Do głównych czynników rozwojowych sprzyjających rozwojowi produkcji elektroniki w Polsce zaliczyć można dużą liczbę nowych inwestycji w technologie montażowe wspieranych przez fundusze Unii Europejskiej. Rośnie także popularność nowych technologii takich jak: wire bondingm, selektywne lutowanie i pokrycia ochronne. Popyt na nowe grupy materiałów tworzą też najnowsze technologie, takie jak oświetlenie LED i związane z tym inwestycje przemysłowe. Kooperacja w zakresie produkcji elektroniki stała się naszą lokalną specjalnością. W przypadku Polski osią rozwoju rynku i silną kartą przetargową jest też tworzący się pomiędzy Europą Zachodnią a Dalekim Wschodem pomost będący pozytywną siłą napędową gospodarki. Powoli stajemy się zapleczem produkcyjnym w zakresie skomplikowanej i nowoczesnej elektroniki.
Na kolejnych stronach Informatora przedstawiamy szereg szczegółowych analiz dotyczących produkcji elektroniki, w których przyglądamy się sytuacji i zjawiskom panującym w branży produkcji kontraktowej, w sprzęcie technologicznym oraz w materiałach wykorzystywanych w procesach wytwarzania urządzeń.
Kontraktowa produkcja elektroniki - kompleksowa oferta i wysoka jakość gwarancją sukcesu
Najważniejsze czynniki sprzyjające rozwojowi rynku usług produkcji kontraktowej w naszym kraju to oczywiście niższe koszty pracy w Polsce, co przekłada się na tańsze usługi. Liczą się też wysokie kompetencje naszej kadry, wiedza na temat technologii produkcji, dobra jakość i rzetelność krajowych firm. Kolejne czynniki to korzystna lokalizacja Polski na terenie Unii Europejskiej, wzrost znaczenia outsourcingu (kooperacji) w produkcji elektroniki na całym świecie, będący wynikiem rosnącego znaczenia specjalizacji i wzrostu stopnia skomplikowania elektroniki.
Polskie firmy zaczynają powoli odnosić korzyści ze zwiększających się kosztów w firmach azjatyckich, a ich konkurencyjność na rynku światowym jest dzisiaj lepsza niż kilka lat temu. Skutkiem jest częściowy powrót produkcji w nasze rejony. Oczywiście nie byłoby to możliwe bez wielu inwestycji krajowych przedsiębiorstw tego typu w park maszynowy, który w ostatnich 5 latach był szczególnie dynamiczny.
Rośnie też rynek krajowej elektroniki, powstaje wiele małych i średnich firm, które rozpoczynają produkcję seryjną swoich opracowań, tworzą się biura konstrukcyjne, a same usługi montażu dostępne są nawet, gdy zamawiający potrzebuje wykonać małą serię. Dominująca technologia montażu powierzchniowego i ogólne trendy konstrukcyjne są dzisiaj takie, że w produkcji zawsze potrzebne są maszyny, nawet dla jednej sztuki prototypowej.
Kryzys trochę pomaga
Gdy na rynku sytuacja jest nie najlepsza, wiele firm, które nie korzystały z usług firm zewnętrznych, przekonuje się do kooperacji. Przedsiębiorstwa z zagranicy, które trwały latami w ustalonych ramach współpracy z lokalnymi firmami lub też produkowały samodzielnie, szukają dzisiaj szans na obniżenie kosztów, stąd kryzys dla branży kontraktowej najczęściej nie oznacza spadku liczby zleceń. Firmy szukają sposobów poprawy rentowności i nieustannie sprawdzają, co za ile mogą otrzymać. Gdy trend ten dotyczy producentów, którzy do tej pory wytwarzali sami lub firm zagranicznych szukających swoich szans na rynkach położonych na wschód od Odry, można się tylko cieszyć. Ale gdy pytania ofertowe płyną od producentów elektroniki korzystających z usług kontraktowej produkcji, oznacza to niestety presję na obniżenie ceny. Część firm wręcz uważa, że producenci OEM mają absurdalnie wygórowane oczekiwania wobec kosztów usług i wymuszają poziom uniemożliwiający rozwój firmom kontraktowym. Mimo że ceny montażu nierzadko stanowią tylko 1% ceny finalnej urządzenia, nadal są widoczne oczekiwania w kierunku ich redukcji.
Rynek kontraktowy nie jest też ograniczony do obszaru Polski, w zakresie większych serii silną barierą są dla nas oczywiście Chiny, ale dla mniejszych serii realną konkurencją są także firmy rumuńskie i ukraińskie. One w pewnym stopniu ograniczają tempo rozwoju rynku krajowego i nawet jeśli za tamtejszymi usługodawcami nie kryje się zawsze najwyższa jakość, na relacje w kraju z pewnością oddziałują.
Stałe zainteresowanie produkcją własną
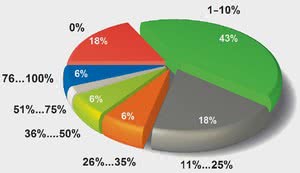
Wiele firm kontraktowych, a zwłaszcza te, które zainwestowały sporo środków w maszyny i urządzenia technologiczne, jest zainteresowana współpracą z partnerami z zagranicy. Polskie firmy są w stanie zapewnić niższe koszty przy niezłej jakości, stąd przy dużej konkurencji i ograniczonej chłonności rynku krajowego otwarcie się na zagranicę wydaje się naturalne. Ale czy poza tą chęcią przekłada się to na jakieś wyniki? Ankieta przeprowadzona wśród firm mówi, że co piąta firma nie eksportuje usług wcale, dla blisko dwóch trzecich zlecenia zagraniczne przynoszą do 25% sprzedaży, czyli mało. Patrząc na to zestawienie od drugiej strony, widzimy, że do powyżej połowy sprzedaży za granicę przyznało się ok. 15% firm. Czyli potencjał do wzrostu w tym obszarze jest duży.
Coraz więcej firm produkcyjnych inwestuje we własne linie produkcyjne, wbrew modzie na outsourcing i nie patrząc na to zagadnienie od strony ekonomicznej. Wynika to w dużej mierze z charakteru i profilu naszego rynku, nastawionego na sprzęt specjalistyczny, na krótkie i średnie serie, częste zmiany oraz modyfikacje w zakresie funkcjonalności produktów. Wielu producentów takich urządzeń woli mieć własny park maszynowy, pozwalający na optymalizację produkcji, bo elastyczność, pełne panowanie nad jakością i produkcją ma dla nich wymiar większy niż obniżki kosztów. Chęć do trzymania produkcji we własnym zakresie to także zaszłość historyczna, wynik istnienia stereotypów w myśleniu wśród kadry zarządzającej i właścicieli oraz co często mówią szefowie firm kontraktowych, skutek niedokładnego liczenia kosztów w firmach, zarówno po stronie produkcji, jak też wynikających ze złej jakości. Niestety małe i średnie firmy są często zarządzane przez kadrę inżynieryjną, skupiającą się na aspektach technicznych i rozwoju produktów od strony technologii. Dla takich osób zarządzanie firmą jest zwykle działalnością drugoplanową, realizowaną metodami chałupnicznymi, patrząc od strony wiedzy i kompetencji menedżerów po studiach w tym kierunku. Stąd produkcja w firmie jest także rozwijana, bo kadra tego chce.
Sprzyja temu coraz większa dostępność i lepsze ceny maszyn do montażu, które mają dzisiaj często funkcje zoptymalizowane pod kątem produkcji niskoseryjnej, o wysokiej elastyczności i niewielkich rozmiarach. W ramach automatu pick & place dostępne są też opcje nakładania pasty lutowniczej, a cała linia technologiczna wcale nie jest taka duża. Producenci elektroniki korzystali w ostatnich latach z możliwości wsparcia finansowego zapewnianych przez wiele funduszy strukturalnych UE, podobnie zresztą jak producenci kontraktowi. Urządzenia kupowane w ramach projektów rozwojowych służyły poprawie potencjału technologicznego, co też wpłynęło na to, że inwestycje w produkcję własną nie są postrzegane wyłącznie przez pryzmat kosztów.
Wpływ rynku międzynarodowego i krajowych OEM-ów
Pozycja firm dalekowschodnich wielu specjalistom wydaje się uprzywilejowana na skutek polityki celnej i rządowej w zakresie wsparcia dla rodzimego biznesu. Małe stawki celne dla elektroniki gotowej importowanej z Chin, w połączeniu z kilkunastoprocentowym cłem na materiały, tworzą preferencje dla tamtejszych usługodawców. Jest to szczególnie widoczne w przypadku większych serii produktów, o które w zasadzie rynek rodzimych krajowych przedsiębiorców nie ma co walczyć.
Ceny usług kontraktowych zbijają też producenci elektroniki, którzy zainwestowali w park maszynowy o dużej wydajności, niezbędny dla własnej działalności. Maszyny praktycznie zawsze mają dużą rezerwę mocy przerobowych, stąd firmy te próbują sprzedać nadwyżki na wolnym rynku. W ich przypadku ekonomia działania ma inny wymiar, bo takie zlecenia traktowane są jako premia w normalnym okresie, a w czasie dekoniunktury sposób na zgromadzenie środków finansowych niezbędnych do opłacenia kosztów stałych przedsiębiorstwa. Innymi słowy producent elektroniki może sprzedać usługi poniżej kosztów i dalej uważać to za opłacalne, bo w ten sposób zmniejsza sobie ew. stratę, przestój. Takie zlecenia zewnętrzne to też element szkolenia kadry i nabywania doświadczenia. Efektem jest przesuwanie progów odniesienia cenowego w dół dla całego rynku.
Nowości pojawiające się w branży kontraktowej
Od mniej więcej pięciu lat większość nowości w usługach kontraktowych można powiązać z rosnącym znaczeniem jakości w produkcji, czyli wzrostem zaawansowania technologicznego, powtarzalności i dokładności procesu technologicznego. Dlatego wiele nowych produktów pojawiających się na rynku związanych jest z kontrolą montażu za pomocą testów optycznych nakładanej pasty lutowniczej, połączeń po lutowaniu, inspekcji rentgenowskiej trudno dostępnych miejsc, na przykład między laminatem a spodem układu w obudowie BGA.
Idąc dalej w tym kierunku, do nowości zalicza się często sprzęt do lutowania selektywnego, w tym takiej operacji dokonywanej na fali oraz do lutowania kondensacyjnego, a więc za pomocą par cieczy. Te operacje dotyczą gęsto upakowanych płytek drukowanych, zawierających elementy przewlekane, wciskane, a także podzespoły o dużych gabarytach. Mimo wielu zalet montażu powierzchniowego, technicznych i ekonomicznych, nadal na płytkach znaleźć można wiele elementów przewlekanych. Są one nieodłączną częścią elektroniki dużej mocy, systemów zasilających, układów wejściowych w systemach pomiarowych i wielu innych aplikacji. Złącza, elementy indukcyjne, tranzystory mocy, moduły, filtry, anteny, ekrany i podobne są montowane ręcznie, stąd większość producentów musi mieć stanowiska do obsadzania takich elementów. Lutowanie selektywne to z pewnością metoda na ograniczenie nakładów pracy ręcznej przy montażu i konieczności utrzymywania w działaniu agregatu do lutowania na fali. Elementy THT można wówczas lutować w jednym cyklu, i jednocześnie uwolnić się od problemów z powtarzalnością montażu ręcznego. Dla producentów montaż THT to źródło kosztów, czynnik negatywny dla jakości (z uwagi na pracę ludzką). Dlatego rozwiązania pozwalające automatyzować operacje THT, w całości lub chociażby w części, cieszą się zainteresowaniem. Na rynku są dostępne automaty pick & place umożliwiające też montaż THT, a wybrane elementy, głównie złącza, są dostępne w wersjach wciskanych.
