Elastyczna elektronika, czyli komponenty i obwody zachowujące funkcjonalność podczas zginania, skręcania i rozciągania, ma duży potencjał zastosowań. Szybki postęp w jej zakresie, jaki nastąpił w ostatnich latach, przyspieszył również rozwój elastycznych układów MEMS. Te zminiaturyzowane, giętkie i rozciągliwe komponenty mechaniczne i elektroniczne zintegrowane na elastycznych podłożach dostosowują się do różnie ukształtowanych powierzchni oraz wytrzymują dynamiczne odkształcenia. Pozwala to na ich wykorzystanie w zastosowaniach wymagających bezpośredniego kontaktu z nieregularnymi i ruchomymi powierzchniami, takimi jak na przykład ludzka skóra i chwytaki robotów.
Materiały
Giętkie układy MEMS wykonywane są z materiałów elastycznych, o odpowiednich właściwościach wytrzymałościowych i parametrach elektrycznych, które są łatwe w obróbce. Dotyczy to podłoży, jak i warstw aktywnych.
Obiecującymi materiałami do produkcji podłoży są poliimidy. W tym zastosowaniu wyróżniają je: stabilność termiczna, minimalne pełzanie, wytrzymałość mechaniczna oraz właściwości izolacyjne. Ponadto są odporne na słabe kwasy i zasady, jak również na popularne rozpuszczalniki organiczne, na przykład etanol i aceton. Niektóre typy poliimidów są światłoczułe, co pozwala na ich obróbkę w procesie litografii. Postać, w jakiej występują (żel), ułatwia ich przetwarzanie. Po utwardzeniu w wysokiej temperaturze wytwarzają jednorodną powłokę. Niestety, brak zdolności do odzyskiwania kształtu po poddaniu silnym naprężeniom ogranicza ich zastosowanie jako wysoce rozciągliwego podłoża.
Kolejnym materiałem o dużym potencjale w dziedzinie podłoży elastycznych układów MEMS jest polidimetylosiloksan, zaliczany do silikonów. Jego ważne zalety to: łatwość obróbki, wytrzymałość mechaniczna, przezroczystość, rozciągliwość, zdolność do odzyskiwania kształtu po naprężeniu, skręceniu, ściśnięciu, obojętność chemiczna, zgodność biologiczna, stabilność termiczna. Materiały, które sprawdzają się jako podłoża giętkich układów MEMS, to oprócz tego m.in.: politereftalan etylenu, polinaftalan etylenu, poliuretan.
Tradycyjne materiały warstwy aktywnej, czyli folie metalowe oraz półprzewodnikowe, są sztywne i podatne na pękanie pod dużymi obciążeniami rozciągającymi. Alternatywą dla nich są nanodruty ze względu na ich elastyczność i właściwości elektryczne. Pod uwagę bierze się również nanorurki węglowe i grafen jako giętkie, dobre przewodniki, stabilne chemicznie, termicznie i skalowane w produkcji masowej. Ważną grupą materiałów są polimery przewodzące, jak PEDOT:PSS, polipirol i polianilina. Pod kątem wykorzystania jako materiały na warstwy aktywne elastycznych układów MEMS badane są oprócz tego kompozyty powstałe jako połączenie izolacyjnej warstwy polimerów z przewodzącymi wypełniaczami, takimi jak nanorurki, grafen, nanodruty.
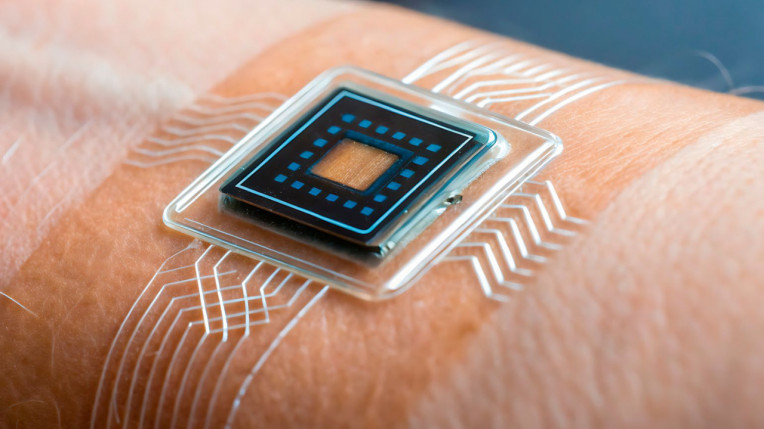
Procesy produkcyjne
Produkcja tradycyjnych układów MEMS wykorzystuje szereg technik, takich jak: fotolitografia, techniki trawienia, w tym trawienie na mokro i na sucho, na przykład trawienie jonami aktywnymi i plazmą sprzężoną indukcyjnie, metody osadzania, jak fizyczne oraz chemiczne osadzanie z fazy gazowej czy osadzanie warstw atomowych i galwanizacja. Ich dopełnieniem są techniki pakowania, które zapewniają integralność strukturalną i funkcjonalność układów MEMS.
