Każdy producent mikrokontrolerów ma w ofercie co najmniej jeden model z interfejsem ethernetowym. Dlatego nie jest niczym dziwnym, że sieci Ethernet można znaleźć na każdym piętrze piramidy sterowania przemysłowego (rys. 1). Ethernet zawsze znajdował się w górnych warstwach zastosowań, w których występują funkcje zarządzania. Niemniej ostatnio przesuwa się on także do dolnej sfery interfejsów Fieldbus, do tej pory zdominowanej przez kilka interfejsów szeregowych jak Modbus czy Profibus.
Wiele odmian Ethernetu
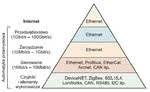
Rys. 1. Automatykę przemysłową realizuje się z użyciem sieci w szerokim zakresie topologii i właściwości
W przemyśle, oraz poza nim funkcjonuje szereg odmian Ethernetu (patrz tabela). Wynika to m.in. z konieczności zachowania kompatybilności pomiędzy starszymi technikami sieciowymi, ale też kompromisów pomiędzy standardowym Ethernetem a wersjami rozszerzonymi umożliwiającymi pracę w czasie rzeczywistym.
Te ostatnie wymagają zwykle stosowania specjalnych kontrolerów ethernetowych, przy czym nie wykorzystuje się tutaj zwykle standardowych mikrokontrolerów. Powodem jest to, że rozszerzenia czasu rzeczywistego nie mogą być w realizowane bez układów FPGA lub ASIC. Typowe ethernetowe realizacje TCP/IP charakteryzują się czasami opóźnień rzędu 1–2ms (dla 100BaseT).
Jeszcze gorzej może być w przypadku, gdy w protokole wykorzystywany jest dostęp typu CSMA/CD (Carrier Sense Multiple Access with Collision Detection). W tym przypadku następuje arbitraż, po którym następuje wybrana transmisja, co w systemie czasu rzeczywistego może mieć katastrofalne skutki.
Z tej właśnie przyczyny Ethernet jest często łączony z sieciami CAN, Modbus i Profibus, które mogą działać izochroniczne w czasie rzeczywistym. Niektóre normy wywodzące się z Ethernetu, jak standard synchronizacji czasu IEEE-1588 i oczywiście TCP/IP, są na ogół obecne w większości przemysłowych wdrożeń tego standardu.
Wykorzystywane są także aktualne normy Power over Ethernet (PoE). Jednakże PoE nie zawsze odpowiada warunkom przemysłowym, które są zwykle bardziej wymagające niż biurowe. Także napięcie jest znormalizowane w przemyśle do 24V, a w większości istniejących systemów PoE stosuje się napięcie 48V.
Przemysłowe wdrożenia Ethernetu działają także bezprzewodowo zgodnie z Wi-Fi 802.11. Ale w wariancie bezprzewodowym jeszcze trudniej uzyskać działanie w czasie rzeczywistym. Dlatego nowe normy bezprzewodowe, jak 802.15.4 i ZigBee, faktycznie komplikują bezprzewodowe sterowanie w przemyśle, ale również wskazują, że Ethernet przemysłowy prawdopodobnie stanie się szkieletem bezprzewodowych sieci czujników i sterowania.
Ethernet nie wystarcza
Wadą klasycznego Ethernetu jest dopuszczanie do opóźnień przesyłania komunikatów w czasie, co nie pozwala na wykorzystanie tej technologii w środowisku działającym w czasie rzeczywistym. W takich zastosowaniach trzeba zatem poszukać modyfikacji Ethernetu na poziomie sprzętowym. Do głównych rodzajów Ethernetu przemysłowego zaliczają się Modbus, Foundation Fieldbus, ProfiNet, Ethernet-Powerlink, EtherCat oraz Sercos.
Każda z nich ma inne, charakterystyczne właściwości i różne mogą być powody jej wyboru w danej aplikacji. Z Ethernetem łączy się również sieci przemysłowe takie jak DeviceNet i ControlNet (rys. 2). DeviceNet zwykle działa w ramach sieci CAN, podczas gdy ControlNet ma własną platformę do łączności w czasie rzeczywistym.
Wszystko to wiąże razem wspólny protokół przemysłowy CIP (Common Industrial Protocol). Udostępnia on uzgodnioną infrastrukturę powiadamiania. Usługi czasu rzeczywistego zwykle mieszczą się w protokole DeviceNet lub ControlNet, a Ethernet tworzy szkielet infrastruktury. W Ethernecie zamykane są także komunikaty dla poszczególnych odmian Modbusa (rys. 3).
