Parametry podłoży, które trzeba wziąć pod uwagę, projektując PCB, można podzielić na: termiczne, elektryczne, chemiczne oraz mechaniczne. Do tych pierwszych zalicza się: temperaturę zeszklenia, współczynnik rozszerzalności cieplnej, temperaturę rozkładu chemicznego i przewodność cieplną. Najważniejsze parametry elektryczne to: stała dielektryczna, współczynnik strat dielektrycznych, rezystywność i odporność na przebicie. Do trzeciej kategorii zalicza się palność i stopień absorpcji wilgoci. Parametry mechaniczne to z kolei: wytrzymałość na zginanie, moduł Younga oraz czas do rozwarstwienia.
Czym jest temperatura zeszklenia?
Wraz ze wzrostem temperatury powyżej tej granicznej, określonej dla danego materiału, podłoża PCB miękną. Wartość progową, przy której następuje przejście ze stanu twardego do miękkiego (plastycznego), określa temperatura zeszklenia (glass transition temperature, Tg). W postaci tej podłoże pozostaje, dopóki jego temperatura nie przekroczy temperatury topnienia. Z kolei gdy ostygnie, powraca do pierwotnej postaci. Typowe wartości temperatury zeszklenia to +130…+150°C. W przypadku podłoży o podwyższonej wytrzymałości na ciepło Tg przekracza +170…+180°C.
Kolejnym parametrem jest współczynnik rozszerzalności termicznej CTE (Coefficient of Thermal Expansion). Charakteryzuje on to, jak szybko materiał się rozszerza wraz ze wzrostem temperatury. W związku z różnicą wartości współczynników CTE dielektryka i miedzi można się spodziewać problemów z ciągłością połączeń w obrębie płytki drukowanej w razie jej nagrzania się.
Po przekroczeniu temperatury zeszklenia CTE zwiększa się, chociaż nie we wszystkich kierunkach jednakowo. Współczynniki rozszerzalności cieplnej podłoży wzdłuż osi x i y mają typowo małą wartość, zwykle 10 … 20 ppm/°C. Ograniczone rozszerzanie się podłoży w tych kierunkach wynika z właściwości materiałów, z których się je wykonuje. CTE w poziomie nie zmienia się zbytnio, nawet po przekroczeniu temperatury zeszklenia. Współczynnik rozszerzalności termicznej wzdłuż osi z, który znacznie wzrasta po przekroczeniu Tg, nie powinien z kolei być większy niż 70 ppm/°C. W przeciwnym razie gwałtowne rozszerzanie się podłoża w pionie może mieć groźne skutki, m.in. powodując naprężenia przewodnika w przelotkach. Konsekwencjami tego jest z kolei podnoszenie się padów i pękanie przelotek na krawędziach i na ściankach.
Rozkład chemiczny i przewodność cieplna
Ważny parametr to również wartość progowa temperatury, przy której zachodzi rozkład chemiczny dielektryka (thermal decomposition, Td), na skutek którego traci on co najmniej 5% swojej masy. W przeciwieństwie do zeszklenia jest to proces, który nie jest odwracalny. Efekty chemicznej dekompozycji materiału podłoża PCB są trwałe.
Wybierając podłoże trzeba określić maksymalną temperaturę, na jaką płytka drukowana będzie narażona – zwykle jest to temperatura lutowania – należy odnieść do wartości Tg oraz Td. Najlepiej, jeżeli będzie wyższa niż temperatura zeszklenia i zarazem niższa niż temperatura rozkładu chemicznego, która w przypadku popularnych materiałów przekracza +320°C.
Ostatnim parametrem zaliczanym do tej samej kategorii, co temperatury Tg, Td oraz współczynnik CTE jest przewodność termiczna. Charakteryzuje ona zdolność podłoża do przenoszenia energii cieplnej. Im jest większa, tym więcej ciepła jest przez niego przekazywanego do otoczenia. To z kolei przekłada się na mniejszy wzrost temperatury dielektryka. Generalnie większość podłoży PCB ma przewodność cieplną rzędu ułamka W/mK. Jest to bardzo mała wartość w porównaniu z miedzią, której przewodność termiczna wynosi 386 W/mK. Dlatego to właśnie ten materiał głównie odpowiada za odprowadzanie nadmiaru ciepła z PCB.
