Na początku należy zaznaczyć, że bardzo często dobre praktyki z różnych dziedzin kłócą się ze sobą i/lub z wymaganiami aplikacji. Jeśli na przykład priorytetem jest jak najmniejszy rozmiar urządzania, jego komponenty należałoby zamontować jak najbliżej siebie, łącząc je wąskimi ścieżkami, prowadzonymi w małych odstępach. Takie urządzenie najprawdopodobniej nie działałoby jednak prawidłowo z kilku powodów.
Kompromis i właściwe priorytety
Jednym z nich byłyby sprzężenia pomiędzy sygnałami w zbyt gęsto rozmieszczonych ścieżkach. Ponadto elementy różnego typu, układy cyfrowe, analogowe, radiowe, nagromadzone na małej powierzchni w dużej liczbie mogłyby, z powodu różnic w częstotliwości pracy, impedancji lub poziomach napięć, wzajemnie się zakłócać. Niełatwe byłoby także wykonanie bardzo wąskich ścieżek oraz montaż podzespołów bardzo blisko siebie.
W dalszej części artykułu przedstawiamy więcej przykładów wytycznych z różnych dziedzin stojących ze sobą w sprzeczności. Stosowanie się do nich wymaga kompromisu, ten zaś, w pierwszej kolejności, oceny ważności celów projektu.
Jak można uniknąć kumulowania się ciepła?
Rozmieszczenie elementów elektronicznych na płytce drukowanej należy przeanalizować pod wieloma różnymi względami. Są to na przykład zasady kompatybilności elektromagnetycznej. Dzięki ich przestrzeganiu zapobiega się zaburzaniu przez elementy płytki pracy sąsiednich komponentów i innych urządzeń elektronicznych znajdujących się w pobliżu.
Z kolei na podstawie wyników analizy termicznej projektu PCB można uniknąć skupienia obok siebie podzespołów, które nagrzewają się najbardziej. To zapobiega kumulacji wydzielanego przez nie ciepła. Ponadto można odseparować od nich elementy wrażliwe na temperaturę. W zależności od ich typu oraz materiałów, z których je wykonano, niezrobienie tego może mieć różne negatywne skutki.
Wpływ temperatury
Na przykład krzem, podstawowy materiał do budowy elementów półprzewodnikowych, na wzrost temperatury reaguje zmianą przewodności cieplnej, nawet o kilkadziesiąt procent w temperaturach powyżej +100ºC. Oddawanie ciepła do otoczenia przez układ scalony jest wówczas utrudnione. To prowadzi do jego nagrzewania się, przez to do nieprawidłowego działania, a nawet zniszczenia.
Wraz ze wzrostem temperatury maleje wytrzymałość połączeń lutowanych oraz trwałość połączeń klejonych. W wyniku naprężeń towarzyszących zmianom temperatury spowodowanych różnicami pomiędzy współczynnikami rozszerzalności cieplnej elementów PCB dochodzi do ich odkształcania, pękania i rozrywania połączeń. Wysoka temperatura przyspiesza również przebicie starzeniowe dielektryków i elektromigrację.
Dylematy projektanta PCB
Na podstawie wyników analizy termicznej projektu PCB można wykryć konieczność zastosowania chłodzenia lub zwiększenia jego wydajności. W tym celu używa się radiatorów, wentylatorów albo modułów Peltiera.
Na przykładzie chłodzenia można wykazać, że reguły, które zapewniają najlepsze wyniki w jednej dziedzinie, mogą się kłócić z dobrymi praktykami w innym zakresie. Problematycznym elementem bywa ekran, który izoluje od otoczenia podzespoły emitujące silne zaburzenia elektromagnetyczne, blokuje on bowiem drogę przepływu ciepła w procesie konwekcji. W rezultacie ciepło wydzielane przez ekranowane podzespoły, z braku możliwości rozproszenia się w otoczeniu, wnika w płytkę, nagrzewając sąsiednie ścieżki i elementy.
Kolejnym przykładem kłopotliwego elementu jest radiator. W pewnych warunkach może on zacząć działać jak antena. Przyczynia się wówczas do nasilenia się zaburzeń elektromagnetycznych, które są emitowane przez komponent, który chłodzi.
