W niniejszej części przedstawione zostaną typowe nieprawidłowości konstrukcji paneli przeznaczonych do automatycznego montażu, ich negatywne następstwa oraz wskazówki pozwalające projektować takie panele, które nie będą sprawiały problemów podczas produkcji oraz montażu pakietów. Na koniec omówione zostaną typowe uchybienia spotykane w specyfikacjach parametrów techno logicznych projektów oraz budowach obwodów wielowarstwowych.
Konstruowanie paneli
Większość obwodów drukowanych, szczególnie średnie i duże serie produkcyjne, umieszczana jest w panelach na potrzeby zautomatyzowanych linii montażowych. Mogą one być projektowane przez klientów lub - na podstawie ich wytycznych - przez producenta PCB. W przypadku, gdy klient potrzebuje panelizacji obwodów, ale nie dostarczył żadnych wytycznych, panel zostanie ułożony przez producenta, na bazie parametrów technologicznych projektu oraz swojego doświadczenia.
Niestety nie wszystkie panele klientów są ułożone w sposób prawidłowy, a spotykane błędy mogą prowadzić m.in. do wichrowania laminatu lub rozpadania się (depanalizacji) już na etapie produkcji. Niewłaściwy projekt może ponadto powodować dodatkowe problemy podczas montażu elementów, lutowania oraz w czasie depenalizacji zmontowanych pakietów.
Prawidłowo zaprojektowany panel charakteryzuje się możliwie dużą sztywnością, która zapewnia jego integralność na etapie obróbki mechanicznej podczas produkcji oraz przeciwdziała nadmiernemu uginaniu się laminatu pod ciężarem elementów w trakcie montażu i lutowania. Jednocześnie pożądane jest, aby charakteryzował się on możliwie łatwą obróbką mechaniczną.
Najprostszym typem paneli spełniającym wymienione kryteria są te, w których poszczególne obwody są w całości rylcowane (fot. 1). Mają one dużą sztywność, szczególnie dla grubszych laminatów (1 mm i więcej) i są przeznaczone do obwodów o prostokątnych kształtach wykonywanych na laminatach o grubości co najmniej 0,5 mm, w których mozaiki nie przylegają bezpośrednio do krawędzi obrysu, lecz są odsunięte od niej o 0,1 0,5 mm zależnie od grubości laminatu. Ich wadą jest gorsza tolerancja wymiarów w porównaniu do paneli frezowanych, uwarunkowana dokładnością samej operacji rylcowania oraz fakt, że krawędzie obwodów nie są idealnie prostokątne (rys. 1).
W przypadku paneli rylcowanych składających się z różnych obwodów należy pamiętać o przemyślanym ich rozmieszczeniu. Na rysunku 2a przedstawiono nieprawidłową konstrukcję tego typu. Jak widać, rylcowanie mniejszych obwodów uszkodzi powierzchnie większych, gdyż dla rylcowania skokowego (skipping, jumping scoring) potrzebna jest pewna droga do zatrzymania piły oraz jej podniesienia. Aby skorygować omawiany projekt, wystarczy oddzielić wiersze obwodów pasem laminatu o wysokości ?10 mm, co zabezpieczy dolny wiersz obwodów przed nacinaniem podczas rylcowania skokowego górnego wiersza (rys. 2b).
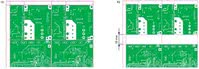
Rys. 2. Fragment nieprawidłowego (a) oraz właściwego (b) ułożenie rylcowanego panelu z różnych płytek
Panele dla laminatów cieńszych od 0,8 mm i/lub o nieregularnym kształcie obrysu powinny być konstruowane jako frezowane z mostkami (fot. 2). Panele frezowane stosuje się także w sytuacji, kiedy wymiary obwodów i ich tolerancje są krytyczne. W celu zapewnienia dużej sztywności i jednocześnie łatwej depenalizacji zmontowanych pakietów obwody trzymane są w panelu za pomocą mostków (fixing tab), które od strony krawędzi obwodu są nawiercane (perforowane). Widok przykładowego mostka przedstawiono na fotografii 3.
