Niniejsza, druga część artykułu poświęcona będzie charakterystyce elektrycznych testerów ostrzowych, określanych także jako igłowe lub adapterowe. Przedstawione zostaną szczegóły procedury testu adapterowego obwodów drukowanych oraz porównanie z testowaniem przy wykorzystaniu testerów palcowych. Na koniec omówione zostanie testowanie optyczne obwodów, jego zasada działania oraz możliwości i ograniczenia.
Testery ostrzowe
W odróżnieniu od testerów z ruchomymi sondami, które mają niewielką liczbę głowic pomiarowych (zwykle 4) w testerach ostrzowych wykorzystuje się znaczną liczbę nieruchomych sond pomiarowych, które występują w postaci igieł o zróżnicowanych średnicach (rys. 1). Średnice ostrzy dopasowane są do powierzchni pól kontaktowych punktów testowych obwodu drukowanego, przy czym do średnicy 1,8 mm stosowane są igły sztywne, a powyżej tej granicy sprężyste - wyposażone w dodatkowe sprężynki poprawiające elastyczność.
Igły zapewniają połączenie elektryczne pomiędzy wybranymi punktami testowymi PCB a tzw. kasetą testera, która jest matrycą gniazd układu pomiarowego rozmieszczonych ze stałym rastrem. Jej rozmiar warunkuje obszar pola roboczego testera ostrzowego, a więc maksymalny rozmiar obwodu jaki można testować.
W prostych jednostronnych testerach igłowych występuje pojedyncza dolna kaseta będąca podstawą do zamocowania adaptera. Taka konstrukcja pozwala testować obwód drukowany od jednej strony. Testery bardziej zaawansowane wyposażone są w dwie kasety i mogą wykorzystywać dwa adaptery, dzięki czemu badają jednocześnie obie strony obwodu.
Najbardziej powszechny raster gniazd kasety wynosi 100 mils (2,54 mm), co umożliwia zastosowanie ok. 16 igieł i kanałów pomiarowych na obszarze 1 cm² powierzchni PCB. W zależności od klasy urządzenia raster kasety może być gęstszy i wynosić 70 mils (ok. 1,78 mm) lub nawet 50 mils (1,27 mm), dając możliwość obsadzenia ok. 32 oraz 62 igieł i kanałów pomiarowych na 1 cm² powierzchni obwodu drukowanego.
Dla zagwarantowania prawidłowego i trwałego rozmieszczenia sond igłowych względem badanego obwodu drukowanego, przy równoczesnym zapewnieniu dobrego kontaktu elektrycznego igieł z punktami testowymi obwodu oraz gniazdami kasety, konieczne jest zastosowanie przystawki, nazywanej adapterem lub (z j. angielskiego) fiksturą (rys. 2).
Budowa adaptera
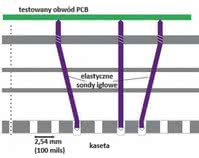
Rys. 3. Przekrój adaptera jednostronnego, dla kasety z rastrem 100 mils, z opisem elementów składowych
Przykładową strukturę adaptera jednostronnego przedstawiono na rysunku 3. Zawiera on cztery płyty wykonane z pleksiglasu (PMMA) o określonych grubościach. Płyty są powiercone względem siebie tak, aby dzięki elastyczności igieł dopasować ich rozmieszczenie wynikające z układu punktów testowych obwodu drukowanego do najbliżej położonych gniazd kasety.
Prawidłowe dopasowanie do rastra kasety wymusza otworowanie dolnej płyty adaptera. Igły mogą swobodnie poruszać się pionowo i wsuwać się w gniazda kasety zapewniając połączenie elektryczne. Uzyskanie dobrego kontaktu elektrycznego wymaga zastosowania docisku pomiędzy badanym obwodem a adapterem i kasetą. W testerze jednostronnym docisk realizowany jest przez ruchomy stolik, a w dwustronnym przez ruchomą górną kasetę. Elementy te napędzane są zwykle siłownikiem pneumatycznym poprzez układ dźwigni pozwalający regulować siłę docisku.
Proces projektowania adaptera odbywa się przy wykorzystaniu specjalnego oprogramowania i jest etapem przygotowawczym poprzedzającym właściwe testowanie. Przebiega on dłużej niż opracowanie programu do testowania dla testera palcowego dla tego samego obwodu. Oprogramowanie na bazie netlisty oraz rozmieszczenia zewnętrznych mozaik (a przez to punktów testowych) obwodu względem rastra gniazd kasety, dobiera współrzędne usytuowania i rodzaje sond igłowych.
W przypadku układów SMD o gęsto położonych polach lutowniczych stosuje się technikę przeciwsobnego rozsuwania igieł sąsiadujących pól (ang. staggering) Program rozmieszcza także dodatkowe elementy jak stożkowe kołki bazujące obwód drukowany wobec adaptera oraz różnego typu wsporniki zapewniające odpowiednią sztywność całej struktury w płaszczyźnie poziomej i jednocześnie elastyczność w kierunku pionowym.