Miękkość i podatność na odkształcenia elastycznych podłoży stanowią poważne wyzwanie dla tych technik. W związku z tym konieczne jest wykorzystanie sztywnych podłoży nośnych, wykonanych na przykład z krzemu albo szkła, które podtrzymują elastyczne podłoża docelowe podczas obróbki. Nośnik musi ściśle przylegać do giętkiego podłoża, by zapewnić stabilność i zapobiec jego rozwarstwianiu. Łączy je warstwa spoiwa, umożliwiająca oderwanie elastycznego układu MEMS od nośnika już po zakończeniu obróbki. Ta warstwa pośrednia musi być też odporna na żrące działanie odczynników, które są używane w procesie produkcyjnym. Przykładem jest klej silikonowy.
Druk
W produkcji giętkich układów MEMS wykorzystuje się również technikę druku, czyli osadzania na elastycznych podłożach materiałów warstwy aktywnej w postaci tuszy stanowiących ich mieszaninę z rozpuszczalnikiem. W zależności od techniki druku, pod wpływem ciepła (druk termiczny) albo zjawiska piezoelektrycznego (druk piezoelektryczny), dysza uwalnia krople tuszu. Te są następnie kierowane z określoną prędkością w kierunku podłoża, na którym osadzają się pod wpływem grawitacji oraz oporu powietrza. Po zetknięciu z nim, pod wpływem napięcia powierzchniowego, układają się w dany wzór. Kiedy rozpuszczalnik odparowuje, krople się zestalają.
Technika druku zapewnia oszczędność materiałów i precyzyjne oraz powtarzalne osadzanie warstw aktywnych na elastycznych podłożach różnego typu. Z drugiej strony jednak rozdzielczość pozioma wzorów drukowanych jest mniejsza niż ta osiągalna w procesie fotolitografii, zaś kontrola grubości warstwy jest mniej precyzyjna niż w metodach fizycznego i chemicznego osadzania z fazy gazowej.
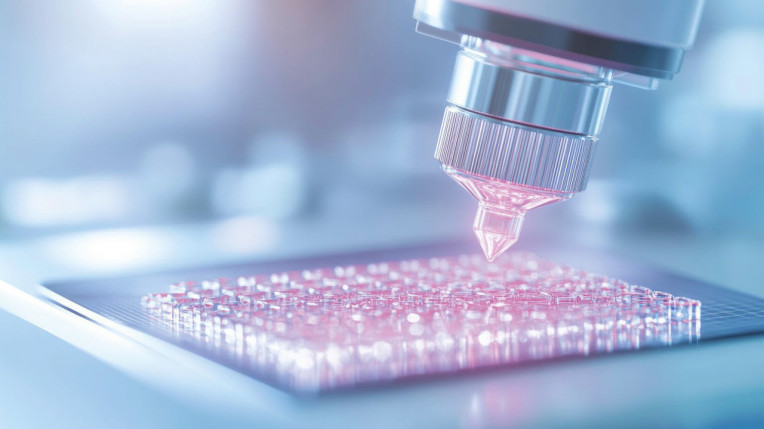
Druk transferowy
W produkcji elastycznych układów MEMS mają zastosowanie również techniki druku transferowego. Taką jest miękka litografia, w której wzory warstw aktywnych nanosi się na elastyczne podłoża z wykorzystaniem stempli. Technika ta jest prosta i opłacalna.
Proces miękkiej litografii ma dwa etapy: wytwarzanie szablonu oraz jego późniejsze wykorzystanie do przeniesienia wzoru na giętkie podłoże. Wzorniki są zazwyczaj wykonywane konwencjonalnymi metodami fotolitografii i trawienia.
W zakresie transferu wzoru w dziedzinie miękkiej litografii stosuje się różne podejścia. W jednym z nich mikrostrukturyzowany szablon zalewa się ciekłym polimerem, który po utwardzeniu zostaje od wzornika oderwany. W taki sposób wykonywana jest struktura, która odwzorowuje szablon. Żeby ułatwić usunięcie polimeru, na powierzchnię wzornika często nakłada się środek antyadhezyjny.
W drugim podejściu najpierw wykonuje się stempel, na przykład z polidimetylosiloksanu, przez uformowanie go na szablonie z krzemu. Następnie stempel jest pokrywany funkcjonalnym tuszem i dociskany do elastycznego podłoża docelowego. W taki sposób tusz w formie mikrowzoru zostaje przeniesiony na podłoże. Ta metoda zapewnia wierny transfer wzoru, zadowalającą rozdzielczość i przepustowość. Techniką druku transferowego, która odgrywa istotną rolę w produkcji elastycznej elektroniki, jest również sitodruk.
