Różne materiały rozmaicie reagują na zmiany temperatury. Na przykład w przypadku krzemu, pod wpływem temperatury przewodność cieplna maleje w przybliżeniu o 20% przy wzroście temperatury w zakresie od około 77ºC do około 127ºC. Utrudnia to oddawanie ciepła do otoczenia przez strukturę układu scalonego, która nagrzewa się w trakcie pracy.
Bez dodatkowego chłodzenia może to skutkować jej uszkodzeniem. Innym przykładem jest miedź. W przypadku tego materiału pod wpływem temperatury zmienia się rezystywność - przy wzroście temperatury o każde kolejne 10ºC parametr ten rośnie w przybliżeniu o 4%. Z tego powodu zmienia się rezystancja ścieżek łączących komponenty na płytce, a w rezultacie także rozkład napięć i prądów w obrębie PCB.
W przypadku wielu materiałów wykorzystywanych w elektronice wraz ze wzrostem temperatury zmienia się również współczynnik sprężystości i plastyczność. Przykładem jest stop Sn3,5Ag, którego moduł Younga maleje w przybliżeniu o 20% w zakresie temperatur od 50ºC do 100ºC. W efekcie zmniejsza się wytrzymałość połączeń lutowanych.
Rozrywanie połączeń, odkształcenia lub pękanie scalonych ze sobą elementów może być też efektem naprężeń, które powstają przy zmianach temperatury na skutek niedopasowania pod względem współczynnika rozszerzalności cieplnej. Przy wzroście temperatury zmniejsza się też trwałość połączeń klejonych. Do negatywnych zjawisk, które zachodzą szybciej pod wpływem temperatury, zalicza się również m.in. przebicie starzeniowe dielektryka oraz elektromigrację.
Analiza termiczna
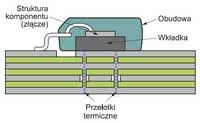
Rys. 1. Obudowy typu QFN mają metalowe wkładki zamocowane na spodzie, które służą do odprowadzania ciepła wydzielanego w strukturze komponentu
Problemów w funkcjonowaniu urządzeń elektronicznych spowodowanych temperaturą można uniknąć, przeprowadzając rzetelną analizę termiczną projektu PCB. Pozwala ona określić rozkład temperatur w obrębie poszczególnych części urządzenia, dzięki czemu można wykryć miejsca, w których ciepło wydzielane przez komponenty urządzenia będzie się kumulować.
Oceniając, jak wpłynie to na pracę innych podzespołów, można zawczasu odpowiednio zmodyfikować projekt urządzenia lub uzupełnić go o właściwy system chłodzenia. W zależności od potrzeb konieczne może być zamontowanie dodatkowych radiatorów, wentylatorów lub pomp ciepła. Analiza termiczna może się ograniczać do wyznaczenia średniej temperatury PCB.
Z reguły jednak wykorzystuje się w niej złożony model urządzenia, który pozwala na przeanalizowanie tego, jak w czasie zmienia się rozkład temperatur i jak wpływa to na parametry poszczególnych komponentów. By taki model odzwierciedlał rzeczywiste warunki, uwzględnić trzeba szereg czynników, m.in. przepływ powietrza wokół komponentów wywołany naturalną i wymuszoną konwekcją oraz zjawisko promieniowania i przewodzenia ciepła.
Sprawę dodatkowo komplikuje fakt, że analizie poddawane są konstrukcje o skomplikowanej geometrii, składające się z wielu komponentów elektronicznych nagromadzonych na stosunkowo niewielkiej powierzchni. Ponieważ samodzielne przeprowadzenie takiej symulacji wymagałoby rozległej wiedzy m.in. z zakresu dynamiki płynów, w tym celu wykorzystuje się specjalistyczne oprogramowanie.
Uproszczona analiza termiczna
Przed przystąpieniem do analizy termicznej z wykorzystaniem specjalistycznych narzędzi można jednak wykonać pewne uproszczone obliczenia, które pozwalają opracować wstępny projekt PCB. Wykorzystując proste modele cieplne elementów urządzenia, można na przykład określić wymagany rozmiar i sposób konstrukcji PCB oraz sprawdzić, czy konieczne jest zastosowanie dodatkowego chłodzenia, a jeżeli tak, to w przybliżeniu o jakiej wydajności.