Inwestycje w jakość to także urządzenia do hermetyzacji elektroniki (zalewanie, lakierowanie i lakierowanie selektywne). W zakresie elementów do nowości zaliczają się urządzenia pozwalające na montaż BGA, układów chip on chip, układanie elementów na podłożach elastycznych.
Nowości na rynku EMS to także usługi powiązane z produkcją, jak badania klimatyczne, kontrola oryginalności elementów oraz wszystkie składniki usługi kompleksowej zleceń: od projektu, wsparcia inżynieryjnego, wykonania (łącznie z PCB) poprzez zakup elementów ich ułożenie po testowanie gotowych podzespołów oraz wysyłkę do klienta, a także serwis i refurbishment. Można więc powiedzieć, że nowością na rynku jest coraz większa integracja usług.
Do nowinek zaliczają się także pomiary czystości jonowej płytek drukowanych, pozwalające ocenić stopień zabrudzenia procesu technologicznego, co ma znaczenie dla zapewnienia niskich upływności oraz odporności na korozję połączeń lutowanych. To także szablony metalowe o zmiennej grubości (stopniowane), które stosuje się na upakowanych płytkach drukowanych po to, aby zapewnić odpowiednią ilość pasty lutowniczej dla dużych elementów i jednocześnie nie powodować zwarć w rejonach o gęstym upakowaniu. Szablony te wykonuje się metodami cięcia laserowego z wykorzystaniem blach stalowych z pocienionymi lokalnie fragmentami.
Przenikanie się obszarów działalności
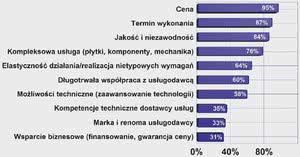
Oczekiwania klientów korzystających z usług firm EMS i CEM wydają się jasno sprecyzowane. Na pierwszej pozycji ulokowała się cena. Odrobinę słabiej oceniono, ale cały czas jako bardzo ważne, termin wykonania i jakość usługi. Warto zauważyć wysokie notowania kompleksowej usługi oraz elastyczności działania, czyli innymi słowy chęci i zdolności organizacyjnej do dopasowania się do nietypowych wymagań i specyficznej sytuacji. Klienci oczekują, że producent kontraktowy będzie pomagał, a nie stawiał warunki i wymagania i wyraźnie oczekują, aby rynek EMS/CEM był "klienta".
Skoro potencjał niektórych firm EMS obejmuje już praktycznie wszystkie etapy wytwarzania urządzeń elektronicznych, nic dziwnego, że niektóre firmy inwestują we własne produkty. Proces ten nie zachodzi w dużej skali, ale pokazuje, jak płynne są dzisiaj granice w biznesie elektronicznym. Dystrybutorzy komponentów podejmują się realizacji usług kontraktowych, z kolei dostawcy takich usług wchodzą na rynek dystrybucji, np. importując niezbędne do projektów elementy. Producenci elektroniki z własnym parkiem maszynowym sprzedają na rynku nadwyżki mocy przerobowych, ale równolegle firmy elektroniczne kupują maszyny po to, aby mieć produkcję pod kontrolą.
Jeszcze do niedawna wydawało się, że producenci elektroniki będą rezygnować z produkcji, zostawiając sobie projektowanie, marketing i sprzedaż, ale wydaje się, że ta koncepcja mało komu przypada do gustu. Pełne zorientowanie na outsourcing to domena raczej nowych firm oraz tych mniejszych, które nie mają pieniędzy na własny park maszynowy, firm, dla których elektronika nie jest głównym biznesem.
Dzisiaj kluczowym zagadnieniem na rynku EMS są komponenty. W kompleksowej usłudze to one w największym stopniu kształtują ceny usług. Dlatego firmy EMS starają się wypracować bezpośrednie kontakty z producentami, dystrybutorami dalekowschodnimi po to, aby mieć lepsze ceny zakupu od tych, które proponuje rynek krajowy.
Przyszłość kontraktowej produkcji elektroniki
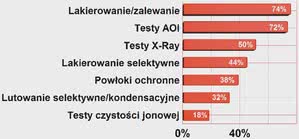
Na wykresie zilustrowano znaczenie poszczególnych nowości, czyli co spośród zyskujących popularność usług w zakresie produkcji elektroniki ma największe znaczenie dla rynku. Zdaniem ankietowanych specjalistów najważniejsze są operacje zabezpieczające przed wpływem środowiska i rozbudowane opcje testowania (AOI, X-Ray). Czyli obojętnie pod jakim kątem patrzy się na rynek i tak zawsze na czoło wysuwają się zagadnienia związane z jakością.
Specjaliści jednym głosem potwierdzają, że usługi EMS to przyszłość produkcji, nie tylko w branży elektronicznej. Na razie rozwój bazuje głównie na tym, że sam rynek elektroniki rośnie. Ale duża liczba firm tego typu w kraju, z czego wiele powstało w ostatnich latach i coraz większa konkurencja powodują spadek cen i wzrost wymagań klientów. Niedługo dostarczenie produktu w określonym terminie, o odpowiedniej jakości, we właściwej cenie, z wydłużonym terminem płatności nie będzie już wystarczające. Producenci EMS będą musieli przyjąć większą odpowiedzialność za produkt końcowy. Pośrednio będzie to też skutek nacisku na kompleksowość, w tym projektowanie elektroniki. Coraz większe skomplikowanie urządzeń, mniejsze rastry, wielowarstwowe płytki będą kierować zainteresowanie klientów ku dostawcom usług zapewniających pomoc w tym obszarze, a więc firmy specjalizujące się tylko w montażu będą tracić swoje atuty. To już widać po tym, ile projektów jest niedostosowanych do produkcji, wymagających konsultacji, zmian technologicznych i pracy konstruktorskiej.
Obwody drukowane - połączenie produkcji płytek z montażem kontraktowym i projektowaniem tworzy poszukiwane na rynku usługi kompleksowe
Rynkowi obwodów drukowanych w Polsce sprzyja ogólny rozwój branży elektronicznej, a zwłaszcza powstawanie małych i średnich firm produkujących specjalistyczne urządzenia przemysłowe i użytkowe. Małe i średnie serie nierzadko lokują się poza zainteresowaniem dostawców z Chin i tym samym dają szansę na zbalansowanie trudnych relacji pomiędzy krajowymi producentami a importerami. Takie specjalistyczne urządzenia wymagają często modyfikacji i modernizacji konstrukcji, konieczności szybkiego przygotowania prototypu lub wersji indywidualnie dopasowanej do wymagań odbiorcy. W takich przypadkach korzystniej kontaktować się z lokalnym producentem niż czekać na dostawę z Dalekiego Wschodu.
Na rynek krajowy trafiają też zlecenia produkcyjne od firm zagranicznych. Firmy EMS muszą gdzieś zamówić do nich płytki, nierzadko u lokalnych wytwórców, którzy mają produkcję certyfikowaną pod względem jakości i są w stanie w krótkim czasie dostarczyć obwody drukowane. Przy widocznych obecnie trendach do maksymalnego skracania czasu wprowadzania produktu na rynek, w praktyce zawsze na montaż zostawia się minimum czasu, dlatego wiele krajowych firm EMS, chcąc sprostać różnym wymaganiom klienta, współpracuje z kilkoma producentami krajowymi i importerami PCB, elastycznie korzystając z ich możliwości.
Korzystny dla branży jest też wzrost kosztów produkcji w Azji, który hamuje trend przenoszenia produkcji elektroniki w tamte rejony oraz daje szansę krajowym producentom PCB na zlecenia.
Problem jest jeden, ale za to dotkliwy
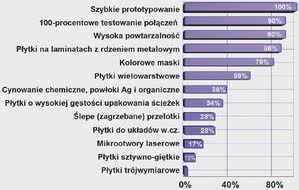
Co jest potrzebne krajowym firmom w zakresie obwodów drukowanych oraz jakie usługi spośród nowości są bardziej popularne? Klienci oczekują głównie szybkiego prototypowania płytek, pełnego testowania i wysokiej powtarzalności, a więc innymi słowy zapewnienia jakości. Na bardzo wysokiej czwartej pozycji są obwody na laminatach z rdzeniem metalowym, co przekonuje po raz kolejny, że sektor oświetlenia LED jest oczkiem w głowie wielu krajowych producentów.
Bez cienia wątpliwości największym problemem krajowego rynku obwodów są płytki drukowane z Dalekiego Wschodu. Nie jest to temat dla rynku nowy, który pojawił się w ostatnich kilku latach, ale o ile jeszcze 5 lat temu można było dyskutować na temat siły oddziaływania tego zjawiska na rynek i wskazywać, że w zasadzie dotyczy on wąskiego obszaru zastosowań i kilku firm zajmujących się importem płytek do Polski, to obecnie widać, iż import doszedł do takiej skali, że silnie oddziałuje na biznes.
Jeszcze pięć lat temu płytki importowane trafiały do specjalistycznych aplikacji, tam gdzie potrzeba było zapewnić wiele warstw ścieżek, wysoką gęstość upakowania ścieżek, ślepe przelotki i podobne nowinki. Takich płytek w kraju się nie wytwarzało z uwagi na ogromne koszty technologiczne lub potencjał produkcyjny był niewystarczający pod względem wydajności, terminu wykonania i jakości. Dzisiaj importuje się także płytki o mniejszej skali złożoności, w tym te najpopularniejsze obwody 4- i 2-warstwowe, a linia podziału między rynek zajmowany przez producentów krajowych i importerów przebiega przez wielkość zamówienia, cenę i termin wykonania. O ile te złożone płytki były w sumie korzystne dla rynku, o tyle proste obwody wyróżniają się wyłącznie ceną, a to już dla żadnej branży nie jest zjawisko pozytywne.
Płytki z Chin są konkurencyjne w wielu obszarach rynku z uwagi na trudności w dotrzymaniu tempa rozwoju ze strony firm o mniejszej wielkości. Produkcja PCB jest bardzo kapitałochłonna, a wprowadzanie nowych rozwiązań i technologii wymaga niestety dużych inwestycji, na które stać tylko największych graczy. Nowe urządzenia, zapewniające odpowiednią wydajność, powtarzalność parametrów i dobry uzysk, a także pozwalające na miniaturyzację elektroniki, przekładającą się na coraz większe upakowanie elementów ścieżek i otworów, są po prostu bardzo drogie. Ich kupno i eksploatacja ma sens, gdy firma może koszt rozłożyć na wiele metrów kwadratowych płytek, a niestety ostatnie pięć lat w gospodarce to okres, kiedy relacje są naznaczone kryzysem i spadkami sprzedaży.