Przelotki cieplne
Na podstawie wniosków z analizy termicznej projektu PCB można zdecydować o wykonaniu w niej przelotek cieplnych. Ich rolą jest zmniejszenie rezystancji termicznej na złączu element - płytka drukowana. Najlepiej, jeżeli mają one formę warstwy miedzi umieszczonej bezpośrednio pod obudową (rys. 1), nie jest to jednak opłacalne. W zamian wykonuje się je w postaci układu oddzielnych platerowanych przelotek jak na rysunku 2.
Liczba i rozmiar przelotek zależą od możliwości ich realizacji w obrębie danej płytki. Należy zachować odpowiedni odstęp między nimi i od granicy obszaru przeznaczonego na ich realizację. Znaczenie ma też wypełnienie przelotek. W przypadku strat mocy poniżej kilku watów przelotki całkowicie wypełnione miedzią mają jednak tylko nieco mniejszą rezystancję termiczną niż te jedynie wewnątrz nią platerowanych.
Pułapki analizy termicznej
Wnioski z analizy termicznej należy wyciągać ostrożnie. Pochopne działania mogą mieć przykre skutki, jeśli zmiany wprowadzone w projekcie PCB okażą się niepotrzebne albo niewystarczające. Jeżeli zostaną przyjęte nadmiernie pesymistyczne założenia i użyte będą zbyt drogie podzespoły, na przykład z materiałów o lepszych właściwościach cieplnych, wentylatory o większej wydajności chłodzenia, niż ta wymagana lub zbędne elementy, na przykład dodatkowe radiatory, projekt będzie nieekonomiczny.
Z drugiej strony niedoszacowanie ilości ciepła wydzielanego przez elementy urządzenia lub ich wrażliwości na zmiany temperatury może doprowadzić do ich zniszczenia. Żeby temu zapobiec, poprawki wprowadza się już po zbudowaniu urządzania, na przykład montując w nim dodatkowe radiatory lub wentylatory. Takie zmiany są jednak droższe i komplikują konstrukcję. Mogą też negatywnie wpływać na parametry urządzania.
Jeszcze o rozmieszczeniu komponentów
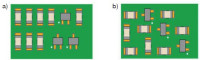
Rys. 3. Podzespoły tego samego typu lepiej jest ustawić w jednym kierunku a) niż rozmieszczać w sposób nieuporządkowany b)
Sposób montażu podzespołów ma wpływ na ich rozmieszczenie na płytce drukowanej. Generalnie przyjmuje się zasadę, że najlepiej jest umieścić wszystkie komponenty przeznaczone do montażu powierzchniowego na tej samej, dolnej warstwie PCB. Podobnie, z tym że na górnej warstwie, powinno się zgrupować wszystkie komponenty przeznaczone do montażu przewlekanego.
Dzięki takiemu rozdzieleniu elementów proces ich montażu przebiega sprawniej. Wlutowanie podzespołów w płytkę drukowaną usprawnia również ustawienie tych podobnego typu w tym samym kierunku. Zostało to zilustrowane na rysunku 3. Lepiej także jest, jeżeli komponenty o większych rozmiarach nie przysłaniają tych mniejszych.
Taką sytuację przedstawia rysunek 4. W dalszej części artykułu przedstawiamy dobre praktyki w zakresie prowadzenia ścieżek sygnałowych oraz realizacji płaszczyzny masy.
Prowadzenie ścieżek sygnałowych
Jeżeli chodzi o ścieżki sygnałowe, to na wstępie należy wytypować kluczowe sygnały, tzn. na przykład te bardziej wrażliwe na zewnętrzne zaburzenia, takie które mogą być źródłem takich zaburzeń oraz te, które przebiegając obok siebie, mogą się wzajemnie zakłócać. Jeżeli konieczne okaże się odizolowanie pewnych sygnałów, najprościej zapewnić między nimi fizyczny dystans, na przykład prowadząc je na innych warstwach.