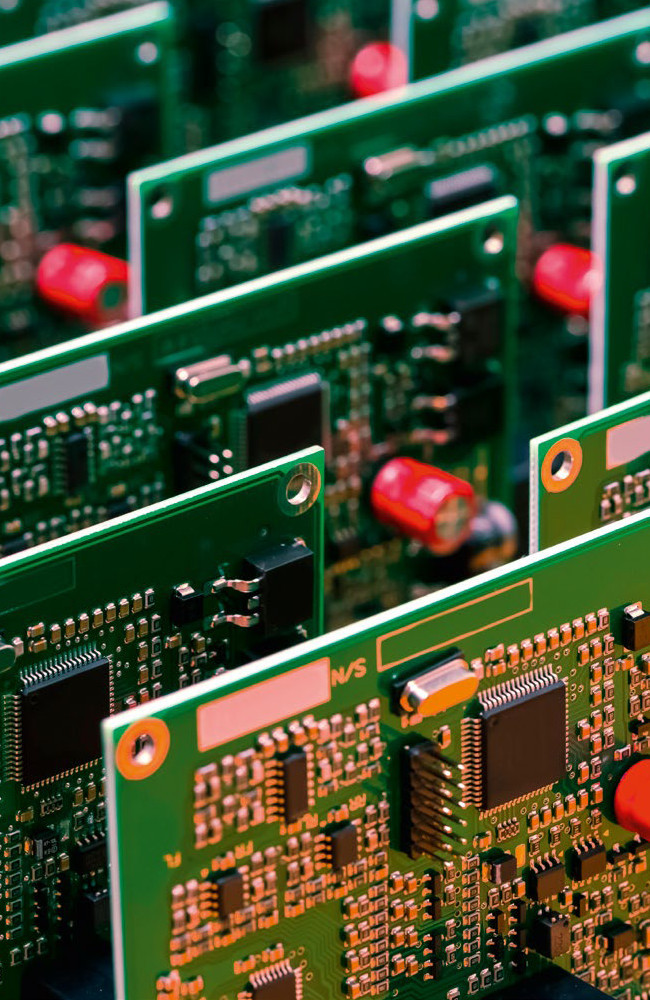
Stała dielektryczna i tangens kąta strat
Stałą dielektryczną Dk definiuje się jako stosunek ładunku zgromadzonego w dielektryku, który jest umieszczony między dwoma metalowymi elektrodami do ładunku zgromadzonego, gdy materiał dielektryczny zostanie zastąpiony przez próżnię. Innymi słowy, parametr ten określa stosunek przenikalności elektrycznej dielektryka do przenikalności elektrycznej próżni, czyli przenikalność względną εr. Stała dielektryczna charakteryzuje zdolność dielektryka do magazynowania energii w polu elektrycznym. Jej wartość może się zmieniać w obrębie materiału, dlatego w specyfikacji jest zazwyczaj podawana jako średnia. Zależy też od częstotliwości, malejąc wraz z jej wzrostem. W przypadku większości podłoży PCB mieści się w zakresie od 2,5 do 4,5.
Kolejny ważny parametr to współczynnik strat dielektrycznych Df, inaczej tangens kąta stratności (tg δ). Jest wyrażany jako stosunek natężenia składowej rzeczywistej (czynnej) do składowej urojonej (biernej) prądu elektrycznego płynącego przez dielektryk w zmiennym polu elektrycznym. Określa, jaka część energii pola elektromagnetycznego ulega przemianie na ciepło w jednostce objętości dielektryka. Współczynnik strat dielektrycznych podłoży PCB mieści się zazwyczaj w przedziale od 0,02 do 0,001. Zależy od częstotliwości, przy zwiększaniu której również wzrasta.
Znaczenie Dk i Df
Im mniejsze wartości mają Dk i Df, tym mniejsze są straty dielektryczne. Wybierając podłoże o mniejszej przenikalności względnej, można też zmniejszyć grubość PCB. Najlepiej wyjaśnić to na przykładzie linii paskowej jak na rysunku 1. Impedancję charakterystyczną linii transmisyjnej tego typu określa wzór:
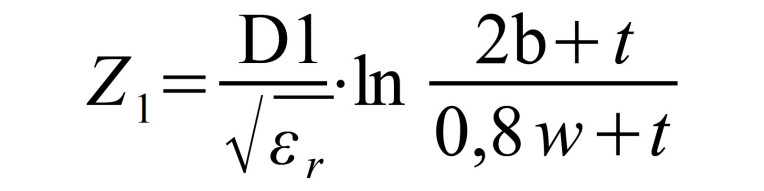
gdzie: t to grubość ścieżki, w – jej szerokość, a b – odległość między płaszczyznami uziemienia. Z zależności tej wynika, że żeby uzyskać konkretną impedancję przy określonej szerokości ścieżki, jeżeli użyty zostanie dielektryk o większej przenikalności względnej, konieczne będzie zwiększenie odstępu pomiędzy płaszczyznami uziemienia. Oznacza to, że zwiększy się całkowita grubość płytki drukowanej.