Liczba mostków determinuje sztywność całego panelu. Zaleca się stosowanie ich nie rzadziej niż co 5 cm obrysu obwodu dla laminatu o typowej grubości 1,55 mm. Dla cieńszych laminatów liczbę mostków trzeba zwiększyć, a dla grubszych dopuszczalne jest stosowanie ich co 6-7 cm obrysu obwodu. Przy rozmieszczeniu mostków należy pamiętać, że nie mogą one być rozmieszczane wzdłuż metalizowanych krawędzi obwodu oraz powinny uwzględniać inne ograniczenia wynikające z późniejszych operacji montażowych.
Zachowaniu dużej sztywności paneli sprzyja ich ograniczony rozmiar, który powinien być tym mniejszy, im cieńszy zastosowano laminat. Rozmiar panelu nie może być mniejszy niż minimalny rozmiar pojedynczego obwodu. Z drugiej strony maksymalny dopuszczalny rozmiar panelu ograniczony jest polem roboczym linii do montażu automatycznego, sztywnością konstrukcji panelu oraz polem roboczym formatów stosowanych przez producenta PCB. Dobrą praktyką jest konstruowanie paneli o wymiarach zbliżonych do formatu A4 lub mniejszych.
W większości przypadków do paneli dodawane są marginesy będące dodatkowymi pasami laminatu umieszczane wzdłuż dłuższych krawędzi paneli lub ramki wokół ich zewnętrznych krawędzi. Elementy te spełniają kilka funkcji: wzmacniają sztywność panelu, służą jako obszary dla podajników transportowych linii montażowej oraz umieszcza się na nich znaczniki referencyjne dla automatów (tzw. fiduciale). Istotne jest, aby fiduciale były rozmieszczane tak, aby obróbka mechaniczna panelu ich nie uszkadzała.
Niekiedy projektuje się panele o mieszanej obróbce, w których proste odcinki krawędzi obwodów są rylcowane, a nieregularne frezowane. Dla takich paneli należy pamiętać, aby nie układać na rylcowanie obwodów, w których występują wycięcia w obrysie, ponieważ nie będzie możliwe ich dokładne wykonanie. Zjawisko to przedstawiono na rysunku 3a, gdzie strzałkami zaznaczono miejsca, w których wystąpią pozostałości po frezowaniu. Wyjątkiem są obwody o symetrycznych wycięciach znajdujących się na przeciwległych bokach, które można ułożyć krawędziami "na styk" do rylcowania (rys. 3b), przy jednoczesnym zachowaniu dużej dokładności frezowania.
Konstrukcja panelu powinna także uwzględniać elementy, których fragmenty wystają poza obszar obwodu po montażu. Dla takich projektów należy przewidzieć dodatkowe odstępy pomiędzy sąsiednimi wierszami i kolumnami obwodów w panelu. Ułożenie w tym przypadku panelu rylcowa nego na styk uniemożliwi montaż na obszarach zasłoniętych przez elementy zamontowane już na sąsiednich obwodach.
Czasami obwody, które klient zamówił do wykonania pojedynczo, muszą być wyprodukowane w panelu, ze względu na bardzo mały rozmiar pojedynczej sztuki (poniżej 30 mm). Wynika to z faktu, że obróbka mechaniczna tak małych, pojedynczych obwodów staje się problemem technologicznym lub niekiedy jest nawet niemożliwa. W sytuacji tego typu panel konstruowany jest przez producenta PCB i konsultowany z klientem.
Nieprawidłowości specyfikacji technologicznej
Jak wspomniano w pierwszej części artykułu, dokumentacja produkcyjna powinna zawierać pojedynczą specyfikację technologiczną (tzw. kartę technologiczną), w której zapisy umożliwiają jednoznaczną interpretację informacji. Typowe uchybienia specyfikacji odnoszą się do nieprawidłowych zapisów dotyczących pożądanych grubości warstw miedzi, laminatu oraz opisów budów obwodów wielowarstwowych. Niekiedy problemem jest zbyt mała liczba informacji o technologii projektu.
