Infineon przeprowadził badania określające wpływ wyższych częstotliwości (aż do 50 kHz) przełączania falowników na sprawność energetyczną zespołu falownik plus silnik. Dotyczy to urządzeń bazujących na tranzystorach przełączających o szerokiej przerwie energetycznej (WBG), a więc z węglika krzemu (SiC) i azotku galu (GaN). W artykule omówiono szczegóły tych badań i omówiono wyniki symulacji i pomiarów.
Konfiguracja testowa
Konstrukcja falownika składa się z trzech stopni półmostkowych wykonanych jako modułowe płytki nakładkowe. Takie podejście upraszcza i przyspiesza testowanie różnych rozwiązań w zakresie technologii przełączania. W rezultacie falownik zawiera sześć tranzystorów mocy CoolGaN 600 V o RDS(ON)=55 mΩ (IGT60R070D1) oraz CoolSiC 650 V w obudowie TOLL (IMT65R048M1H). Elementy te są sterowane przez dwukanałowe drivery bramki z rodziny EiceDRIVER o oznaczeniu 2EDF7175F.
Pomocnicze napięcia zasilania dla driverów strony dolnej i górnej mostka zrealizowano z użyciem izolowanego zasilacza, zapewniającego możliwość regulacji napięcia wymaganej dla różnych technologii: SiC 18 V i GaN 10 V. Aby zapewnić precyzyjną kontrolę sterowania przełącznikami w falowniku, za pomocą czujników prądu Halla XENSIV TLI4971 mierzone są prądy w każdej z faz wyjściowych. Następnie wyniki pomiarów trafiają do mikrokontrolera XMC XMC4400, który wykorzystuje również czujniki położenia wirnika do realizacji sterowania polowego (Field Oriented Control, FOC) przy regulacji prędkością silnika synchronicznego z magnesami trwałymi (Permanent Magnet Synchronous Motor, PMSM).
Silnik indukcyjny działa też jako hamulec mechaniczny bazujący na prądach wirowych w celu regulacji momentu obrotowego wału. Użycie jako obciążenia silnika indukcyjnego zapewniło płynne działanie bez zacinania się przy małych prędkościach charakterystycznego dla hamulców mechanicznych. Płytka i konfiguracja testowa użyte w tej analizie pokazane są na rysunku 1.
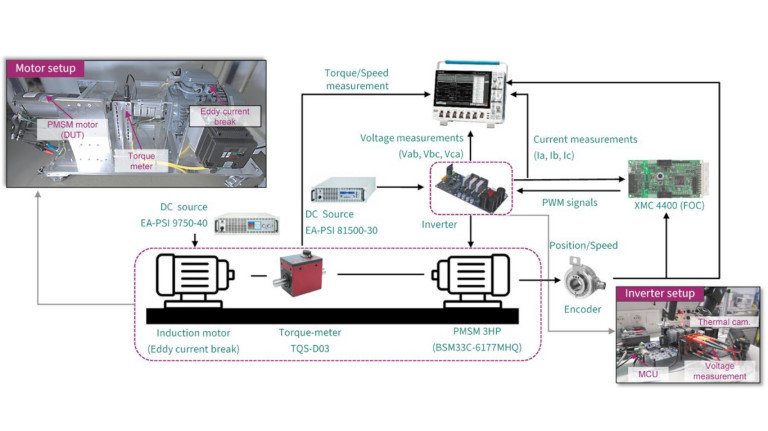
Straty mocy falownika
W falowniku energia jest tracona, gdy prąd stały, a dokładniej wyprostowanie napięcie sieci jest przekształcane na prąd przemienny trójfazowy. Sumaryczne strata energii wynika ze strat rezystancyjnych w elementach falownika, procesu przełączania (komutacji) w przełącznikach mocy i strat powstających w nieidealnych elementach pasywnych. Ilość traconej energii zależy od konstrukcji i specyfikacji falownika i jest bezpośrednio związana z częstotliwością przełączania stopnia mocy.