Nacisk na obniżanie ceny, spadek zamówień nie sprzyjają możliwości amortyzacji drogich inwestycji, tym samym presja konkurencyjna ze strony importerów obwodów azjatyckich się nasila. Efekt jest taki, że pomijając wyjątki, produkcja w kraju ogranicza się dzisiaj do małych i średnich serii. Duże zamówienia wykonywane są w Chinach. Wzrosła też liczba firm zajmujących się importem płytek, duża aktywność tamtejszych agentów i pośredników, którzy nieustannie spamują skrzynki pocztowe ofertami, powoduje, że płytki importują także bezpośrednio producenci elektroniki.
Coraz większą aktywność na rynku przejawiają pośrednicy, którzy biorą na siebie cały ciężar kontaktów z azjatyckimi producentami i ryzyko handlowe. Ich lokalne biura aktywnie szukają klientów, konkurują z producentami i między sobą. Nie zmieniają one układu sił na rynku, jeśli chodzi o oferty handlowe, ale z pewnością przyczyniają się do poszerzenia dostępności i zmniejszenia ryzyka handlowego.
Komu najbardziej dokuczają płytki importowane?
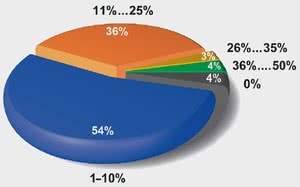
Ilustracja, jaką część sprzedaży krajowi producenci uzyskują z zagranicy. W ostatnich trzech latach sprzedaż ta nieco wzrosła. Nie jest to jakiś wielki i przełomowy skok, ale widać wyraźnie, że zmalała liczba firm, które nie eksportowały płytek wcale lub bardzo mało, a wzrosła grupa tych, które z eksportu miały ok. 25% sprzedaży. Dane te mogą sugerować, że firmy przyciśnięte konkurencją ze strony importerów PCB zostały zmuszone do takich działań.
Wydaje się, że najwięksi krajowi wytwórcy umiejętnie i skutecznie bronią się przed opisanymi negatywnymi zjawiskami. Widać to po tym, że inwestują w nowe maszyny i rozwijają technologię produkcji w kierunku większej wydajności. Swoją aktywność kierują w stronę rynku krajowego i Europy Zachodniej, proponując przede wszystkim dużą szybkość realizacji usług, wysoką jakość, elastyczne podejście do wymagań klienta, błyskawiczne prototypowanie i podobne usługi wykorzystujące bliskość geograficzną.
Kilka firm równolegle do produkcji płytek oferuje też usługi montażu kontraktowego (np. Techno-Service, Kompania, Printor). To z pewnością jest dobra metoda na poprawę rentowności w zakresie produkcji PCB i szansa na dotarcie do innej grupy klientów za pomocą kompleksowej usługi produkcyjnej.
Gorzej z producentami średniej wielkości, tymi którzy bazowali przez lata na rynku krajowym i wytwarzali obwody 1-i 2-warstwowe. Dla nich cenowa konkurencja dalekowschodnia jest bardzo dokuczliwa, bo zmusza do konkurowania wyłącznie niską ceną, a jednocześnie minimalne marże odbierają większość szans na rozwój i skazują na stagnację w biznesie.
Wydaje się, że penetracja i siła oddziaływania konkurencyjnego ze strony firm chińskich sięga już maksimum i dalej się nie powinna posunąć. Wskazuje na to kierunek zmian w kosztach produkcji po tamtej stronie oraz to, że coraz liczniej importowane są płytki słabe. Azja nie zawsze oznacza dobrą jakość i w pogoni za niską ceną ta ostatnia coraz częściej spada poniżej akceptowalnego poziomu i na rynku jest wiele firm, które oferują marne importowane obwody drukowane. Jest to typowy trend biznesowy - importerzy, którzy wyczuli wcześnie ten trend i nawiązali kontakty w dobrymi producentami w Azji po to, aby zaoferować niedrogie produkty zaawansowane technicznie, nie mają problemów z jakością. Takie firmy z reguły nie zajmują się płytkami 1- i 2-warstwowymi. Ale w ślad za nimi poszło wielu naśladowców, których nie fascynuje technologia, ale duża marża handlowa, która często jest najważniejsza.
Szansą dla firm krajowych jest właśnie dobre zbalansowanie współczynnika ceny do jakości, postawienie na szybką obsługę, także w zakresie błyskawicznego prototypowania i nieustanne zdobywanie nowych klientów. Elektronika jest sektorem nieustannie się rozwijającym, a krajowa branża PCB ma dobre opinie na temat kwalifikacji technologiczno-technicznych. Wydaje się, że sensowne jest poszerzanie usług o montaż, jeśli nie samodzielnie, to przez bliskie kontakty i ścisłą współpracę z firmami kontraktowymi, a także rozszerzenie biznesu o usługi inżynierskie związane z płytkami, na przykład projektowanie obwodów, przeprojektowanie i modernizacje starszych projektów lub weryfikację technologiczną.
Produkcja obwodów drukowanych to bardzo trudny sektor do konkurowania, ale gdy kryzys w gospodarce odpuści, branża powinna złapać oddech. Nadzieję można też pokładać w nowych, szybko rozwijających się sektorach, jak na przykład oświetlenie LED. Większość firm dostarcza płytki drukowane na laminatach z rdzeniem aluminiowym, które stanowią bazę dla modułów oświetleniowych, ale gorzej wygląda oferta z szybkim prototypowaniem.
Nowości
Do nowości na rynku PCB można zaliczyć obwody elastyczne, nowe podłoża do układów w.cz. i oczywiście bardzo popularne płytki z radiatorem aluminiowym lub konstrukcje związane z zarządzaniem ciepłem w obwodach drukowanych. Płytki z rdzeniem metalowym pojawiają się w ofertach większości firm produkujących obwody drukowane, a ich względnie duża dostępność powoduje, że coraz chętniej są stosowane także w innych aplikacjach profesjonalnych. Wykonywane są też konstrukcje specjalne, ale wymagają one dużego doświadczenia i wiedzy w zakresie obróbki niestandardowych materiałów.
Oferta technologiczna producentów płytek zawsze odzwierciedla faktyczne zapotrzebowanie rynku i pomijając badania naukowe, nie zdarza się, aby producent inwestował w urządzenia i technologię, w przypadku braku portfela zamówień. Ale z kolei potrzeby klientów biorą się z tego, co dzieje się w podzespołach, a dokładniej w malejących rozmiarach obudów.
Zlecenia eksportowe
Skoro w Polsce udało się zrealizować koncepcję bycia zapleczem produkcyjnym dla Europy Zachodniej w zakresie usług produkcyjnych, to można by snuć nadzieję, żeby nasz kraj stał się także zapleczem dla obwodów drukowanych, dzięki którym ich producenci mogliby korzystać z atutów bliskości, jakości i elastyczności operacyjnej do rynków sąsiednich. Potwierdza to, że wielu producentów pokłada nadzieje w eksporcie i stara się wykorzystać możliwości i szanse, jakie daje wspólny europejski rynek.
O ile chęci zawsze były, o tyle z praktycznymi działaniami przez wiele lat był już problem. W ankietach przeprowadzanych przy okazji opracowywania kolejnych edycji raportu poświęconego PCB zawsze udział eksportu w całkowitej sprzedaży krajowych producentów wypadał bardzo słabo i dla większości firm nie przekraczał zwykle 5%. Wyjątki, dla których eksport płytek za granicę nie był dziełem przypadku, można było policzyć na palcach jednej ręki. Przyczyną tego rozdźwięku było to, że eksport w praktyce opierał się na transakcjach okazyjnych, bo rynek krajowy dla wielu naszych firm był wystarczająco chłonny, a na dodatek wyjście z produktem poza granice Polski wymaga niestety zapewniania porządnej jakości, często popartej certyfikatami oraz raczej dotyczy tych bardziej skomplikowanych płytek. Stąd firmy średnie eksportowały, gdy trafiła się okazja, a mali producenci nie zajmowali się zagranicą wcale.
Importerzy płytek
Krajobraz firm na rynku obwodów drukowanych zmienia się rzadko, a większość z firm produkcyjnych jest obecna w branży od dawna lub nawet od bardzo dawna. Zmiany w ostatnim okresie to raczej ruchy na plus, bowiem przybyło importerów, a producenci utrzymali swoją liczność i potencjał.
Jeśli chodzi o importerów płytek, to są nimi dystrybutorzy podzespołów tacy jak Elhurt, Masters i Andpol. Firmy te w ostatnich latach rozszerzyły swoją działalność o usługi montażu i dzisiaj proponują swoim klientom kompleksowe usługi produkcyjne obejmujące komponenty, płytki i układanie podzespołów, a niekiedy także projektowanie i przeprojektowanie płytek. Dla wielu klientów możliwość przekazania starego urządzenia elektronicznego do modernizacji, np. w celu zmiany technologii na SMT, jest cenną możliwością. Na rynku jest coraz więcej firm słabo związanych z elektroniką a mimo to zmuszonych do elektronizacji swoich wyrobów. Dla nich kompleksowe usługi wydają się modelowo skrojone pod potrzeby.
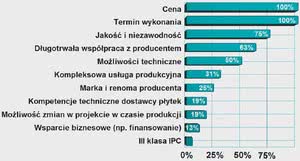
Ocena czynników składających się na ofertę handlową wraz ze skalą ich ważności. Najważniejsza jest oczywiście cena i termin wykonania. Kolejny istotny czynnik to jakość, ale znaczące wskazania dostały też kryteria związane z możliwościami technicznymi, długotrwałą współpracą z producentem a także kompleksową usługą produkcyjną. Znaczenie tego ostatniego kryterium w kolejnych latach może jeszcze wzrosnąć, bo stale rozwijający się sektor EMS w cięższych czasach będzie wchłaniał więcej zleceń produkcyjnych z kraju i zagranicy. Producenci PCB mogą więc dostarczać im obwody do produkcji lub inwestować w potencjał produkcyjno-projektowy u siebie.
Płytki drukowane z importu oferuje również firma SoftCom. Specjalizuje się w dostawach wielowarstwowych obwodów drukowanych dla zaawansowanej elektroniki profesjonalnej oraz szybkim wykonywaniu projektów prototypowych. Od niedawna SoftCom oferuje również klientom usługę produkcyjną nastawiając się na krótkie serie.
Osobną kategorią firmy importowej jest NCAB, który jest pośrednikiem pomiędzy wieloma fabrykami PCB na Dalekim Wschodzie a klientami w Europie. Niemniej duża skala działania firmy daje jej możliwość współpracy z producentami pracującymi na wyłączność NCAB, co sprzyja szybkiej obsłudze, dobrej ofercie i pozwala zachować nadzór nad jakością. Sieć lokalnych biur zapewnia obsługę klienta i rozliczenia.
W ostatnich kilku latach grono importerów poszerzyło się o firmy takie jak Profill, Solitech i Technosystem oraz 3E (firmy kontraktowe), Sidus i Propox (producenci). Płytki drukowane oferują też dostawcy katalogowi jak RS Components i Farnell element 14. Oferta bazuje na współpracy z zewnętrznymi partnerami (dla Farnella to Eurocircuits) i pozwala np. zamówić płytkę bezpośrednio z programu Eagle.