Grubości warstw miedzianych
Specyfikowana w karcie technologicznej grubość warstw miedzianych jest interpretowana przez producentów PCB, w tym TS PCB, jako docelowa (końcowa), o ile klient wyraźnie nie zapisał, że dotyczy ona miedzi bazowej, będącej grubością folii miedzianej surowego laminatu zastosowanego do produkcji. Końcowa grubość warstw miedzianych jest ostateczną grubością mozaik w wyprodukowanym obwodzie i w przypadku obwodów z metalizacją (płyty dwustronne i wielowarstwowe) jest ona sumą grubości miedzi bazowej laminatu i nakładanej galwanicznie (rzędu 25-30 µm). Oznacza to, że do produkcji obwodów dwustronnych ze standardową grubością miedzi końcowej 35 µm stosowany jest laminat bazowy z miedzią 18 µm oraz że nie jest możliwe uzyskanie końcowej grubości miedzi 18 µm dla tego typu obwodów.
W przypadku obwodów jednostronnych oraz rdzeni obwodów wielowarstwowych typowy laminat ma folię miedzianą o bazowej grubości 35 µm, która jest równocześnie grubością końcową, ponieważ laminaty te nie przechodzą procesu metalizacji. Możliwe jest zatem uzyskanie obwodów jednostronnych z miedzią końcową 18 µm, ponieważ do ich produkcji można wykorzystać laminat bazowy dla obwodów dwustronnych.
Przy specyfikowaniu grubości miedzi w karcie technologicznej najbezpieczniej posługiwać się grubością docelową. Niestety czasami klienci błędnie posługują się bazową grubością miedzi, myśląc, że jest ona tożsama z końcową. Niekiedy takie uchybienie można wykryć u producenta PCB, jednakże w większości przypadków wyprodukowane zostaną obwody z miedzią o większej - niż w rzeczywistości potrzebował klient - grubości, co podniesie ich koszt i może rzutować na funkcjonowanie układów elektronicznych z liniami transmisyjnymi o projektowanych impedancjach.
Grubości laminatów
Podobnie jak dla mozaik, także dla laminatów stosuje się pojęcia grubości bazowej i końcowej. Grubość bazowa jest początkową grubością laminatu wykorzystywanego do produkcji, która dla obwodów jedno- i dwustronnych, za wyjątkiem rdzeni obwodów wielowarstwowych, zawiera grubości folii miedzianych. Końcowa grubość laminatu jest powiększona o grubości nakładanych podczas produkcji powłok: miedzi galwanicznej, pokrycia (cyny lub złota) oraz masek antylutowniczych.
W przypadku, kiedy grubość końcowa laminatu jest niekrytyczna, w karcie technologicznej najlepiej operować bazową grubością laminatu i jej tolerancją. Natomiast w projektach, gdzie grubość obwodu jest parametrem krytycznym, klienci powinni uwzględniać grubości nakładanych powłok oraz zamieszczać w karcie technologicznej informacje o oczekiwanej końcowej grubości laminatu i jej tolerancji. Średnie grubości powłok są uzależnione od technologii projektu i dostępne w specyfikacji technologicznej producenta PCB. Niekiedy projekty są przez producenta wyjaśniane, ponieważ przyrost grubości laminatu wskutek nakładania kolejnych powłok może uniemożliwić uzyskanie końcowej grubości wyspecyfikowanej przez klienta.
Budowy obwodów wielowarstwowych
Parametry budowy obwodu wielowarstwowego, czyli przekroju poprzecznego informującego o układzie i typie poszczególnych warstw, powinny już na etapie projektowania uwzględniać możliwości technologiczne oraz wachlarz materiałów, jakimi dysponuje producent PCB. Zastosowanie wyszukanych rdzeni i prepregów (pre-impregnated materials - mieszanina włókna szklanego i żywicy) oraz ich nietypowego wzajemnego układu może w skrajnych przypadkach uniemożliwić produkcję obwodu. W takich sytuacjach producent zwykle zaproponuje alternatywną budowę o parametrach najbardziej zbliżonych do pierwotnej, ale na bazie materiałów, jakie ma na stanie. Odrzucenie przez klienta tej propozycji spowoduje zwiększenie czaso- i kosztochłonności realizacji projektu z uwagi na konieczność zamówienia niestandardowych materiałów, o ile nie istnieją inne przesłanki technologiczne, które całkowicie wykluczają możliwość produkcji obwodów.