Parametry komponentów wykorzystywane we wstępnych obliczeniach analizy termicznej są zwykle podawane w specyfikacji komponentu. Zasady takiej uproszczonej analizy zostaną przedstawione na przykładzie analizy termicznej projektu czterowarstwowej PCB, na której zamontowany będzie układ scalony w obudowie typu QFN (Quad Flat No-Lead) - rysunek 1. Charakterystyczną cechą obudów tego rodzaju jest metalowa wkładka zamocowana na spodzie, która służy do odprowadzania ciepła wydzielanego wewnątrz komponentu.
Przykład
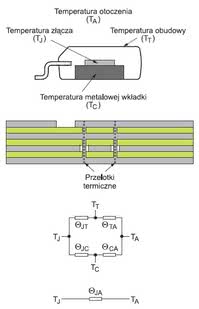
Rys. 2. Rezystancję termiczną złącze-otoczenie można wyznaczyć jako zastępczą wartość równoległego połączenia rezystancji termicznych kanałów, którymi ciepło jest odprowadzane do otoczenia
Jednym z kluczowych parametrów, których znajomość jest wymagana do przeprowadzenia zgrubnej analizy cieplnej, jest termiczna rezystancja między złączem i otoczeniem (ΘJA). Jest to zastępcza wartość równoległego połączenia rezystancji termicznych kanałów, którymi ciepło jest przez dany komponent odprowadzane do otoczenia (rys. 2).
Część ciepła, która jest przekazywana bezpośrednio z wnętrza układu do jego obudowy, napotyka opór charakteryzowany przez rezystancję ΘJT. Następnie ciepło to jest wydzielane do otoczenia przez obudowę dzięki zjawisku konwekcji i radiacji, napotykając opór wyrażany ilościowo przez rezystancję termiczną ΘTA.
Oprócz tego wymiana zachodzi też za pośrednictwem metalowej wkładki na spodzie komponentu reprezentowanej przez rezystancję termiczną (ΘJC), przez którą ciepło wnika do PCB. Stąd jest ono również w procesie konwekcji i promieniowania odprowadzane do otoczenia, napotykając opór wyrażany przez parametr ΘCA.
Ten z kolei obejmuje sumę rezystancji: ΘCU - oporu termicznego płaszczyzny miedzi, ΘFR4 - termicznej rezystancji laminatu, ΘVIA - rezystancji termicznej przelotek umieszczonych bezpośrednio pod metalową wkładką oraz ΘSA, czyli opór termiczny na styku powierzchni PCB i powietrza. Rezystancję ΘJA wyznaczyć też można jako iloraz różnicy temperatury złącza i temperatury otoczenia przez moc strat układu.
Przykładowo jeżeli moc strat komponentu wynosi 1W, temperatura w jego otoczeniu będzie się utrzymywać na poziomie 40ºC, natomiast maksymalna temperatura jego złącza nie powinna przekroczyć 100ºC, to ze wzoru tego wynika, że jego rezystancja termiczna wynosi (100ºC-40ºC)/1W = 60ºC/W.
Parametr ten jest jednym ze składników wzoru inżynierskiego pozwalającego oszacować wymagane pole powierzchni PCB. Wartość tej wielkości wyrażaną w cm2 wyznacza się jako iloraz 500 przez różnicę ΘJA i ΘJC. Zakładając, że ΘJC wynosi 10ºC/W rozmiar PCB w tym wypadku powinien wynosić co najmniej 5cm².
Efektywność analizy termicznej
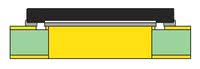
Rys. 3. Wykonanie przelotki termicznej w postaci warstwy miedzi bezpośrednio pod metalową wkładką na spodzie obudowy nie jest opłacalne
Niezależnie od precyzji, z jaką został opracowany model termiczny projektu PCB, dokładność wyników analizy cieplnej zależy przede wszystkim od danych wejściowych, głównie od informacji o parametrach poszczególnych komponentów (m.in. stratach mocy, wydzielanym cieple, dopuszczalnej temperaturze pracy).
Jeżeli dane te nie będą zgodne z rzeczywistością, wyniki analizy będą błędne, a zmiany w projekcie urządzenia wprowadzone na tej podstawie mogą okazać się niepotrzebne lub niewystarczające. Pierwszy przypadek jest skutkiem przyjęcia w analizie nadmiernie pesymistycznych założeń. Jest to niekorzystne z różnych względów.