Podobnie jak w CIP, Modbus-TCP zapewnia współdziałanie, ale nie reagowanie ściśle w czasie rzeczywistym. Musi to zostać zrównoważone z szybkością Ethernetu, który dla tego rozwiązania jest szybszy od większości innych wdrożeń. Zatem przydatność Ethernetu będzie tutaj zależała od aplikacji. Foundation Fieldbus HSE (szybki Ethernet) jest podobny do Modbus-TCP i do Ethernet/IP, ponieważ używane są w nim standardowe stosy i sprzęt Ethernetu, przystosowywane przez gotowe mikrokontrolery z Ethernetem.
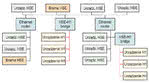
Rys. 4. Architektura Foundation Fieldbus obsługuje liczne protokoły transportowe, przy czym interfejsy High-speed Ethernet – Fieldbus umożliwiają różnym urządzeniom komunikowanie się ze sobą, w tym tunelowanie ruchu
Ale Fieldbus H1 – szeregowa magistrala sterująca, będąca pozostałością po poprzednich – pozostaje częścią infrastruktury, zapewniając sterowanie urządzeń krytycznie uzależnionych czasowo (rys. 4). Podsieci H1 i HSE są powiązane węzłem mostu. Czas reakcji w Ethernet/IP, Modbus-TCP i Fieldbus HSE jest rzędu 1ms, nawet przy stosowaniu standardu Ethernet.
Sposoby na czas rzeczywisty
ProfiNet, EPL, EtherCat i Sercos III podchodzą do tego inaczej niż norma Ethernet. W wielu wypadkach można użyć gotowego rutera czy przełącznika. W większości przypadków jednak wszystkie węzły w podsieci muszą być kompatybilne z zastosowaną normą. Analogicznie, normalny ruch Ethernetu może być kierowany przez sieci niestandardowe lub poza nimi.
Ogólnie jednak biorąc, na granicach znormalizowanych i nieznormalizowanych podsieci Ethernet używa się specjalizowanych bram, ruterów i przełączników. W przypadku ProfiNet wykorzystywane są specjalizowane układy rozdzielające ruch Ethernet na cykle, dzielone później na ruch w czasie rzeczywistym i inne (rys. 5).
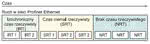
Rys. 5. W ProfiNet ruch w czasie rzeczywistym jest dzielony na izochroniczny oraz ruch w czasie „niemal rzeczywistym” dla sygnałów alarmu
Część ruchu w czasie rzeczywistym jest dalej dzielona na sekcje ruchu izochronicznego i czasu tzw. miękkorzeczywistego. Każda z sekcji ma przydzieloną część czasu kontrolowaną przez układ nadrzędny podsieci. Sekcja czasu miękkorzeczywistego jest zwykle używana do komunikatów asynchronicznych, takich jak alarmy. Wszystkie komunikaty w czasie rzeczywistym są dokładnie dopasowane do odpowiedniej szczeliny czasowej, więc wszystkie urządzenia w sieci muszą utrzymywać się w synchronizmie.
Sekcja nie w czasie rzeczywistym nie uczestniczy w normalnym ruchu Ethernet, w którym musi dochodzić do kolizji. Ale wszystkie pakiety tego cyklu muszą być wysyłane w określonych ramach czasowych. Dodatkowo powtórzenia, które nie zmieszczą się w bieżącym cyklu, muszą być odkładane. W Ethernet-Powerlink (EPL) stosuje się podobne podejście, ale węzeł nadrzędnego menedżera przesyła pakiety we właściwym czasie, posługując się synchronizacją (rys. 6).
Każdy układ sprawdza te pakiety i reaguje zgodnie ze standardowym ruchem Ethernet, nadchodzącym w trakcie przedziału asynchronicznego. Czas trwania przerw pomiędzy cyklami jest krótki, ale zbliżony do przerw w innych wrażliwych na czas wdrożeniach Ethernetu. Zaletą EPL jest to, że pozwala używać standardowych urządzeń i interfejsów Ethernetu, ale dla zapewnienia dodatkowej wymiany potwierdzeń wymaga modyfikacji stosów protokołów.
