Wprowadzanie poprawek do gotowego projektu PCB bywa niekiedy dość kłopotliwe, może ponadto skutkować nieumyślnym popełnieniem dodatkowych błędów. Należy zatem na tyle starannie wykonywać każdy etap projektowania płytki, aby minimalizować ryzyko powstania poważnych błędów, wymagających znacznej modyfikacji całego projektu.
Reguły projektowe
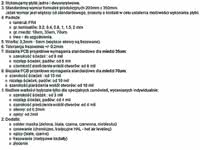
Rys. 1. Przykład możliwości technicznych producenta ze strony internetowej jednej z popularnych polskich wytwórni płytek
Pierwszym krokiem podczas projektowania każdej płytki PCB powinno być określenie reguł projektowych (PCB guidelines). Należy wykonać tę czynność jeszcze przed położeniem pierwszego komponentu czy wyznaczeniem pierwszej ścieżki. Dobrze dobrane reguły projektowe zapewniają ochronę przed znaczną liczbą problemów, które mogą potencjalnie wystąpić podczas produkcji.
Aby móc prawidłowo określić reguły projektowe, należy zapoznać się z ofertą i możliwościami wykonawcy płytki. Na stronie internetowej producenta znaleźć można zazwyczaj informacje nt. ograniczeń produkcyjnych (przykład pokazano na rys. 1) lub nawet gotowe pliki DRC (Design Rule Check), które można zaimportować w wykorzystywanym środowisku projektowym.
Do podstawowych reguł projektowych zalicza się minimalną szerokość ścieżek, minimalny odstęp między ścieżkami oraz rozmiar otworów/przelotek. Dobranie nieodpowiednich reguł może doprowadzić to tego, że producent nie będzie w stanie wykonać płytki lub wykona ją niewłaściwie.
Rozmieszczenie elementów
Rozmieszczanie elementów na płytce jest być może najbardziej krytycznym etapem całego cyklu projektowego, gdyż właśnie od tego zależy łatwość prowadzenia połączeń elektrycznych oraz końcowy rozmiar płytki. Sposób rozmieszczenia komponentów ma również decydujący wpływ na przebieg oraz efektywność procesu montażu.
Aby uniknąć kłopotów na etapie montażu płytki (szczególnie jeśli jest to montaż automatyczny), należy podczas rozmieszczania elementów zwrócić szczególną uwagę na następujące aspekty:
- orientacja elementów. Komponenty tego samego lub podobnego rodzaju powinny być w miarę możliwości ułożone w tym samym kierunku (jak pokazano na rys. 2a), gdyż minimalizuje to ryzyko powstania błędu podczas procesu lutowania. Takie ułożenie ułatwia rozprowadzanie pasty lutowniczej oraz rozpływ lutowia.
- przesłanianie elementów. Podczas korzystania z niektórych technik lutowania (np. lutowanie manualne, na fali czy gorącym powietrzem) należy szczególnie uważać, aby montowane elementy nie przesłaniały się wzajemnie - może to bardzo utrudnić montaż lub przyczynić się do powstania nieprawidłowych połączeń lutowniczych. Na rysunku 2b przedstawiono konsekwencje takiej sytuacji dla lutowania na fali. Jeśli małe komponenty zostaną podczas przechodzenia przez falę przesłonięte (uwzględniając kierunek fali), mogą pozostać nieprzylutowane.
- rozmieszczenie elementów na warstwach. Dostępność różnych sposobów przeprowadzenia montażu i jego koszt zależą w dużej mierze od tego, w jaki sposób elementy rozmieszczone zostaną na obu warstwach płytki. Jeśli w projekcie wykorzystuje się zarówno elementy przewlekane, jak i montowane powierzchniowo, najtaniej będzie rozmieścić wszystkie komponenty na warstwie górnej. Bardziej szczegółowy opis zależności pomiędzy rozmieszczeniem elementów na różnych warstwach płytki a dostępnymi sposobami montażu przedstawiony został w dalszej części tekstu.
Montaż mieszany
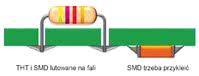
Rys. 3. Jeśli rozmieścimy elementy THT w warstwie górnej a SMD w warstwie dolnej, całość będzie można zmontować podczas jednego procesu lutowania na fal
Decydując się na korzystanie zarówno z elementów SMD, jak i THT, należy liczyć się ze wzrostem kosztów wytworzenia płytki z uwagi na konieczność realizacji dodatkowych etapów podczas jej montażu. Możliwość zastosowania poszczególnych technik montażu oraz ich koszt zależą głównie od sposobu rozmieszczenia komponentów różnego typu na płytce.
