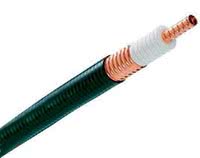
Fot. 1. Kabel koncentryczny z karbowaną folią miedzianą i spienionym dielektrykiem zapewnia dużą odporność na narażenia mechaniczne
Początkowo telegraficzne, a potem telefoniczne, kable podmorskie składały się z przewodnika w cylindrycznym izolatorze, wytwarzanym wtedy z naturalnego lateksu, uzyskiwanego z drzew kauczukowych. Był on odporny na niskie temperatury i wysokie ciśnienie morskiego dna. Otaczająca izolator woda morska tworzyła zewnętrzny przewodzący biegun przewodu. Patent na pierwszy kabel współosiowy uzyskał w roku 1880 angielski inżynier i matematyk Oliver Heaviside.
Pięćdziesiąt lat później, w roku 1929, pierwszy amerykański patent (nr 1 835 031) na nowoczesny "współosiowy system przewodowy" otrzymali Lloyd Espenishied i Herman Affel z A&T Bell Labs. W firmie tej kontynuowano pionierskie prace nad przewodami koncentrycznymi, które doprowadziły do ustalenia optymalnej dla nich impedancji falowej.
Doświadczenia te w zależności od aplikacji wykazały, że dla transmisji mocy wynosi ona 30 Ω, dla minimalnych strat 77 Ω i 60 Ω dla wysokiego napięcia. Powszechnie w następstwie przyjęła się kompromisowa do transmisji wielkich częstotliwości impedancja 50 Ω.
W wyniku rosnącego szybko używania kabli koncentrycznych w czasie II wojny światowej w USA powstała dla tych kabli norma. Poszczególne ich rodzaje zaczęto nazywać według numerów stron podręcznika "Radio Guide", na których je opisano, w rezultacie przyjęły się nazwy RG-6, RG-58 itd. Obecnie najbardziej rozpowszechnionym i wyczerpującym przemysłowym standardem kabli współosiowych do 12 GHz jest MIL-DTL-17 (dawniej MIL-C-17).
Początkowo w koncentrykach wykorzystywano sztywne falowodowe przewody rurowe, w których współosiowy przewód był podtrzymywany w powietrzu koncentrycznymi rozpórkami izolacyjnymi lub wytłaczanym materiałem dielektrycznym. Konstrukcja ta wyewoluowała do półsztywnej ciągnionej rurki, dającej się dostosowywać do potrzeb instalacyjnych przez wyginanie, ale prezentującej doskonałe własności elektryczne.
Sztywna rurka koncentryka została następnie zastąpiona elastycznym miedzianym i cynowanym oplotem drucianym, znacznie ułatwiającym układanie kabla. Taki kabel jest dużo łatwiejszy przy instalowaniu, jednak podatny na pęknięcia, gdy zginany wielokrotnie. Giętki kabel z oplotem pokryty termoplastyczną koszulką stał się odtąd rozwiązaniem stosowanym powszechnie.
Rola dielektryka w kablu
Dielektryczny materiał kabla zarówno izoluje wewnętrzny przewód od ekranu, jak i mechanicznie utrzymuje jego centralną pozycję. Przy wielkich częstotliwościach większość energii jest przenoszona nie przewodem, lecz dielektrykiem (rys. 2). Zatem ten dielektryk powinien charakteryzować się małą przenikalnością elektryczną i niskim współczynnikiem strat energii.
Przenikalność elektryczna substancji wyraża jej zdolność do absorbowania pola elektromagnetycznego w porównaniu z próżnią. Przenikalność elektryczna wszelkich substancji jest wyższa niż równa jedności przenikalność próżni. Zatem im przenikalność substancji jest mniejsza, tym mniejsze są w niej straty energii. Miarą sprawności energetycznej dielektryka jest współczynnik strat energii, która jest tracona w formie ciepła. Współczynnik ten winien być zatem jak najmniejszy.
Jak widać w tabeli 1, optymalnym dielektrykiem do przesyłania energii jest próżnia. A stosowanym w praktyce materiałem, o bardzo małej przenikalności, jest teflon (PTFE) o obniżonej gęstości. Materiał ten jest zwany także ekspandowanym lub mikroporowatym PTFE. Jest on równomiernie wypełniony mikroskopijnymi pęcherzykami powietrza.
Im tych pęcherzyków jest więcej, tym jego gęstość jest mniejsza, a parametry elektryczne lepsze. W stosunku do standardowego PTFE charakteryzuje się niższą przenikalnością elektryczną i niższym współczynnikiem strat, ale wystarczającą do stabilnej separacji przewodnika wewnętrznego od zewnętrznego wytrzymałością mechaniczną.
Ewolucja dielektryka
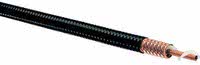
Fot. 3. Kabel koncentryczny z karbowaną folią miedzianą i dielektrykiem powietrznym o niskich stratach. Pozwala też na transmisję dużych mocy. Dystans między żyłą wewnętrzną a płaszczem zewnętrznym zapewniają wkładki z teflonu
Zastąpienie solidnego PTFE ekspandowanym wyzwoliło kolejną ewolucję parametrów kabli współosiowych. Najbardziej rozpowszechnioną techniką produkcji kabli z izolacją PTFE jest spiralne owijanie przewodu centralnego cienką taśmą ekspandowanego PTFE.
