Jedno jest pewne – niezmienny pozostanie główny trend związany z rozwojem elektroniki, jakim jest miniaturyzacja. Można więc spodziewać się wprowadzania coraz mniejszych obudów elementów elektronicznych, a to z kolei pozwoli zwiększać gęstość ich upakowania na PCB. Mniejsze obudowy to również mniejszy raster wyprowadzeń, a więc konieczność zmniejszania grubości ścieżek i zwiększania precyzji ich prowadzenia. Niewątpliwie wzrastać będzie liczba wyprowadzeń układów elektronicznych, co wymusi konieczność wprowadzania nowych typów obudów. Przy tak dużym zagęszczeniu wyprowadzeń normą będą wielowarstwowe płytki drukowane. Właściwie taki stan już osiągnęliśmy.
Można sobie wyobrazić, jakie mogłyby być skutki wad produkcyjnych obwodów drukowanych, gdy po zmontowaniu układu, składającego się często z drogich elementów, nie jest możliwe jego uruchomienie wynikające na przykład ze zwarcia dwóch ścieżek w wewnętrznych warstwach płytki albo w przerwach, czy to w ścieżkach czy w przelotkach. Kluczowy staje się więc wymóg takiego projektowania PCB, aby był spełniony warunek testowalności zarówno samej, gołej płytki, jak i całego zmontowanego na niej układu. Przez cały proces opracowywania płytki drukowanej projektant musi brać pod uwagę podstawowe cechy wymagane do testów elektrycznych: testy mające na celu identyfikację wad produkcyjnych lub montażowych PCB. Innymi słowy, już na etapie projektowania płytki muszą być brane pod uwagę wymagania związane z produkcją. Określa się to angielskim terminem Design for Manufacturability (DFM).
Projekt do testowania gołej płytki
Zdecydowana większość połączeń urządzeń elektronicznych zawarta jest w obwodach drukowanych. Połączenia te, biorąc pod uwagę technologie produkcji współczesnych PCB, są niekiedy bardzo skomplikowane. Proces produkcji obwodów drukowanych jest wieloetapowy i wymaga ciągłej i szczegółowej kontroli na każdym z nich. Staje się to tym trudniejsze, im bardziej złożony jest obwód.
Jedną z metod kontroli jest AOI – Automated Optical Inspection, czyli automatyczna inspekcja optyczna. Inna, choć podobna metoda, to powiększona inspekcja wizualna (augmented optical inspection). Niezaprzeczalną zaletą obydwu tych metod jest ich bezkontaktowość, ale może to być niestety również wada wynikająca z pewnych ograniczeń. Z wyjątkiem obwodów jedno- i dwuwarstwowych o małej gęstości, wielowarstwowe płytki drukowane, a zwłaszcza odmiany o dużej gęstości, będą wymagały bardziej wyszukanej weryfikacji produktu końcowego. Aby zaświadczyć, że gotowa płytka jest wolna od wad i będzie działać zgodnie z projektem, niezbędne jest przeprowadzenie testów elektrycznych na czystej, niezmontowanej jeszcze płytce.
W ramach testów przeprowadzane są pomiary pojemności i rezystancji. Doprowadzenie odpowiednich wymuszeń prądowych do poszczególnych węzłów sieci połączeń na płytce, a następnie sondowanie każdej z nich pozwala zmierzyć występujące w różnych punktach płytki pojemności. Z kolei pomiary rezystancji na końcach ścieżek pozwalają wykryć ewentualne przerwy lub zwarcia.
Należy zwrócić uwagę na to, że rezystancje ścieżek, choć generalnie są bardzo niskie, to jednak zależą w pewnym stopniu od długości połączeń, a także od pola przekroju poprzecznego ścieżki. Może więc okazać się, że gdy badane będą dwie ścieżki tego samego materiału i tego samego przekroju poprzecznego, ale różnych długości, wyniki pomiarów ich rezystancji będą w takim samym stosunku jak długości tych ścieżek. Analogicznie, jeśli mierzone będą dwie ścieżki wykonane z tego samego materiału, mające tę samą długość, ale różniące się grubością miedzi, to stosunek rezystancji tych ścieżek będzie taki sam jak stosunek powierzchni przekroju poprzecznego miedzi tych ścieżek.