W przypadku rozmieszczenia elementów THT na warstwie górnej, a elementów SMD na warstwie dolnej, całość może zostać zmontowana podczas jednego procesu lutowania na fali (rys. 3). Przedtem elementy SMD należy jednak przykleić do płytki.
W dodatku nie można w ten sposób montować układów BGA. W przypadku prostych projektów zaletą jest jednak to, że mogą być w taki sposób zrealizowane na płytce jednostronnej.
Jeśli wszystkie elementy rozmieszczone zostaną w warstwie górnej (rys. 4), montaż będzie musiał przebiegać dwuetapowo. Elementy SMD mogą być lutowane w piecu rozpływowym, zaś układy THT przez lutowanie na fali lub w przypadku niewielkiej ich liczby ręcznie. Takie rozwiązanie jest w większości przypadków najtańsze.
Podczas korzystania z komponentów mieszanych należy w miarę możliwości unikać rozmieszczania układów SMD po obu stronach płytki. Rozwiązanie takie (rys. 5) bardzo ogranicza dostępne sposoby montażu. Układy THT muszą być wtedy lutowane za pomocą fali selektywnej, jednak nie wszystkie zakłady produkcyjne oferują taką możliwość. W innym wypadku trzeba lutować je ręcznie.
Prowadzenie ścieżek
Zaleca się, aby płaszczyzny zasilania oraz masy znajdowały się wewnątrz płytki, symetrycznie względem siebie. W przypadku płytek wielowarstwowych warto przeznaczyć na płaszczyzny masy i zasilania po jednej warstwie wewnętrznej. Pozwala to zapewnić odpowiednio niską, wyrównaną na całym obszarze płytki impedancję masy.
Zapobiega również odkształcaniu płytki, które negatywnie wpływa na dokładność rozmieszczenia elementów. Prowadząc linie zasilania oraz masy, należy zapewnić odpowiednią szerokość ścieżek (w zależności od maksymalnego natężenia prądów zasilania) oraz unikać prowadzenia zasilania w sposób łańcuchowy, czyli od elementu do elementu.
Przebieg ścieżek sygnałowych na każdej z warstw dobrze jest uporządkować względem kierunku - jeśli połączenia na warstwie dolnej biegną horyzontalnie, połączenia na warstwie górnej powinny być prowadzone wertykalnie.
Analiza termiczna
Nieprawidłowy projekt termiczny płytki może być przyczyną poważnych i trudnych do wykrycia błędów. Dlatego dla każdego projektu powinno się wykonać przynajmniej uproszczoną analizę sposobu rozprowadzania ciepła na płytce.
Pierwszym krokiem takiej analizy jest identyfikacja układów rozpraszających największe ilości energii cieplnej. W tym celu można przejrzeć dokumentację układów oraz skorzystać z zawartych tam wskazówek. Najbardziej grzejące się układy muszą być rozmieszczane w odpowiedniej odległości od wszelkich elementów krytycznych oraz wrażliwych na zmiany temperatury otoczenia, takich jak czujniki czy przetworniki.
Następnie należy zastanowić się nad odprowadzeniem ciepła generowanego przez układy. Dobrym sposobem na poprawę właściwości termicznych jest stosowanie przelotek cieplnych (rys. 6). Pozwalają one odprowadzić ciepło z elementu do innych obszarów płytki, z których oddawane jest do otoczenia.
Fiduciale
Terminem fiducial określa się punkt referencyjny na powierzchni płytki, który pozwala na kalibrację maszyny montażowej. Może ona dokładniej określić położenie płytki i dzięki temu precyzyjniej rozmieścić na niej elementy.
Typowy wygląd fiduciala przedstawiono na rysunku 7. Fiducial ma najczęściej kształt koła, z usuniętą maską lutowniczą, bez otworu w środku i bez połączenia ze ścieżkami. Jego rozmiary i kształt nie są precyzyjnie określone, ważne jest jednak, aby wszystkie fiduciale na płytce były dokładnie takie same.
Nie ma precyzyjnej definicji, ile znaczników referencyjnych powinno się znaleźć na powierzchni płytki. Zaleca się użycie przynajmniej trzech w narożnikach płytki, po jednym w każdym narożniku, na wszystkich warstwach, na których znajdują się elementy SMD (jeśli układy te rozmieszczone są na obu warstwach płytki, rozmieszcza się po trzy znaczniki na każdej z warstw).