Na zakończenie procesu projektowania generowane są: program dla testera ostrzowego określający, jakie gniazda kasety będą punktami pomiarowymi obsadzonymi igłami, programy wierceń CNC niezbędne do wykonania otworowania w płytach PMMA - głównych elementów składowych adaptera - oraz dokumentacja złożeniowa.
Na bazie tej dokumentacji wykwalifikowany pracownik montuje poszczególne elementy składowe adaptera w jednolitą strukturę. Jest to proces długotrwały, przy czym najbardziej czasochłonne jest obsadzenie adaptera igłami. W zależności od liczby igieł składanie adaptera jednostronnego może trwać do 1 godziny, a dwustronnego dwukrotnie dłużej. Z tego powodu, aby skrócić czas testowania projektów często powielanych, producenci PCB przechowują dla nich adaptery w stanie złożonym. Pozostałe adaptery archiwizowane są przez pewien okres czasu w stanie rozłożonym.
Procedura testowania
Właściwa procedura testowania polega na zamocowaniu adapterów testowanego projektu w kasetach testera zgodnie z kołkami bazującymi oraz wgraniu programu testu lub nauczeniu testera wzorcowej struktury sieci elektrycznych za pomocą tzw. złotej płytki (ang. golden board).
Następnie odbywa się powtarzalna sekwencja następujących operacji: zamocowania, z uwzględnieniem kołków bazujących, obwodu/panela na dolnym adapterze, docisku górnej kasety testera, podczas której przeprowadzany jest właściwy test dla wszystkich badanych sieci oraz klasyfikacja uszkodzeń, wyjęciu testowanego obwodu z testera. Po podniesieniu górnej kasety wynik testu pojawia się na dołączonym monitorze, a w przypadku wykrycia nieprawidłowości generowana jest informacja zwrotna dla stacji napraw.
Procedura testowania wykorzystuje znaczną liczbę torów pomiarowych testera ostrzowego. Dla przykładowego testera dwustronnego o polu roboczym kaset 25,6×19,2 cala i rastrze 70 mils wynosi ona prawie 200 tysięcy. Tak znaczna liczba torów pomiarowych testera, która z jednej strony świadczy o dużej komplikacji układowej oraz rozbudowaniu całego bloku pomiarowego (rys. 4) i klasyfikacji uszkodzeń, jest jednocześnie zasadniczym atutem tej techniki testowania, gdyż pozwala na przeprowadzanie testów ciągłości i izolacji na wielu sieciach równocześnie.
Współbieżność taka redukuje czas testowania do zaledwie pojedynczych sekund, który jest nieporównywalnie krótszy od czasu testowania tego samego obwodu na testerze palcowym. Wydajność testowania adapterowego może dochodzić do kilku tysięcy punktów testowych na sekundę niezależnie od rozkładu punktów testowych. Dla porównania testery palcowe osiągają zbliżoną liczbę punktów testowych w czasie minuty, ale ich wydajność zależy do rozkładu punktów testowych.
Krótki czas testu zapewnia dużą wydajność testowania, która może być nawet 5-krotnie większa niż dla testera palcowego. Z tego powodu testery ostrzowe wykorzystywane są do testowania elektrycznego dużych serii produkcyjnych obwodów drukowanych.
Z uwagi na większą czasochłonność etapu przygotowawczego, w którym opracowywany jest program do testowania oraz wykonywany i składany adapter, istnieje minimalna liczba formatów produkcyjnych, powyżej których testowanie adapterowe staje się znacznie bardziej wydajne od palcowego. Zwykle granicą opłacalności testu igłowego jest kilkanaście formatów produkcyjnych.
Firmy produkujące testery ostrzowe oferują dodatkowe techniki zwiększające wydajność testowania. Najczęściej są to jednak rozwiązania sprzętowe obejmujące zautomatyzowane systemy załadunku i rozładunku obwodów (rys. 5). Wynika to z faktu, że ręczny załadunek i rozładunek pojedynczego obwodu trwa dłużej niż etapu właściwego testowania. Drugim kierunkiem optymalizacji wydajności jest zwiększanie powierzchni roboczej testera, umożliwiające testowanie adapterowe całych formatów produkcyjnych.
Testowanie optyczne AOI
Jak już wspomniano, testowanie elektryczne weryfikuje zgodność sieci projektu odwzorowanych poprzez mozaiki w rzeczywistym wyprodukowanym obwodzie. Pozwala ono wykryć uszkodzenia fatalne mozaik w postaci zwarć oraz rozwarć, które modyfikują strukturę sieci. W przypadku testowania optycznego przedmiotem weryfikacji jest obraz mozaik rzeczywistego obwodu, który jest porównywany z wzorcowym, wygenerowanym na bazie dokumentacji projektowej obwodu.