Przegląd sieci bazujących na EthernecieNa rynku jest wiele sieci opartych na Ethernecie. Bazują one na różnych protokołach oraz sposobach komunikacji. Poniżej przedstawiono charakterystyki większości spotykanych standardów wraz z zasadą działania i zastosowaniami każdej z sieci komunikacyjnych. EPAEPA (Ethernet for Plant Automation) to chińska wersja standardu Ethernet do zastosowań w przemyśle, jest to także nazwa handlowa spółki Zhejiang Supcon. Standard ten nie jest wspierany przez jakąkolwiek organizację, brak rozpowszechniania urządzeń tego typu na rynku. Protokół bazuje na podziale na szczeliny czasowe na poziomie MAC dla komunikacji w czasie rzeczywistym, cały inny ruch odbywa się z wykorzystaniem standardowego protokołu TCP/IP i/lub standardu Modbus. Ethernet PowerlinkEthernet Powerlink został opracowany w 2001 roku przez Bernecker+Rainer (B&R), standard wspierany jest przez grupę Ethernet Powerlink Standardisation Group (EPSG). Główni producenci urządzeń to B&R, AMK, Baldor, Fraba, Lenze oraz Pepperl+Fuchs. System składa się z zamkniętych podsieci z urządzeniami typu master, które odpowiedzialne są za synchronizację i tworzenie szczelin czasowych. Czas cyklu wynosi od 0,2ms, a zastosowanie to sterowanie robotami i manipulatorami, systemy napędowe. EtherCATStandard opracowany w 2003 roku przez firmę Beckhoff, jest wspierany przez zrzeszającą kilkuset członków EtherCAT Technology Group. Główni producenci urządzeń to Beck IPC (układy master), Beckhoff (serwomechanizmy, układy I/O), ACS-Tech 80, Baumüller, Danaher, Lust, Servo Dynamics oraz Stöber (napędy), Balluff, Fraba i TR Electronics (enkodery). W EtherCAT stacja master połączona jest z hostami typu slave w sieci o topologii pierścienia, przy czym wykorzystana jest fizyczna warstwa Ethernetu. Pojedynczy pakiet przesyłany jest od stacji master poprzez każdą stację slave, a następnie do punktu wyjściowego. Klasyczne urządzenia TCP/IP wymagają podłączenia do sieci za pośrednictwem bram, co umożliwia dekodowanie pakietów TCP/IP. Czasy cyklu wynoszą od 30μs, a synchronizacja zajmuje mniej niż 1μs. Zastosowanie to sterowanie ruchem, układy wejścia/wyjścia i enkodery. Ethernet/IPIP (Industrial Protocol) zdefiniowany został przez firmę Rockwell Automation i obecnie wspierany jest przez zrzeszającą kilkuset członków organizację ODVA. Głównym producentem w dziedzinie sterowników, układów I/O, HMI i napędów jest Rockwell Automation. Pozostałe większe firmy to Accu-sort Systems, Datalogic, Sick, Acromag, Phoenix, Wago, Bosch Rexroth, Parker Hannifin oraz SMC. Protokół oparty jest na klasycznych TCP/IP, UDP/IP oraz CIP i zapewnia możliwość przesyłania danych konfiguracyjnych, diagnostycznych oraz danych I/O przez zwykły Ethernet. Niedeterministyczne przesyłanie informacji możliwe jest z czasem reakcji na poziomie 10ms. Istnieje też możliwość dodania synchronizacji (CIPsyng – IEC61588). Ethernet/IP bazuje na komunikacji okresowej (okres 10– 100ms). Synchronizacja – około 10μs. Protokół jest kompatybilny z Control- Net i DeviceNet, które też są oparte na CIP (Common Industrial Protocol). HSEHigh Speed Ethernet został opracowany przez konsorcjum Fieldbus Foundation w celu połączenia sieci typu Fieldbus z sieciami Ethernet. Urządzeniem spełniającym taką funkcję jest konwerter produkowany przez Emerson Process Management, Endress+Hauser oraz Smar International. Bazuje na zagnieżdżeniu protokołu Fieldbus w ramce Ethernet. HSE pozwala na wykorzystanie do komunikacji Ethernetu – np. w systemach DCS (Distributed Control System). IEC61850Standard IEC 61850 określa protokół komunikacji stosowany przemyśle energetycznym. Wykorzystuje on obiektowy protokół komunikacyjny jako górną warstwę protokołów TCP/IP. Standard wspierany przez UCA International User Group. Jest to obiektowy protokół komunikacyjny na stosie TCP/IP. Modbus/TCP (RTPS)Wprowadzony na rynek przez Schneider Electric i wspierany przez grupę Modbus-IDA, pierwotny protokół Modbus (np. RS485) jest wykorzystywany od 1979 roku. Z czasem został on dostosowany do wykorzystania w sieci Ethernet. Obecnie dostępnych jest kilkaset produktów pochodzących od różnych dostawców. Protokół bazuje na TCP/IP