Dodatkowo, jeśli stosuje się układy o dużej liczbie wyprowadzeń, wymagające bardzo precyzyjnego rozmieszczenia (obudowy BGA, QFN, QFP), warto rozmieścić dodatkowe punkty referencyjne w pobliżu tych układów (rys. 8). Jeśli płytki układa się w arkusz (panel), fiduciale powinno się umieścić również w narożnikach tego arkusza (rys. 9).
Inspekcja projektu
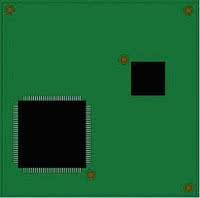
Rys. 8. Przykładowe rozmieszczenie znaczników referencyjnych - w narożnikach płytki i w pobliżu układów trudnych w montażu
Po zakończeniu prac nad projektem bezwzględnie należy poddać go inspekcji, najlepiej prowadzonej niezależnie przez kilka osób. Dwu- lub trzykrotne sprawdzenie całego projektu może wydawać się czynnością żmudną i czasochłonną, często przesądza jednak o powodzeniu całego przedsięwzięcia.
Pierwszym krokiem inspekcji powinno być sprawdzenie projektu za pomocą narzędzi oferowanych przez środowisko projektowe - ERC (Electrical Rules Check) oraz DRC (Design Rules Check). Jeśli prawidłowo zdefiniowano reguły projektowe, na tym etapie powinna być możliwa identyfikacja większości poważnych błędów.
Po pozytywnym ukończeniu wspomnianych testów warto prześledzić przebieg każdej ścieżki na płytce i porównać go ze schematem, upewniając się, że nic nie zostało pominięte. Jest to również dobra okazja do wprowadzenia drobnych korekt, jak np. skrócenia i wyprostowania ścieżek czy złagodzenia ich załamań (nie zaleca się prowadzenia ścieżek pod kątem powyżej 45°).
Przygotowanie dokumentacji produkcyjnej
Prawidłowe przygotowanie dokumentacji produkcyjnej jest warunkiem koniecznym, aby płytka mogła zostać wykonana poprawnie i zgodnie z wolą zamawiającego. Warto zatem przejrzeć zestaw plików produkcyjnych generowanych przez środowisko projektowe, aby upewnić się, że zawiera wszystkie pozycje wymagane przez wytwórnię. Wygenerowane pliki należy trzymać w jednym archiwum o przejrzystej strukturze i nazewnictwie.
Złym pomysłem jest wysyłanie do wytwórni plików projektowych, do których obsługi konieczne jest posiadanie określonego środowiska projektowego, gdyż z dużym prawdopodobieństwem nie będzie ona dysponować takim oprogramowaniem. Zamiast tego zdecydowanie lepiej jest skorzystać z zestawu plików Gerber.
W razie jakichkolwiek problemów, wątpliwości czy sytuacji nietypowych zawsze dobrze jest skontaktować się z wytwórcą płytki - ścisła wzajemna komunikacja zapobiega powstawaniu niedomówień i niejasności, przez co jest kluczem do końcowego sukcesu.
Klasy urządzeń
Dokument normatywny IPC-A-600 (kryteria dopuszczenia płyt drukowanych) definiuje trzy klasy produktów, różniące się dokładnością wykonania oraz niezawodnością:
- klasa 1 (najniższa niezawodność i jakość wykonania) to ogólne produkty elektroniczne domowego zastosowania (np. zabawki, proste AGD), o ograniczonym czasie życia, dla których jedynym wymaganiem jest prawidłowe funkcjonowanie urządzenia.
- klasa 2 to produkty elektroniki przemysłowej i usługowej (np. sprzęt telekomunikacyjny, niektóre urządzenia przemysłowe), gdzie wymagana jest niezawodność i wydłużony czas życia, a nieprzerwane działanie jest pożądane, ale nie jest warunkiem krytycznym.
- klasa 3 (najwyższa niezawodność i jakość wykonania) to urządzenia, które muszą zadziałać zawsze, gdy są potrzebne. Produkty tej klasy wykorzystuje się m.in. w przemyśle motoryzacyjnym, lotniczym oraz aparaturze medycznej.
