Źródła interferencji
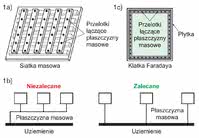
Rys. 1. Siatka masowa (1a), niezalecany i zalecany sposób uziemienia (1b), zastosowanie klatki Faradaya (1c)
Wszystkie możliwe drogi propagacji sygnału są potencjalnymi źródłami pola elektromagnetycznego. Każda z nich, od układu scalonego, ścieżki na płytce po kabel koncentryczny, inaczej wypromieniowuje pole elektromagnetyczne. Ograniczanie poziomu interferencji zaczyna się zatem już na etapie doboru komponentów, a kończy na konstrukcji obudowy.
Pole elektromagnetyczne generowane w urządzeniach elektronicznych jest wynikiem impulsów prądowych propagowanych wzdłuż długich ścieżek lub pętli. Każdy impuls rozchodzący się wzdłuż linii wytwarza pole magnetyczne prostopadłe do kierunku propagacji prądu. Spadek napięcia wynikający z przepływu prądu jest z kolei źródłem pola elektrycznego.
Oddziaływanie tych pól z innymi sygnałami nazywamy interferencjami elektromagnetycznymi. Na poziom interferencji oprócz właściwości linii prądowych (np. długości, ekranowania) wpływ mają również parametry propagowanego sygnału, takie jak częstotliwość, współczynnik wypełnienia, szybkość narastania zboczy oraz amplituda. Rolę odgrywaną przez te parametry najlepiej widzimy rozpatrując transmitowany sygnał w dziedzinie częstotliwości.
Metody zmniejszania poziomu interferencji
Generalnie metody redukcji interferencji elektromagnetycznych można podzielić na pasywne i aktywne. Do pasywnych należy filtrowanie oraz ekranowanie, które na etapie projektowania płytki drukowanej polega na stosowaniu pewnych reguł i zaleceń. Przy filtrowaniu należy rozpatrywać każdą ścieżkę lub bufor wyjściowy.
Ekranowanie z kolei jest metodą bardziej mechaniczną niż elektryczną. Minusem ekranowania jest większa masa i koszt materiałów końcowego produktu. Liczba iteracji przy projektowaniu płytki zależy od stopnia skomplikowania projektu i doświadczenia projektanta.
Projektowanie można w pewnym zakresie ułatwić dzięki zastosowaniu specjalistycznego oprogramowania, np. trójwymiarowych symulatorów elektromagnetycznych wspomagających projektowanie obwodów drukowanych oraz obudów. W metodach aktywnych stosuje się techniki skierowane na przyczyny powstawania interferencji, a nie na redukcję ich skutków.
Spowalnia się szybkości narastania zboczy, eliminuje ostre przejścia w przebiegach czasowych sygnałów oraz stosuje inne techniki wygładzające. Dzięki wydłużeniu czasu narastania zboczy ogranicza się energię częstotliwości podstawowej kosztem energii wyższych harmonicznych. Kolejną metodą, w której również chodzi o zmianę właściwości widmowych sygnału, jest rozpraszanie widma sygnału zegarowego (spread spectrum clocking).
Projekt płytki drukowanej
Opracowanie projektu płytki drukowanej dla urządzenia optymalnego pod względem EMC, zwłaszcza takiego, w obrębie którego wykorzystywane będą układy analogowe i cyfrowe, może okazać się niełatwym zadaniem. Najważniejszą kwestią, wymagającą głębszej analizy, jest sposób realizacji płaszczyzny masy.
Jeżeli na tym etapie projektant PCB popełni błąd, musi liczyć się z dalszymi komplikacjami m.in. w kwestii prowadzenia ścieżek sygnałowych, jak również nierzadko z pogorszeniem parametrów całego urządzenia. Kluczem do minimalizacji problemów z EMC jest uziemienie (masa) o niskiej indukcyjności. Duża płaszczyzna masowa ma małą indukcyjność i tym samym emisję elektromagnetyczną oraz zapewnia niskie przesłuchy sygnału.
Mogą one wystąpić między dowolnymi dwoma drogami na płytce, zależą od indukcyjności i pojemności wzajemnej proporcjonalnie do odległości między ścieżkami, impedancji ścieżek czy nachylenia zbocza sygnałów cyfrowych. W układach cyfrowych przesłuchy spowodowane indukcyjnością wzajemną są z reguły większe niż wynikające z pojemności pasożytniczych.
W celu redukcji indukcyjności wzajemnej należy zwiększyć przerwy między ścieżkami lub zmniejszyć odległość od płaszczyzny masowej. Odprowadzanie sygnału z elementów do masy i dalej do uziemienia jest możliwe za pomocą różnych metod. Płytkę drukowaną o losowo uziemionych komponentach cechuje wysoka indukcyjność płaszczyzny masy oraz nieuniknione problemy z EMC.
W celu minimalizacji impedancji drogi ziemnopowrotnej zaleca się więc stosowanie pełnej płaszczyzny masy pod wszystkimi elementami, co upraszcza proces łączenia podzespołów z masą i zapewnia najkrótszą drogę elektryczną. Jednak wymaga ona dodatkowej pełnej warstwy miedzi na płytce, co może być niewykonalne w przypadku płytek dwuwarstwowych.
W takiej sytuacji zaleca się używanie siatek masowych (rys. 1a), w których indukcyjność masy zależy od odległości między elementami siatki. Ważny jest również sposób łączenia z masą sygnałów. Jeśli umasienie realizowane jest dłuższą drogą, to tworzy się pętla, która działa jak antena i wypromieniowuje energię. Dlatego każda droga ziemnopowrotna powinna być jak najkrótsza i musi prowadzić bezpośrednio do płaszczyzny masowej.
Nie zaleca się łączenia poszczególnych uziemień, a następnie prowadzenia ich do płaszczyzny masowej, gdyż zwiększa to obszar pętli oraz prawdopodobieństwo wystąpienia spadku napięcia na masie. Na rysunku 1b przedstawiono zalecaną metodę łączenia komponentów do płaszczyzny masowej. Nie należy też bez potrzeby dzielić płaszczyzny masy na wydzielone obszary "analogowe" i "cyfrowe" (patrz ramka).
Inną dobrą metodą ograniczenia problemów z kompatybilnością jest otoczenie płytki miedzią na podobieństwo klatki Faradaya i niewyprowadzanie żadnego sygnału na zewnętrz (rys. 1c). Ogranicza to emisję do obszaru ograniczonego klatką i zapobiega interferencjom sygnałów zewnętrznych z sygnałami na płytce. Z punktu widzenia EMC kluczowe jest także prawidłowe ułożenie warstw.
W przypadku użycia więcej niż dwóch należy jedną pełną warstwę wykorzystać jako płaszczyznę masową. W płytkach czterowarstwowych należy płaszczyznę zasilającą umieścić pod płaszczyzną masową, nad która powinny przebiegać drogi sygnałów w.cz.
Jeśli zastosowanie pełnej warstwy masowej w przypadku płytki dwuwarstwowej nie jest możliwe, to należy stosować siatki masowe. Przy braku oddzielnej płaszczyzny zasilającej, drogi masy powinny być prowadzone równolegle do dróg zasilających.