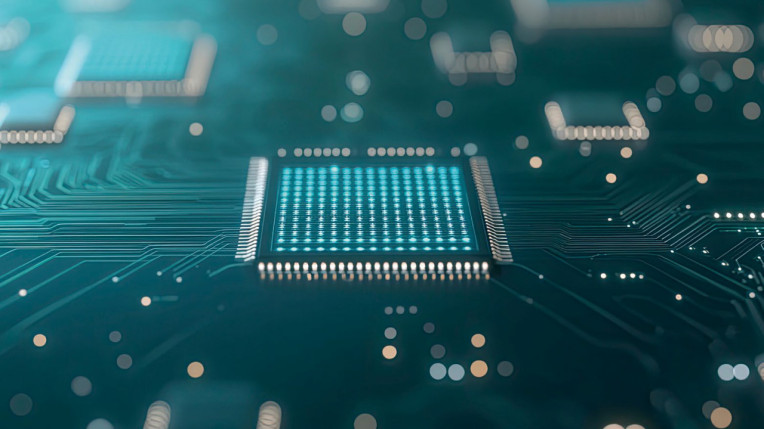
Elastyczne czujniki
Trwają prace nad wykorzystaniem przedstawionych materiałów i technik w produkcji elastycznych układów MEMS, na przykład sensorów. Przykładem są giętkie sensory ciśnienia, które przetwarzają ciśnienie mechaniczne na mierzalne sygnały elektryczne i mają potencjalnie szerokie zastosowania w elektronice noszonej, miękkiej robotyce, diagnostyce klinicznej i interakcji człowiek–komputer. Jedna z takich innowacyjnych aplikacji to sztuczna elektroniczna skóra. Można jej będzie użyć jako pokrycie humanoidalnych robotów opartych na sztucznej inteligencji, które będą mogły wchodzić w bezpośredni kontakt z ludźmi. Inne potencjalne zastosowanie to protezy skóry.
Prace nad elektroniczną skórą, która będzie miała właściwości zbliżone do cech naszej naturalnej powłoki, są prowadzone. Planuje się ją przykładowo wykonywać w postaci matrycy czujników ciśnienia wrażliwych na nacisk, zrealizowanych w oparciu o organiczne tranzystory polowe (Organic Field Effect Transistors, OFET) wbudowane w elastyczne podłoże. W jednej z takich realizacji dielektryk w strukturze OFET ma postać cienkiej, regularnie ustrukturyzowanej gumy, która jest ściśliwa. Bezpośrednia zależność prądu wyjściowego tranzystora OFET od jego pojemności umożliwia pomiar ciśnienia.
Jako materiał dielektryczny w OFET można wykorzystać polidimetylosiloksan, głównie ze względu na jego wspominaną zgodność biomedyczną z tkanką ludzką. Produkcja mikrostrukturyzowanych folii z tego materiału wymaga precyzyjnego procesu zapewniającego jednorodność i wysoką precyzję.
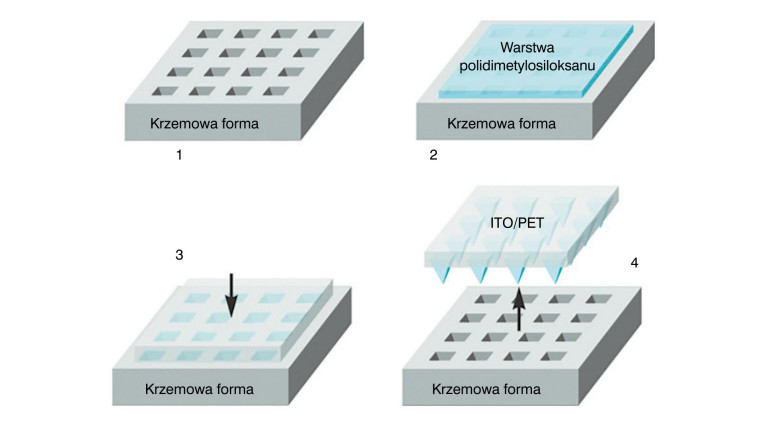
W przykładowej realizacji formę z krzemu zalewa się ciekłym polidimetylosiloksanem. Następnie materiał ten jest odgazowywany próżniowo i zostaje częściowo utwardzany. W kolejnym kroku formę pokrywa się warstwą ITO/PET, czyli folią z politereftalanu etylenu (PET) pokrytą tlenkiem indu i cyny (ITO), która jest przezroczysta i przewodzi prąd. Cała struktura jest ostatecznie utwardzana pod ciśnieniem w temperaturze kilkudziesięciu stopni Celsjusza przez kilka godzin. Przyłożenie równomiernego ciśnienia podczas utwardzania jest kluczowe dla uzyskania struktur czułych na ciśnienie o jednolitym rozkładzie na całej powierzchni. Po utwardzeniu elastyczne podłoże zostaje oderwane od formy (rys. 1).
Monika Jaworowska