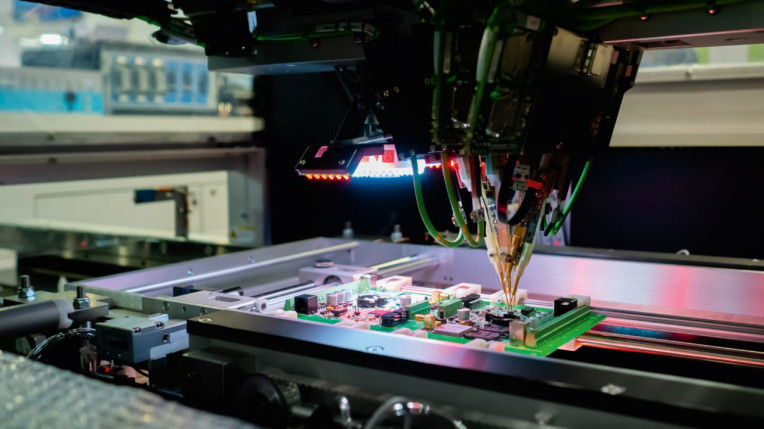
Metodologie testowania płytek drukowanych
Do testowania płytek drukowanych stosowane są generalnie dwie metody: z sondą stałą i sondą latającą. Każda z nich pozwala wykrywać wady produkcyjne PCB, a więc już we wczesnych fazach produkcji urządzeń. Kierowanie do montażu wadliwych płytek mogłoby skutkować poważnymi konsekwencjami finansowymi.
Firmy wykonujące płytki drukowane na zamówienie często oferują testowanie jako opcję zlecenia. Z możliwości tej warto korzystać, szczególnie w przypadku skomplikowanych połączeń na płytce.
Która metoda testowania będzie najlepsza? Trudno udzielić jednoznacznej odpowiedzi. Na pewno w dużym stopniu zależy to od wielkości produkcji. Jeśli liczba wykonywanych płytek drukowanych jest niewielka, na przykład w przypadku serii prototypowych czy produkcji niskoseryjnej albo też produkt podlega dalszym udoskonaleniom lub modyfikacjom, sensownym wyborem jest test sondą latającą. Koszt takiego testu jest obliczany dla każdej badanej sztuki, więc dla małych serii koszt konfiguracji i przetwarzania będzie minimalny. Trzeba jednak pamiętać, że przepustowość stanowiska testowego z sondą latającą będzie mniejsza niż analogicznego stanowiska z sondą stałą. Po osiągnięciu docelowych parametrów urządzenia, a więc często po wielu modyfikacjach, gdy produkt zostanie już ustabilizowany, a wymagana jest produkcja setek lub tysięcy jednostek tygodniowo lub miesięcznie, koszty konfiguracji związane z opracowaniem oprzyrządowania i oprogramowania stanowiska z sondą stałą mogą być uzasadnione.
Testowanie sondą stałą
Testowanie wielowarstwowych płytek drukowanych o dużej skali upakowania elementów i skomplikowanych połączeniach może wymagać jednoczesnego dostępu do wszystkich połączeń. W takim przypadku często są stosowane systemy ze stałymi sondami. Niestety, w tym przypadku stanowisko musi być indywidualnie przygotowywane do każdego projektu. Często jest ono nazywane łóżkiem z igłami, które bynajmniej z fakirami nie ma nic wspólnego (rys. 1). Stanowisko takie jest wyposażone w sprężynowe zaciski sondy, które mają dostęp do każdej sieci połączeń na płytce drukowanej.