Wyższe częstotliwości przełączania zwiększają straty komutacyjne ze względu na większą liczbę przełączeń w jednostce czasu. Dlatego wybór odpowiedniej częstotliwości przełączania falownika jest ważny w celu zoptymalizowania całkowitej sprawności układu napędowego. Na poziom strat ma wpływ użyta technologia półprzewodnikowa tranzystorów oraz parametry z nimi związane, takie jak napięcie znamionowe i prąd, częstotliwość przełączania, współczynnik wypełnienia, szybkość zmiany napięcia (dv/dt) i rezystancja bramki tranzystorów (Rg).
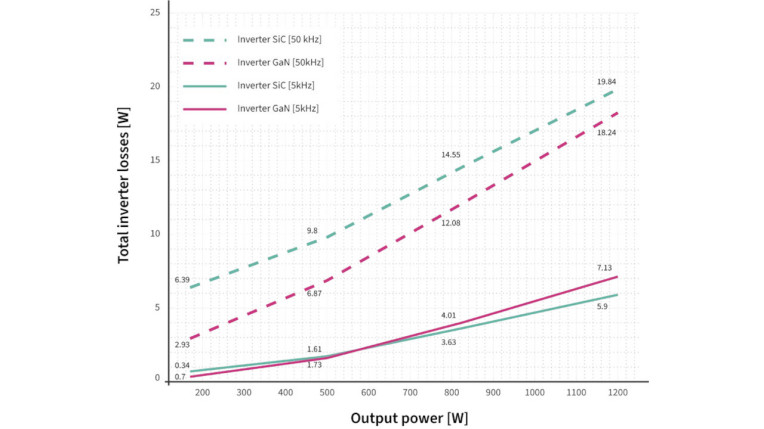
przełączników i częstotliwości
Rysunek 2 przedstawia wyniki symulacji poziomu strat mocy przy użyciu PLECS dla tranzystorów przełączających w technologii GaN i SiC o napięciu znamionowym 600–650 V, pracujących przy napięciu 320 V i prądzie 8 A, od najniższej do najwyższej częstotliwości przełączania. Jak widzimy, elementy SiC mają niewielką przewagę nad GaN-ami przy niższych częstotliwościach (5–10 kHz), jednak od 20–50 kHz GaN zapewniają znacznie niższe straty mocy w porównaniu z technologią SiC. Bez względu na to optymalizacja wydajności i sprawności układu napędowego silnika wymaga również uwzględnienia reszty komponentów systemu.
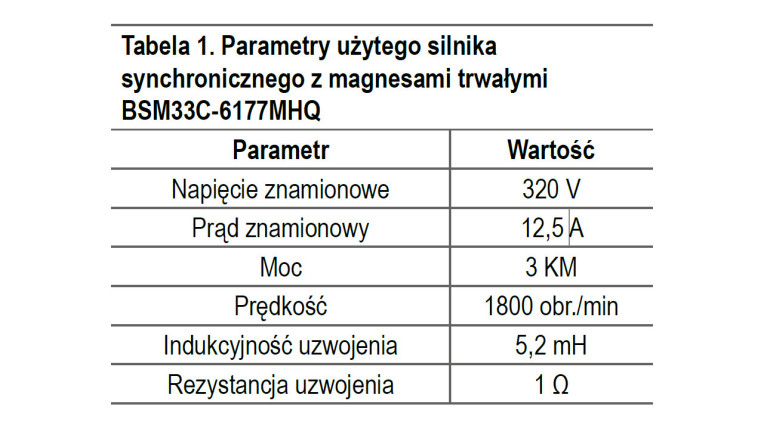
Straty mocy w silniku
W drugiej części skupiono się na stratach powstających w uzwojeniach silnika, których źródłem jest wysoka częstotliwość napięć zasilania. Podział pomiarów na składowe wysokiej i niskiej częstotliwości wykonano przy użyciu iteracyjnego procesu i wielu filtrów dolnoprzepustowych. Rysunek 3 przedstawia wyniki pomiarów prądu uzyskane przez dyskryminację. W przypadku napięcia zastosowano również podobny proces separacji.
