Elementy wbudowane (określane również jako zagrzebane) to układy elektroniczne będące integralną częścią struktury płytki drukowanej. Mogą być nimi elementy dyskretne umieszczane w wewnętrznych warstwach PCB lub elementy pasywne formowane w odpowiedni sposób z warstwy miedzianej (lub z innego materiału).
Klasyczne wielowarstwowe płytki drukowane mają elementy rozmieszczone tylko na warstwach zewnętrznych - warstwy wewnętrzne wykorzystywane są jedynie do rozprowadzenia sygnałów, linii zasilania oraz masy. Takie podejście powoduje, że całkowita powierzchnia płytki nie może być mniejsza od sumarycznej powierzchni wszystkich wchodzących w jej skład elementów, a w zasadzie musi być znacznie od niej większa - należy uwzględnić jeszcze m.in. konieczność zachowania minimalnych odległości pomiędzy elementami.
W przypadku bardzo dużych i złożonych układów ograniczenie to może okazać się dość kłopotliwe i prowadzić do niepożądanego zwiększenia rozmiarów całego urządzenia. Wbudowanie niektórych elementów w strukturę płytki PCB może doprowadzić do rozwiązania tego problemu.
Zalety stosowania elementów wbudowanych
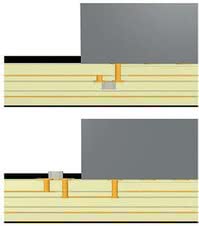
Rys. 1. Wbudowanie elementu pasywnego bezpośrednio pod układem scalonym (góra) pozwala na znaczną redukcję długości połączeń elektrycznych w porównaniu do klasycznego montażu powierzchniowego (dół), w efekcie zaś prowadzi do poprawy jakości pracy urządzenia
Zanim omówiony zostanie sposób projektowania układów wykorzystujących elementy wbudowane, warto przyjrzeć się korzyściom płynącym ze stosowania tego rozwiązania. Jedną z nich jest, jak już wspomniano, możliwość redukcji rozmiarów płytki drukowanej, a dzięki temu także całego urządzenia. Mogą zmniejszyć się również koszty montażu układu (dzięki stosowaniu elementów formowanych).
Obwody drukowane zawierające elementy wbudowane charakteryzują się znacznie lepszymi parametrami dotyczącymi integralności sygnałów oraz dystrybucji zasilania. Jest to spowodowane przede wszystkim mniejszą długością ścieżek elektrycznych pomiędzy poszczególnymi układami.
Ma to szczególne znaczenie w przypadku obwodów wysokiej częstotliwości - skrócenie połączenia między elementami pasywnymi (takimi jak np. kondensatory filtrujące) a układem scalonym obniża wartość pasożytniczych pojemności oraz rezystancji występujących w obwodzie.
Tak jak pokazano na rysunku 1, wbudowanie elementu pasywnego bezpośrednio pod układem scalonym pozwala zminimalizować negatywne efekty związane z długością ścieżek, mogące stanowić problem w przypadku klasycznego montażu powierzchniowego.
Dla elementów umieszczonych w wewnętrznych warstwach płytki drukowanej można stosować dość proste i bardzo skuteczne sposoby ochrony przed działaniem zaburzeń elektromagnetycznych (ochrona EMI) - wystarczy otoczyć układ polem warstwy miedzianej, pełniącym funkcję ekranowania. W pewnych przypadkach rozwiązanie takie może wyeliminować konieczność stosowania dodatkowych, zewnętrznych ekranów.
Głównym problemem wiążącym się ze stosowaniem elementów wbudowanych jest długoterminowa niezawodność układów. Wytrzymałość połączeń lutowniczych umieszczanych w wewnętrznych strukturach laminatu może zostać osłabiona przez późniejsze procesy lutowania, np. lutowanie rozpływowe układów SMD (surface mount device - układ przeznaczony do montażu powierzchniowego).
