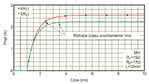
Rys. 3. Termiczna zmiana stałoprądowej rezystancji cewki wpływa na czasy uruchomienia i zwolnienia elektromagnesu. Wraz ze zmianą rezystancji zmienia się stała czasowa obwodu cewki. Powyższe wykresy pokazują zmianę czasu uruchomienia
Przy projektowaniu układu zasilania i obwodów sterujących trzeba brać pod uwagę właściwości elektromagnesu. Jego zadaniem jest wytwarzanie momentu napędowego. Indukcyjność elektromagnesu zmienia się w trakcie jego działania. Wytwarzany moment napędowy zależy od natężenia pola magnetycznego, które z kolei zależy od natężenia prądu w cewce i liczby jej zwojów. W celu zwiększenia momentu trzeba zwiększyć albo liczbę zwojów, albo natężenie prądu, które zależy od rezystancji uzwojenia.
W przytoczonym przykładzie początkowa indukcyjność elektromagnesu wynosi 3,3mH, a rezystancja stałoprądowa 15Ω. Do uzyskania momentu wymaganego do pokonania sprężyny i otwarcia zaworu jest potrzebny prąd o natężeniu 2,2A płynący przez 5ms, a następnie do podtrzymania potrzebny jest prąd 0,75A płynący przez 2s. Po takim cyklu elektromagnes powinien być w ciągu 20ms zdolny do ponownego wzbudzenia. Zgodnie z prawem Ohma sterownik musi dostarczyć elektromagnesowi 33V w trakcie jego włączania i 11,25V w czasie podtrzymywania.
Początkowo wydaje się, że sterowanie napięciem może być dogodne, ale trzeba jeszcze rozważyć inne czynniki. W miarę przepływu prądu przez cewkę ulega ona rozgrzaniu, a jej rezystancja wzrasta, przyczyniając się do wzrostu strat I2R. Efekt ten zależy od średnicy drutu nawojowego. Załóżmy, że cewka elektromagnesu została nawinięta drutem o średnicy 0,13mm i długości 11m. Nagrzewanie się cewki opisuje następujące równanie:
T = TA + 10[33S(I/A)]2-1(234 + TA)
gdzie: S jest czasem działania w sekundach, T – temperaturą drutu po upływie S sekund, A – polem przekroju drutu w tysięcznych cala kwadratowego, I – natężeniem prądu, a TA – temperaturą otoczenia. Rezystancję drutu oblicza się z zależności:
Rt = R20[1 + a20(t - 20)]
gdzie: R20 jest rezystancją w temperaturze 20ºC, a20 – współczynnikiem temperaturowym rezystancji miedzi, równym 0,00393 przy 20ºC, a t – temperaturą końcową. Korzystając z tych równań i opisanego powyżej przebiegu prądu w funkcji czasu, można obliczyć, że po pierwszym cyklu rezystancja cewki wynosi 17Ω. Napięcie potrzebne do kolejnego uruchomienia elektromagnesu wzrasta do 38V, a napięcie podtrzymywania do 13V.
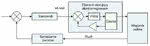
Rys. 4. Elementami pętli prądowej są cewka elektromagnesu, modulator PWM i wzmacniacz sprzężenia zwrotnego. Sterownik jest elementem typu włącz/wyłącz, dostarczającym paliwa do pędnika. Pętla prądowa mieści się wewnątrz pętli sterującej dostarczaniem paliwa, czyli jest w niej zagnieżdżona
Wzrost temperatury nie uwzględnia zmian termicznych cewki. Po kilku dalszych uruchomieniach elektromagnes tak się nagrzewa, że natężenie prądu uruchamiania przestaje być osiągalne. W rezultacie ilość paliwa zasilającego pędnik albo nie jest poprawnie stabilizowana, albo paliwo przestaje do niego dopływać. Zmiany rezystancji stałoprądowej wpływają też na czas uruchamiania i zwalniania elektromagnesu.
Wraz ze zmianami rezystancji zmienia się stała czasowa ładowania. Na rysunku 3 pokazano zmianę czasu uruchamiania elektromagnesu. W przykładowym układzie użyto napięcia zasilania 38V, aby prąd w indukcyjności mógł osiągnąć natężenie 2,2A. Na wykresie widać, że wzrost rezystancji spowodował opóźnienie osiągnięcia natężenia włączenia elektromagnesu o 1ms.
Wybór sposobu sterowania
Stałą czasową ładowania obwodu cewki jest stosunek indukcyjności do rezystancji, w tym przypadku rezystancji stałoprądowej. Im później w elektromagnesie osiągane jest natężenie prądu koniecznie do uruchomienia, tym silniej nagrzewa się drut uzwojenia i tym większa staje się jego rezystancja. Kontrola napięcia na elektromagnesie nie rozwiązuje trudności. Zmiany rezystancji stałoprądowej w czasie będą wpływały na czas uruchamiania.