Takie podejście umożliwia nie tylko graficzne wykrycie uszkodzeń katastroficznych mozaik (zwarcia i rozwarcia), ale także szeregu defektów jakościowych ich wykonania na kilku etapach procesu produkcyjnego: wiercenia oraz frezowania przed trawieniem, fotochemigrafii, galwanicznego miedziowania oraz trawienia mozaik.
Testowanie optyczne pozwala wykryć m.in.: przesunięcie owiertu, występowanie przewężeń i pogrubień ścieżek przewodzących, za grubą metalizację, przetrawienia i niedotrawienia, zarysowania powierzchni. Dla zapewnienia dobrej widoczności mozaik testowaniu AOI poddawane są obwody jeszcze niepokryte maską przeciwlutowniczą.
Tester optyczny wykorzystywany jest także do kontroli jakości odwzorowania mozaik z klisz dla dużych serii produkcyjnych, gdzie badane są pojedyncze formaty serii próbnej pokryte nieutwardzonym fotopolimerem po naświetlaniu kliszami. Celem inspekcji jest detekcja fatalnych defektów seryjnych klisz. W przypadku ich wykrycia warstwa fotopolimeru zostaje zmyta, a proces wykonania klisz, naświetlania oraz inspekcji AOI powtórzony.
Parametry, przebieg i możliwości testowania optycznego zostaną omówione na przykładzie testera Argos 8008 (rys. 6) firmy Mania. Tester ten, dzięki skanowaniu obrazu z rozdzielczością 5000 DPI, umożliwia inspekcję optyczną powierzchni PCB z dokładnością na poziomie 2 milsów. Czas skanowania pojedynczego formatu produkcyjnego, w zależności od wybranego poziomu dokładności inspekcji, wynosi od kilku kilkunastu sekund.
Procedura testowania AOI
Pierwszym etapem testowania AOI, podobnie jak dla testerów palcowych, jest przygotowanie programu testu. Tworzenie programu obejmuje oznaczanie na obrazie formatu produkcyjnego obszarów wyłączonych z testu oraz umieszczanie dla każdej z warstw trzech punktów referencyjnych przeznaczonych do bazowania mechaniki testera. Ze względu na małą liczbę operacji etap ten zajmuje co najwyżej 2-3 minuty lub nawet mniej dla prostszych projektów, a więc najkrócej z omawianych dotychczas technik testowania.
Właściwy etap testowania optycznego przebiega według następującego schematu: załadowanie formatu produkcyjnego, bazowanie testera, skanowanie wierzchniej warstwy mozaik, detekcja nieprawidłowości i ich prezentacja na dołączonym monitorze. Podczas klasyfikacji uszkodzeń, w celu redukcji liczby wykrywanych odstępstw obrazu rzeczywistego obwodu od wirtualnego wzorca, uwzględniane są obszary tolerancji, które dopuszczają niewielkie przesunięcia elementów składowych zeskanowanego obrazu mozaik względem wzorca.
Po sprawdzeniu jednej strony laminatu następuje jego obrócenie i powtórzenie wymienionych operacji. Widok przykładowych defektów rozwarcia i zwarcia przestawiono na rysunku 7, gdzie brakujące elementy mozaik (rozwarcia) oznaczane są kolorem czerwonym, a nadmiarowe (zwarcia) zielonym.
Testowanie optyczne AOI charakteryzuje się dużą wydajnością przekraczającą możliwości testerów elektrycznych. Omawiany model testera dysponuje wydajnością dobową dochodzącą nawet do 200 m² powierzchni badanych obwodów. Innym walorem testu AOI jest lokalizowanie defektów jakościowych mozaik i przez to nieprawidłowości niektórych etapów produkcji obwodów, które nie mogą zostać wykryte testowaniem elektrycznym.
Zasadniczym ograniczeniem testowania optycznego jest brak możliwości weryfikacji warstw niewidocznych np. warstw wewnętrznych w sprasowanych obwodach wielowarstwowych oraz kontroli prawidłowości metalizacji przelotek. Z tych powodów renomowani producenci PCB, w tym TS PCB, w celu kompleksowego testowania wytwarzanych obwodów, wykorzystują testowanie AOI, jako pośredni etap kontrolny łańcucha produkcji, który poprzedza końcowe testowanie elektryczne.
Podsumowanie
W artykule omówiono zagadnienie testowania obwodów drukowanych, które z jednej strony jest dla projektantów PCB rozwiązaniem gwarantującym wysoką niezawodność gotowego urządzenia, a z drugiej strony pozwala producentowi obwodów monitorować na bieżąco jakość oraz prawidłowość realizowanych etapów produkcyjnych.
Dr inż. Dariusz Załęski
Rafał Olszewski
TS PCB Techno-Service S.A.
www.pcb-technoservice.eu