Do zrozumienia zalet nowego podejścia potrzebne jest zrozumienie podstawowych zasad montażu układów elektronicznych w trakcie ich produkcji. Można wyróżnić szereg małych i dużych kroków postępowania w tym procesie. W tabeli 1 zostały zgrupowane kolejne kroki w projektowaniu i produkcji płytek drukowanych oraz ich montażu.
Jak widać, przedstawione podstawowe czynności powierzchniowego montażu komponentów częściowo się pokrywają i zachodzą na siebie. W wykazie wymieniono też liczne czynności cząstkowe oraz ich sprawdzanie. Płytki drukowane o silnym zagęszczeniu wymagają zwykle wielu czynności obrazowania i metalizacji.
W tabeli pominięto sporo czynności montażowych i weryfikacyjnych rozlokowywania kulek pod układy BGA wraz z odprowadzaniem ciepła przy łączeniu ich z podłożem. Zaznajomieni z praktyką montażu układów na płytkach drukowanych zdają sobie sprawę z jego złożoności i uciążliwości. Trudności wniesione przez proces lutowania bezołowiowego wywołały wzrost zainteresowania odmiennymi technikami łączenia, pomijającymi lutowanie, często prostszymi i niekiedy dla nich alternatywnymi.
Przegląd technik montażu nielutowanego
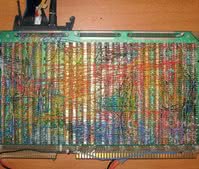
Rys. 1. Fotografia przedstawia prototypową płytkę, zmontowaną za pomocą techniki owijania (wire-wrap), niewymagającą lutowania. Ten sposób montażu był dawniej bardzo popularny
Historia montażu układów elektronicznych jest bardzo obszerna. Montaż nielutowany jest stosowany od ponad stu lat. Złącza wtyczkowo-gniazdkowe, służąc do dziś do połączeń pomiędzy płytkami, powszechnie były stosowane zwłaszcza do łączenia termicznie wrażliwych komponentów z płytką. Sposób ten jest i obecnie stosowany w przypadku mikroprocesorów.
Każdemu elektronikowi hobbyście jest znany prosty sposób ręcznego skręcania dwóch przewodów. Przed laty powstała zautomatyzowana przemysłowa technika owijania przewodem (wire wrapping) sztywnych bolców, niekiedy stosowana do dzisiaj (rys. 1). Inna metoda łączenia nielutowanego, używana przez kilka dekad, polegająca na wciskaniu szpilkowych styków w przewodzące otwory przelotowe w płytkach drukowanych, była stosowana przez wytwórców urządzeń telekomunikacyjnych i serwerów internetowych. Pozwalała unikać szkodliwej dla niektórych komponentów zbyt wysokiej temperatury lutowania. Opartą na technice owijania metodę zastosowano też do niezawodnego łączenia płytek drukowanych (rys. 2).
Technika bezpośredniego trwałego mechanicznego łączenia złotymi, aluminiowymi, a nawet miedzianymi przewodami wyprowadzeń układów scalonych z podłożem pakietu lub płytki drukowanej (tzw. bonding) była stosowana w używanym od lat 70. ubiegłego wieku systemie "chip na płytce" (COB).
Warte także wspomnienia są inne sposoby łączenia metalurgicznego z użyciem pasty spiekającej w przejściowej fazie łączenia i spawania. Spiekane metale są różne, a temperatura ich łączenia nie jest wysoka. Przejściowa płynna faza wiążąca jest jak gdyby połączeniem lutowania ze spawaniem, a metale są łączone ciśnieniowo-termicznie. Gdy zostanie osiągnięta temperatura łączenia, oba metale reagują natychmiastowo, a temperatura topnienia powstałego stopu jest wyższa od temperatur topnienia obu składników.
Ostatnią metodą łączenia jest spawanie, które może być dokonywane w różny sposób, na przykład laserowo lub rezystancyjnie. Metoda laserowa jest lepiej znana od tej drugiej. W procesie rezystancyjnym doprowadzenia są spawane krótkim przepływem prądu o dużym natężeniu i pod dużym naciskiem przy zastosowaniu topnika, podobnie jak przy lutowaniu. Jednak proces ten jest stosunkowo powolny.