Najczęściej okazuje się, że projekt urządzenia wykonanym ze zbyt dużą rezerwą jest nieekonomiczny, ponieważ zastosowano w nim zbyt drogie komponenty, przykładowo z materiałów o lepszych właściwościach termicznych albo wentylatory o większej niż wymagana wydajności chłodzenia lub wykorzystano całkiem zbędne dodatkowe elementy systemu chłodzenia.
Przeciwieństwem jest niedoszacowanie ilości ciepła wydzielanego przez elementy urządzenia lub ich wrażliwości na zmiany temperatury otoczenia. Wymaga też zwykle wprowadzenia poprawek już po zbudowaniu urządzenia. W takim wypadku najczęściej montuje się dodatkowe radiatory lub wentylatory.
Komplikuje to jednak konstrukcję, podwyższa koszty, a nawet może negatywnie wpłynąć na niezawodność urządzenia. Nie ma bowiem wówczas gwarancji, że mimo dodatkowego chłodzenia uda się uniknąć przegrzewania wrażliwszych podzespołów.
Wskazówki projektowe
Wyniki analizy termicznej stanowią podstawę do wprowadzenia odpowiednich modyfikacji w konstrukcji PCB. W zależności od specyfiki projektu można zastosować różne rozwiązania. Jednym ze sposobów jest zwiększenie efektywności oddawania ciepła przez nagrzewające się komponenty. Można to uzyskać m.in. przez zmniejszenie rezystancji termicznej złącze- otoczenie.
W przypadku wcześniej omawianego komponentu w obudowie QFN można to zrealizować na przykład, wykonując pod nim termiczne przelotki. Idealnym rozwiązaniem byłoby stworzenie przelotki w postaci warstwy miedzi bezpośrednio pod metalową wkładką na spodzie obudowy, jak na rysunku 3. Mimo że jest to wykonalne, taka konstrukcja nie jest opłacalna, stąd możliwości jej zastosowania są bardzo ograniczone.
W zamian przelotki termiczne realizuje się w postaci układu oddzielnych platerowanych przelotek jak na rysunku 4. Przy ich projektowaniu i wykonywaniu należy przestrzegać kilku zasad. Liczba i rozmiar przelotek powinny zależeć od możliwości ich realizacji w obrębie danej płytki.
Przyjmuje się jednak, że średnica każdej z nich nie powinna być mniejsza niż 0,25mm i nie większa niż 0,3mm, należy też zachować odpowiedni odstęp między nimi oraz od granicy obszaru przeznaczonego na ich realizację. Ten ostatni powinien zajmować taką powierzchnię jak metalowa wkładka na spodzie komponentu.
Istotny jest też sposób wypełnienia przelotek. Okazuje się, że w przypadku strat mocy poniżej 5W całkowite wypełnienie przelotek miedzią pozwala uzyskać tylko nieznacznie mniejszą rezystancję termiczną niż w wypadku przelotek jedynie wewnątrz platerowanych tych materiałem (rys. 5).
Kompromis
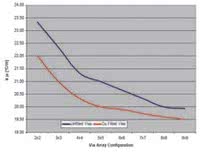
Rys. 5. Wpływ rozmiaru pola przelotek termicznych zamontowanych pod komponentem o rozmiarze 7×7 mm i stratach mocy 3W na ich rezystancję termiczną w przypadku przelotek wypełnionych miedzią i przelotek platerowanych
Realizacja niektórych rozwiązań konstrukcyjnych, których wprowadzenie jest uzasadnione ze względu na wyniki analizy termicznej, może się jednak okazać utrudniona. Dotyczy to na przykład kwestii rozmieszczenia komponentów PCB. W tym wypadku niejednokrotnie wymagany jest kompromis wynikający z konieczności przestrzegania równocześnie zasad elektrycznych.
Jedną z takich reguł jest wytyczna, zgodnie z którą poszczególne komponenty należy rozmieszczać możliwe jak najbliżej siebie, dzięki czemu zrealizować można krótkie ścieżki łączące ich wyprowadzenia. Jest to istotne ze względu na konieczność zapewnienia integralności sygnałów.