Producenci krajowi
Największe firmy krajowe dysponują dużym potencjałem produkcyjnym, wykonują samodzielnie płytki wielowarstwowe, a sporą część produkcji wysyłają na eksport. Wszystkie firmy z tej grupy to przedsiębiorstwa obecne na rynku od kilkudziesięciu lat. Takie firmy to m.in. Techno-Service, Eldos, Hatron i Kono. W dalszej kolejności można wymienić także Eltar, Faldruk, Norel, Unidruk, a także mniejsze firmy jak Elpin, Elmax i inne. Wśród producentów płytek drukowanych znajdują się firmy, które uzupełniają produkcję PCB montażem kontraktowym. Są to Kompania Elektroniczna i Printor.
W raporcie uczestniczy także Instytut Tele- i Radiotechniczny wytwarzający prototypy, krótkie i średnie serie płytek i pakietów elektronicznych o wysokim stopniu precyzji. Działalność ta jest pochodną prac naukowych Instytutu, który zajmuje się tematyką obwodów drukowanych.
Urządzenia technologiczne do produkcji elektroniki - niezbędne dla firm EMS, do zapewnienia jakości i wysokiej konkurencyjności na rynku
Potencjał urządzeń i sprzętu technologicznego do produkcji elektroniki określają w dużej mierze popularność usług montażu kontraktowego, wzrost zainteresowania jakością produkcji, coraz większe otwarcie na rynki zagraniczne, presja na minimalizację kosztów w produkcji i ogólny szybki wzrost złożoności urządzeń. Bycie konkurencyjnym na rynku elektroniki wiąże się dzisiaj ze stałymi inwestycjami w park maszynowy, dlatego zainteresowanie sprzętem technologicznym zawsze będzie duże.
W ostatnich pięciu latach najważniejszym czynnikiem sprzyjającym rynkowi sprzętu technologicznego do produkcji elektroniki były z pewnością fundusze rozwojowe UE i analogiczne programy wsparcia zakładające poprawę stopnia zaawansowania technologicznego i konkurencyjności na rynku dla małych i średnich przedsiębiorstw. Skorzystało z nich wiele firm elektronicznych, dla których niewielki wkład własny, wsparty kredytem banku i dotacją z UE stał się filarem rozwoju i szansą wybicia się.
Dobrej koniunkturze sprzyja też korzystna sytuacja w krajowej branży elektroniki i zlecenia montażowe płynące z zagranicy. Polska korzysta tutaj ze swojej bliskości do rynków skandynawskich i Europy Zachodniej oraz tego, że jesteśmy postrzegani jako kompetentne i niedrogie zaplecze produkcyjne dla bogatych krajów europejskich.
Korzystny wpływ na relacje mają też nowe, szybko rozwijające się technologie (np. lampy LED, urządzenia związane z odnawialną energią), pod których produkcję kupuje się specjalizowany sprzęt. Na kolejne lata optymizmem napawa tendencja odwrotu od zlecania produkcji w krajach Dalekiego Wschodu. Szczególnie dotyczy to produkcji małoseryjnej i średnioseryjnej specjalistycznej, a więc tej, w której chcemy się specjalizować.
Wymagania odbiorców (zagranicznych i krajowych) co do technologii i jakości także cały czas rosną, przez co starsze urządzenia do produkcji są stopniowo wymieniane na nowe. W miarę upływu lat dynamika tego procesu jest coraz większa. Proces ten zachodzi też poprzez dokładniejsze wymogi klientów realizowane przez audyty, którzy dokładnie sprawdzają, czy zapewnienia producenta EMS mają pokrycie w rzeczywistości.
Nieustanne zainteresowanie jakością
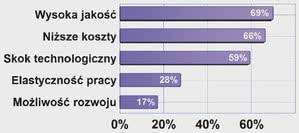
Ocena wagi poszczególnych czynników skłaniających firmy do inwestycji w park maszynowy potwierdza wysokie znaczenie jakości w elektronice, długofalowego rozwoju firmy oraz jej przewagi konkurencyjnej. Duże znaczenie maszyn i sprzętu technologicznego dla rozwoju przekłada się też na pozycję i postrzeganie przez rynek dostawców tych produktów. Firmy te, zwłaszcza zajmujące się tylko tytułową tematyką, są traktowane jako źródło postępu, technologii i wiedzy przekazywanej od producentów do klientów.
Wiele nowości rynku urządzeń technologicznych do produkcji elektroniki wiąże się ze wzrostem znaczenia jakości. Firmy skupione w naszej branży interesują się, inwestują posiadane kapitały i przykładają dużą uwagę do rozwoju posiadanej technologii produkcji w stronę jej większego zaawansowania, powtarzalności, dokładności i precyzji, a także do minimalizacji braków i problemów technicznych powstających przy produkcji. Trend ten wyraźnie widać w stale rosnących wymaganiach technicznych odbiorców zagranicznych i krajowych, rosnącej liczbie firm na rynku, które stawiają na zaawansowane technologie oraz w strukturze sprzedaży krajowych dostawców sprzętu do produkcji.
Presja na jakość to także wynik tego, że od lat krajowi producenci elektroniki wspierają swoją działalność za pomocą wielu funduszy i programów rozwojowych Unii Europejskiej. Można nawet pokusić się o twierdzenie, że zdecydowana większość nowych inwestycji wykorzystuje jakieś dofinansowanie, a ponieważ takie wsparcie kierowane jest w stronę poprawy konkurencyjności na rynku, domyślnie pieniądze wydawane są na nowe urządzenia.
Nowości
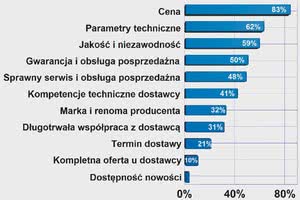
Zestawienie najważniejszych kryteriów branych pod uwagę przy selekcji dostawcy nie jest zaskakujące. Podobnie jak w wielu innych analizowanych sektorach rynku, tutaj także na czołowym miejscu znalazła się trójka łącząca cenę, parametry techniczne oraz jakość. Ale już kolejne dwa kryteria określające ogólnie obsługę posprzedażną są tu znaczącym wyróżnikiem, pokazującym dobitnie, że w tym obszarze zakupy nie są dziełem przypadku, tylko drobiazgowych kalkulacji. Natomiast małe znaczenie terminu dostawy wiąże się z tym, że inwestycje w park maszynowy planowane są zazwyczaj z dużym wyprzedzeniem.
Zainteresowanie poprawą jakości produkcji widać w każdym przypadku, gdy pyta się dostawców o nowe produkty i co cieszy się rosnącą popularnością. W znakomitej większości firmy wymieniają wówczas wizyjne systemy inspekcji, testery funkcjonalne, sprzęt do inspekcji AOI i X-Ray oraz pasty SPI. Urządzenia te pozwalają na szybką i wnikliwą kontrolę poprawności montażu pakietów, zwłaszcza gdy płytki zawierają układy BGA oraz microBGA, małe elementy o rozmiarze 0201 albo i 01005.
Postęp w elektronice szybko przenosi się na sferę produkcji, gdyż nowe miniaturowe elementy elektroniczne, także te w obudowach bezwyprowadzeniowych, coraz liczniej i częściej pojawiają się na płytkach. Wiele nowych funkcji i możliwości staje się dostępnych właśnie dzięki temu, że w projektach wykorzystano nowe elementy, a aby je montować, testować, czyli po prostu wykorzystywać, trzeba mieć stosowny sprzęt. To samo dotyczy większej wrażliwości nowoczesnej elektroniki na zaburzenia, wpływ środowiska, narażenia mechaniczne, upływ czasu i podobne czynniki, które są konsekwencją rosnącej złożoności układów elektronicznych, szybkiej miniaturyzacji oraz pokrewnych im trendów, takich jak coraz niższe napięcia zasilania, większe częstotliwości pracy i podobne.
Większa wrażliwość elektroniki na wpływ środowiska leży u źródła rosnącej popularności kolejnego segmentu urządzeń, jakim jest sprzęt do selektywnego nakładania powłok ochronnych (konforemnych), lutowania selektywnego i kondensacyjnego. Zainteresowanie takimi technologiami to efekt rosnącej złożoności płytek drukowanych, które zawierają obok siebie wiele różnych elementów elektronicznych, w tym tych montowanych powierzchniowo i technologią przewlekaną, takich gdzie obok siebie umieszczone są małe i duże elementy itp. Sprzęt do lakierowania pozwala zabezpieczyć płytki przed wpływem środowiska.
Producenci sprzętu technologicznego nieustannie analizują takie obszary, szukając możliwości automatyzacji i ulepszenia technologii w produkcji. Przykładem, że wyniki takich działań pojawiają się na rynku, mogą być nowe wielogłowicowe automaty montażowe, w których poza układaniem podzespołów SMT dodatkowo zapewniono możliwość montażu elementów przewlekanych lub łączących montaż SMT z nakładaniem pasty i kleju. W ten sposób zamiast kilku urządzeń wystarcza jedno.
Wzrost zaawansowania technologicznego widać w każdym obszarze rynku związanym z montażem komponentów, na przykład urządzeniami do inspekcji pasty w trzech wymiarach, montowaniem układów w technologii PoP (Package over Package), pracą na płytkach drukowanych o dużych rozmiarach przekraczających 1 metr. Rośnie zainteresowanie dodatkowymi możliwościami urządzeń, np. w automatach montażowych pomiarem siły nacisku ssawki, weryfikacją komponentów, inteligentnymi podajnikami, funkcjami traceability i podobnymi udogodnieniami.
Własny park maszynowy oczkiem w głowie
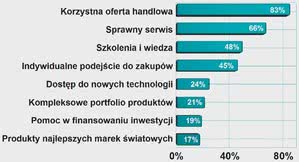
Oczekiwania, jakie mają firmy OEM w stosunku do dostawców sprzętu i urządzeń. Na pierwszej pozycji znalazła się dobra oferta cenowa, ale zaraz poniżej był to już serwis i obsługa posprzedażna, szkolenia i wsparcie techniczne, a także indywidualne podejście do potrzeb danej firmy. Innymi słowy, kupujący w opisywanej branży oczekują od dostawców nie tylko produktów, ale wartości dodanej związanej z technologią. Idealny dostawca nie tylko powinien sprzedać najlepiej pasujący w danych okolicznościach sprzęt, ale również nauczyć producenta, jak wykorzystać jego możliwości.
Coraz więcej producentów elektroniki inwestuje we własne linie produkcyjne, ograniczając w ten sposób zlecenia dla dostawców EMS. Ma im to przynieść oszczędności, lepszą jakość, większą elastyczność a przez to zapewnić wzrost konkurencyjności wyrobów. To zjawisko wydaje się w pewnej opozycji do trendu outsourcingu, który miał zdominować produkcję elektroniki. Rosnąca złożoność płytek drukowanych, coraz mniejsze i delikatniejsze elementy miały stopniowo zmieniać proporcje pomiędzy produkcją we własnym zakresie i kontraktową na korzyść tej ostatniej. Niemniej nie widać, aby taki proces stawał się dominującym trendem, bo wielu producentów rozbudowuje swoje parki maszynowe, widać też przypadki, że są firmy, które po osiągnięciu odpowiedniej skali działania inwestują we własne działy produkcji.