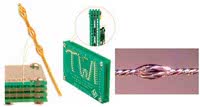
Rys. 2. Przykład połączeń pomiędzy płytkami drukowanymi za pomocą techniki skręcania przewodów (źródło: Medallion Technology)
Oprócz mechanicznych rozwiązań połączeniowych stosowane są techniki elektromechanicznych połączeń adhezyjnych. Istnieją trzy rodzaje tych technik: przewodzeniowe, anizotropowe i nieprzewodzeniowe. Pierwsza z nich opiera się na użyciu żywicy z domieszką materiału przewodzącego, zwykle srebra lub coraz częściej materiałów nanowęglowych.
W drugiej stosuje się materiał adhezyjny w postaci błony lub cieczy, nasyconej cząstkami przewodzącymi, umożliwiającymi przewodność elektryczną wzdłuż osi Z, ale nie osi X lub Y. W trzeciej użyty materiał nie przewodzi, stosuje się go dla sygnałów sprzężonych pojemnościowo albo gdy napięcie jest dostatecznie wysokie, aby tę izolację przebić. Czasem izolację tę przebija się mechanicznie. Najszersze zastosowanie mają dwie pierwsze metody.
Przewodzące materiały adhezyjne stosuje się w przypadku niskiej odporności termicznej komponentów, na przykład LED w plastikowych obudowach. Materiały takie są zwykle stosowane w urządzeniach z przełącznikami membranowymi i drukowanymi lub szablonowymi połączeniami tuszem srebrowym na niskotemperaturowych polimerach, na przykład poliestrach.
Innym rodzajem alternatywnego lutowania są anizotropowe spoiwa przewodzące. Są one powszechnie używane do łączenia wyświetlaczy ze sterownikami i przesyłania sygnałów w płaskich wyświetlaczach panelowych różnych rodzajów. Ich zaletą jest możliwość wykonywania niezbędnych w tych zastosowaniach niezawodnych połączeń o bardzo drobnej skali. Historia połączeń nielutowanych jest jak widać bogata i zróżnicowana.
Eliminacja lutowia przy projektowaniu
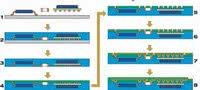
Rys. 3. Na proces Ockhama, bez lutowania, składają się następujące czynności. W pełni sprawdzone komponenty są umieszczane na nośniku (w tym przypadku trwałym). Układ zostaje zakapsułowany, odpowiednią metodą (np. laserem) jest tworzony dostęp do jego wyprowadzeń, układ jest nieelektrycznie metalizowany i formowane są połączenia. Nakładane zostają dodatkowa warstwa dielektryka i kolejne obwody (źródło: Verdant Electronics)
Z punktu widzenia wydajności i użyteczności omówione techniki unikania lutowania mają wiele zalet. Powstają także inne rozwiązania obchodzące się bez lutowania, z wyboru raczej niż z konieczności. Jednym z nich jest metoda nazwana procesem Ockhama dla uczczenia imienia XIII-wiecznego logika i filozofa, który za test skuteczności uznawał prostotę. Podstawą tego procesu jest odwrotna kolejność procesu łączenia.
Komponenty (czyli sprawdzone i wtopione w obudowy układy scalone oraz dyskretne i scalone elementy bierne, cewki, anteny, złącza itp.) są najpierw osadzane na podłożu, osłaniane, a następnie ze sobą łączone za pomocą zwykłej techniki obwodów drukowanych, nieryzykownego, dojrzałego i znanego procesu przemysłowego. Łączenie uprzednio rozmieszczonych komponentów dokonuje się przez nanoszenie na nie miedzianych ścieżek. Kolejne etapy procesu Ockhama są zilustrowane na rysunku 3.
Nowość tego sposobu polega na odwróceniu kolejności tworzenia układu. Połączenia elektroniczne następują po umiejscowieniu komponentów. Są one najpierw umieszczane na tymczasowym lub ostatecznym podłożu, a następnie łączone elektrycznie. W pierwszym przypadku podłożem może być usuwalna kleista błona, a w drugim stałe podłoże, do którego komponenty są trwale przyklejane.