Rodzaje elementów wbudowanych
Jak już wspomniano, wyróżnia się dwa sposoby wbudowywania elementów w strukturę płytki: formowanie ich z warstwy miedzianej lub umieszczanie w wewnętrznych warstwach laminatu. Poprzez odpowiednie formowanie warstwy miedzianej uzyskać można elementy pasywne, charakteryzujące się określoną rezystancją lub pojemnością. W wewnętrznych warstwach laminatu umieszczać można zarówno elementy dyskretne, jak i całe układy, a nawet chipy krzemowe pozbawione obudowy.
Korzystanie z elementów formowanych obniża koszt montażu całego układu, nie wymaga również wprowadzania żadnych zmian w sposobie produkcji obwodów drukowanych. Takie rozwiązanie może być stosowane w celu zmniejszenia rozmiarów płytki, choć korzystając z dostępnych na rynku pasywnych elementów dyskretnych, które stają się coraz mniejsze (np. w obudowie 01005), można już bardzo często uzyskać zbliżone efekty.
Elementy formowane wciąż mają jednak wiele zalet - umożliwiają obniżenie wielkości pasożytniczych występujących w układzie oraz skrócenie całkowitej długości połączeń elektrycznych na płytce. Niewątpliwie nadal stanowią ciekawą alternatywę dla dyskretnych elementów pasywnych montowanych powierzchniowo.
Jeśli mowa o układach umieszczanych w wewnętrznych warstwach laminatu, przed technologią tą wciąż stoi wiele wyzwań. Główny problem stanowi sposób tworzenia połączenia elektrycznego pomiędzy układem wbudowanym a obwodem drukowanym. Proces ten może być wykonywany dwoma metodami - poprzez lutowanie tradycyjne lub z wykorzystaniem montażu nielutowanego (połączenie bezpośrednie).
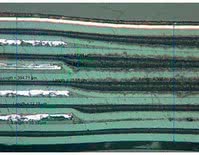
Rys. 3. Przykład układu wykonanego w technologii CIP (Chip-in-Polymer). Kolejne warstwy laminatu nakładane są bezpośrednio na wbudowane komponenty, nie ma więc potrzeby wykonywania otworów. Na powierzchni płytki mogą pojawić się jednak związane z tym nierówności
Tradycyjne połączenia lutownicze mogą zostać uszkodzone w czasie ponownego rozgrzewania laminatu (np. podczas montażu powierzchniowego). Wysoka temperatura może spowodować rozpływ utworzonego już połączenia lutowniczego, a przez to nieprawidłową pracę układu (utratę połączenia lub zwarcie padów).
Aby przezwyciężyć takie problemy, można korzystać z innych, nielutowanych metod montażu, które polegają na bezpośrednim połączeniu miedzianych przelotek z wyprowadzeniami układu. Takie rozwiązanie wymaga jednak stosowania specjalnych układów, których wyprowadzenia (pady) pokryte są warstwą miedzi (nie zaś stopu cyny, tak jak w przypadku standardowych chipów). Na rynku od pewnego czasu dostępne są już tego typu produkty, czego przykładem może być seria GRU firmy Murata, zawierająca kondensatory przeznaczone specjalnie do montażu wbudowanego.
Umieszczenie układów w wewnętrznych warstwach laminatu wymaga wprowadzenia dodatkowych etapów do procesu produkcji obwodów drukowanych. Te dodatkowe czynności różnią się, w zależności od zastosowanej technologii wbudowywania układu, zawsze jednak wymagają uzyskania przestrzeni we wnętrzu laminatu, w której umieszcza się wbudowywany układ. Najpowszechniej stosowane metody to:
- Integrated Module Board (IMB) - montowane komponenty umieszczane są w otworze drążonym w rdzeniu płytki. Otwór ten jest następnie wypełniany polimerem, który zapewnia chemiczną, mechaniczną oraz elektryczną zgodność z podłożem. Połączenia lutownicze również zalewane są polimerem, co pozytywnie wpływa na ich niezawodność i wytrzymałość.