Powodów, że tak się dzieje, jest kilka i jeden z nich, dotyczący chęci lepszej kontroli, możliwości szybkich zmian w wytwarzanym asortymencie i szybkiego reagowania na potrzeby rynku, cały czas jest podnoszony od lat. Do tego dochodzi to, że podobnie jak firmy kontraktowe, tak samo producenci elektroniki mogą korzystać z dotacji i wsparcia ze strony funduszy i programów rozwojowych, przez co zakupy linii technologicznej na własne potrzeby stały się celem osiągalnym i realnym. Za trzeci czynnik może być uznana coraz lepsza i bardziej konkurencyjna oferta rynku w zakresie sprzętu produkcyjnego, dzięki której podstawowy zestaw o niewyszukanych możliwościach daje się kupić za stosunkowo niewielkie pieniądze. Producenci w ostatnich latach wprowadzili na rynek też szereg urządzeń skonstruowanych specjalnie pod potrzeby małych firm produkcyjnych.
Dostawcy sprzętu technologicznego
Najbardziej znaczącą grupę dostawców tworzą przedsiębiorstwa posiadające szeroką i kompletną ofertę urządzeń do produkcji, dla których zasadniczą część działalności stanowi sprzedaż urządzeń do montażu podzespołów. Każda z takich firm jest powiązana zwykle z jednym producentem maszyn pick & place, dostawcą pieców, sitodrukarek i innych grup. Największe firmy mają w takich obszarach więcej niż jednego dostawcę, ale tak dobranych, aby firmy nie były do siebie w opozycji.
Najczęściej wiodącym partnerem dla firm dystrybucyjnych jest producent automatów montażowych. Nierzadko, gdy firma wytwarza także inne składniki linii produkcyjnej, wokół niej kręci się cały biznes. Takie firmy w tym zestawieniu to Ambex, Amtest, CPS-IEP, Essemtec, Interflux, New Comp Polska, PAKT Electronics, PB Technik, Renex, Scanditron, RobTools, SMT-TECH.
Poza wymienioną grupą funkcjonują firmy specjalistyczne skupiające się na wybranych dziedzinach, na przykład urządzeniach do nakładania powłok ochronnych oraz lutowania selektywnego (AMB Technic, CH Ersbloech, APCom) lub innym sprzęcie, z zasady niezwiązanym bezpośrednio z montażem podzespołów. W przypadku tych firm oferta dystrybucyjna jest tu najczęściej uzupełnieniem innej działalności. Takie firmy to WG Electronics, sprzedający specjalistyczne automaty do produkcyjnego programowania pamięci Flash, mikrokontrolerów i innych elementów, testery boundary-scan, liczarki i pakowarki podzespołów. W grupie tej sklasyfikować można także producentów szablonów metalowych (Semicon) i sprzedawcę maszyn do ich produkcji (SE Spezial). Specjalistycznym dostawcą jest także PCB Technology, oferująca maszyny do produkcji PCB.
W zestawieniu nie może zabraknąć firmy Mechatronika - jedynego krajowego producenta urządzeń, takich jak automaty i półautomaty do montażu SMD, piece do lutowania rozpływowego, dozowników pasty i kleju, drukarek szablonowych. Drugim producentem jest białostocka firma Neotech, projektująca i wytwarzająca maszyny do produkcji cewek i dławików (nawijarki, urządzenia pakujące, urządzenia cynujące, urządzenia pomiarowo-monitorujące oraz kompletne linie produkcyjne).
Kolejną grupą są przedsiębiorstwa mające ofertę skierowaną w stronę serwisów, odbiorców związanych z pomiarami, kontrolą i testowaniem, a także oferujące narzędzia ręczne i urządzenia uzupełniające podstawowe elementy linii technologicznej. Przykładem jest tu Biall, sprzedający sprzęt serwisowy do napraw PCBA, Labem, Lenz, RobTools oraz firmy katalogowe (Conrad, Farnell).
Na koniec warto wymienić firmy, które w zakresie tematyki raportu specjalizują się w dostawach mebli i wyposażenia produkcji (Treston) i dostawców stopów lutowniczych (Cynel, Lenz, Solder Chemistry).
Materiały do produkcji elektroniki - wzrost świadomości firm elektronicznych podstawą rozwoju
Materiały do produkcji elektronicznej to duża i różnorodna grupa produktów, która oferowana jest w kraju przez kilkadziesiąt firm dystrybucyjnych i produkcyjnych. Wyroby te na rynku mają spore znaczenie, co wynika w dużej mierze z pozycji, jaką na naszym rynku zajmuje montaż kontraktowy. Jest to także pochodna wielu zmian i trendów, które najłatwiej można określić jako wzrost znaczenia jakości i zaawansowania technologii we współczesnej elektronice. Rynek materiałów cechuje się także wysokim stopniem specjalizacji i dużą liczbą ciekawych nisz technologicznych, pozwalających rozwijać biznes nawet małym, ale wąsko specjalizowanym dostawcom przy silnej konkurencji.
Rozwój rynku materiałów i usług związanych z produkcją to w największym stopniu pochodna szybkiego rozwoju samej elektroniki. Wraz z tym, jak rośnie rynek, pojawia się coraz większe zapotrzebowanie na materiały wykorzystywane podczas produkcji i jest to naturalny proces w branży. Pomagają też takie czynniki jak wzrost zaawansowania technologicznego urządzeń i coraz wyższe wymagania techniczne stawiane przed urządzeniami elektronicznymi. Wraz z nimi pojawia się konieczność realizacji dodatkowych operacji podczas produkcji, na przykład lakierowanie, zalewanie, wzmacnianie, zabezpieczanie, oznaczanie. Każda z takich czynności wiąże się z wykorzystaniem specjalistycznych materiałów oraz często także sprzętu służącego do nakładania i dystrybucji materiałów chemicznych.
Postępująca miniaturyzacja, coraz większa złożoność układowa, spory udział w rynku układów zasilanych niskimi napięciami, a nawet duża liczba interfejsów komunikacyjnych powodują, że wrażliwość współczesnych układów elektronicznych na wyładowania elektrostatyczne lub narażenia mechaniczne jest dzisiaj znacznie większa niż dawniej. Współczesna elektronika jest delikatna mechanicznie i wrażliwa elektrycznie, przez co produkcja wymaga poświęcenia uwagi na zabezpieczenie i ochronę układu podczas eksploatacji przed narażeniami.
W procesie rozwoju rynku pomaga też coraz większe otwarcie się naszych producentów OEM i EMS na eksport, bo zwykle wymagania partnerów zagranicznych wymuszają dbanie o wiele zagadnień związanych z wysokim poziomem technicznym i odpornością środowiskową urządzeń.
Zainteresowanie jakością
Zapotrzebowanie na materiały i usługi produkcyjne bardzo często jest silnie powiązane ze wzrostem znaczenia jakości w produkcji elektroniki. Firmy skupione w naszej branży inwestują i przykładają dużą wagę do rozwoju posiadanej technologii produkcji w stronę jej większego zaawansowania, powtarzalności, dokładności i precyzji, a także w kierunku minimalizacji braków i problemów technicznych powstających przy produkcji. Trend ten wyraźnie widać w stale rosnących wymaganiach technicznych, powiększającej się liczbie firm na rynku, które stawiają na zaawansowane technologie.
Na zainteresowanie jakością, dobrymi materiałami i usługami o wysokiej jakości mają też wpływ inwestycje zagraniczne. Z jednej strony tworzą one popyt, nierzadko w obszarach mało popularnych w kraju lub jeszcze niedocenianych przez rodzime firmy, z drugiej strony firmy takie edukują w pewnej mierze rynek, wskazując, co jest popularne i warte inwestycji. W produkcji elektroniki pojawia się wiele nowości, urządzeń, materiałów, np. stopów i past lutowniczych lub środków chemicznych. Nierzadko w określonym obszarze funkcjonuje kilka równoległych technologii, podobnych, ale różnych w szczegółach i o niejasnych perspektywach rozwojowych. Producenci elektroniki niejednokrotnie unikają inwestycji w takiej sytuacji i wyboru określonego rozwiązania, gdyż boją się ryzyka nietrafienia w coś, co się nie przyjmie lub po krótkim czasie zostaną wycofane ze sprzedaży. Stąd technologie wykorzystywane przez duże firmy zagraniczne mają nierzadko charakter wskazujący na długoterminowe perspektywy.
Ochrona antystatyczna
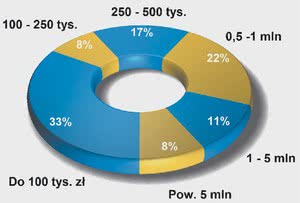
Materiały i sprzęt związane z ochroną przed elektrycznością statyczną dla wszystkich dostawców są dodatkiem do innych produktów zaopatrzenia produkcji. Są to wyroby trwałe, o niewielkim stopniu skomplikowania technicznego i oferowane przez wielu producentów. Dlatego prawie zawsze pełnią one funkcję dodatku, na którym się zarabia niewiele, ale który dobrze uzupełnia ofertę firm zorientowanych na obsługę firm elektronicznych. Część firm, a zwłaszcza te o szerszej ofercie, akceptuje tę zależność i nawet niewielka sprzedaż jest dla nich satysfakcjonująca. Dla co trzeciej firmy sprzedaż nie wykracza poza próg 100 tys. zł rocznie, ale jednocześnie co piąta ma obroty powyżej 1 mln.
Specjaliści zajmujący się rynkiem produktów antystatycznych zgodnie podkreślają, że jednym z najważniejszych czynników sprzyjających rozwojowi branży jest wzrost świadomości firm elektronicznych, głównie producentów urządzeń elektronicznych. Tematyka ochrony przed wyładowaniami elektrostatycznymi z pewnością nie jest w branży nowością, ale dopiero w ostatnich latach widać poważne zainteresowanie firm elektronicznych oraz to, że do zagadnienia tego podchodzi się z rozwagą. Wcześniej, a więc około dekady temu, zabezpieczenie antystatyczne produkcji było nierzadko robione amatorsko, byle jak i bez kontroli, czy faktycznie ochrona jest skuteczna. Widać to było zwłaszcza w mniejszych firmach, takich które nie miały kontaktów biznesowych z zagranicą lub nie zajmowały się zaawansowanymi technologiami.
Takie zjawiska w znacznej części są już przeszłością, a za tę zmianę w znacznej mierze odpowiedzialna jest nowoczesna technologia. Konstrukcja większości sprzętu elektronicznego opiera się dzisiaj na montażu powierzchniowym, a więc bazuje na znacznie większej miniaturyzacji i elementach elektronicznych o mniejszych wymiarach. Układy półprzewodnikowe pracują obecnie przy mniejszych napięciach znamionowych, pobierają znacznie mniejszą moc niż kiedyś i są wielokrotnie bardziej złożone. Skutkiem tych procesów jest znacznie większa podatność nowych komponentów na wyładowania, wymuszająca skuteczniejszą ochronę.
