Silniki bezszczotkowe tej samej mocy co komutatorowe są mniejsze i lżejsze, dzięki brakowi komutatora i szczotek są cichsze, są praktycznie bezobsługowe, a ich żywotność jest dłuższa. Mechaniczny interfejs szczotkowo-komutatorowy zostaje w nich zastąpiony elektronicznym z układami do zasilania i sterowania silnikiem.
Sterowniki wyposażone w odpowiednie algorytmy kontroli obrotów udoskonalają działanie tych silników. Ale dla ich zrozumienia trzeba przyjrzeć się działaniu elektromagnetycznej komutacji silników komutatorowych. Szczotki dostarczają uzwojeniom silnika napięcia w potrzebnej sekwencji. Grafitowe szczotki stykają się z kilkusegmentowym walcowym komutatorem, umocowanym na osi wirnika, zapewniając przełączanie w odpowiednich momentach. Przełączanie to maksymalizuje moment obrotowy wirnika w trakcie 360° jego obrotu.
W silniku bezszczotkowym tę rolę spełnia układ elektroniczny wraz z czujnikami Halla (rys. 1 i 2). Czujniki te synchronizują sterownik z chwilową pozycją wirnika. Silniki bezszczotkowe są zwykle wyposażane w trzy czujniki Halla, które naprzemiennie sterują dostarczaniem uzwojeniom stojana napięć odpowiedniej polaryzacji w miarę obrotów wirnika. Napięcia te są przesunięte w sposób zgodny z polami biegunów stojana. Zawsze wzbudzane są dwa z trzech uzwojeń.
Sterownik PWM
W systemie tradycyjnym silniki bezszczotkowe są zasilane przez wzmacniacz liniowy (rys. 4a). Sterowanie liniowe obciążenia rezystywnego przy średnim poziomie mocy cechuje się niską sprawnością 50%. Obecnie stosuje się modulację szerokości impulsów (PWM), która zamienia analogowe napięcie sterujące w ciąg impulsów o zmiennym współczynniku wypełnienia (rys. 4b).
Poczynając od zerowego współczynnika (brak impulsów), w miarę wzrostu szerokości impulsów silnik zaczyna wirować aż do osiągnięcia wymaganej szybkości i momentu obrotowego. Przy sterowaniu PWM straty występują tylko w rezystancji przewodzenia przełączającego MOSFET-a i diody zwrotnej, dzięki czemu sprawność napędu wynosi 80% do 95%. Przy dużych częstotliwościach przełączania straty te rosną.
Sterowanie PWM oprócz poprawy sprawności kontrolując szybkość i moment ogranicza natężenie prądu rozruchowego. Optymalna szybkość przełączania zależy od bezwładności, indukcyjności uzwojeń i zastosowania. Zwiększanie jej powiększa straty, a zmniejszanie ogranicza częstotliwościowe pasmo systemu i powoduje wzrost impulsowych tętnień prądu, które stają się niszczące dla sterownika.
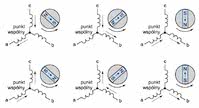
Rys. 3. W wyniku wirowania pól uzwojeń stojana pola dwóch wzbudzonych uzwojeń tworzą kąt prosty z polem stałego pola magnesu wirnika, co maksymalizuje chwilowy moment obrotowy
Do czasu pojawienia się wyspecjalizowanych scalonych sterowników projektanci trójfazowych silników bezszczotkowych musieli konstruować trzy oddzielne sterowniki bramek z sześciu MOSFET-ów. Przykładem współczesnego takiego scalonego trójfazowego sterownika silnika bezszczotkowego może być SA305. Ten układ firmy Apex dostarcza do 300 W mocy dzięki wyjściowym układom DMOS i sterującym układom logicznym CMOS. Jest wyposażony w ochronę nadprądową, przeciwzwarciową i termiczną.
Wyłącza się, gdy chwilowe natężenie prądu przekroczy 12 A. Zawiera trzy niezależne półmostki, dostarczające szczytowego prądu wyjściowego 10 A przy sterowaniu przez mikrokontroler lub DSP. W trakcie działanie jedno z uzwojeń silnika jest sterowane sygnałem o wysokim poziomie, drugie niskim, a na trzecie sygnał jest niepodawany. Poprawną synchronizację tej sekwencji zapewnia sprzężenie zwrotne przez czujniki Halla. Informują one nieustannie mikrokontroler o pozycji wirnika względem uzwojeń stojana.
Gdyby górna i dolna część półmostka sterownika przewodziły równocześnie, wystąpiłoby zwarcie skrośne, przeciążające układ i niszczące MOSFET-y. W SA305 zapobiega temu chwilowy czas martwy, który uniemożliwia włączenie drugiego z MOSFET-ów, zanim nie zostanie wyłączony pierwszy. SA305 sygnalizuje także defekty i monitoruje prąd w każdej z trzech faz silnika.
Każdy silnik bezszczotkowy może być kontrolowany przez mikrokontroler. Na przykład układ PIC18F2331 firmy Microchip zawiera 14-bitowy moduł PWM sterujący ruchem wirnika z zapobiegającym zwarciom programowalnym czasem martwym (rys. 5).