W miarę możliwości warto projektować budowy symetryczne względem środka przekroju poprzecznego, co pozwoli uzyskać zbliżone napięcia powierzchniowe z obu stron laminatu. Niekiedy wykonanie symetrycznej budowy jest niemożliwe, np. ze względu na określone impedancje mozaik, co może przyczynić się do wichrowania się gotowych obwodów podczas lutowania na linii montażowej. Zjawisko to jest spowodowane występowaniem różnych naprężeń powierzchniowych laminatu na skutek niesymetrycznej struktury.
Innym zagadnieniem związanym z projektowaniem budowy jest liczba i typy użytych prepregów. Większość producentów obwodów, w tym TS PCB, zaleca stosowanie co najmniej dwóch prepregów rozdzielających sąsiednie warstwy przewodzące, gdyż użycie pojedynczego znacznie podnosi ryzyko delaminacji. Z drugiej strony jedynym ograniczeniem maksymalnej liczby prepregów jest grubość laminatu po sprasowaniu. Warto pamiętać, że ze wzrostem grubości warstw miedzianych konieczne jest zastosowanie większej liczby prepregów w celu zapewnienia optymalnego wypełnienia żywicą obszarów bez miedzi i zredukowania do minimum zjawiska delaminacji. Nie jest zatem możliwe uzyskanie obwodu wielowarstwowego o grubości 0,8 mm i mniejszej dla warstw miedzianych o grubości 105 µm. Aby jednocześnie uniknąć zbytniego przyrostu grubości zaleca się wówczas stosowanie najcieńszego prepregu 1080 (3,04 mils), który charakteryzuje się ponadto dużym nasyceniem żywicą. Dobrą praktyką jest także możliwie największe wypełnianie warstw wewnętrznych obszarami miedzi, co wpływa korzystnie na proces prasowania laminatu.
W przypadku obwodów ze ślepymi przelotkami występuje zależność ich średnicy od dopuszczalnej głębokości wiercenia i w efekcie możliwej liczby warstw do połączenia. Redukcji rozmiarów ślepych przelotek sprzyja jak najmniejsza odległość pomiędzy łączonymi warstwami. Jeżeli nie ma innych przeciwwskazań, to zaleca się ich stosowanie na możliwie cienkich laminatach, o grubości poniżej 1 mm. Jeśli pożądana jest większa grubość materiału, to warto tak zaprojektować obwód, aby ślepe przelotki łączyły tylko warstwy zewnętrzne z najbliższymi wewnętrznymi, oddzielić te warstwy dwoma prepregami 1080, a zadaną grubość końcową laminatu uzyskać przez zastosowanie grubszych rdzeni.
Innym uchybieniem dokumentacji płyt wielowarstwowych jest brak informacji o kolejności warstw wewnętrznych. Taką informację można przekazać poprzez odpowiednie nazewnictwo plików mozaik, ponumerowanie warstw na mozaikach lub opis słowny w specyfikacji. Układ warstw może mieć kluczowe znaczenie, szczególnie dla szybkich układów cyfrowych pracujących z wysokimi częstotliwościami, w których występują linie transmisyjne o dopasowanych impedancjach. Projekt pozbawiony tej informacji na pewno będzie wyjaśniany przez producenta.
Podsumowanie
W artykule przedstawiono typowe nieprawidłowości elektronicznej dokumentacji produkcyjnej determinującej jej jakość, która ma zasadniczy wpływ na szybkość i koszt realizacji projektów. Przesyłanie do producenta PCB nadmiarowej liczby plików, stosowanie niewłaściwych formatów oraz dostarczanie lakonicznych, a czasami nawet sprzecznych informacji opisujących technologię wykonania znacznie utrudniają przygotowanie projektu do produkcji, powodują duże problemy we właściwej interpretacji rzeczywistych oczekiwań klienta i wydłużają proces produkcji projektu z uwagi na konieczność jego wyjaśniania i kompletowania informacji.
Dr inż. Dariusz Załęski
Specjalista ds. Rozwoju Oprogramowania
TS PCB Techno-Service S.A.
www.pcb-technoservice.eu