W przypadku ochrony antystatycznej wpadki bywają kosztowne i niestety stale się zdarzają. Gdy usterka zostanie wykryta na etapie testowania produkcji, problem może być mniej dokuczliwy finansowo, ale niestety serwis gwarancyjny u klienta, nawet przy niewielkiej liczbie wadliwych egzemplarzy, potrafijuż znacząco wpłynąć na finanse producenta.
W rozmowach z dostawcami podzespołów elektronicznych często przytaczane są historie wielkich wpadek biznesowych wynikających ze złej jakości komponentów lub usług zamawianych u tanich dostawców, w niektórych firmach chińskich lub problemów wynikających z nadmiernych oszczędności. Dostawcy renomowanych produktów podkreślają, że nic tak nie działa na ich korzyść, jak zmiana dostawcy na taniego i późniejsze problemy z jakością, bo wówczas te oczywiste zależności, o których powtarzają klientom do znudzenia i często bez wzbudzania uwagi, zyskują namacalne potwierdzenie finansowe i stają się wiarygodne.
Uszkodzenia układów elektronicznych na skutek wyładowań ESD potrafią być wyjątkowo dokuczliwe oraz ujawnić się po pewnym w czasie już podczas eksploatacji. Koszty napraw i wymian są w stanie pogrążyć nawet sporą firmę i niewątpliwie każde takie wydarzenie można postrzegać jako kamień milowy w zmianie świadomości rynku.
Jakość i wymagania prawne
Duża konkurencyjność w branży wymusza większą dbałość o jakość produktów i usług, zwłaszcza w sektorze produkcji kontraktowej. Otwarte granice sprzyjają nawiązywaniu kooperacji z partnerami zagranicznymi, a coraz większe znaczenie usług EMS i outsourcingu w produkcji tworzy wieloelementową strukturę zależnych podmiotów gospodarczych, które muszą chronić swoją pozycję i kompetencje. W relacjach tych aktywną rolę odgrywają zleceniodawcy firm kontraktowych, którzy w trosce o jakość swoich wyrobów wymuszają na nich właściwe podejście do ochrony ESD. Można też powiedzieć, że posiadanie skutecznej ochrony przed ESD jest obecnie często warunkiem uzyskania intratnych zleceń i można tę zmianę traktować jako konsekwencję rosnącej świadomości rynku.
Pozytywne wsparcie dają też regulacje prawne, np. dyrektywy europejskie lub natowskie. Stąd wymogu ochrony nie daje się też tak prosto lekceważyć lub pomijać, nawet gdy tej świadomości nie ma. Nierzadko ma ją klient, który zanim podpisze kontrakt, chętnie obejrzy halę produkcyjną, bo zasada "ufaj i sprawdzaj" w omawianym obszarze zagadnień technicznych ma sens.
Czynniki negatywne są typowe
Podobnie jak można to zaobserwować w przypadku wielu innych produktów dla elektroniki, tak samo w przypadku materiałów antystatycznych największym problemem rynku są tanie produkty pochodzące od wytwórców z krajów azjatyckich, które konkurują na rynku ceną.
Ostatnie kryzysowe lata znacznie uwypukliły znaczenie ceny jako głównego kryterium selekcji wyboru produktu i dostawcy. Stała presja działów zakupowych, które z jednej strony są premiowane za to, co uda im się "urwać" z faktur zakupowych, a z drugiej strony są luźno powiązane z działem produkcji, a jeszcze mniej w zakresie odpowiedzialności, prowadzi niestety do wielu patologii.
Niestety fakturowy koszt zakupu zbyt często jest głównym kryterium selekcji dostawcy, a tanie produkty nie zawsze zapewniają skuteczną ochronę przed ESD. Stąd decyzja o zakresie ochrony i tym, co wybrać, powinna zapadać na poziomie inżynierskim. W praktyce za dobór zabezpieczeń odpowiada nierzadko "zakupowiec", który ma niską świadomość zagrożeń i zbyt łatwo ulega pokusie kupna tańszych zamienników podzespołów, o innych parametrach w stosunku do założeń projektowych. Wydaje się, że ochrona antystatyczna produkcji powinna być dziedziną, w której taki rozdział pomiędzy działem zakupów a np. nadzorem technologicznym produkcji nie jest korzystny. Specjaliści sygnalizują, że nadal popełnia się wiele błędów w kwestii doboru i stosowania środków ochrony ESD, co można podsumować tym, że w tym zakresie chyba nigdy nie osiągniemy stanu pełnej wiedzy rynku. Stała edukacja kolejnych nowych firm i pracowników wydaje się stałym elementem tego biznesu.
Nowości w materiałach
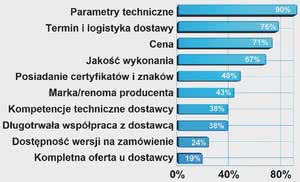
Mimo wielu opinii na temat znaczenia ceny na rynku materiałów antystatycznych i komponentów ochronnych paradoksalnie zdaniem ankietowanych specjalistów najważniejsze są parametry techniczne oraz termin i logistyka dostawy. Cena uplasowała się dopiero na trzecim miejscu, co jest zaskakujące i może wynikać z tego, że rynek ma już dzisiaj za sobą etap niewiedzy lub też braku przekonania co do celowości inwestowania w środki ochrony, co powoduje, że w pewnym stopniu sprzedają się one "same" w ramach kompleksowego zaopatrzenia. Gdy głównym produktem firmy staje się kompleksowa usługa, znaczenie ceny pojedynczego czynnika składającego się na większą całość staje się mniej istotne i znaczenie ceny maleje.
W zakresie materiałów do produkcji elektroniki próżno szukać przełomowych nowości lub też produktów zdolnych do jakościowej zmiany technologii w tej branży. Z uwagi na szerokość rynku i wielką liczbę producentów rynek zmienia się ewolucyjnie, czyli małymi krokami. Wspólną cechą wielu pojawiających się nowych wyrobów jest poprawa jakości procesu technologicznego poprzez lepsze własności mechaniczne, środowiskowe, precyzję itp. Nierzadko nowości zapewniają też równorzędne parametry po niższej cenie lub z lepszą wydajnością.
Przykładami mogą być pasty lutownicze przeznaczone do lutowania elementów precyzyjnych, o zwiększonej odporności mechanicznej, porównywalną z produktami ołowiowymi oraz mające lepsze parametry fizykochemiczne, umożliwiające precyzyjne nakładanie i dawkowanie po to, aby dało się montować wielokońcówkowe układy scalone o małym rastrze wyprowadzeń. Do nowości w pastach lutowniczych można też zaliczyć produkty o przedłużonej trwałości do blisko roku, które kierowane są do firm realizujących nieregularną produkcję, montujących płytki prototypowe lub zajmujących się serwisem.
Odejście od technologii ołowiowej spowodowało też wysyp nowych stopów lutowniczych. Producenci eksperymentują z różnymi mieszankami metali po to, aby ograniczyć liczbę powstających defektów w kontaktach podczas montażu, starają się poprawić stabilność długoterminową połączeń i zapewnić lepsze zwilżanie powierzchni. Karty katalogowe za każdym razem zawierają wiele wykresów i odniesień do starszych produktów, w stosunku do których nowe materiały zapewniają duży postęp. Skład chemiczny większości nowych stopów wydaje się bazować na cynie, do której dodawane są niewielkie ilości dodatków takich, jak miedź, nikiel, german, srebro, kadm i innych metali. Wraz z powiększającym się znaczeniem oświetlenia LED na znaczeniu zyskują też nowoczesne materiały termoprzewodzące, wykorzystywane w konstrukcji cieplnej modułów.
Dostawcy materiałów
Najważniejszą grupę dostawców materiałów do produkcji elektroniki tworzą firmy dystrybucyjne, zajmujące się dostawami urządzeń do produkcji, a więc sprzedażą automatów do układania elementów, pieców, urządzeń do nakładania pasty lutowniczej, kontroli optycznej i podobnego sprzętu. Tacy dostawcy mają zwykle bardzo szerokie oferty, współpracują z wieloma producentami zagranicznymi, czasem nawet sami produkują wybrane pozycje asortymentowe, na przykład materiały antystatyczne lub szablony laserowe. Poza urządzeniami i narzędziami związanymi bezpośrednio z procesem wytwarzania, firmy te sprzedają materiały eksploatacyjne, materiały do lutowania, lakiery, zalewy, środki do mycia i podobne środki chemiczne. Takimi firmami są na przykład PB Technik, Renex, Production Solutions, Robtools, PAKT Electronics, Semicon, Ambex.
W zakresie produktów antystatycznych największy potencjał ma firma Renex z Włocławka, która produkuje m.in. odzież antystatyczną, krzesła, obuwie, rękawiczki i opaski. Firma systematycznie poszerza asortyment własnych produktów antystatycznych, które oferowane są pod marką Reeco. Produkcją krzeseł ESD zajmują się też firmy Robtools i PAKT Electronics, mamy ponadto producenta obuwia ochronnego do użytku w strefach EPA - firmę Julex. Liczącą się pozycję ma także LaFot Elektronik.
Drugą grupę firm tworzą dystrybutorzy podzespołów, którzy w ramach szerokiej i kompleksowej oferty sprzedają narzędzia, chemię, materiały do lutowania, produkty antystatyczne i podobne akcesoria. Biorąc pod uwagę, że poza masową produkcją są one potrzebne w wielu innych specjalistycznych miejscach, jak laboratoria projektowe i badawcze, serwisy, sprzedaż materiałów przez dystrybutorów wydaje się tak samo naturalna jak podzespołów półprzewodnikowych. W omówieniu takimi firmami są TME, Masters, RS Components, Micros, Farnell element 14, Conrad, Dacpol.
Trzecią widoczną grupą dostawców są firmy zajmujące się sprzedażą głównie chemii i sprzętu do jej dystrybucji. Nie sprzedają natomiast dużych urządzeń do montażu elementów, pieców i sitodrukarek, jak Semicon lub Lenz, a w zakresie materiałów i sprzętu do ochrony antystatycznej także LaFot Elektronik. Czwarty sektor rynku tworzą producenci i dostawcy materiałów do lutowania, a więc lutów, past i topników. Są to MBO-Hutmen - wytwórca stopów lutowniczych past i topników dla lutowania oraz Cyne-Unipress i Interflux.
Węższą specjalizację rynkową ma natomiast firma Treston Ergona, która jest polskim oddziałem fińskiego producenta modułowych systemów mebli przemysłowych zwykłych i z zabezpieczeniem ESD oraz systemów magazynowania małych części i komponentów.
Obudowy dla przemysłu i urządzeń elektronicznych to kluczowe komponenty dla każdej aplikacji
Obudowa to produkt, który we współczesnej technice pełni taką samą funkcję jak płytka drukowana - każde urządzenie, konsumenckie, przemysłowe lub specjalne opiera na niej swoją funkcjonalność, bo determinuje ona wiele kluczowych parametrów technicznych. Dobra obudowa to taka, która wspiera aplikację, zapewniając odporność mechaniczną i środowiskową, odprowadzanie ciepła, ochronę EMC i ESD, bezpieczeństwo i wiele podobnych zagadnień. Do tej listy dochodzą jeszcze czynniki pozatechniczne, gdyż szczególnie w przypadku elektroniki konsumenckiej atrakcyjny wygląd, dobre materiały, ciekawa kolorystyka w takim samym stopniu decydują o powodzeniu sprzedaży i o pozytywnym postrzeganiu wyrobów. Wymagań stawianych przed obudową jest wiele, dlatego dostawcy obudów to w dużej części firmy specjalizujące się w tej tematyce, dysponujące zwykle szerokim asortymentem i kompleksową ofertą, do której zalicza się także usługi mechaniczne. Ich klientami są producenci szukający gotowych i dopracowanych w szczegółach produktów.