Błona lub podłoże prowizorycznie, ale dokładnie, je unieruchamiają do momentu ostatecznego ich pokrycia. Dzięki temu sprawdzone i wtopione komponenty tworzą monolityczny i trwały zespół. Dostęp do jego poszczególnych elementów realizuje się od spodu przez usunięcie tymczasowej warstwy albo mechaniczną lub laserową obróbką podłoża.
Do wykonywania połączeń obecnie stosuje się odpowiednią technikę metalizacyjną, jak napylanie lub nieelektryczna metalizacja. Przewiduje się, że w przyszłości w użytkowanie wejdzie powszechna dzisiaj technika strumieniowego druku zmodyfikowanymi tuszami przewodzącymi. Można przewidzieć, że jej praktyczna elastyczność umożliwi szybkie dokonywanie przeróbek i korekt w trakcie projektowania i montażu układów prototypowych.
Dzięki nielutowanym procesom łączenia, jak powyżej opisany, urządzenia elektroniczne nie tylko będą tańsze, ale w procesie wytwarzania wykażą się wielu zaletami, jak odporność termiczna, hermetyczność, ekranowanie przed EMI, a także możliwością osadzania komponentów elektromechanicznych i optycznych i innych w podłożu.
Zalety montażu niskotemperaturowego
W montażu układ nie jest narażony na związane z lutowaniem bezołowiowym wysokie temperatury, zatem wyeliminowany jest problem poziomu odporności na wilgoć (MSL). (MSL jest ustaloną przez JEDEC miarą wywołanego lutowaniem ryzyka uszkodzenia komponentu wybuchowym odgazowaniem zawartej w nim wilgoci). Tradycyjne lutowanie bezołowiowe wymaga temperatury 220°C, a stopy SAC blisko 260°C. Przy takim wzroście temperatury ciśnienie par wody wzrasta więcej niż dwukrotnie.
Istotną zaletą nielutowanego montażu jest fakt, że powstałym układom można przypisać poziom MSL-1. Nie wymagają one zatem w normalnych warunkach ochrony przed wilgocią w trakcie składowania ani przestrzegania czasu jego trwania czy później konieczności wygrzewania. Ponadto proces ten umożliwia stosowanie komponentów niewytrzymujących temperatur lutowania bezołowiowego (aluminiowych kondensatorów elektrolitycznych, niektórych optoelektroników, złączy itp.). Inną potencjalną jego zaletą jest możliwość łatwego osadzania radiatorów, a nawet przewodów cieplnych bezpośrednio w podłożu jako integralnych elementów urządzenia.
Korzyści w projektowaniu układów

Rys. 4. Przedstawione są odwrócone działania produkcyjne, zgodne z procesem Ockhama, będące przygotowaniem do techniki nadruku. Po zakapsułowaniu i odsłonięciu doprowadzeń obwód tworzy się drukiem atramentami izolacyjnym i przewodzącym w ciągu kilku minut
Tak jak w przypadku standardowych płytek drukowanych, struktura połączeń pomiędzy komponentami musi zostać zaprojektowana i utworzona. Przy tym nowym podejściu znika wiele ograniczeń. Nie ma potrzeby tworzenia dużych pól kontaktowych na płytce drukowanej, niezbędnych do przylutowania podzespołów, co pozwala na uproszczenie ich trasowania. Dzięki temu ich rozmieszczenie może zostać zagęszczone, a liczba warstw płytki i liczba głębokich przelotek zmniejszona, ponieważ w razie potrzeby można przewidzieć specjalne struktury.
Proces bez lutowania także ułatwia zastosowanie sieci systemu zasilania (interconnected mesh power system, IMPS), opracowanego na Uniwersytecie Arkansas. Układy IMPS powstają na bazie siatki przewodów zasilania i uziemiania o trzykrotnej szerokości wybranej minimalnej szerokości przewodów sygnałowych w minimalnej odległości. Przewody sygnałowe są wtedy kierowane w siatce pomiędzy zwężonymi tam gdzie trzeba przewodami zasilania i uziemiania.
