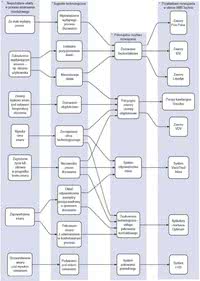
Rys. 1. Możliwe metody postępowania i istniejące przemysłowe rozwiązania w przypadku wystąpienia niepożądanych zjawisk w procesie montażowego nakładania smaru
Jednak to właśnie precyzyjne smarowanie w operacjach montażowych stanowi znaczną liczbę aplikacji, w których usprawnienia są czasem trudne do wykonania. Wiemy to dobrze, bo nasze rozwiązania nie spotykają się nawet z poważnymi kontrofertami. Dlaczego więc wiele osób nie wydaje się tym zagadnieniem specjalnie zainteresowane?
Jedną z odpowiedzi może być fakt, że smarowanie jest niedocenianą operacją i często bagatelizowaną. Wydaje się, że po prostu należy nanieść trochę smaru za pomocą pędzla lub zanurzyć element w oleju... i po sprawie. Uwagę inżynierów zwracają centralne układy smarowania oraz smarowanie jako proces w utrzymaniu ruchu, a w Internecie łatwiej znaleźć artykuł o smarowaniu ciała końską maścią niż informację o smarowaniu montażowym w produkcji.
W praktyce zagadnienie to jest znacznie bardziej złożone, niż się zwykle początkowo wydaje, a realizacja smarowania w operacjach montażowych stawia wysokie wymagania, takie jak:
- smarowanie musi zostać wykonane, a od jego niezawodności może zależeć ludzkie życie.
- smar jest nakładany tylko raz, w czasie montażu i operacja smarowania nie będzie nigdy później możliwa,
- smar nie może pobrudzić użytkownika lub jego ubrania,
- nakładanie smaru wymaga wysokiej precyzji, a tylko od niej zależy trwałość urządzenia,
- element nieposmarowany jest brakiem, który nadaje się wyłącznie do utylizacji,
- smar ma trudne do ustabilizowania właściwości,
- smar jest bardzo drogi i zależy nam na jego oszczędnym nałożeniu.
W dalszej części omówione zostaną tylko wybrane zagadnienia z powyżej wymienionych oraz w miarę możliwości pokazane zostaną przykłady. Na rysunku 1 pokazane zostały możliwe metody postępowania i istniejące przemysłowe rozwiązania w przypadku wystąpienia niepożądanych zjawisk w procesie montażowego nakładania smaru.
Złożoność zjawiska smarowania
Jednym z przypadków, w których od niezawodnego smarowania zależy życie ludzkie, jest smarowanie wiązań narciarskich. Są one smarowane tylko w czasie montażu w produkcji, później powierzchnia smarowana nie jest dostępna. Zresztą gdyby była, mogłaby zostać zanieczyszczona w czasie eksploatacji lub niestarannej konserwacji.
Smar o specjalnych właściwościach przeszedł operację przepakowania w małe opakowania produkcyjne, które zostały dokładnie pozbawione pęcherzyków powietrza. Jakiekolwiek wtrącenia powietrza mogłyby bowiem uniemożliwić niezawodność procesu smarowania. Dawka bowiem wynosiła tylko ok. 3 mg na jedno wiązanie, więc nawet niewielki bąbelek wprowadzałby znaczne zaburzenie procesu.
W myśl koncepcji zarządzania jakością W.E. Deminga jakość zależy od prawidłowo opracowanego procesu, a nie od jego kontroli. W tym wypadku przez ostatnie 10 lat wyprodukowano około 100 mln wiązań - nie mamy informacji o żadnych brakach, a jedyną informacją zwrotną są regularne zamówienia na przepakowany w laboratorium AMB Technic, odpowietrzony smar.
Smary są wrażliwe na złe dozowanie
Smary, zwłaszcza te o wysokich parametrach, są bardzo wrażliwe na obróbkę, jak pompowanie, mieszanie i nakładanie. W tych operacjach zachodzą niepożądane procesy, np. rozwarstwianie się oleju lub koagulacja uszlachetniających dodatków (np. teflonowych). W takich wypadkach ważną operacją jest dostarczenie smaru z opakowania handlowego, które często nie jest dostosowane do operacji montażowych.
Smary, które bardzo często okazują się wrażliwe na wysokie ciśnienia pompowania, można zabezpieczyć przed takim zagrożeniem poprzez przepakowanie do niskociśnieniowego podajnika smaru lub kartusza technologicznego. Zwykle stosowane pompy wysokociśnieniowe nie tylko poddają smar sprężaniu do kilkuset czasem atmosfer, ale utrzymują go w tym stanie przez wiele godzin, a nawet miesięcy. Nic dziwnego, że smary, które w uproszczeniu są jakby "gąbkami" nasyconymi olejem, wydzielają z siebie olej i tracą zaprojektowane przez producenta właściwości smarne i aplikacyjne.
Jedną z sytuacji praktycznych, z jakimi spotkaliśmy się w naszej pracy była destrukcja delikatnego smaru, który zostawiony na wiele godzin pod ciśnieniem wyższym niż tylko 2 bary ulegał koagulacji. Pojawiały się wtrącenia, rodzaj kłaczków i zgrubień, które zatykały dysze dozujące precyzyjnych zaworów. Zastosowanie niskociśnieniowego układu zasilania zapobiegło niepożądanym efektom, a proces został ustabilizowany.