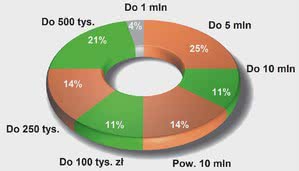
Średnia wartość obrotów dostawców obudów jest relatywnie duża – nie brakuje firm, które mają sprzedaż przekraczającą 5 mln zł rocznie (25%), a nawet powyżej 10 mln zł (14%). Innymi słowy obudowy są produktem, który pozwala dobrze zarobić, a nawet utrzymać wyspecjalizowaną w tej tematyce firmę. Zdaniem ankietowanych pełną specjalizację w tym kierunku ma 16% firm, czyli inaczej mówiąc, co szósta firma z tego zestawienia to dostawca specjalizowany, dla którego obudowy to centrum biznesu. Wydaje się, że to nie jest dużo, ale i tak znacznie więcej niż dla innych grup wyrobów.
Obudowy to niewątpliwie produkty uniwersalne i trafiające do wielu branży typów produktów, przez co czynników wzrostu dla tego rynku trzeba szukać także w branżach pokrewnych elektronice oraz w klimacie biznesowym panującym w kraju. Spośród wielu różnych czynników stymulujących pozytywnie rynek obudów w kraju warto wymienić na samym początku powstawanie nowych firm produkujących własne urządzenia. Firmy takie, najczęściej małe, a po pewnym czasie nierzadko też średnie, produkują specjalistyczne urządzenia w małych seriach i tym samym są modelowym klientem dla dostawców obudów. To samo dotyczy firm integracyjnych, wykonawców systemów i instalacji, które kupują na rynku komponenty standardowe automatyki i elektroniki, a dalej montują je w obudowach na obiektach, tworząc gotowe systemy. Poza nowymi inwestycjami tego typu takie projekty dotyczą także modernizacji starych rozwiązań: linii technologicznych, systemów pomiarowych i sterujących, komunikacji, struktury informatycznej, monitoringu itp. Stopień nasycenia środowiska urządzeniami technicznymi stale się powiększa, a każdy komponent musi być odpowiednio obudowany.
Im większa skala działania producentów OEM, tym zapotrzebowanie na obudowy katalogowe i dostarczane przez niezależnych wytwórców się zmniejsza, bo przy dużych seriach opłaca się już wytwarzać je we własnym zakresie lub też zamawiać wersje na zamówienie u producenta. Ale w warunkach krajowych takie firmy są w mniejszości w stosunku do całej reszty. Dlatego nowe inwestycje, rozwój branży budowlanej, modernizacja istniejących obiektów infrastrukturalnych, przenoszenie projektów z zagranicy do Polski i związany z nimi eksport, są obszarami gdzie aktywność takich specjalistycznych firm i popyt na obudowy jest wyraźnie widoczny, wyraźnie rozwijają branżę. Obszarów zastosowań jest znacznie więcej, bo uniwersalność tytułowych produktów i ich niezbędność powoduje, że rynek zbytu jest bardzo szeroki. Wystarczy przytoczyć branże wymieniane przez specjalistów w ankietach jako wiodące i perspektywiczne w kolejnych latach: telekomunikacja razem z M2M, kolejnictwo, energetyka, medycyna, inteligentny budynek, elektronika przemysłowa, energetyka wraz z OZE i inne, jak chociażby wojsko, aby zrozumieć, jakie możliwości rozwoju kryją się w omawianym sektorze.
Rynek obudów napędzają także nowe rozwiązania, na przykład w zakresie systemów automatyki budynków, gdzie urządzenia są częścią systemów, dla których wspólnym mianownikiem jest oszczędzanie energii. Takie systemy składają się z wielu części, montowanych na ścianach i rozdzielnicach, o skalowalnej konstrukcji i są połączone magistralą, co zapewniają specjalizowane pod tym kątem obudowy, gwarantujące szybkość montażu, brak pomyłek podczas instalacji itd.
Wchodzące na rynek coraz bardziej rozbudowane systemy elektroniczne wymuszają wprowadzanie na rynek nowych rodzin obudów, mieszczących więcej płytek (3-4) i zapewniających większą liczbę złączy sygnałów, przy zachowaniu łatwości obsługi i serwisu systemu. Z kolei w aplikacjach przemysłowych coraz ważniejsze są aspekty niezawodności i bezpieczeństwa - na rynku obudów widać to w tym, że projektanci wybierają sprawdzone konstrukcje, dzięki którym mogą wygodnie projektować coraz bardziej skomplikowane instalacje. Istotna jest bardzo dobra dostępność do dokumentacji (rysunki 3D), co znacznie ułatwia pracę.
Każdy sektor rynku ma problemy, obudowy nie są wyjątkiem
Znaczna część rynku obudów związana jest z nowymi inwestycjami w gospodarce. Trafiają one do produkowanych urządzeń, realizowanych systemów i instalacji oraz są bazą do modernizacji starszych produktów. W związku z tym rynek obudów w zakresie koniunktury jest powiązany dość mocno z ogólną sytuacją w przemyśle w Polsce i częściowo także w całej Unii Europejskiej. Od wstrząsu w gospodarce w połowie 2008 roku minęło już ponad pięć lat i cały czas niestety borykamy się z mniejszą liczbą inwestycji i ograniczeniami w finansowaniu projektów.
Drugim czynnikiem niekorzystnym dla rynku obudów jest import z krajów azjatyckich. Jest on szczególnie widoczny w zakresie standardowych obudów z tworzywa sztucznego i małych obudów metalowych. Import ten jest najbardziej dokuczliwy w tych cięższych czasach, kiedy znaczenie ceny jest duże, a przetargi ustawiane są przede wszystkim pod kryterium kosztów. Konkurencja cenowa na rynku obudów jest faktem, a rosnące ceny surowców i metali w połączeniu z wysokimi kosztami przygotowania produkcji wyrobów (np. formy wtryskowe) ograniczają możliwości obudowywania urządzeń za pomocą produktów wykonywanych na zamówienie, zwłaszcza te z tworzyw.
Specjaliści związani z rynkiem obudów sygnalizują, że inżynierowie projektanci mają też zbyt małą wiedzę na temat obudów: dostępnych rozwiązań mechanicznych, oferty akcesoriów, usług indywidualizacji, pokryć, a także możliwości konstrukcyjnych. Bezsprzecznie asortyment dostępnych na rynku produktów jest ogromny, co wymaga od konstruktorów zaangażowania, uwagi i poświęcenia sporo czasu na analizę katalogów. Wielu projektantów elektroniki skupia się w całości na systemie elektronicznym i rozwiązaniach układowych, do obudowy osoby te znacznie rzadziej przykładają uwagę i czas, co niestety utrudnia biznes, zwłaszcza promocję nowych rozwiązań.
Coraz większy asortyment
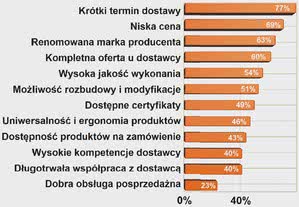
Najważniejszym czynnikiem oferty handlowej jest dzisiaj krótki czas dostawy, a nie cena. Jest to w dużej części wpływ kryzysu na rynek i skutek ogólnej niechęci klientów do kreślenia długotrwałych planów, którzy wolą kupować na bieżąco potrzebne ilości. Gotowe obudowy kupowane są do produkcji małych lub co najwyżej średnich serii, specjalistycznych urządzeń, które nierzadko wytwarza się na zamówienie. Producenci kupują przez to obudowy dopiero po uzyskaniu pewności co do kontraktu, tym bardziej że w porównaniu do innych elementów nie są to produkty tanie.
Coraz większa liczba producentów obudów dysponuje kompleksową ofertą produktów. Asortyment zwiększa się, obejmując wszystkie popularne i uniwersalne grupy (jak wersje prostopadłościenne lub na szynę), które są uzupełniane o bardziej specjalistyczne rozwiązania, np. wersje do automatyki budynkowej, wyświetlaczy lub też zoptymalizowane pod kątem określonych branży. Efektem są coraz bardziej opasłe katalogi, zacierające się powoli pierwotne podziały, np. na plastik i metal, liczne wyroby konsumenckie i profesjonalne oraz te determinowane przez technologię wykonywania lub sam materiał. Innymi słowy producenci nieustannie rozszerzają swoje oferty poziomo, starając się wypracować sobie kompleksowe oferty w strategicznych obszarach. To samo dotyczy dystrybutorów specjalizujących się w obudowach, łączących różne niekonkurujące ze sobą marki.
Kolejna rzecz warta uwagi to fakt, że usługi mechaniczne i indywidualizacja produktów katalogowych stały się standardem. Wiercenie otworów, frezowanie kanałów i pól pod wyświetlacz i klawiaturę oraz podobne operacje wykonywane na obrabiarkach CNC jeszcze kilka lat temu były wyróżnikiem wybranych firm, atutem i sposobem na zaoferowanie klientom większej wartości dodanej. Był oto także sposób na to, aby posługując się typowymi wyrobami katalogowymi, stworzyć ofertę o cechach indywidualnych. Ponieważ pomysł był dobry i trafił w potrzeby klientów, dzisiaj stał się standardem.
Niektórzy producenci inwestują dzisiaj w usługi szybkiego prototypowania z wykorzystaniem drukarek 3D. Pozwalają one już obecnie na szybkie wykonywanie drobnych detali i obudów z tworzyw do serii próbnych, za kilka lat można oczekiwać, że podobne możliwości będą dostępne dla wersji metalowych. Co więcej, w warunkach polskich, gdy drukowanie 3D się upowszechni i tą metodą będzie można zapewnić wysoką jakość, można oczekiwać, że w obszarze specjalistycznych wyrobów małoseryjnych wiele się może zmienić.
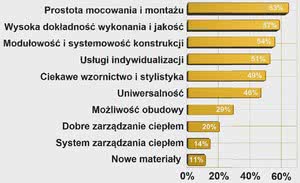
Zestawienie najważniejszych kryteriów technicznych i funkcjonalności związanych z obudowami, które projektanci biorą pod uwagę przy selekcji produktów spośród ofert różnych producentów. Na czołowych pozycjach znalazły się prostota montażu i mocowania oraz wysoka dokładność i jakość, a także modułowość i systemowość konstrukcji. Oznacza to, że firmy chcą kupować obudowy bezproblemowe, takie które okażą się nie tylko niekłopotliwe w produkcji, ale również nie okażą się konstrukcją zamkniętą i niepodatną na zmiany. Kolejne dwie pozycje, a więc usługi indywidualizacji oraz ciekawe wzornictwo, to dowód, jak wielkie zmiany zaszły w branży w ostatnich latach, bo jeszcze dekadę temu te dwie pozycje wylądowałyby na samym dole.