z protokołem Modbus. Do komunikacji wykorzystuje się model pytań i odpowiedzi z komunikacją okresową co 20–100ms. Rozwiązanie nie jest deterministyczne – działanie w czasie zbliżonym do rzeczywistego możliwe jest tylko z użyciem RTPS (Realtime Publisher Subscriber). Szerokość pasma dla TCP/IP wynosi 90–100%. Zastosowanie główne to podłączenie sieci Modbus z sieciami Ethernet. Jest to też prosty protokół do obsługi wejść/wyjść oraz odczytywania i zapisywania rejestrów. P-Net z IPRozwiązanie oferowane przez Danish National Committee, w którym zaproponowano wykorzystanie Ethernetu w oparciu o model HSE (omówiony powyżej). Jak dotychczas brak produktów, protokół jest w fazie rozwoju. ProfinetStandard wspierany przez Profibus International, organizację zrzeszającą ponad 1200 członków i grup regionalnych z kilkudziesięciu krajów świata. Wybrane firmy i produkty: Beckhoff – PLC oraz moduły I/O; Comtrol: moduły I/O i bramy; Danfoss, Bosch Rexroth, SEW Eurodrive: napędy i sterowniki; Siemens: PLC, napędy, moduły I/O, karty PC; Yokogawa: PLC; HMS, Hilscher: moduły I/O, bramy; Wago: moduły I/O; Phoenix Contact: moduły I/O. Profinet jest szczególnie często wykorzystywany w Niemczech, gdzie odbiorami urządzeń tego typu są m.in. firmy z sektora motoryzacyjnego – Audi, BMW, Daimler-Chrysler, Volkswagen. W działaniu do większości funkcji Profinetu stosowany jest klasyczny protokół TCP/IP, nie ma przy tym ograniczeń co do ruchu sieciowego tego typu. Do obsługi urządzeń I/O i im podobnych w czasie rzeczywistym (do 1ms) wykorzystuje się adresowanie bezpośrednie oraz priorytety wiadomości. Do obsługi w czasie rzeczywistym poniżej 1ms z synchronizacją <1μs wykorzystuje się sprzętowe przełączniki sieciowe połączone szeregowo lub w pierścień. Protokół wykorzystuje synchronizację zgodną z IEC 61588. Szerokość pasma protokołu TCP/IP wynosi 50–100%. Czas cyklu zawiera się od 250μs z 30 osiami i 50% udziałem pakietów TCP/ IP. Synchronizacja <1μs. Zaletą Profibusa jest możliwość łatwej integracji z sieciami Profibus oraz, Interbus. Sercos IIIInterfejs ten powstał na bazie Sercos – standardu magistrali do sterowania napędami, która wspierana jest przez Intressengemeinschaft Sercos Interface i ma obecnie ugruntowaną pozycję na rynku. W Sercosie III do komunikacji wykorzystano niektóre warstwy protokołu Ethernet. Wbudowany w każdym urządzeniu systemu przełącznik sieciowy pozwala na utworzenie topologii pierścienia lub łańcucha. Urządzenia TCP/IP mogą być podłączone do ostatniego przełącznika układu łańcuchowego. Czas cyklu transmisji wynosi od 31μs z ośmioma osiami. Synchronizacja <1μs. Zastosowania obejmują sterowanie napędami i ruchem. Istnieje możliwość podłączenia urządzeń I/O i wykorzystania TCP/IP na potrzeby parametryzacji i dodatkowej komunikacji. SynqNetOpracowany przez firmę Motion Engineering będącą obecnie częścią Danaher Motion. SynqNet stosowany jest w rozwiązaniach z zakresu sterowania ruchem maszyn, w przemyśle półprzewodnikowym i elektronicznym. Produkty wytwarzane są m.in. przez AMC, Danaher, Glentech, Kollmorgen i Panasonic. Do działania wykorzystywana jest warstwa fizyczna Ethernetu, a każde urządzenie zawiera po dwa interfejsy Ethernet (dla danych odbieranych oraz wysyłanych). Cechą charakterystyczną jest też brak komunikacji z wykorzystaniem TCP/IP. Czas cyklu wynosi od 25μs z czterema osiami. Zastosowania to sterowanie napędami i ruchem. Vnet/IPProtokół został opracowany w roku 2004 przez firmę Yokogawa. Nie jest wspierany przez żadną organizację. Bazuje na protokole HTTP, wykorzystuje TCP/IP i rozszerzony o protokół RTP (Realtime and Reliable Datagram Protocol). Czasy reakcji są na poziomie 10ms, nie ma synchronizacji. Zastosowania to zwykła komunikacja TCP/IP oraz aplikacje wykorzystujące HTTP. |
W EPL można operować cyklami transmisji 200ms z jitterem synchronizacji stacji do 1ms. EtherCAT idzie o krok dalej, umieszczając wiele komunikatów w jednym pakiecie Ethernet (rys. 7). Pakiety są ekspediowane poprzez każdy z węzłów, który informacje włącza do tych pakietów lub je z nich wydobywa. Do obsługi bardziej wyrafinowanych wdrożeń Ethernet w EtherCAT używa się kontrolerów na bazie układów FPGA.
