Do takich zadań wykorzystuje się technologie montażu powierzchniowego oraz dodatkowe operacje takie jak conformal coating, underfill, dam & fill, zalewanie czy wylewanie uszczelek. Takie potrzeby wymuszają też zastosowanie w produkcji elektroniki klejów SMA, past termoprzewodzących, zalew, uszczelniaczy, a nawet smarów i olejów, nakładanych coraz bardziej precyzyjnie, czysto i wydajnie.
Rosnąca precyzja dozowania oraz możliwość stosowania trudniejszych w obróbce materiałów pozwala na jeszcze większą miniaturyzację i ograniczenie wymiarów oraz kosztu jednostkowego operacji montażowej. W ten sposób wąskie gardła w technologii produkcji są po kolei eliminowane, dzięki czemu postęp wydaje się nie mieć końca (rys. 1).
Jest jednak jeden parametr produkcyjny, który do tej pory sprawiał kłopoty większe niż inne ograniczenia - wielkość partii produkcyjnej. Zastosowanie precyzyjnych urządzeń dozujących w małej skali działalności napotyka zrozumiałą barierę inwestycyjną. Do każdego rozmiaru produkcji potrzebne jest więc inne rozwiązanie i konfiguracja, która spełni wymagania stawiane przez klientów.
Dozowanie w produkcji
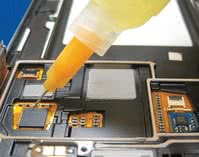
Fot. 3. Dyspenser serii Ultimus I firmy Nordson EFD jest precyzyjnym urządzeniem do zastosowania nawet w ręcznych aplikacjach małoseryjnych
W zależności od stopnia komplikacji procesu trzeba rozróżnić dwa podstawowe aspekty, w których powinna nastąpić analiza: automatyzacja produkcji i reologia. Są to prawie całkowicie rozdzielne obszary, w których obowiązują całkowicie różne kryteria oceny.
W obszarze automatyzacji procesu dozowania możemy wyróżnić kilka poziomów zaawansowania: dokładność pozycjonowania dawki, prędkość pozycjonowania, transport detalu do i od urządzenia oraz realizacja ruchów postępowych w czasie np. nakładania uszczelek bądź precyzyjnego zalewania np. przy podlewaniu układów BGA (rys. 2).
Wydajność
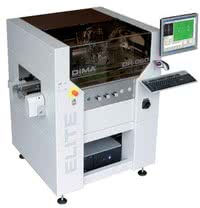
Fot. 4. Stacja DR-060 może zostać zastosowana nie tylko do nakładania klejów SMA czy pasty lutowniczej, ale również do wykonywania mniej wymagających operacji underfill
Podstawowymi urządzeniami w tym obszarze są dyspensery, w których pozycjonowanie dawki i detalu odbywa się ręcznie (fot. 3). Niemniej przy rozważaniu ich użycia w bardzo precyzyjnych aplikacjach często zapomina się, że wydajność produkcyjna tych maszyn jest zmienna.
Jeśli operacja montażu staje się mniej wymagająca technologicznie - czyli tolerancje dawek płynu i ich wielkości rosną, wzrasta znacząco wydajność. Są takie aplikacje, gdy jeden operator jest w stanie nałożyć nawet 10-20 tys. dawek płynu dziennie. Z kolei przy kilku detalach można poświęcić więcej czasu na pozycjonowanie dawek pod mikroskopem lub kamerą, nawet za pomocą dodatkowych ręcznych manipulatorów.
Gdy wolumen produkcji wzrasta, celowe może okazać się zastosowanie robota, manipulatora trój- lub cztero- osiowego pracującego poza linią (off-line). Ogranicza się w ten sposób czas konieczny do pozycjonowania końcówki dozującej i można wykonać operacje nakładania bardziej precyzyjnych linii w trybie mokro-na-sucho.
Tak określa się operacje, gdzie estetyka połączenia lub jego stabilność wymiarowa jest oczekiwana po usieciowaniu płynu. Przykładem jest estetyczne wklejanie ekranów lub szybek wizjerów w obudowach, operacja underfill, a także nakładanie uszczelek wylewanych, które po utwardzeniu muszą zachować stabilność wymiarową.