Jako konsekwencja kompleksowej oferty poszerza się też liczba wykonań specjalizowanych (spożywcze, wandaloodporne, przeciwwybuchowe), które nierzadko bazują na tak finezyjnych rozwiązaniach mechanicznych, że tworzą nowe możliwości technologiczne dla urządzenia. W ich przypadku żartobliwa dyskusja, która czasem pojawia się w rozmowach na temat tego, co jest ważniejsze, obudowa czy zawartość, przestaje mieć wydźwięk humorystyczny, bo taka obudowa determinuje kluczową funkcjonalność.
Rynek obudów uporał się też z dawniejszym problemem, kiedy na obudowy katalogowe trzeba było długo czekać. Producenci rozbudowali na tyle swoje magazyny, że są w stanie dostarczać większość produktów praktycznie od ręki. Zmiana ta może nie wydawać się aż tak istotna, ale dla niewielkich firm skupionych na rynkowych niszach nierzadko oczekiwanie na dostawę było sporym ograniczeniem biznesowym, zwłaszcza w gorszych czasach, gdy mało kto jest w stanie sprecyzować swoje plany w dłuższym horyzoncie i wiele projektów realizowanych jest ad hoc.
Obudowa to nie tylko mechanika, tę podstawową prawdę też już poznali wszyscy przedsiębiorcy. Tak samo liczą się ciekawe wzornictwo (kształty, ergonomia, kolorystyka), jak i funkcjonalność. Najbardziej widać to w zakresie urządzeń przenośnych, na przykład w sprzęcie pomiarowym przeznaczonym do pracy w terenie, gdzie kluczowe jest rozmieszczenie elementów interfejsu użytkownika, zapewnienie odporności na udary, wilgoć i brud. Znaczenie wzornictwa jest oczywiście największe w przypadku obudów plastikowych, być może dlatego, że one dają największe możliwości kreacji w tym zakresie. Podobne rozważania można odnieść do ochrony elektromagnetycznej, którą dobra obudowa potrafiwspierać.
Na koniec rozważań warto zauważyć, że nowoczesne obudowy tworzą wsparcie dla nowych technologii, np. wyświetlaczy z panelami dotykowymi, a producenci obudów współpracują z dostawcami komponentów określanych jako interfejs użytkownika (złącza, klawiatura, wyświetlacz, zasilanie).
Szafy i elementy wielkogabarytowe - atrakcyjna nisza, ale nie dla każdego
Osobną popularną i cenną biznesowo grupę produktów w branży obudów tworzą pełnogabarytowe szafy sterownicze, które wykorzystywane są do montażu urządzeń do rozdziału energii, sterowników, napędów i oczywiście systemów teleinformatycznych. Produkty takie, choć często znajdziemy w ofercie dostawców sprzedających również mniejsze gabarytowo obudowy, różnią się znacząco od tych ostatnich. Szafy wykonywane są zazwyczaj z blachy stalowej, często fosforanowanej i malowanej. Ich konstrukcja nośna składa się z profili stalowych tworzących szkielet, do których dołączane są podłoga i sufit oraz ściany i drzwi. Użytkownik może dobierać nie tylko wielkość, ale też sposób łączenia, materiał drzwi, itd., a do tego często różne urządzenia dodatkowe (wentylatory, klimatyzatory, systemy rozdziału energii, panele oświetleniowe) oraz osprzęt (np. mocowania, haki, nogi, itd.).
![]() |
![]() |
Szafy to obudowy, które zwykle są wypakowane sprzętem elektronicznym po brzegi. Ich typowe zastosowanie to centrum informatyczne firmy, zawierające serwer, sprzęt sieciowy, centralę telefoniczną, zasilanie gwarantowane, system alarmowy, rejestrator wideo z kamer monitoringu, system archiwizacji danych i podobne urządzenia. Sprzęt taki stanowi podstawę infrastruktury firmy, stąd obudowa, która je mieści, musi być nie tylko wysokiej jakości, ale zawierać szereg przemyślanych rozwiązań umożliwiających rozbudowę wraz z przedsiębiorstwem, wydajne chłodzenie, serwis i obsługę techniczną urządzeń i podobne czynniki. Taką obudowę kupuje się na lata, stąd szafy można traktować jako niszową na rynku obudów kategorię, ale wartościową i chwilami nawet elitarną.
Stała reprezentacja firm
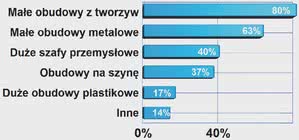
Wykres prezentuje, które typy obudów cieszą się największą popularnością na rynku i zbytem. Bezsprzecznie liderem są małe obudowy plastikowe, a na kolejnym miejscu małe obudowy metalowe. Jest to z pewnością wynik potencjału aplikacyjnego, bo wiadomo, że najwięcej na rynku sprzedaje się urządzeń niewielkich od strony gabarytów. Nawet jeśli obudowy duże są droższe, to jednak z uwagi na mniejszą sprzedaż ich globalny potencjał okazuje się mniejszy.
Obudowy są produktami, które znajdziemy u wielu różnorodnych dostawców działających na rynku - można oszacować, że na rynku funkcjonuje ponad 50 takich podmiotów. Niecałą połowę dostawców funkcjonujących na rynku polskim stanowią krajowi producenci tych produktów, którzy są aktywni zarówno w zakresie produktów z metalu, jak i tworzyw sztucznych.
Przez lata obudowy produkcji krajowej można było odróżnić na pierwszy rzut oka, gdyż w zamian za gorszą jakość i surowe wzornictwo były one zdecydowanie tańsze. Niemniej producenci krajowi w ostatnich latach sporo zainwestowali w park maszynowy, nierzadko korzystając ze wsparcia z funduszy, kupili wtryskarki, maszyny do obróbki blach i spawania, przez co jakość ich wyrobów znacznie się poprawiła. Zmiany widać także w zakresie wzornictwa, bo nowe produkty nie przypominają już kanciastych i siermiężnych poprzedników. Dzięki temu producenci krajowi cały czas są na rynku silną konkurencją dla firm zagranicznych.
Wśród nich są zarówno dostawcy urządzeń dla przemysłu, dla sektora elektronicznego, jak też firmy obsługujące klientów z wielu branż, w tym dostawcy katalogowi. Z pewnością ważną grupę stanowią producenci krajowi, tacy jak m.in. Agmar, Kradex, Maszczyk, Radiolex, Ergom, Jakubowski oraz ZPAS. Wielu z nich oferuje obudowy z tworzyw sztucznych, niektórzy szerszy asortyment obudów metalowych, jeszcze inni skupiają się na oferowaniu szaf przemysłowych.
Cechą wspólną jest fakt, że firmy te nieraz zapewniają produkty do aplikacji wprawdzie niewielkich pod względem wolumenu, ale o często wymagających cechach - np. w zakresie odporności na czynniki środowiskowe czy o wysokim poziomie indywidualizacji. Pomijając Kradeksa i Maszczyka, polskie firmy produkcyjne w większości zajmują się wytwarzaniem obudów metalowych, które przeznaczone są do zastosowań w telekomunikacji, sterowniach, systemach zasilania, systemach komputerowych i podobnych zastosowaniach przemysłowych, takich gdzie zamówienia dotyczą niewielkich serii produktów, ale za to na przykład wymagających zapewnienia dużej odporności na czynniki środowiskowe, o indywidualnych wykonaniach lub po prostu tańszych.
W takich ramach mieszczą się m.in. pulpity i panele sterownicze, systemy alarmowe i kontroli dostępu, urządzenia telewizji przemysłowej, zasilacze, obudowy do sprzętu teleinformatycznego, szafy telekomunikacyjne i podobne. Takie zastosowania pozwalają współistnieć małym innowacyjnym firmom krajowym razem z silną konkurencją ze strony dużych producentów, głównie niemieckich.
Do kluczowych na rynku dostawców zagranicznych należą przedsiębiorstwa będące oddziałami producentów zagranicznych. W raporcie przedstawiono kilkanaście takich firm - są nimi m.in. Apra, Euro-Box, Fibox, Phoenix Contact i przede wszystkim Pentair oraz Rittal. Pozostałą grupę dostawców stanowią dystrybutorzy i resellerzy, którzy często oferują po kilka marek produktów.
O ile dla producentów biznes ten jest główną działalnością, o tyle dla dystrybutorów najczęściej łączony jest z czymś innym. To ostatnie wynika z faktu, że wielu producentów ma nieraz wąską specjalizację i dystrybutor, chcąc zapewnić szeroką ofertę produktów dla różnych odbiorów, musi pozyskiwać je od kilku wytwórców.
Dla części firm dystrybucyjnych obudowy stanowią jeden z kluczowych elementów oferty, co dotyczy m.in. tych skupiających się na sektorach elektrotechnicznym i automatyki, dla innych zaś - w szczególności zajmujących się dystrybucją katalogową - jeden z komplementarnych elementów bardzo szerokiej oferty. Obudowy znajdziemy też u dostawców obudów do systemów komputerowych i mechaniki 19".
Producenci zwykle specjalizują się we właściwym dla siebie typie (metalowe lub plastikowe), obszarze rynku, a nawet konkretnych aplikacjach, wytwarzając produkty niszowe, na przykład produkty odlewane. Produkcja obudów to stanowczo zbyt szeroka branża, aby możliwe było jej zdominowanie przez kilka wiodących w skali świata firm. Równocześnie produkcja obudów to obszar kapitałochłonny od strony przygotowania produkcji, maszyn, oprzyrządowania, form wtryskowych i tym samym producenci nie są w stanie szybko poszerzać asortymentu. W zamian wypracowują swój styl, który staje się rozpoznawalny, specjalizują się na grupy urządzeń lub branże. Ogranicza to siłę konkurowania z innymi firmami i zapewnia dużą różnorodność.
Dystrybutorzy
Przykładem firm dystrybucyjnych silnie zaangażowanych na rynku obudów tego typu może być LC Elektronik, oraz firmy takie jak Apar, Dacpol, Eltron, dla których obudowy wydają się mieć spore znaczenie biznesowe.
Drugą grupę firm tworzą dystrybutorzy związani z jednym lub maksymalnie dwoma producentami. Obudowy w tym przypadku są uzupełnieniem i dopełnieniem innej części biznesu i pozwalają im zwiększyć wartość dodaną. Przykładem może być tutaj firma CSI, Semicon, LaFot, Eltronika, Microdis, Mera, Soyter Components, Spezial lub Elhurt.
Firm dystrybucyjnych, które sprzedawałyby tylko obudowy, a na dodatek jednego producenta, nie ma. Powodem są wcześniej omawiane ograniczenia wynikające z wąskiej specjalizacji producentów, konieczności zapewnienia kompleksowej oferty i usług, a także ograniczona wielkość rynku wykluczająca możliwość osiągnięcia rentowności. Obudowy sprzedają też wszyscy dystrybutorzy katalogowi, na przykład TME, Farnell element14 i RS Components. Firmy te mają szerokie spektrum produktów, bez znamion specjalizacji.