Warto ponieść związane z tym większe koszty, bo EtherCAT jest rozwiązaniem o najszybszej reakcji i najkrótszym cyklu. EtherCAT może także obsłużyć zwyczajny ruch w Ethernet. Do przesyłania ruchu przez podsieci nie typu EtherCAT są potrzebne rutery, bramy czy przełączniki EtherCAT. W takich podsieciach synchronizacja w czasie nie jest możliwa, ale pakiety EtherCAT z wieloma komunikatami z danymi da się wysyłać przez podsieci nieEtherCAT, poprawiając w ten sposób całkowitą sprawność transmisji.
Sercos pierwszej generacji, o szybkości przenoszenia 2 i 4 Mb/s, był używany głównie w zastosowaniu do obrabiarek. Sercos III, podobnie jak inne wdrożenia przemysłowego Ethernetu, transmituje dane z szybkością Fast Ethernetu 100Mb/s. Z drugiej strony odbiega od standardowej architektury koncentratora Ethernetu i realizuje podwójny, przeciwbieżny, samonaprawiający się pierścień. Eliminuje to potrzebę kompatybilności z urządzeniami typowymi.
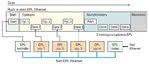
Rys. 6. Ethernet-Powerlink (EPL) dla utrzymania korzyści zachowania ruchu w czasie rzeczywistym wymaga użycia wyłącznie urządzeń typu EPL. Układ zarządzający EPL, dla uniknięcia kolizji, które by zachodziły w normalnej sieci Ethernet, wprowadza cykliczną pracę urządzeń EPL
Oznacza to także specjalizowane realizacje na poziomie węzłów. Sercos III powstał w celu poprawienia parametrów przy zachowaniu kompatybilności z Sercosem. Przesyłanie konwencjonalnego ruchu Ethernet do i z tych pętli jest możliwe, ale Sercos III pozostanie zapewne w obszarze przemysłowym, podczas gdy standardowy Ethernet będzie szkieletem korporacyjnym. Liniowa wersja Sercos III jest możliwa, ale brakuje jej redundancji podwójnej pętli.
Nic innego tylko Ethernet?
W wielu aplikacjach używanie wyłącznie Ethernetu jest niewykonalne. Ale parametry i wydajność mikrokontrolerów z ethernetowym wyposażeniem nieustannie wzrastają, umożliwiając łatwe włączanie również i niestandardowych lub rozszerzonych protokołów Ethernetu jak CIP. Są one często większe od podstawowych stosów protokołów komunikacyjnych, ale ich rozmiary mogą się zmieniać w zależności od liczby dostępnych funkcji.
Wydaje się, że Ethernet nadal pozostanie siecią komplementarną, ponieważ wiele aplikacji kontrolnych nie jest ograniczonych ani zasilaniem, ani właściwościami. Także interfejsy fieldbusowe, takie jak CAN, będą więcej niż wystarczające dla potrzeb sterowania przemysłowego u dołu piramidy. Ethernet może istnieć od góry do dołu całej hierarchii, z dopuszczeniem takich mieszanek jak CANopen, Sercos na EPL lub Modbus-TCP.

Rys. 7. W EtherCAT podpakiety wielu urządzeń są wiązane w jeden pakiet Ethernetu. Może to znacznie zwiększyć szybkość przesyłu danych w sieci. W podsieci mogą współistnieć pakiety EtherCAT ze standardowym ruchem TCP/IP
Oczywiście możliwości współistnienia różnych norm są ograniczane przez producentów, którzy często wprowadzają jakąś własną drobną zmianę, uniemożliwiającą współdziałanie podzespołów różnego pochodzenia. Przeważnie dzieje się tak w pozostałych z przeszłości standardach Fieldbusa, a zdarza się na poziomie Ethernetu.
Prowadzi to zwykle do systemów jednego producenta – przynajmniej na poziomie podsieci – nadając większości przemysłowych systemów sterowania wyróżniających właściwości. Niemniej, używanie wspólnych norm, jak Ethernet, znacznie zbliżyło producentów w zakresie normalizacji, po prostu z potrzeby współdziałania z innym znormalizowanymi protokołami Fieldbusów. (KKP)