Precyzyjny sposób owijania zapewnia kablowi wymaganą średnicę izolatora obejmowanego następnie miedzianym ekranem z drucianej plecionki. Sposób ten pozostawał podstawową techniką produkcji kabli koncentrycznych dla wielkich częstotliwości przez ponad dwie dekady.
Ostatnio technika ta jest zastępowana techniką wyciskania PTFE. Technika ta ma szereg zalet, charakteryzuje się szczególnymi elektrycznymi i mechanicznymi udoskonaleniami. Powiększony obraz przekroju dielektryka DynaCore firmy Dynawave jest pokazany na rysunku 3.
Zwiększona odporność na ściskanie
Wyciskany dielektryczny rdzeń PTFE kabla jest bardziej jednorodny, a jego okrągły kształt jest pięciokrotnie odporniejszy na ściskanie niż rdzeń nawijany. Dane te dla dwóch różnych poziomów nacisku są pokazane w tabeli 2. Przyjęto, że nadepnięcie na kabel przez przeciętnego człowieka wywołuje nacisk ok. 7 kg/cm długości niechronionego rdzenia kabla.
A także, że siła ok. 14 kg/cm długości odpowiada naciskowi obejmy służącej do przytwierdzania kabla. Dzięki zwiększonej odporności wyciskanego rdzenia kablowego jest on mechanicznie wytrzymalszy i jego układanie w trakcie instalacji w systemie staje się łatwiejsze, lżejsze i tańsze.
Mechaniczna giętkość kabla koncentrycznego ułatwia jego wyginanie w trakcie instalowania wzdłuż skomplikowanej nieraz trasy przebiegu. Musi on zachować swoje elektryczne parametry przy minimalnym promieniu zgięcia. W miejscach silnego zgięcia jego przekrój z okrągłego staje się owalny, obniżając na tych odcinkach impedancję falową.
Powoduje to przesunięcie fazowe i zwiększenie VSWR (napięciowy współczynnik fali stojącej). W tabeli 3 podano dla obu rodzajów dielektryka, nawijanego i wyciskanego, jego procentową owalizację przy promieniu zgięcia równemu dwukrotnej średnicy kabla. Widać, że technika wyciskania lepiej utrzymuje okrągłość niż technika nawijania.
Ciasno zginane rdzenie nawijane wykazują rozchodzenie się warstw po stronie zewnętrznej, a ścieśnianie od strony wewnętrznej, co może wywoływać fałdy lub wypukłości. Na rysunku 7 widać nierówności rdzenia nawijanego (po lewej) i gładkość rdzenia wyciskanego (po prawej).
Usprawnienie montażu

Fot. 4. Kabel koncentryczny podwójnie ekranowany: folią i plecionką zapewnia niską emisję pasożytniczą i przesłuchy
Dielektryki nawijane sprawiają trudności w trakcie przygotowywania do montażu wtykowych złączy za pomocą zautomatyzowanych narzędzi ucinających, powodując rozchodzenie się, rozciągnięcia lub rozdarcia zakończenia. Wyciskany izolator PTFE zawsze dobrze zachowuje swój okrągły kształt (rys. 7).
Pozwala sprawniej i szybciej przygotowywać kabel do montażu złączy wtykowych i montować je precyzyjniej z unikaniem poprawek. Ma to szczególne znaczenie dla dokładnego dopasowywania impedancji obwodów wielkiej częstotliwości i minimalizacji VSWR.
Udoskonalone parametry systemu
Produkcja wysokiej jakości niskostratnych kabli koncentrycznych wymaga zaawansowanego projektowania i kontrolowania procesu wytwarzania. Na giętkie kable wielkiej częstotliwości składa się od trzech do siedmiu warstw elektrycznych i mechanicznych, których parametry dla optymalnej współpracy muszą ściśle spełniać wszelkie wymagania.
Wszystkie te warstwy, aż do końcowej postaci kabla w koszulce, powstają w wyrafinowanych urządzeniach według doborowych technologii materiałowych. Dla osiągnięcia najlepszych i powtarzalnych parametrów najważniejsza jest zdolność do eliminacji wszelkiego rodzaju odchyleń w procesie wytwórczym.
Dielektryk odgrywa podstawową rolę dla mechanicznych i elektrycznych parametrów kabla koncentrycznego. Każda możliwość eliminacji wszelkich odchyłek w dielektryku w znacznym stopniu poprawia jego właściwości. Wszystkie omówione parametry wyciskanego PTFE mają również wpływ na obniżenie szumów, wywoływanych przez strukturalny VSWR.
Zakończenie
Współczesne wymagania dla niskostratnych kabli koncentrycznych wysokiej częstotliwości przyczyniły się do licznych innowacji w projektowaniu i technice ich produkcji.
Powstanie wytwarzanego metodą wyciskania ekspandowanego dielektryka PTFE dało projektantom nowe możliwości zaspokajania potrzeb, przez poprawienie wytrzymałości na zgniatanie, zginanie i skręcanie, ułatwiło montaż złączy i obniżyło szumy. (KKP)