Znanym zjawiskiem jest też niepożądane starzenie się smaru, które zachodzi, nawet gdy materiał jest pozostawiony pod niskim ciśnieniem. Czasami w operacjach montażowych zużywane są bowiem ilości na tyle niewielkie, że opakowanie handlowe okazuje się zbyt duże, by zużyć je w czasie dopuszczalnego przez producenta czasu. Okres ten jest dodatkowo skrócony przez niepożądane wysokie ciśnienie pompowania. W takiej sytuacji skorzystanie z możliwości przepakowania smaru w mniejsze opakowania technologiczne umożliwia nie tylko zaoszczędzenie na materiale, ale dodatkowo stabilizuje proces, czyniąc go powtarzalnym.
Dozowanie smaru
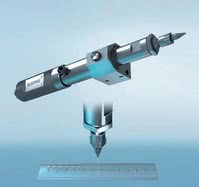
Fot. 2. Zawór IDV firmy SOMA, podający objętościowo i bezkontaktowo dawkę smaru, uniezależnia dozowanie smaru od zmiany jego lepkości w wyniku zmian temperatury
W przypadkach, gdzie ważne jest dokładne i powtarzalne, a przy tym szybkie dozowanie smaru niepodważalną alternatywą są zawory umożliwiające całkowicie bezkontaktowe jego dozowanie. Takie rozwiązania oferują kilka korzyści. Poszczególne dawki są podawane impulsowo, co pozwala na "digitalizację" dawkowania smaru. Każda dawka w procesie produkcyjnym może zostać zrealizowana jako wielokrotność podstawowej, która może być bardzo mała. Daje to możliwość całkowicie liniowego zwiększania dawki w funkcji liczby impulsów, co jest łatwe do realizacji w czasie budowania stanowiska produkcyjnego.
Dozowanie jest niezależne od fluktuacji lepkości smaru wywołanej choćby zmianami temperatury. Smary, jak wiele organicznych substancji, zmieniają swoją lepkość pod wpływem temperatury i to w praktyce przemysłowej jest częstym, choć bagatelizowanym zjawiskiem. Ponadto dozowanie jest prowadzone z odległości od kilku do kilkudziesięciu milimetrów. W procesach, gdzie zaangażowane są roboty pozycjonujące detal względem końcówki zaworu (lub odwrotnie), można pominąć ruchy zbliżające zawór oraz detal i prowadzić nakładanie nawet "w locie".
Zawory bezkontaktowe są produkowane w dwóch wersjach: całkowicie wolumetrycznej i quasi-wolumetrycznej. Warto zwrócić uwagę na to zjawisko i dopytać potencjalnego dostawcę, na ile oferowane rozwiązanie jest zaawansowane technicznie i daje określone korzyści przy zakupie.
Zawory objętościowe mają, jak każde rozwiązanie techniczne, swój zakres pracy. Dobór określonego zaworu jest sprawą kluczową, bo jeśli jednorazowa dawka będzie zbyt mała, zawór powinien mieć możliwość szybkiego "przeładowania", by wykorzystać technikę kilkukrotnego dawkowania. W innym wypadku konieczna może się okazać inwestycja w kilka zaworów pracujących równolegle albo zamiennie, co zajmuje czas, miejsce i angażuje niepotrzebnie środki finansowe.
Dozowanie objętościowe jest odpowiedzią na niestabilność smaru wywołaną zmianami temperatury, ale także zmianami lepkości związanymi ze zmianą partii towaru lub w czasie przechowywania smaru. Skorzystanie z możliwości przełożenia smaru w mniejsze opakowania technologiczne redukuje ten wpływ. Ogranicza także koszty zapasów magazynowych oraz marnotrawstwo związane z utylizacją niewykorzystanego, bo przeterminowanego smaru.
Współczesne precyzyjne pompy kawitacyjne, sterowane za pomocą serwonapędów, pozwalają na ciągłe dozowanie materiałów gęstych, takich jak smary i oleje, również w procesach ciągłych, ale o zmiennej prędkości. Można bowiem dostosować prędkość wypływu do prędkości linii lub prędkości robota tak, żeby na jednostkę powierzchni została nałożona jedynie taka ilość środka smarnego, która jest konieczna ze względów technicznych.
Wprowadzane są połączenia pomp kawitacyjnych z zaworami specjalnymi, co daje nieskończenie wielkie możliwości procesowe. Ponieważ jednak poruszone tu zagadnienie charakteryzuje zbyt duża liczba zmiennych, warto skorzystać z możliwości testów laboratoryjnych w profesjonalnym laboratorium aplikacyjnym.
Podsumowanie
Czy systemy precyzyjnego smarowania montażowego są wydatkiem? Z pewnością są. Czy to jest wydatek uzasadniony? Nasze doświadczenie w dotychczasowych przypadkach pokazuje, że obniżenie kosztu przypadającego na jednostkę produktu, ze szczególnym uwzględnieniem kosztów pozaprodukcyjnych, takich jak reklamacje, koszty nadzoru i kontroli, zwroty i poprawki, pozwalają na zwroty inwestycji liczone w pojedynczych miesiącach.
Jeśli więc potrzebujecie Państwo zredukowania kosztów jednostkowych oraz pewnego procesu, najlepsze, co można zrobić, to przyjrzeć się załączonemu diagramowi i przymierzyć go do swoich procesów produkcyjnych. Chętnie udzielimy odpowiedzi na każde pytanie, jakie się w tej sytuacji może pojawić.
Marek Bernaciak
AMB Technic
www.amb.pl