Lepszym rozwiązaniem jest sterowanie prądem w cewce. Wszystkie zmienne związane z zachowaniem się elektromagnesu utrudniają, jeżeli wręcz nie uniemożliwiają, uzyskanie sprawnego działania w otwartej pętli. Niezbędne jest więc sterowanie w pętli zamkniętej. Sterowanie napięciowe nie ma sensu. Cewka musi być sterowana prądem, co zapewnia niezawodność działania. Pętla sterująca z rysunku 2 musi zostać uzupełniona przez dodanie pętli prądowej w układzie sterowania cewką (rys. 4).
Składnikami pętli prądowej są: cewka elektromagnesu, modulator PWM i wzmacniacz sprzężenia zwrotnego. Sterownik jest elementem typu włącz/wyłącz, dostarczającym paliwa do pędnika. Pętla prądowa znajduje się w pętli poleceń sterowania paliwem, czyli jest w niej zagnieżdżona. Wymagania dla pętli prądowej są narzucane przez pętlę procesu. Do właściwego zaprojektowania pętli prądowej jest niezbędna pełna znajomość działania pętli procesu.
W tym przypadku jest to pętla 50Hz, aktualizująca co 20ms polecenia sterownika kierowane do złącza sumującego w układzie sterowania elektromagnesem. Polecenia te muszą być wykonywane w czasie znacznie krótszym, tak aby pędnik był gotowy do przyjęcia następnego polecenia. Pasmo częstotliwościowe pętli prądowej musi być 5–10 razy szersze niż pasmo pętli zewnętrznej, co zapewni, że pętla elektromagnesu nie wywoła niestabilności w pętli zewnętrznej. Powinno tu wystarczyć pasmo 1 kHz.
Synchronizacja z systemową częstotliwością zegarową
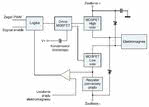
Rys. 5. Częstotliwość PWM musi być na tyle duża, aby mogła zapewnić wystarczającą rozdzielczość prądu sterującego
Rysunek 5 pokazuje zależności pomiędzy elementami sterowania elektromagnesem i sygnałem sterującym. Częstotliwość zegarowa PWM musi być na tyle wysoka, aby zapewnić odpowiednią rozdzielczość prądu sterującego. Na szczęście elektromagnes jest urządzeniem binarnym, włączonym (2,2A) lub wyłączonym (0A). Dwa punkty sterujące systemu to stan włączenia (2,2A) i trzymania (0,75A). Jeśli elektromagnes stanowi część większego systemu i sąsiaduje z czułymi elementami elektronicznymi, lepiej będzie zsynchronizować częstotliwość PWM z systemową częstotliwością zegarową.
Do wybrania właściwej częstotliwości PWM potrzebna jest szczegółowa wiedza o podatności systemu na zaburzenia. Znajomość indukcyjności elektromagnesu jest pomocna w doborze pojemności kształtującej obciążenie przy częstotliwości PWM. Istotne znaczenie mają właściwości sterujących tranzystorów FET (im wyższa częstotliwość PWM, tym wyższe straty przełączania). W omawianym przykładzie wykorzystano częstotliwość PWM równą 125 kHz i współczynnik wypełnienia 90%.
Wejście Enable/Disable umożliwia przepuszczenie do układu sterowania napięcia sterującego prądem elektromagnesu. Obwód sterujący może być wyłączony poprzez wyłączenie częstotliwości PWM. Polecenie prądowe może przybierać stan logiczny wysoki lub niski. W opisywanym przykładzie 5V zapewnia prąd włączenia, a 0V prąd podtrzymywania. Elektromagnes jest zasilany przez parę baterii o nominalnym napięciu 28V. Napięcie pracy tych baterii wynosi od 32 do 24V, zatem napięcie zasilania może się zmieniać w granicach od 64 do 48V.
Zasada działania
Układ sterujący podaje do obu tranzystorów MOSFET sygnał zegarowy PWM o współczynniku wypełnienia 90%. Gdy natężenie prądu w elektromagnesie osiągnie poziom włączenia, komparator zatrzymuje sygnał PWM. Gdy napięcie sterowania prądem elektromagnesu przechodzi w stan niski, komparator uruchamia sygnał PWM do momentu, gdy prąd w cewce spadnie poniżej natężenia podtrzymywania. Sterownikami high-side i low-side są tranzystory MOSFET o bardzo małej rezystancji dren-źródło.
Pozwalają wykorzystywać całkowite napięcie zasilania, pomniejszone jedynie o spadek napięcia RDS(on), bardzo szybko włączając w cewce przepływ prądu. Sygnał zegarowy o współczynniku wypełnienia 90% zapewnia skuteczne napięcie baterii wynoszące 50,4V. Tranzystor MOSFET musi zostać dobrany tak, aby zapewnić wymagane natężenie prądu włączania elektromagnesu z odpowiednim marginesem. Dobrym wyborem na początek może być tranzystor o maksymalnym prądzie drenu przynajmniej dwukrotnie większym od prądu włączenia oraz o odpowiednio dużym napięciu dren-źródło.