Jeżeli wymagana jest pełna izolacja, można dodatkowo poprowadzić je wzajemnie prostopadle, a warstwy, na których się znajdą, rozdzielić płaszczyzną masy. Umieszczenie ścieżek prostopadle do siebie ogranicza sprzężenie pojemnościowe, które jest szczególnie duże, jeżeli ścieżki na kolejnych warstwach są prowadzone równolegle do siebie. Płaszczyzna masy między warstwami pełni z kolei funkcję ekranu. Z powodu sprzężenia indukcyjnego należy z kolei unikać prowadzenia długich ścieżek równolegle do siebie na jednej warstwie.
Sygnały specyficzne
Niektóre sygnały wymagają większej uwagi konstruktora. Przykładem jest sygnał zegara. Ścieżki w tym przypadku powinno się prowadzić liniami prostymi, unikając zakrętów. Nie należy korzystać z wielu warstw sygnałowych ani stosować przelotek, które wydłużają ścieżkę oraz powodują zmianę jej impedancji, co może skutkować odbiciem sygnału. Ścieżkę taką najlepiej umieścić na najwyższej warstwie. Jeżeli można ją wykonać tylko na warstwie wewnętrznej, powinna znajdować się między dwoma płaszczyznami masy.
Inny przykład to ścieżki dla sygnałów różnicowych. Powinno się je umieszczać w odległości co najmniej dwukrotnie większej, niż wynosi odstęp między nimi. Same ścieżki pary różnicowej należy prowadzić jak najbliżej siebie. Ogranicza to odbicia sygnałów. Na całej ich długości odległość ta nie powinna się zmieniać. Przelotek najlepiej nie stosować w ogóle, a jeśli to konieczne, to powinno się je wykonać w obydwu ścieżkach pary różnicowej.
Płaszczyzna masy
Bardzo ważną częścią płytek drukowanych stanowi płaszczyzna masy, pełni ona bowiem wiele funkcji. Przede wszystkim stanowi odniesienie dla wszystkich napięć występujących w obrębie płytki. Ponadto spełnia rolę ekranu i radiatora. Płaszczyzna masy ma także wpływ na parametry pasożytnicze elementów PCB, zmniejsza ich indukcyjność i zwiększa pojemność. W związku z powyższym należy jej poświęcić wiele uwagi.
Najlepiej, gdy płaszczyzna masy zajmuje całą jedną warstwę płytki. Najłatwiej zrealizować to w płytkach wielowarstwowych. Na płaszczyznę masy i płaszczyznę zasilania przeznacza się w nich wewnętrzne warstwy, ścieżki sygnałowe prowadząc na tych zewnętrznych.
W przypadku płytki dwuwarstwowej realizacja płaszczyzny masy w ten sposób może w ogóle nie być możliwa. Wówczas zaleca się, żeby przynajmniej 75% powierzchni warstwy przeznaczyć na masę.
Dzielić, czy nie dzielić?
W przypadku płytek drukowanych z obwodami typu mixed-signal płaszczyznę masy często dzieli się na dwie części. Ma to na celu odizolowania masy układów cyfrowych od masy komponentów analogowych. Nie zawsze jest to najlepsze rozwiązanie.
Nie jest ono bowiem zgodne z dwoma bardzo ważnymi zasadami z dziedziny kompatybilności elektromagnetycznej. Pierwsza reguła wymaga zapewnienia jak najkrótszej drogi przepływu prądu powrotnego. Jeżeli się jej nie przestrzega, a rozmiar pętli utworzonej przez prąd powrotny będzie odpowiednio duży, można nieświadomie zbudować antenę ramową.
Alternatywa dla podziału
Druga zasada wymaga, żeby całe urządzenie miało tylko jedną płaszczyznę odniesienia. Jeżeli z kolei nie spełni się tego zalecenia można niechcący zbudować antenę dipolową. Oba ograniczenia można oczywiście obejść, jednak zwykle skomplikuje to projekt PCB.
Dlatego można wykorzystać tylko jedną płaszczyznę masy, natomiast obwody podzielić na dwie sekcje: analogową i cyfrową. Należy jednak unikać wówczas prowadzenia ścieżek przez część analogową i część cyfrową płaszczyzny masy jednocześnie.
Monika Jaworowska