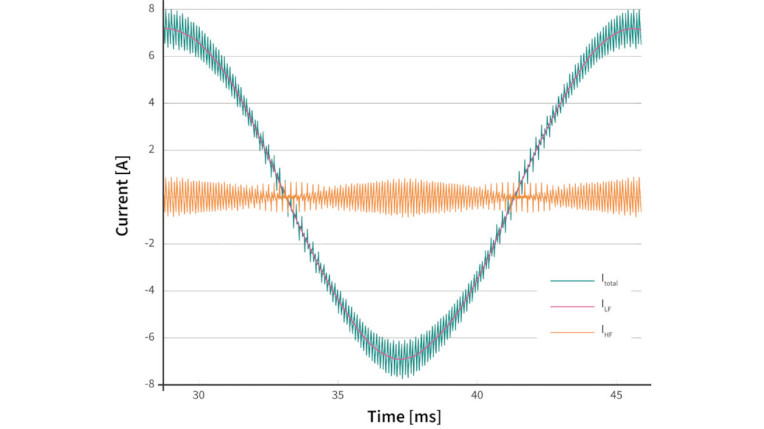
częstotliwości PWM
Rysunek 4 przedstawia prąd fazowy o wysokiej częstotliwości po przeprowadzeniu kondycjonowania. Zgodnie z oczekiwaniami tętnienia prądu są niższe przy wyższych częstotliwościach przełączania, a mniejsze tętnienia prądu pomagają również zmniejszyć ilość traconej energii.
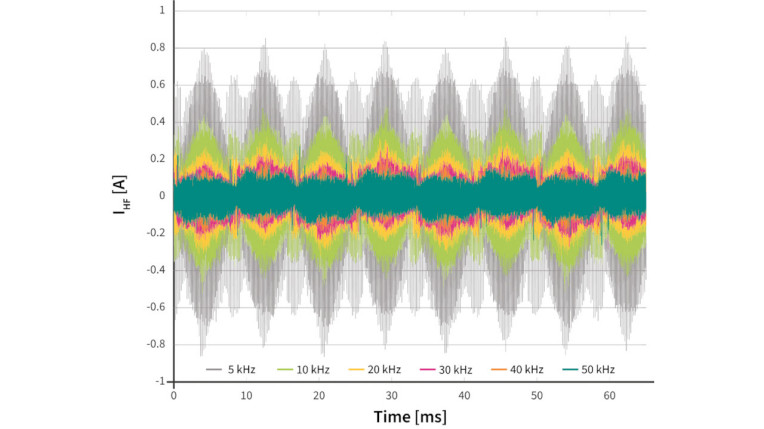
Straty mocy w silnika przy dużej częstotliwości
Wysokoczęstotliwościowe straty mocy w silnikach można obliczyć przy użyciu następującego równania:

Wielkość tego parametru dla różnych częstotliwości przełączania i różnych prędkości obrotowych silnika pokazano na rysunku 5, gdzie:
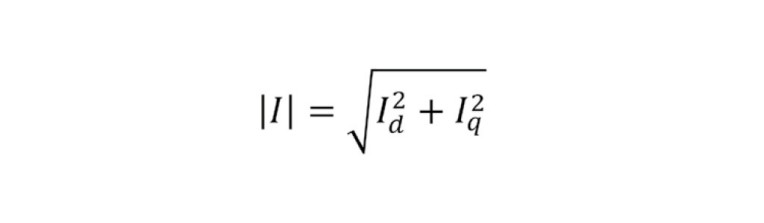
Straty przy 900 obr./min i 50 kHz są zbyt małe, aby je pokazać na wykresie.