W tym przypadku najlepiej zastosować dwa jednakowe n-kanałowe tranzystory MOSFET. Do tranzystora górnego należy dołączyć układ bootstrapu, zapewniający dostatecznie duże napięcie bramka-źródło. Występuje on w większości scalonych sterowników tranzystorów MOSFET, a w ich danych technicznych zamieszczony jest sposób obliczania pojemności kondensatora podbijającego napięcie. Kondensator obciążenia jest połączony równolegle z zasilaniem.
Dostarcza on ładunek dla początkowego impulsu prądowego indukcyjności i filtruje zakłócenia w systemie. Kondensator ten musi być dostosowany do obciążenia, czyli konkretnej indukcyjności. Jego rola jest tym ważniejsza, im elektromagnes znajduje się dalej od zasilacza. Najlepszy jest kondensator ceramiczny ze względu na niską równoważną rezystancję szeregową (ESR). Aplikacja wymaga, aby spadek napięcia zasilania w trakcie przełączania PWM nie przekraczał 2V. Kondensator musi dostarczać prądu przez 90% cyklu PWM, czyli przez 7,2μs. Jego pojemność można obliczyć z równania:
dU = I(dt/C) + IR
skąd:
C = I(dt/dU - IR)
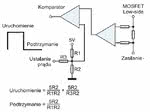
Rys. 6. Obwód pętli sterowania zamyka czujnik rezystorowy i komparator, w którym sygnał z czujnika jest porównywany z sygnałem sterowania prądem
gdzie zmiana napięcia dU = 2V, a I jest prądem włączania równym 2,2A. R oznacza rezystancję ESR ceramicznego kondensatora i wynosi 100mΩ. Po podstawieniu powyższych wartości otrzymujemy minimalną wartość C równą 8,9μF, gwarantującą spadek napięcia nieprzekraczający 2V. Dopuszczalne napięcie pracy kondensatora nie powinno być mniejsze niż dwukrotne napięcie zasilania. Diody Schottky’ego sprowadzają do masy ładunki indukowane przez zanikające pole magnetyczne po wyłączeniu elektromagnesu. Dzięki temu elektromagnes jest doprowadzany możliwie najszybciej do stanu początkowego, a zakłócenia w układzie są minimalizowane.
Pętlę prądowego układu sterującego zamyka czujnik prądowy i komparator, który porównuje napięcie czujnika z napięciem sterującym prądem elektromagnesu. Obwód ten pokazano na rysunku 6. Relacje czasowe sygnału Enable/Disable i sygnału sterującego prądem elektromagnesu są bardzo istotne. Sygnał Enable/Disable musi przejść w stan wysoki w tym samym momencie, w którym narasta sygnał sterujący. Po włączeniu elektromagnesu sygnał sterujący przechodzi w stan niski, powodując generację prądu podtrzymywania. Jeśli zostanie aktywowany sygnał Enable, przez cewkę płynie prąd ustalony na wejściu sterującym.
Zakłócenia impulsowe
Ponieważ opisany system charakteryzuje się pracą impulsową, pętla prądowa sterownika generuje zaburzenia. Jedynym sposobem ograniczania niekorzystnego wpływu zaburzeń na pozostałą część systemu jest blokowanie dróg, którymi mogą się przedostawać. Specjaliści napisali całe tomy na temat rozmieszczania elementów i rozprowadzania połączeń we wzmacniaczach ze sprzężeniem ładunkowym. Podstawowe zasady każą utrzymywać możliwie najkrótsze ścieżki pomiędzy tranzystorami MOSFET a kondensatorami i diodami. Przy bramkach należy stosować rezystory szeregowe spowalniające przełączanie. Jest bardzo ważne, aby warstwa płytki drukowanej zawierająca ścieżki sąsiadowała z grubą warstwą uziemiającą.
Ścieżki wysokoprądowe powinny być bardzo szerokie i najlepiej prowadzone jedna nad drugą przez całą drogę do złącza. Od złącza do elektromagnesu należy użyć ekranowanej skrętki. Przy obliczaniu rezystancji obciążenia należy pamiętać o spadku napięcia na przewodach wiązki. Ścieżki prądowe elektromagnesu powinny być możliwie krótkie i charakteryzować się jak najmniejszą rezystancją. Opisany układ sterowania jest prosty i może być zrealizowany na powierzchni około 6,3cm2. Większy prąd wymaga większej powierzchni. Jeżeli precyzyjne sterowanie elektromagnesem jest mniej ważne od zajmowanej powierzchni płytki, można użyć sterowania napięciowego z otwartą pętlą. (KKP)