Przede wszystkim należy dokonać wyboru, czy decydujemy się na terminale przyłączeniowe (terminal bloki), czy system gniazdo-wtyk. Te pierwsze stosujemy w przypadku małej liczby podłączanych przewodów lub braku konieczności częstego rozłączania układu. Druga opcja zazwyczaj używana jest, jeśli producent urządzenia chce zapewnić klientowi/instalatorowi łatwość montażu lub ewentualnego serwisu - rozłączenie układu polega na wypięciu wtyków z gniazd, bez konieczności żmudnego rozszywania wiązki. Gwarantuje to także uniknięcie pomyłek podczas ponownego montażu.
W obu opcjach możemy wybierać między różnymi sposobami przyłączania przewodów - za pomocą śruby, sprężyny, zaprasowywania lub nacinania izolacji. Warto poznać pokrótce specyfikę każdego takiego rozwiązania.
Sposoby przyłączania przewodów
Przyłącze śrubowe jest najczęściej spotykane. Główną przyczyną ciągłej popularności jest przyzwyczajenie instalatorów do tego typu rozwiązania (jest ono tak intuicyjne, że każdy jest w stanie sobie z nim poradzić), a także przekonanie, że mocne dokręcenie śruby zapewni właściwy styk, gwarantując niską rezystancję połączenia.
Warto tu rozróżnić dwa systemy - z prostym blaszanym ochronnikiem przewodu oraz z klatką windową. Rozwiązanie bez blaszki ochronnej należy wykluczyć, gdyż dokręcanie śruby w złączu bezpośrednio do żyły przewodu powoduje jej ewidentne uszkodzenie. Ochronnik może być stosowany w mniej odpowiedzialnych aplikacjach (warto zwrócić uwagę na kształt komory przewodu - jeśli jest okrągła, to przy pierwszym przykręceniu żyły o małym przekroju ochronnik na pewno ulegnie odkształceniu, utrudniając wyjęcie przewodu i stwarzając problemy przy ponownym jego podłączeniu).
Do aplikacji, gdzie niezawodność systemu jest krytyczna, warto wybrać rozwiązanie z klatką windową. Złącza z oferty firmy Phoenix Contact mają klatkę, która zapewnia odporność na wibracje oraz zwalnia z okresowej kontroli i dokręcania śruby złącza. Uzyskano to przez specjalny kształt elementu, który zapewnia automatyczne zaciskanie się gwintu na śrubie. Dodatkowo zapewniona jest szeroka tolerancja przekrojów przyłączanych przewodów oraz skuteczna ochrona przed ich uszkodzeniem.
Coraz częściej projektanci urządzeń decydują się na przyłącze sprężynowe znacznie przyspieszające montaż. Konstrukcje sprężyn dociskowych w złączach opracowanych w firmie Phoenix Contact gwarantują niską rezystancję połączenia, a także odporność na wibracje. Tutaj także można wybierać spośród kilku wariantów.
Złącza z klatkową sprężyną napinającą wymagają użycia narzędzia (wkrętaka) zarówno przy podłączaniu, jak i odłączaniu przewodu. Jego końcówkę należy wcisnąć w odpowiedni otwór, otwierając w ten sposób komorę zacisku. Po wprowadzeniu przewodu i wysunięciu wkrętaka sprężyna dociska przewód do styku. Alternatywnie dostępna jest wersja z dźwigienką, którą należy nacisnąć w celu otwarcia komory.
Inna opcja to sprężyna typu Push-In, gdzie podczas podłączania przewodu w postaci drutu lub linki z zaciśniętą tulejką wystarczy go wcisnąć w odpowiedni otwór złącza. Specjalna konstrukcja elementu dociskowego zapewnia w miarę niskie siły wtykania, gwarantując jednak odpowiedni docisk do elementu stykowego a także zabezpieczenie przed wyrwaniem przewodu. Zwolnienie żyły następuje po wciśnięciu oznaczonego przycisku obok przewodu lub poprzez wsunięcie wkrętaka w odpowiedni otwór (w zależności od wybranej wersji złącza). W przypadku terminali przyłączeniowych można wybrać kształt i lokalizację przycisku zwalniającego tak, aby zapewnić jak najwygodniejszą obsługę. Do specyficznych aplikacji dostępne są warianty specjalne, np. w postaci sprężyny Push-In połączonej z dźwignią zwalniającą (dla większych przekrojów, np. 16 mm²).
Producenci wiązek kablowych preferują połączenia zaciskane - pozwalają one na szybki i pewny montaż za pomocą maszyn, które są ich standardowym wyposażeniem. Po zdjęciu izolacji z przewodu i nałożeniu na niego elementu stykowego ulega on zaprasowaniu, tworząc doskonałe połączenie elektryczne. Następnie element stykowy wraz z kablem jest zatrzaskiwany w komorze złącza.
Innym stosowanym i sprawdzonym sposobem przyłączenia przewodu jest styk nacinający (lub przebijający) izolację. Jest on o tyle wygodny, że nie wymaga wstępnej obróbki przewodu (zdjęcia izolacji, zaciśnięcia tulejki kablowej), co znacznie przyspiesza proces montażu. W przypadku terminali przyłączeniowych oraz wtyków żyłę przewodu wprowadza się w otwór złącza, a następnie palcami (dla małych przekrojów), szczypcami (dla złączy wielobiegunowych) lub wykorzystując wkrętak jako dźwignię (dla większych przekrojów), wsuwa się żyłę pomiędzy noże przecinające izolację.
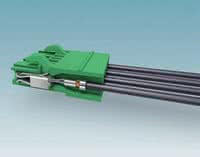
Rys. 4. Wtyk z przyłączem zaciskanym daje się łatwo wdrożyć do wielkoseryjnej produkcji wiązek kablowych. Styki dostarczane są na szpuli do automatu zaciskającego
Miejsce styku żyły z nożem, który jest jednocześnie elementem stykowym, jest ściśle otoczone tworzywem izolacji, zapewniając gazoszczelność połączenia, co przekłada się na wysoką odporność na ewentualną korozję. Należy jednak trzymać się zaleceń z kart katalogowych odnośnie do dopuszczalnego przekroju żył, gwarantując tym właściwy docisk elementów w miejscu styku, zakresu temperatur (-25...50°C) oraz rodzaju izolacji (najczęściej stosowane są PCW i PE).
Temperatura instalacji jest istotna, ponieważ w jej niższych wartościach izolacja jest zbyt twarda, a w wyższych zbyt plastyczna, co może spowodować niecałkowite jej przecięcie. Inny materiał izolacji można zastosować, ale wymaga to przeprojektowania konstrukcji styku nożowego - jeśli brany pod uwagę jest duży wolumen produkcji, należy taką opcję rozważyć wspólnie z producentem złącza.
Szeroka gama złączy do druku firmy Phoenix Contact pozwala także na wybór terminalu lub wtyku z odejściem przewodu w konkretnym kierunku, co pozwala na swobodną aranżację przyłączy do dowolnego urządzenia. Dzięki takiej mnogości dostępnych opcji konstruktor ma możliwość swobodnego projektowania, bez konieczności kompromisu pomiędzy wygodą a jakością połączenia oraz dostosowaniem do warunków, w jakich przyjdzie pracować jego urządzeniom.
inż. Piotr Andrzejewski
Phoenix Contact
www.phoenixcontact.pl