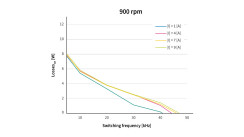
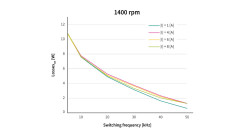
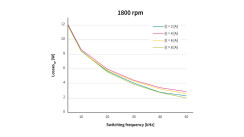
Wyniki pokazują wyraźny wpływ częstotliwości nośnej PWM na poziom strat w silniku, przy czym straty mocy dla dużych częstotliwości są znacznie mniejsze. Największe występują przy 1800 obr./min i 5 kHz. W tym punkcie pracy wynoszą około 12 W, podczas gdy przy tej samej prędkości i częstotliwości 50 kHz wynoszą tylko 2 W, co stanowi 10-watową oszczędność energii.
Innym spostrzeżeniem jest to, że straty wysokoczęstotliwościowe zależą od prędkości obrotowej silnika, prawdopodobnie z powodu wyższych prądów wirowych w elektromagnesach przy większych prędkościach. Straty w rdzeniu to kolejna cecha, która zmienia się wraz z prędkością, przy czym histereza zwiększa się wraz z prędkością silnika, co również wpływa na poziom utraty mocy w silniku.
Straty całkowite
Na wydajność układu napędowego silnika wpływają parametry takie jak obciążenie, prędkość i temperatura. Zmniejszenie strat energii w stosunku do mocy wyjściowej zapewnia optymalną wydajność pracy silnika. Analiza łączna strat silnika o wysokiej częstotliwości i falownika (rys. 6) wykazała, że optymalny punkt pracy, w którym układ napędowy silnika wykazuje najniższe straty w stosunku do swojej mocy wyjściowej, został osiągnięty przy częstotliwości przełączania 20 kHz podczas pracy z nominalną prędkością 1800 obr./min i 50-procentowym obciążeniu znamionowym, tj. 1,1 kW.
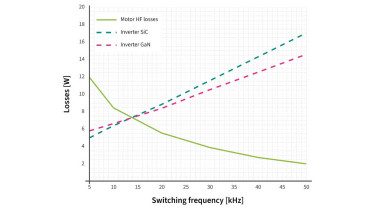
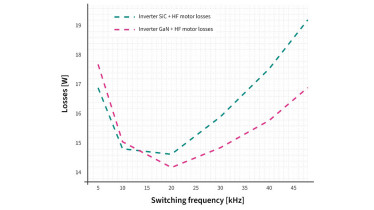
Utrzymywanie punktu pracy jak najbliżej tego warunku jest kluczowe dla zminimalizowania rozpraszania mocy. Rysunek 6 potwierdza ponadto, że wybór optymalnej częstotliwości nośnej PWM wymaga oceny na poziomie całego systemu, w tym rozważenia technologii półprzewodnikowej, która determinuje poziom strat komutacyjnych i maksymalną częstotliwość nośną dla PWM.
Podsumowanie
W przypadku stosowania tranzystorów mocy o szerokiej przerwie energetycznej układy napędowe silników pracujące przy wyższych częstotliwościach przełączania mogą zapewnić wyższą całkowitą wydajność systemu. Jednak częstotliwość przełączania powinna być starannie dobrana ze względu na kompromis między wielkością strat w falowniku i silniku.
Wyniki pomiarów i symulacji wykazały, że straty mocy w silniku dla prądów zasilających o wysokiej częstotliwości są mniejsze przy wyższej częstotliwości nośnej PWM. Jednak konieczna jest dalsza analiza wpływu żywotności łożysk i uzwojeń silnika przy wysokich częstotliwościach przełączania i szybkich stanach przejściowych.
Nowo projektowane napędy silników muszą uwzględniać możliwości kryjące się w półprzewodnikach SiC i GaN, gdyż wymagania rynku w zakresie sprawności urządzeń cały czas się zwiększają. Ponadto przyszłe projekty powinny również pomóc rozwiązać problemy pojawiające się przy wyższych częstotliwościach przełączania, np. zużycie łożysk i grzanie się uzwojeń itp.
Infineon
www.infineon.com