Działanie silnika bezszczotkowego
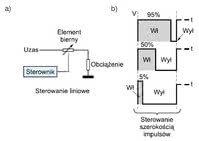
Rys. 4. Tradycyjna liniowa technika sterowania silnikiem (a) i zapewniająca wyższą sprawność technika sterowania za pośrednictwem PWM (b)
Jednym z krytycznych momentów w działaniu silnika bezszczotkowego jest przyłożenie napięcia do nieruchomego silnika. Wirnik wtedy nie dostarcza wstecznej siły elektromagnetycznej (Ewst), która wyraża się zależnością
Ewst=KN.S
gdzie KN oznacza stałą napięciową w V na tysiąc obr./min, a S oznacza szybkość w tysiącach obr./min.
Po przyłożeniu do silnika napięcia wirnik zaczyna się obracać i generować Ewst zgodnie z powyższą zależnością. Jeśli silnik jest napędzany napięciem stałym U, pobiera prąd o natężeniu I:
![]() |
gdzie U oznacza przyłożone napięcie, RS - rezystancję pary uzwojeń stojana, LS - indukcyjność pary uzwojeń stojana, a t - czas.
W równaniu tym chwilowa wartość natężenia prądu I jest funkcją wstecznej siły elektromotorycznej Ewst i stałej czasowej LS/RS. Rysunek 6 po lewej stronie przedstawia przebieg prądu, poczynając od stanu nieruchomości wirnika (Ewst = 0), charakterystyczny dla obwodu RL, narastający zgodnie ze stałą czasową L/R.
Jeżeli silnik nie jest zasilany napięciem stałym, lecz impulsowym PWM (rys. 6, po prawej), prąd narasta wykładniczo przez czas trwania pierwszego impulsu, a po jego zakończeniu wykładniczo maleje. Następny impuls napięcia wywołuje ponowny wzrost prądu, a jego przebieg w czasie przybiera zębaty kształt. Obroty silnika wzrastają, jego moment obrotowy jest wprost proporcjonalny do natężenia prądu. Trzy podstawowe parametry: przyłożone napięcie, częstotliwość przełączania i współczynnik wypełnienia PWM, mogą być programowane niezależnie. Od wyboru tych wielkości zależy przyspieszenie silnika, szybkość jego obrotów i moment napędowy.
Przykład
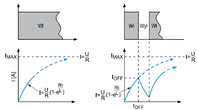
Rys. 6. Przebiegi prądowe w silniku bezszczotkowym zasilanym prądem stałym (z lewej) i zasilanym impulsowo PWM (z prawej)
Przykładowo silnik bezszczotkowy o małej bezwładności z momentem 0,049 kg·m przy 5000 obr./min charakteryzuje się rezystancją (RS) 1,2 Ω i indukcyjnością (LS) 2,6 mH każdej pary uzwojeń stojana. Stała momentu KM tego silnika wynosi 0,011 kg·m/A, a stała napięciowa KN 8,9 V/1000 obr./min.
W pierwszym kroku trzeba sprawdzić, czy dopuszczalne natężenie prądu 12 A w silniku nie zostanie przekroczone, co spowodowałoby wyłączenie układu scalonego sterownika.
Jeśli U/R > 12 A, to należy wziąć pod uwagę szereg czynników, w tym rezystancję 1,2 Ω RS. Jeżeli przyjmie się napięcie zasilania 60 V, to U/R = 60/1,2 = 50 A. Po przyłożeniu napięcia natężenie prądu w silniku początkowo rośnie zgodnie z powyższym równaniem, a w miarę zwiększania się Ewst zaczyna się zmniejszać (rys. 7).
W czasie normalnego działania silnika prąd wskutek oddziaływania wstecznej siły elektromotorycznej nigdy nie osiąga maksymalnej wartości. Przyspieszenie obrotów silnika jest wyznaczane jego momentem obrotowym i bezwładnością. Przy bardzo małej stałej czasowej L/R w stosunku do mechanicznej stałej czasowej prąd może osiągnąć maksimum, zanim rozwinie się Ewst. W opisywanym przykładowym układzie natężenie prądu silnika nie jest wyższe niż 8 A, sporo mniej niż 12 A.
Jeśli prąd ten mógłby przekroczyć dopuszczalną dla sterownika wartość , należałoby użyć w obwodzie szeregowego rezystora lub dławika, który ograniczyłby prąd szczytowy i di/dt, wpłynęłoby to jednak niekorzystnie na sprawność systemu. Prąd rozruchowy silnika przy napędzie PWM daje się kontrolować przez ograniczenie współczynnika wypełnienia sygnału impulsowego. W układzie SA305 takie sprzężenie zwrotne daje się łatwo wprowadzić.
Zastosowanie mikrokontrolera z monitorowaniem chwilowego natężenia prądu w każdej z faz pozwala utworzyć pętlę z algorytmem rozruchowym, pozwalającym przybliżyć się prądowi do granicy 12 A, ale jej nie przekroczyć. Warto zachować niewielką rezerwę i przyjąć na przykład 11 A. Dzięki temu uzyskuje się maksymalną szybkość rozruchu, ze współczynnikiem wypełnienia sterowanym czujnikami trzech faz.
KKP