Obszar zastosowań czujników i przetworników temperatury jest bardzo szeroki. Wykorzystuje je przemysł spożywczy, w tym piekarnie, suszarnie, zakłady przetwórcze, elektrociepłownie, rafinerie, cukrownie. Korzysta z nich farmacja, zakłady metalurgiczne, są one podstawą współczesnych systemów ogrzewania i klimatyzacji, tworząc w ten sposób bardzo duży, stabilny i jednocześnie na tyle różnorodny rynek, który pozwala na równoległe funkcjonowanie dość dużej jak na warunki krajowe liczby firm dystrybucyjnych i producentów.

Rys.1. Wyniki ankiety obrazujące skalę wzrostu obrotów na przestrzeni ostatniego roku. Aż 46% firm biorących udział w raporcie zanotowało wzrost większy niż 25%
To dlatego, że oprócz szerokiej oferty produktów standardowych na rynku potrzebne są produkty wykonywane na indywidualne zamówienie. Wynika to z ciągłych procesów modernizacji parku maszynowego zachodzących w polskich przedsiębiorstwach, których celem jest automatyzacja procesów przemysłowych i modernizacja.
Trwałość czujników temperatury jest ograniczona, dlatego spory nurt sprzedaży tworzy zapotrzebowanie z działów utrzymania ruchu. To dlatego, że pomiar temperatury w agresywnym środowisku szybko niszczy nawet odporne konstrukcje, co jest wielkim wyzwaniem dla działów rozwoju nieustannie poszukujących nowych materiałów i rozwiązań.
Niniejsze opracowanie na temat czujników i przetworników temperatury jest kontynuacją poprzedniego raportu na ten temat, jaki był opublikowany w Elektroniku 7/2003. Pięć lat przerwy jest na tyle długim okresem, aby można było przyjrzeć się zjawiskom, jakie w tym czasie zaszły na rynku.
Półprzewodniki z daleka od przemysłu
Pomiar temperatury za pomocą termistorów oraz czujników półprzewodnikowych w zastosowaniach profesjonalnych ogranicza się do kilku obszarów związanych głównie z kontrolą klimatu. Cała ogromna reszta zastosowań obejmująca przemysł spożywczy i przetwórczy, energetykę, ciepłownictwo, farmację, przemysł wydobywczy i metalurgiczny i wiele innych podobnych branż jest dla sensorów półprzewodnikowych przez cały czas niedostępna.
Nie chodzi nawet o osiąganą dokładność pomiaru lub też o mniejszy od innych rodzajów czujników zakres pomiarowy, ale głównie o niestandardowość rozwiązań półprzewodnikowych od strony elektrycznej i wykonania mechanicznego, a także niekompatybilność z istniejącym osprzętem, takim jak na przykład moduły kondycjonujące.
Czujniki półprzewodnikowe pojawiają się jako część składowa wchodząca w skład urządzeń OEM, na przykład regulatorów temperatury w systemach wentylacji i ogrzewania pomieszczeń, w motoryzacji, stacjach monitoringu klimatu, układach kontroli stanu urządzeń wbudowanych do wnętrza obudowy i innych podobnych zastosowaniach.
W tych aplikacjach liczą się ich miniaturowe wymiary, łatwość dołączenia do mikroprocesorów oraz wysoka czułość niezmuszająca do każdorazowego stosowania rozbudowanych układów wzmacniających.
Krzemowe czujniki temperatury oraz termistory pojawiają się także w układach zabezpieczających przed niekontrolowanym wzrostem temperatury i prostych regulatorach, na przykład w sterownikach obrotów wentylatora. Są one też stałym elementem rejestratorów temperatury, a zwłaszcza wersji zasilanych z baterii, takich które używa się na przykład do kontroli warunków transportu żywności.
W takich aplikacjach liczy się jak najniższy sumaryczny koszt rozwiązania, co sprzyja typowym układom scalonym dostępnym na rynku. Mimo, że podzespoły elektroniczne to elementy, które nie mają dużych wymiarów, w wielu zastosowaniu okazują się zbyt wielkie, aby mogły zostać umieszczone w cienkiej rurce metalowej, jaka chroni dużą część czujników termoparowych.