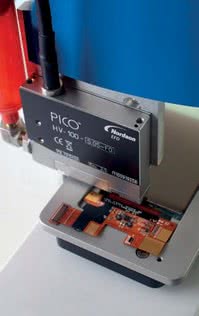
Fot. 5. Robot stolikowy Bluestar może być wyposażony w bezkontaktowe zawory Pico-Dot i wykonywać zaawansowane operacje nakładania klejów lub uszczelniaczy
Po przekroczeniu dalszych wymagań w zakresie wolumenu produkcji lub przy konieczności wbudowania procesu nakładania płynu w linię można zastosować platformy pozwalające na integrację in-line. Mają one w standardzie kamery do programowania i korekty pozycjonowania głowicy według fiduciali, pozwalając na uruchomienie większej produkcji seryjnej (fot. 5).
Najbardziej zaawansowane są systemy in-line, które łączą zaawansowanie automatyki procesu z zachowaniem sterowania procesem nakładania płynu. Takie platformy służą do wysoko wydajnego i precyzyjnego nakładania np. klejów SMA lub wzmacniania układów BGA za pomocą technologii underfill wykonywanej bezkontaktowo.
Urządzenia te są tak wyspecjalizowane, że mają inną specyfikację w przypadku nakładania lakierów i powłok konformalnych, a inną w przypadku nakładania klejów SMA, past lub topników. Szczególną cechą takich zaawansowanych platform jest możliwość pozycjonowania dynamicznego w technologii fids-on-the-fly, która skraca kilkakrotnie nieprodukcyjny czas pozycjonowania (fot. 6).
Reologia materiałów
Jeśli chodzi o reologię płynów, a więc zagadnienie ich zachowania się w czasie przepływu, to należy rozpatrywać ją w kilku aspektach, z uwagi na wiele inter-akcji pomiędzy podłożem, płynem montażowym, urządzeniem dozującym i warstwą automatyczną, których macierz decyzyjna jest wielowymiarowa.
Reologia należąca do mechaniki ośrodków ciągłych jest nauką młodą, doświadczenia są dopiero zdobywane i na bieżąco modyfikowane razem z powstawaniem nowych klejów, uszczelniaczy, past termoprzewodzących, zalew elektroizolacyjnych czy lakierów ochronnych. Nawet w rozwiniętych gospodarkach dziedzina ta jest nowa i nie jest wykładana na uczelniach technicznych. Stąd istotny staje się transfer wiedzy od specjalistów do przemysłu, gdyż kupowanie sprzętu w ciemno kończy się niejednokrotnie porażką.
Porównanie systemów nakładania płynów musi być rozpatrywane jakościowo, przy zrozumieniu całego procesu technologicznego, a nie jedynie poprzez porównania poszczególnych składników czy wyrwanych z kontekstu parametrów deklarowanych przez producenta.
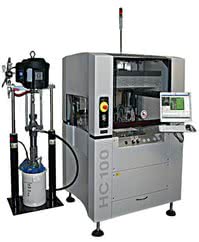
Fot. 6. Platforma in-line typu HC-100 firmy Nordson Dima stanowi znakomity pomost ułatwiający wdrożenie dozowania na linii montażowej
Wybranie właściwej technologii dozowania wymaga rozważenia przynajmniej następujących aspektów:
- dostosowanie systemu do płynu montażowego pod względem kompatybilności chemicznej i mechanicznej,
- panowanie nad zmianami lepkości płynu montażowego,
- uzyskanie powtarzalności dozowania dawki,
- panowanie nad sedymentacją wypełniaczy,
- stabilizacja temperatury podłoża,
- zdefiniowanie możliwości dozowania bezkontaktowego,
- kontrola rozpływu po nałożeniu,
- sposób i metoda utwardzania,
- kontrola jakości, założenie sprzężeń zwrotnych,
- zapewnienie raportowania i tworzenia logów produkcyjnych,
- informowanie systemu zarządzania produkcją (np. FIS).
Podsumowanie
Artykuł jest próbą pokazania, że porównanie systemów do nakładania, dozowania i mieszania płynów montażowych odbiega od stosowanych w branży elektronicznej zestawień, np. maszyn pick & place. Systemy dozujące wymagają specjalistycznych podzespołów, z których wiele ma konstrukcję chronioną patentami, a większość podlega ciągłym modyfikacjom, gdyż dziedzina dozowania przemysłowego materiałów płynnych istnieje dopiero około 50 lat, co jest okresem krótkim w rozwoju techniki i standardy jeszcze nie zostały ustanowione.
Marek Bernaciak