Dwie płytki sztywne połączone elastycznym kablem sprawdzają się na krótkie odległości, jednak całkowity koszt jest w tym przypadku większy od ich sztywno-elastycznego odpowiednika z powodu konieczności zastosowania kabla, złączy oraz wykonania montażu tych elementów. Ponadto konstrukcja ta jest podatna na awarię połączeń i charakteryzuje się krótszym czasem życia. W obwodach rigid-flex problemy z kontaktami nie występują, co zwiększa niezawodność, a tym samym jakość i czas życia produktu.
Symulacja kosztów
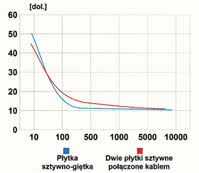
Rys. 1. Porównanie kosztu produkcji płytki rigid-flex oraz jej odpowiednika w postaci dwóch płytek sztywnych połączonych kablem w funkcji liczby wyprodukowanych sztuk
W niektórych projektach zastosowanie rigid-flex nie będzie opłacalne, dlatego należy ustalić, w jakiej sytuacji koszty jednej i drugiej opcji będą porównywalne. Taką symulację można wykonać na podstawie wyceny kosztu produkcji i montażu. Na rysunku 1 porównano koszt produkcji czterowarstwowej płytki sztywno-giętkiej z dwiema elastycznymi warstwami wewnątrz z kosztem jej odpowiednika w postaci dwóch czterowarstwowych płytek sztywnych połączonych kablem.
Obydwa przypadki różnią się jedynie kablem i złączami wymaganymi przy płytkach sztywnych, a koszt produkcji zawiera koszt montażu i został podany w oparciu o rzeczywistą wycenę wykonaną przez producenta PCB.
Po osiągnięciu 100 sztuk projekt wykorzystujący płytki sztywno-giętkie staje się tańszy niż jego odpowiednik sztywny, czego głównym powodem jest brak kabli, złączy, a także konieczności ich montażu, dzięki czemu liczba operacji montażowych jest mniejsza a testowanie prostsze, co obniża całkowity koszt. Mniej komponentów do zamówienia zmniejsza ryzyko łańcucha dostaw, a ponadto płytkę rigid-flex można zaprojektować tak, aby konserwacja była bardziej dogodna i tym samym tańsza przez cały czas życia produktu.
Czas projektowania
Kluczowym czynnikiem przy analizowaniu realności zastosowania rigid-flex w danym projekcie są koszty produkcji, montażu, testowania i logistyki, ale nie można także zapominać o kosztach projektowania i rozwoju. Projektowanie części elastycznej PCB oraz integracja płytki z produktem końcowym zwykle wymaga współpracy z konstruktorami mechaniki. Jest to proces długi, drogi i podatny na błędy.
Standardowe narzędzia do projektowania PCB nie obsługują trybu 3D ani definiowania i symulowania elastycznej części, która w rzeczywistości może być składana, skręcana i zwijana, dopasowując się do danego mechanizmu. Nie umożliwiają one nawet definiowania różnych warstw dla różnych części projektu, czyli np. innych w części elastycznej.
Z tego względu projektanci rigid-flex musieli dotąd ręcznie przetwarzać sztywne i elastyczne części swoich projektów 3D na wymagany w produkcji format 2D. Następnie ręcznie oznaczali wszystkie elastyczne obszary projektu i upewniali się, że komponenty i przelotki nie zostały umieszczone w pobliżu przejścia między obszarami sztywnymi i elastycznymi. Ponadto musieli stosować się do wielu dodatkowych zasad, z których większość nie jest wspierana przez standardowe oprogramowanie do projektowania PCB.
Większa trudność projektowania płytek rigid-flex niż płytek sztywnych jest przyczyną znacznie mniejszej konkurencyjności cenowej tej technologii. Na szczęście najnowsze narzędzia zawierają zaawansowane możliwości projektowania w 3D, wsparcie dla definiowania i symulacji zagięć czy złożeń w części elastycznej projektu oraz umożliwiają definiowanie różnych stosów warstw dla różnych obszarów projektu. Narzędzia te eliminują konieczność wykorzystywania oprogramowania CAD do projektowania obszarów elastycznych, oszczędzając projektantom czas i pieniądze.
Projektowanie w 3D kluczem do sukcesu
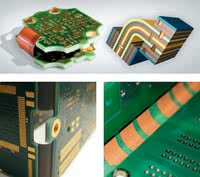
Rys. 4. Ilustracja pokazuje, jak realizowane jest przejście warstw pomiędzy obwodem elastycznym a sztywnym
Wczesne współdziałanie projektantów z producentami płytek drukowanych to kolejny czynnik poprawiający konkurencyjność cenową technologii rigid-flex. Projekty sztywno-elastyczne wymagają bliższej współpracy między projektantami i producentami niż jest to konieczne przy tradycyjnych projektach PCB.
Aby stworzyć udany projekt tego typu, projektant powinien w porozumieniu z producentem wypracować zasady, do których będzie się stosował. Zalicza się do nich określenie liczby warstw projektu, dobór materiałów, ustalenie rozmiarów ścieżek i przelotek, sposobów łączenia oraz gabarytów. Właściwe narzędzie, obsługujące modelowanie w 3D, umożliwi łatwe zdefiniowanie tych kwestii, co pozwoli na optymalizację projektu rigid-flex oraz jego łącznego kosztu.
Podsumowanie
Wykorzystanie technologii sztywno-elastycznej może zdecydować o sukcesie produktu. Obecne trendy w przemyśle i rosnące wymagania klientów powodują, że inżynierowie docierają do granic możliwości, co wymusza na nich poszukiwanie alternatywnych rozwiązań w projektowaniu elektronicznym.
Ponadto wymogi narzucane obecnym urządzeniom przenośnym sprawiają, że technologia rigid-flex trafia do głównego nurtu i staje się znacznie bardziej realna w wielu aplikacjach. Dostępność nowoczesnych narzędzi obsługujących modelowanie trójwymiarowe znacząco minimalizuje trudności w projektowaniu rigid-flex oraz powoduje, że tego typu rozwiązania stają się bardziej pożądane i w pewnych warunkach są nawet tańsze niż tradycyjne płytki drukowane połączone kablem.
Grzegorz Michałowski