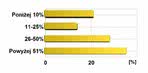
Rys.3. W przypadku 35% przedsiębiorstw, które nadesłały ankiety, czujniki i przetworniki temperatury tworzą ponad połowę obrotów
Takich czynników z pewnością dałoby się wymienić jeszcze kilka i wszystkie po części tworzą defensywną pozycję dla półprzewodników w przemyśle.
Elektroników taka sytuacja z pewnością może dziwić, gdyż przyzwyczailiśmy się do tego, że wszystko co zostanie zelektronizowanie staje się automatycznie lepsze i wypiera dotychczasowe rozwiązania. W przypadku pomiarów temperatury w przemyśle tak się nie stało.
Trudno prognozować, gdzie w perspektywie kilku lat będzie przebiegała linia podziału między dotychczasowymi rozwiązaniami bazującymi na termoparach i termorezystorach i półprzewodnikami, jednak należy przypuszczać, że aktualna pozycja wynika tylko z uwagi na brak dobrej propozycji od strony technologii.
Przełomem mogą stać się rozwiązania bezprzewodowego pomiaru temperatury, które cieszą się coraz większym zainteresowaniem klientów. Jak na razie komunikacja bez kabli bazuje na konstrukcji modułowej urządzeń, w której do całego osprzętu dodano jeszcze jeden obwód odpowiedzialny za łączność. Niemniej coraz częściej istnieje możliwość, aby cały układ elektroniczny czujnika temperatury, łącznie z nadajnikiem bezprzewodowym został zrealizowany w postaci jednego kawałka krzemu. Takie połączenie, bezsprzecznie najlepsze od strony ekonomicznej, może z czasem przebić się na rynku.
Cyfryzacja pomiarów temperatury
Obojętnie czy chodzi o elektronikę konsumencką, sprzęt wojskowy, czy też urządzenia elektroniczne dla przemysłu, wszystkie te branże przechodzą stopniową cyfryzację działania. W przypadku czujników temperatury cyfryzacja jest również dzisiaj jednym z najważniejszych trendów rozwojowych.
Tanie mikrokontrolery o wielkiej wydajności i precyzyjnych układach peryferyjnych wypierają klasyczne konstrukcje bazujące na układach dyskretnych. Podobnie jak w przypadku wielu innych urządzeń, firmy dostrzegły, że korzystniej jest przeprowadzać obróbkę sygnału z czujnika po stronie cyfrowej.
Tym samym przechodzimy do kolejnego etapu wykorzystania mikrokontrolerów w pomiarach temperatury, takiego w którym są one używane nie tylko w roli elementu sterującego działaniem, ale głównego, najważniejszego i często jedynego komponentu aktywnego w układzie. Linearyzacja, kalibracja, uniwersalność we współpracy z wieloma różnymi sensorami daje się zapewnić za pomocą rozbudowanego oprogramowania.
Nie bez znaczenia jest to, że jest to działanie korzystne od strony ekonomicznej i wygodne. Wygoda ta dotyczy zarówno producentów, którzy mogą szybciej dokonywać modyfikacji produktu i dodawać nowe funkcje bez konieczności żmudnego zmieniania układu elektronicznego. Dla użytkowników czujników cyfryzacja objawia się też po stronie „inteligencji” konstrukcji, pozwalającej część czynności wykonać automatycznie.
Skoro w wielu zastosowaniach istnieje konieczność dopasowania czujnika do wymagań danego środowiska pomiarowego, to wiadomo, że najłatwiej można to osiągnąć za pomocą programowania w sprawdzony na wielu produktach. Aby osiągnąć takie cele producenci wbudowują do wnętrza przetworników temperatury mechanizmy cyfrowej transmisji danych między sterownikiem przetwornika systemem nadrzędnym.
Dane cyfrowe nakładane są na analogowe sygnały pętli prądowej, co zapewnia możliwość pracy z wcześniejszymi urządzeniami. Inne rozwiązania opierają się na cyfrowych protokołach komunikacyjnych, gdzie czujnik jest elementem sieci łączącej wszystkie elementy systemu pomiarowego w obiekcie.
Ewolucyjna cyfryzacja zapewniająca szeroko rozumianą uniwersalność przetwornika pomiarowego jest dzisiaj cechą charakterystyczną rynku i wyróżnikiem wielu producentów.