Przestrzeganie tej zasady jest jednak niepożądane, jeżeli uwzględni się rozkład ciepła wydzielanego przez te podzespoły. Rozmieszczenie wielu komponentów w bezpośrednim sąsiedztwie skutkuje bowiem skupieniem w tym miejscu wielu źródeł ciepła, co zawsze prowadzi do dalszego podwyższenia temperatury pozostałych komponentów w tym skupisku.
Dlatego niejednokrotnie przestrzeganie optymalnego rozkładu ścieżek na PCB może skutkować uszkodzeniem wrażliwszych komponentów, jeżeli kwestia wpływu wydzielanego ciepła zostanie całkiem pominięta. Innym przykładem jest zasada, zgodnie z którą komponenty, które nagrzewają się najmocniej, powinny być umieszczane możliwie najbliżej krawędzi płytki, tuż przy wlocie powietrza z wentylatora, tak aby można było im zapewnić jak najskuteczniejsze chłodzenie.
Może się to jednak okazać niepraktycznym rozwiązaniem z punktu widzenia rozmieszczenia ścieżek sygnałowych w przypadku, gdyby konieczne było umieszczenie blisko tej krawędzie komponentów, które należy połączyć z innymi, zamontowanymi w innej części PCB.
Kompatybilność elektromagnetyczna

Rys. 6. Duży radiator może być źródłem wielu problemów na etapie montażu urządzenia, a także później, w czasie jego eksploatacji
Zasady, których przestrzeganie gwarantuje zachowanie przez dane urządzenie kompatybilności elektromagnetycznej, również czasem mogą się wykluczać z wytycznymi zapewniającymi optymalny rozkład ciepła w obrębie PCB. Przykładem jest konstrukcja otworów wentylacyjnych lub perforowanej płytki, przez którą przekazywane jest powietrze chłodzące.
Zasady kompatybilności wymagają, aby każdy wlot wentylacyjny w obudowie miał możliwie najmniejszy stosunek powierzchni otwartej do powierzchni jednolitej. Z drugiej strony ograniczenie powierzchni otworów negatywnie wpływa na skuteczność chłodzenia - im jest ona mniejsza, tym bardziej rośnie rezystancja przepływu, co redukuje ilość powietrza przepływającego przez obudowę.
Innym przykładem jest wykorzystanie ekranów, które izolują od zaburzeń otoczenia komponenty. Z perspektywy analizy termicznej stanowią one dodatkowy problem, gdyż ograniczają drogę przepływu ciepła w procesie konwekcji. W efekcie większość ciepła wydzielanego przez komponent z braku możliwości rozproszenia do otoczenia wydziela się do płytki, nagrzewając ją, a przy okazji także sąsiadujące ścieżki i podzespoły.
Kolejnym kłopotliwym z punktu widzenia zasad kompatybilności EM komponentem systemów odprowadzania ciepła z urządzeń elektronicznych są radiatory. W pewnych warunkach element ten może zacząć pełnić rolę anteny, zwiększając emisję zaburzeń.
Naprężenia mechaniczne
Pod względem efektywności chłodzenia większy radiator, o dużej liczbie żeberek, lepiej spełnia swoją funkcję niż mniejszy komponent. Niestety wraz z rozmiarem rośnie też masa i powierzchnia zajmowana przez taki element. W efekcie czasem taki duży radiator może stać się znaczącą przeszkodą hamującą przepływ powietrza chłodzącego.
Oprócz tego zamontowanie radiatora o dużych rozmiarach w porównaniu do reszty elementów PCB może być trudne. Dodatkowo może on wówczas zacząć wywierać stosunkowo duży nacisk na element lub samą płytkę w miejscu, gdzie zostanie zainstalowany (rys. 6), powodując powstawanie naprężeń mechanicznych, a w efekcie zniekształceń i pęknięć.
Naprężenia mechaniczne mogą też wystąpić w przypadku, gdy projektując PCB, nie uwzględni się efektu rozszerzalności cieplnej niektórych materiałów, kierując się przy ich wyborze wyłącznie ich dużą przewodnością cieplną. Przykładem takiego materiału jest miedź, której przewodność termiczna wynosi około 400 W/mK.
Niestety charakteryzuje ją też duża wartość rozszerzalności cieplnej, dla porównania w przybliżeniu sześciokrotnie większa niż w przypadku krzemu. Może to powodować różne komplikacje, na przykład w realizacji techniki Through-Silicon Vias.
Monika Jaworowska