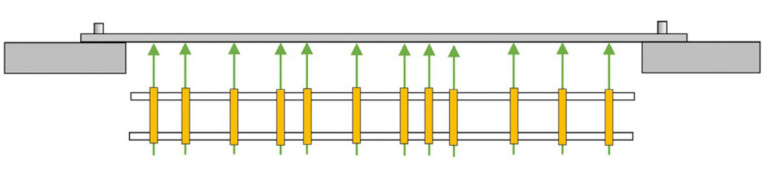
Przed rozpoczęciem testów każde stanowisko musi być indywidualnie przygotowane i skonfigurowane. Płytki są mocowane w odpowiednich uchwytach. Czynność ta musi być jednak wykonana bardzo precyzyjnie, tak aby zapewnić dopasowanie pól testowych do sond, które będą następnie na nie opuszczane. Bardzo często, można nawet powiedzieć, że zwykle, płytki wymagają dołączania sond z obu stron – od góry i od dołu. Zapewnia to odpowiednio skonstruowana platforma. Jedno stanowisko może liczyć nawet kilkaset sprężystych igieł dołączanych do pól testowych.
Rzeczywisty cykl testowy jest bardzo szybki. Test w zasadzie polega na ocenie, czy dana płytka jest sprawna, czy nie, dlatego jest nazywany "go and no-go". Jeśli okaże się, że dany egzemplarz został zakwalifikowany jako wadliwy, możliwa jest identyfikacja typu usterki, a nawet konkretnej jej lokalizacji.
Jak widać, testowanie sondą stałą jest szybkie i wydajne. Jest to jednak metoda wymagająca opracowania oprzyrządowania i programu testowego kierowanego specjalnie do konkretnego przypadku. Pociąga to oczywiście spore koszty, które ponadto muszą być powtarzane po każdej, choćby najmniejszej zmianie dokonanej na płytce. W takich przypadkach należy liczyć się z modyfikacją platformy utrzymującej igły pomiarowe, a w najgorszym przypadku nawet całą jej wymianę.
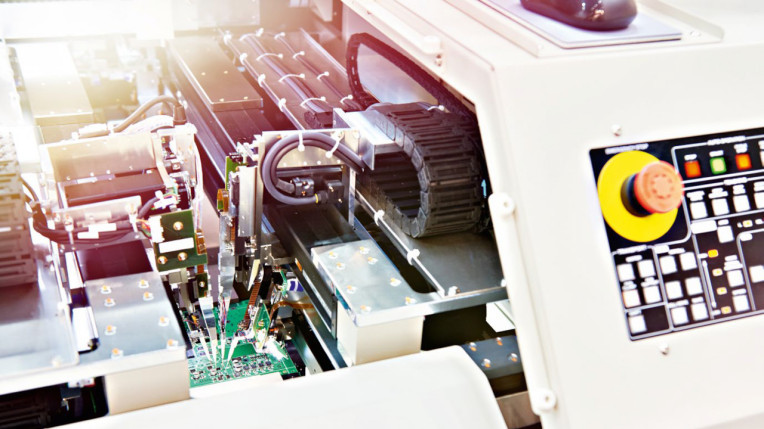
Testowanie sondą latającą
Stanowiska z sondami latającymi zostały skonstruowane specjalnie do testowania płytek o bardzo dużym upakowaniu elementów i ścieżek. Nie mają one sztywno ustawionych igieł pomiarowych, tak jak w stanowiskach z sondami stałymi. Oczywistą korzyścią tego rozwiązania jest znaczne obniżenie kosztów przygotowania stanowiska i kosztów prowadzenia testów. Niestety, ideały jak wiadomo nie istnieją, i obok wielu niepodważalnych zalet, sondy latające mają też pewne wady. Przyjrzyjmy się budowie stanowiska z latającymi sondami przedstawionego na rysunku 2. Składa się ono z 4 do 8 sond, które mogą stykać się zarówno z górną, jak i dolną stroną płytki. W przeciwieństwie do sond stałych, sondy latające mogą przemieszczać się po całej powierzchni PCB. Czuwa nad tym program przygotowany specjalnie dla każdej płytki. Test przebiega więc wyraźnie wolniej niż w przypadku sond stałych. Ograniczona jest też liczba jednocześnie testowanych sieci połączeń. Pełny test może także wymagać wykonania kilku cykli pomiarowych. Korzyścią jest natomiast łatwa adaptacja stanowiska potrzebna do kontynuowania testów po dokonaniu zmian na płytce. Zmiany dotyczą wyłącznie oprogramowania, nie trzeba przeprojektowywać całej platformy z sondami.