- Embedded chip build-up (ECBU) - do obwodu drukowanego wbudowywane są struktury krzemowe (chipy). Układy te umieszczane są na warstwie poliamidowej, na niej tworzone są również połączenia elektryczne z resztą płytki (rys. 2).
- Chip-in-Polymer (CIP) - układy montowane są w warstwach dielektryka dobudowywanych do powierzchni płytki PCB, nie zaś w jej rdzeniu. Dzięki temu nie ma konieczności wykonywania otworów w płytce, dodatkowa warstwa jest bowiem formowana na powierzchni płytki już po umieszczeniu tam wbudowywanych układów (rys. 3).
Projektowanie elementów pasywnych formowanych
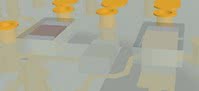
Rys. 4. Wbudowane komponenty mogą być całkowicie zabudowane lub częściowo widoczne. Na rysunku pokazano fragment projektu z trzema elementami wbudowanymi - dwa z nich (zewnętrzne) umieszczone są w otwartych otworach, element środkowy jest całkowicie zabudowany i nie będzie widoczny po wykonaniu obwodu drukowanego
Poprzez formowanie elementów na płytce konstruuje się zazwyczaj rezystory lub kondensatory. W obu przypadkach bardzo ważna jest znajomość właściwości materiałów wykorzystywanych w procesie produkcji obwodu drukowanego.
Rezystor wbudowany jest po prostu obszarem wykonanym z materiału o znanej rezystywności, charakteryzującym się określonymi wymiarami. Rezystancja takiego obszaru może być obliczona z wykorzystaniem wzoru:
![]() |
w którym ρ oznacza rezystywność (opór właściwy) materiału, L jest długością, zaś A polem przekroju poprzecznego obszaru rezystora (W i t to odpowiednio szerokość oraz grubość tego obszaru). Kluczową sprawą jest dobór odpowiedniego materiału, z którego wykonany będzie obszar rezystora (charakteryzującego się właściwą rezystywnością), gdyż od tego zależą finalne wymiary tego elementu na płytce.
Wbudowane kondensatory formować można na wiele sposobów, m.in. jako kondensatory płaskie, czyli parę wykonanych z przewodnika równoległych okładek (elektrod) rozdzielonych warstwą dielektryka. Pojemność tak skonstruowanego układu wyrażana jest wzorem:
![]() |
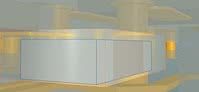
Rys. 5. Wbudowany element, całkowicie niewidoczny z zewnątrz - screen z Altium Designer 14. By rysunek był bardziej czytelny, zarys elementu zaznaczono niebieskimi liniami, zaś zarys otworu liniami pomarańczowymi
gdzie ε0 jest przenikalnością elektryczną próżni, εr to względna przenikalność elektryczna warstwy rozdzielającej okładki (laminatu), A to powierzchnia okładek, zaś d to odległość między nimi (grubość laminatu). Zaprojektowanie kondensatora charakteryzującego się określoną pojemnością wymaga znajomości parametrów laminatu, z którego wykonana jest płytka, jak również odległości między kolejnymi jej warstwami.
Jak wynika z równania, pojemność układu wzrasta wraz ze zmniejszaniem się grubości warstwy dielektrycznej pomiędzy okładkami, stąd też warto korzystać z wytrzymałych laminatów, które umożliwiają minimalizację odległości między kolejnymi warstwami płytki - pozwala to jednocześnie obniżyć całkowitą grubość wielowarstwowego obwodu drukowanego.
Produkcja płytek PCB zawierających elementy wbudowane
Podczas wytwarzania tradycyjnych płytek PCB kolejne etapy procesu produkcji są wyraźnie rozdzielone - na początku powstaje sam obwód drukowany, który następnie przekazywany jest do montażu (ręcznego lub automatycznego). Każdy z tych etapów może być realizowany w innym miejscu i u innego wyspecjalizowanego wytwórcy.