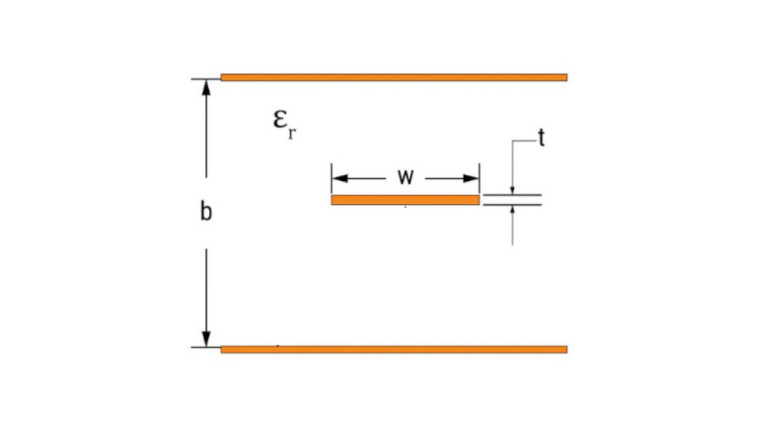
Ma to znaczenie szczególnie w przypadku PCB o dużym zagęszczeniu połączeń. Wynika to stąd, że grubsze płytki drukowane wymagają przelotek o większym współczynniku kształtu, czyli stosunku ich głębokości do średnicy. Im są głębsze i jednocześnie węższe, tym ich wykonanie jest trudniejsze z powodu ograniczeń procesów technologicznych wykorzystywanych w tym celu. W związku z tym wybierając podłoże o mniejszej przenikalności względnej, można sporo zaoszczędzić na przelotkach wykonywanych taniej tradycyjnymi, mechanicznymi metodami niż droższymi, przy użyciu lasera, który pozwala na wykonywanie przelotek o większych współczynnikach kształtu.
Jak ważna jest stała dielektryczna?
Również to, że stała dielektryczna podłoża jest funkcją częstotliwości, ma swoje konsekwencje, ma ona bowiem wpływ na dwa inne, ważne parametry: impedancję charakterystyczną i prędkość fali. Prędkość propagacji sygnału w linii transmisyjnej jest odwrotnie proporcjonalna do przenikalności względnej. W efekcie, w wyniku zmian stałej dielektrycznej, różne składowe częstotliwości sygnału będą propagować z różnymi prędkościami. To z kolei prowadzi do rozproszenia sygnału.
Ponadto, w związku z tym, że Dk maleje wraz ze wzrostem częstotliwości, jak wynika ze wzoru 1, impedancja charakterystyczna linii transmisyjnej będzie równocześnie rosła. W konsekwencji przy wyższych częstotliwościach nasileniu ulegną odbicia sygnału. Najlepiej więc wybrać podłoże o maksymalnie płaskiej charakterystyce zmienności stałej dielektrycznej w interesującym nas przedziale częstotliwości.
Trzeba też pamiętać, że stała dielektryczna żywicy jest mniejsza niż włókien. Dlatego im większa jest zawartość tej pierwszej, tym mniejsza jest wypadkowa wartość Dk podłoży. Oprócz tego są one wewnętrznie niejednorodne i anizotropowe. W efekcie w niektórych częściach płytki drukowanej są bardziej nasycone żywicą, a w innych występuje więcej włókien. Odpowiada temu nierównomierny rozkład stałej dielektrycznej, której wartość będzie miejscami różna.
Rezystywność
Do grupy parametrów elektrycznych zalicza się również: rezystywność powierzchniową i skrośną. Rezystywność powierzchniowa charakteryzuje opór dla przepływu prądu upływu po powierzchni materiału izolacyjnego, zaś rezystywność skrośna – opór dla przepływu prądu upływu w głąb dielektryka. Im większe są wartości rezystywności powierzchniowej i skrośnej, tym mniejszy prąd upływu i tym lepsze właściwości izolacyjne materiału. Typowe wartości tych parametrów podłoży PCB są rzędu MΩ w przypadku rezystywności powierzchniowej oraz MΩ·cm dla rezystywności skrośnej.
Kolejny parametr to odporność dielektryka na przebicie. Jest ona istotna w układach pracujących z wysokimi napięciami i wymagających gwarantowanej izolacji między poszczególnymi warstwami miedzi w obwodach wielowarstwowych. Typowe wartości tego parametru w przypadku podłoży PCB są rzędu kilkudziesięciu kV.