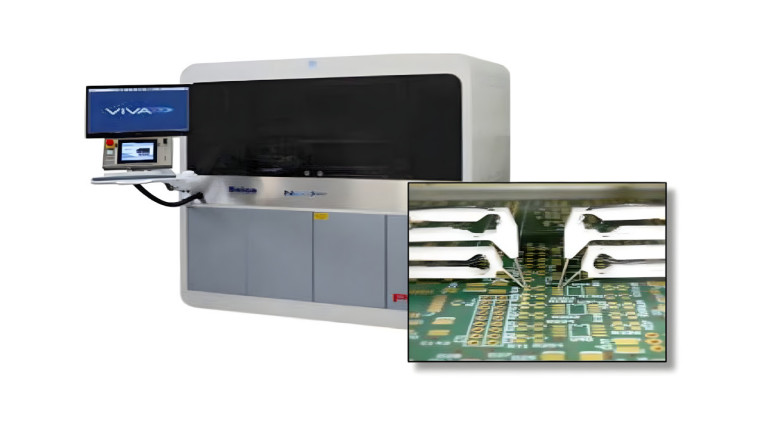
Podsumujmy zatem zalety stanowiska testowego z sondą latającą:
- eliminuje koszty i czas przygotowania oprzyrządowania,
- umożliwia szybkie opracowanie programu testowego, co przekłada się na łatwą integrację zmian projektowych,
- zapewnia dużą swobodę dostępu praktycznie do dowolnego miejsca na płytce, nawet w przypadku braku punktów testowych,
- sterowany programowo kontakt sondy z punktem pomiarowym, programowalny dla dowolnego typu płytki,
- zapewnia stosowanie różnych rozwiązań testowych zintegrowanych w jednym systemie testowym,
- zapewnia zintegrowane pozycjonowanie i precyzję pomiaru .
Igły sondy latającej nie mogą jednak zapewnić pełnego testu parametrycznego, co jest możliwe w testerach z sondą stałą. Stanowi to problem podczas testowania wysokiej jakości wyrobów wojskowych, lotniczych i medycznych. Zazwyczaj wymagają one jednoczesnego testowania PCB pod kątem przerw i, co ważniejsze, zwarć. Z tego względu stanowiska do testowania płytek o bardzo dużej złożoności mogą wymagać stosowania dodatkowego mocowania igieł, a nawet kilku takich mocowań.
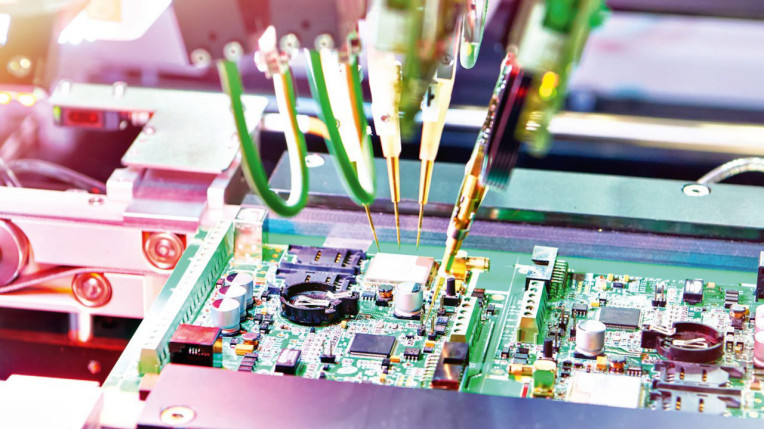
Przesyłanie danych do testu na płytce drukowanej
Przygotowanie stanowiska z latającą sondą do testu danej płytki wymaga zebrania szeregu informacji umożliwiających opracowanie odpowiedniego oprogramowania i ewentualnego osprzętu. Potrzebne dane to:
- szczegóły mechaniczne,
- przekrój warstwy,
- lista połączeń,
- dane CAD (plik Gerber).