Produkcja układów zawierających elementy wbudowane umieszczone w wewnętrznych warstwach laminatu wymaga równoległej realizacji obu tych procesów. Wbudowywane komponenty muszą być umieszczane w odpowiednich miejscach już w momencie wytwarzania obwodu drukowanego. Za montaż takich elementów odpowiedzialny jest wytwórca PCB, co otwiera nowe perspektywy rozwoju dla producentów maszyn do precyzyjnego montażu SMT.
Producenci układów do montażu SMT muszą jednak uwzględnić specyficzne wymagania związane z montażem elementów wbudowanych. Otwory, w których umieszcza się te komponenty, wykonywane są zazwyczaj z bardzo dużą precyzją, przez co dopuszczalny błąd pozycjonowania montowanego elementu jest raczej niewielki, znacznie mniejszy niż w przypadku montażu powierzchniowego.
Dodatkowo konieczna jest dokładna kontrola siły, z jaką urządzenie umieszcza układ wewnątrz wgłębienia - uszkodzenie komponentu zamontowanego na zewnętrznej powierzchni płytki może być wykryte podczas inspekcji wizualnej, w przypadku elementów wbudowanych detekcja uszkodzeń jest znacznie trudniejsza. Takich elementów nie można również, w przeciwieństwie do układów montowanych na powierzchni płytki, w łatwy sposób wymienić w przypadku uszkodzenia, ich nieprawidłowe działanie może zaś błędnie wpłynąć na pracę całego urządzenia.
Otwór, w którym umieszcza się wbudowywany komponent, nie zawsze musi być zamykany ze wszystkich stron. Pozostawienie takiego otwartego otworu umożliwia wizualną inspekcję układu, upraszcza również jego montaż. Przykład takiego rozwiązania pokazano na rysunku 4.
Przykład oprogramowania wspierającego pracę z elementami wbudowanymi
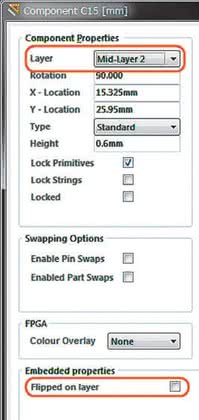
Rys. 7. Edytując właściwości wybranego komponentu, można określić go jako wbudowany (wybierając jedną z wewnętrznych warstw w polu Layer). Można również wybrać orientację odwrotną do globalnie określonej orientacji wybranej warstwy (pole Flipped on layer)
Choć korzystanie z elementów wbudowanych było początkowo domeną dużych przedsiębiorstw OEM wypuszczających na rynek wielkoseryjne układy, w których liczy się każdy centymetr kwadratowy powierzchni płytki PCB, obecnie korzystanie z tej technologii staje się dostępne również dla mniejszych producentów.
Coraz więcej firm produkujących obwody drukowane ma w swojej ofercie tego typu usługi. W tym samym kierunku podążają również twórcy oprogramowania typu EDA (Electronic Design Automation). Przykładem może być popularne środowisko Altium Designer, które od wersji 14. wprowadza możliwość projektowania płytki drukowanej z wykorzystaniem komponentów wbudowanych.
W środowisku Altium Designer komponenty mogą być umieszczane na każdej warstwie sygnałowej, nie zaś, jak w podejściu tradycyjnym, jedynie na warstwach zewnętrznych - górnej i dolnej. Jeśli element zostanie umieszczony na warstwie wewnętrznej, niewidocznej z zewnętrz, oprogramowanie uzna go za komponent wbudowany.
Program dopuszcza dwa sposoby wbudowywania elementów. Pierwszy z nich to utworzenie wgłębienia (cavity), w którym umieszczony zostanie układ. Drugi sposób, stosowany w przypadku obudów o niewielkich rozmiarach (np. 0201), nie wymaga wykonywania otworu.