Absorpcja wilgoci
Tytułowy parametr charakteryzuje stopień wchłaniania wilgoci przez podłoże PCB. Jest podawany jako procentowy wzrost jego masy spowodowany przez absorpcję wody. W przypadku większości podłoży mieści się w zakresie od 0,01% do 0,20%.
Nadmierna absorpcja wody powoduje pogorszenie się właściwości termicznych oraz elektrycznych dielektryka i sprzyja tworzeniu się w nim pasożytniczych, dendrytowych struktur przewodzących CAF (Conductive Anodic Filament). Jest to skutek zjawiska elektromigracji. Niepożądane struktury w postaci metalicznych ścieżek powstają między przelotkami, przelotkami a ścieżkami i pomiędzy tymi ostatnimi (rys. 2). W procesie ich tworzenia się można wyróżnić dwa etapy.
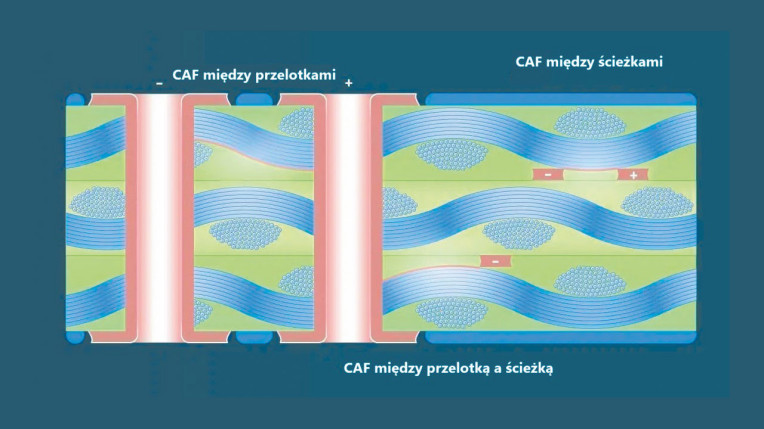
Pierwszym jest pogorszenie stanu materiału podłoża na styku żywicy z włóknami. Sprzyjają temu nadmierna wilgoć i podwyższona temperatura. W drugim etapie następuje rozrost przewodzących struktur. Na szybkość jego postępowania ma wpływ szereg czynników, w tym: odległość pomiędzy przeciwnie spolaryzowanymi przewodnikami, umiejscowienie/kąt między przelotkami w stosunku do kierunku ułożenia włókien w podłożu, polaryzacja napięcia, wilgotność, temperatura, warunki pH. Proces migracji miedzi jest nieodwracalny.
Parametry mechaniczne
Zdolność materiału dielektrycznego do wytrzymywania naprężeń bez pękania jest określana jako wytrzymałość na zginanie. Jest ona wyrażana w kg/m². Wytrzymałość dielektryka charakteryzuje również moduł Younga (moduł rozciągania). Określa on stosunek naprężenia do odkształcenia w określonym kierunku. Moduł rozciągania, wyrażany w N/m², jest przez niektórych producentów podawany w specyfikacji zamiast wytrzymałości na zginanie, jako miara zdolności podłoża PCB do wytrzymywania naprężeń. Ważnym parametrem jest również ten określający, ile czasu musi upłynąć, by warstwy PCB uległy rozwarstwieniu w określonych warunkach temperatury i wilgoci.
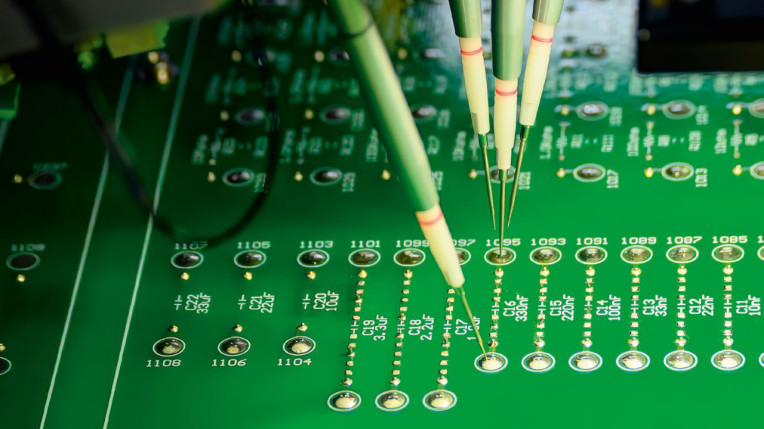
Monika Jaworowska