Na tej podstawie można sformułować prosty przewodnik, w którym zostały zebrane wskazówki ułatwiające przygotowanie stanowiska. Zalecenia dotyczą konkretnej firmy wykonującej testy, nie muszą być więc uniwersalne. Zlecając produkcję płytek z ich testowaniem, zawsze warto upewnić się, czy istnieją jakieś ograniczenie lub wymagania dotyczące testów.
- Zapewnienie dostępu do wszystkich połączeń z dolnej powierzchni płytki. Można zaryzykować stwierdzenie, że zdecydowana większość obecnie produkowanych płytek jest na tyle złożona, że konieczne jest rozmieszczanie sond po obu stronach płytki, a to wiąże się z drastycznym skomplikowaniem oprzyrządowania. Bezpośrednią tego konsekwencją jest nawet podwojenie kosztów testu.
- Igła sondy powinna zapewniać bardzo dobry styk z testowanym połączeniem. Można przyjąć, że powierzchnia styku gwarantująca niezawodny kontakt ma kształt koła o średnicy 0,030 cala (~0,75 mm). Jest to parametr, który w wielu przypadkach jest możliwy do realizacji, ale firma testująca płytki musi być przygotowana na dużo bardziej wymagające przypadki. Jeśli konieczne okaże się zastosowanie sond o mniejszej powierzchni styku, oprzyrządowanie może wymagać "sond prowadzonych" (guided probes), co dodatkowo zwiększa złożoność oprzyrządowania testowego.
- Punkty styków sond powinny znajdować się nie bliżej niż 0,050 cala (~1,3 mm). Dostępne są wprawdzie mniejsze sondy, ale są one zazwyczaj delikatniejsze i bardziej wiotkie. Powoduje to pogorszenie jakości styku stwarzające niekiedy pewne problemy.
- Problemem jest również mała odległość między powierzchnią styku sondy a elementami znajdującymi się na płytce. Preferowana odległość między obudową elementu a środkiem powierzchni testowej nie powinna być mniejsza niż 0,060 cala (~1,5 mm). Umożliwi to dostęp do tych samych lokalizacji sondy podczas testu montażu.
- Należy zapewnić otwory pozwalające na stabilne mocowanie płytki na stanowisku testowym. W opisywanym przypadku wymagane są otwory o średnicy 0,125 cala (~3,2 mm) wywiercone w przeciwległych rogach płytki drukowanej.
Jak już było wspomniane, szczególne wymagania mogą być potrzebne do testu zwarć mierzącego izolację między poszczególnymi połączeniami. Test mierzy impedancje między połączeniami i sprawdza, czy mieszczą się one w ustawionej tolerancji. Impedancje są obliczane dla określonej częstotliwości prądu pomiarowego.
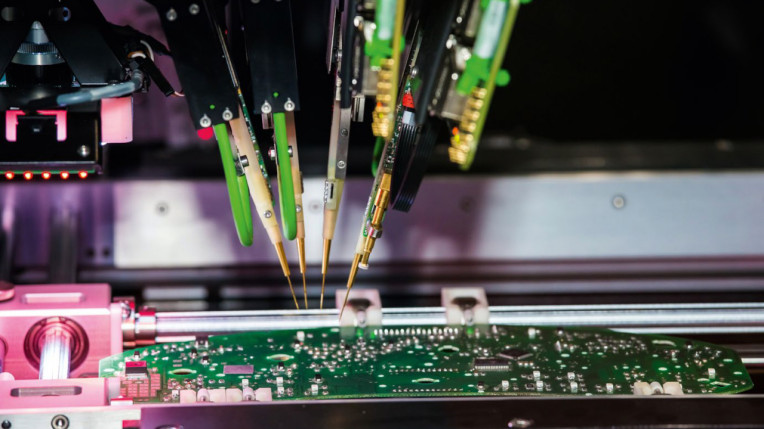
Należy pamiętać, że pełny test w ogólnym przypadku obejmuje nie tylko testy elektryczne, ale też funkcjonalne. Ale jest to już zupełnie inne zagadnienie.
Źródło: https://www.magazines007.com/pdf/Design007-Jan2022.pdf
Jarosław Doliński