Element po zamontowaniu jest po prostu obudowywany kolejno dołączanymi warstwami płytki - w rezultacie na powierzchni płytki tworzy się małe wypiętrzenie bezpośrednio w miejscu, pod którym znajduje się komponent.
W przypadku, gdy dla elementu wykonuje się otwór, może on być, jak już wspomniano, zamknięty lub otwarty. Z punktu widzenia projektanta proces umieszczania takiego komponentu jest taki sam, bez względu na rodzaj otworu.
Definiowanie kształtu wgłębienia dla komponentu z biblioteki PCB
Jeśli wybrany element ma zostać wbudowany w wewnętrzną warstwę płytki i konieczne jest wykonanie otworu (Cavity) w strukturze laminatu, otwór ten jest definiowany jako część footprintu w edytorze biblioteki PCB (PCB Library). Warto zauważyć, że zdefiniowanie kształtu otworu nie uniemożliwia umieszczenia tego elementu w warstwie zewnętrznej - w takiej sytuacji parametr ten zostanie po prostu zignorowany przez oprogramowanie. Aby zdefiniować kształt otworu, należy wykonać opisane niżej czynności.
Należy umieścić obiekt typu Region w warstwie mechanical layer. Obiektowi należy nadać kształt i rozmiar projektowanego otworu - musi w pełni otaczać obudowę układu, zapewniając minimalny wymagany zapas odległości. By ustalić potrzebną wartość tej tolerancji, warto skonsultować się z wykonawcą płytki.
W oknie edycji parametrów obiektu (rys. 6) należy ustawić atrybut Kind jako Cavity definition.
Następnie należy określić głębokość otworu - zazwyczaj będzie to wysokość obudowy układu wraz z zapasem odległości wymaganym przez wykonawcę płytki.
Umieszczanie i określanie orientacji wbudowanego komponentu
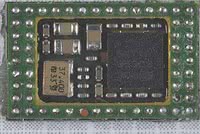
Rys. 9. Przykład stosowania komponentów wbudowanych w urządzeniu mobilnym. Na zdjęciu przedstawiono moduł Wi-Fi montowany w telefonie Samsung Galaxy S4. Komponenty umieszczone są w otwartym wgłębieniu
Aby wbudować wybrany element w wewnętrzną warstwę płytki, należy otworzyć okno edycji właściwości tego elementu (rys. 7) i w polu Layer zaznaczyć jedną z warstw wewnętrznych - tę, w której chcemy umieścić komponent.
Kierunek umieszczenia elementu (góra lub dół) definiowany jest przez ustawienia danej warstwy, które znaleźć można w oknie Layer Stack Manager (rys. 8). Jeśli istnieje potrzeba, aby wybrany komponent miał orientację odwrotną do określonej dla całej warstwy, należy w oknie edycji jego parametrów zaznaczyć pole Flipped on Layer (rys. 7).
Podsumowanie
Wraz z rozpowszechnianiem nowoczesnych technologii wytwarzania obwodów drukowanych, urządzenia wykorzystujące elementy wbudowane zdobywają coraz większą popularność. Tego typu układy znaleźć można m.in. w produktach mobilnych, takich jak smartfony i tablety, w których rozmiary urządzenia są jednym z najważniejszych parametrów (rys. 9).
Technologia ta, wykorzystywana już od pewnego czasu przez dużych producentów, staje się obecnie szeroko dostępna również dla mniejszych projektów. Coraz więcej wytwórni obwodów drukowanych włącza do swojej oferty tego typu usługi. Od pewnego czasu istnieją również szeroko dostępne narzędzia projektowe wspierające stosowanie komponentów wbudowanych.
Warto pamiętać, że wbudowanie niektórych elementów w strukturę płytki drukowanej pozwala ograniczyć rozmiary projektowanego urządzenia oraz poprawić jego parametry elektryczne.
Damian Tomaszewski