Określenie klasy urządzenia należy do obowiązków zlecającego produkcję. Zakład produkcyjny powinien zostać poinformowany o pożądanej klasie wykonania płytki, szczególnie jeśli ma to być klasa 3, musi również zadeklarować gotowość do wykonania produktu tej jakości. Dopuszczalne jest też określenie odmiennych typów klas dla różnych charakterystyk płytki - dla przykładu, można określić, że w wykonanych płytkach odstęp pomiędzy ścieżkami powinien spełniać wymagania dla klasy 3, a pozostałe cechy powinny spełniać wymagania dla klasy 2.
Dyrektywa RoHS
Od czasu wprowadzenia dyrektywy RoHS (Restriction of Hazardous Substances) szczególnego znaczenia nabrała kontrola rodzajów materiałów wykorzystywanych w stopach lutowniczych. Jeśli gotowy produkt ma spełniać wymagania dyrektywy, bezpieczniej jest zawrzeć taką informację bezpośrednio w dokumentacji produkcyjnej. Podobnie jest w przeciwnym przypadku - jeśli nie jest konieczne lutowanie z wykorzystaniem stopu bezołowiowego (produkt jest wyłączony spod dyrektywy RoHS), również należy zaznaczyć to w dokumentacji przesyłanej do wytwórcy.
Typowe błędy
Poniżej wymieniono przykłady często popełnianych podczas projektowania błędów, które zazwyczaj bywają później źródłem kłopotów podczas montażu.
Umieszczanie przelotek na polach lutowniczych. Podczas lutowania w piecu rozpływowym pasta lutownicza wpływa do wnętrza przelotki znajdującej się na polu lutowniczym, montowany element pozostaje zaś nieprzylutowany. Aby tego uniknąć, przelotki należy umieszczać obok pól lutowniczych.
Zbyt mały rozmiar elementów. Jeśli inne uwarunkowania tego nie wymuszają, nie trzeba stosować elementów w najmniejszym dostępnym rozmiarze. Mogą być one wprawdzie tańsze od większych odpowiedników, ich montaż jest jednak droższy i bardziej kłopotliwy. Większe elementy ułatwiają ponadto proces kontroli jakości oraz ewentualnej późniejszej naprawy płytki.
Brak łezek przy pierścieniach wokół małych otworów. W przypadku małych otworów (przelotki, pady) brak łezki w miejscu styku miedzianego pierścienia otworu ze ścieżką może być przyczyną powstania rozwarcia (rys. 10). Ryzyko powstania rozwarcia rośnie wraz ze zmniejszaniem się średnicy otworu oraz szerokości pierścienia. Zjawisko to wynika przede wszystkim ze zbyt małej sztywności wykorzystywanych w procesie produkcji wierteł.
Zbyt małe średnice otworów dla elementów THT. Projektanci zapominają niekiedy, że metalizacja zmniejsza średnicę otworu o ok. 0,1 mm, mniej więcej tyle samo wynosi też dokładność procesu wykonywania otworów. Projektując metalizowane otwory dla elementu THT, należy zwiększyć ich średnicę przynajmniej o 0,2 mm. Warto pamiętać, że jeśli nawet otwór będzie trochę zbyt duży, nie będzie to stanowić większego problemu. Jeśli jednak będzie za mały i nie da się w niego włożyć nóżek elementu, konieczne będzie rozwiercenie otworu (zniszczy metalizację) lub zginanie jego nóżek, które jest bardzo czasochłonne.
Napisy na polach lutowniczych. Warstwa opisowa płytki w żadnym wypadku nie powinna nachodzić na pola lutownicze, ponieważ może to utrudnić lub wręcz uniemożliwić prawidłowy montaż elementu.
Podsumowanie
Projektowanie płytki PCB jest procesem długim i trudnym. Nawet najmniejszy błąd lub niedopatrzenie może stanowić o sukcesie lub porażce całego przedsięwzięcia. W dodatku skutki popełnionych błędów często widoczne są dopiero po zakończeniu produkcji płytki, czasem zaś ujawniają się już w trakcie użytkowania produktu. Warto zatem starać się minimalizować ryzyko popełnienia błędu i maksymalizować prawdopodobieństwo ich detekcji na etapie projektowym, podczas którego ich naprawienie jest zdecydowanie najmniej kosztowne.
Produkcja płytki w wytwórni to nie tylko zwieńczenie cyklu projektowego, ale również skomplikowany i zaawansowany technologicznie proces. Prawidłowość jego przebiegu zależy w dużej mierze od jakości projektu - by ją poprawić, warto m.in. poznać możliwości zakładu produkcyjnego i dopasować do nich swój projekt.
Damian Tomaszewski