Przy projektowaniu struktur IMPS z myślą o wieloczipowych modułach scalonych, te rozwiązania dają się zastosować do połączeń wyższego rzędu. W firmie Hewlett Packard jest rozwijany podobny koncept architektury Power Mesh do płytek drukowanych z drugostronną warstwą metaliczną. Siatka nie jest nigdy przerywana ani odłączana.
Wszystkie ścieżki sygnałowe są liniami przesyłowymi współpłaszczyznowymi w stosunku do zasilania i masy, co zostaje zachowane, gdy sygnał przechodzi od punktu X do Y. Przesłuchy są bardzo słabe, ponieważ pomiędzy każdą parą ścieżek sygnałowych znajduje się masa zmiennoczęstotliwościowa. Wstępna siatka ustala dopuszczalne trasy sygnałów. Koncepcja ta jest idealna do rozmieszczania komponentów z użyciem wspólnej podziałki siatki, a do rozprowadzania ścieżek sygnałowych w kanałach może zostać użyty każdy router EDA.
Obowiązującą zasadą projektowania nadal jest utrzymywanie minimalnej odległości pomiędzy zasilaniem a masą, przez zwężenie szerokości ścieżek. Za pomocą tej metody projektowania można w porównaniu ze sposobami tradycyjnymi znacznie zredukować liczbę warstw, uzyskując obniżenie mierzalnych szumów i przesłuchów.
Na przykład nawet standardowe płytki 14-18-warstwowe z przelotkami dają się zredukować do 4-warstwowych, a 8-warstwowe do dwuwarstwowych. W połączeniu z opisanym powyżej procesem bez lutowania i z użyciem bezpośrednich połączeń HDI z wyprowadzeniami komponentów, kombinacja taka z powodzeniem może sprostać wymaganiom dla połączeń we/wy do 400 we/wy na cm². Proces nielutowania umożliwia wreszcie tworzenie struktur o wysokim zagęszczeniu, ponieważ komponenty mogą być umieszczane ciasno "na styk", a nawet nasuwane jeden na drugi.
Montaż w stosy
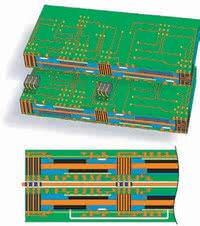
Rys. 5. Użycie odwrotnego procesu połączeń bez lutowania pozwala na tworzenie konstrukcji niemożliwych do uzyskania innym sposobem. Pokazana struktura wyróżnia się wieloma użytecznymi cechami, w tym wbudowaną techniką odprowadzania ciepła, prowadzenia krótkich połączeń i możliwością wprowadzania, mogących być w przyszłości potrzebnych, kanałów optycznych
Inną zaletą nielutowanych struktur, konstruowanych w sposób odwrotny, jest to, że podzespoły mogą być montowane w stosy i równocześnie łączone zarówno na brzegach, jak i w środku. Powstają w ten sposób pakiety silnie zagęszczone.
Całkiem realne są możliwości tworzenia struktur połączeń wzajemnych, o możliwościach superkomputera, w objętości jednometrowego, a nawet mniejszego sześcianu. Jest to możliwe dzięki znacznej redukcji ścieżek sygnałowych i zapewnieniu czystego zasilania.
Jest też nadzieja włączenia rozwiązań zarządzania ESD w urządzeniu, a nie wewnątrz układów scalonych. Takie podejście dodatkowo zredukuje zapotrzebowanie mocy, bo zmniejszone zostają zarówno wymagania we/wy, jak i rdzenia, zwłaszcza gdy będą zapewnione czyste ścieżki połączeń w całym systemie.
Jednakże gęstość energetyczna nie będzie zerowa, zatem zaletą jest istnienie integralnego ośrodka odprowadzania ciepła czy nawet przewodu cieplnego wbudowanego w urządzenie i stykającego się bezpośrednio z obudowami układów scalonych, a w przypadku pakietów flip-chip z bezpośrednio wybranym elementem odprowadzającym. Spodziewany wygląd takiego zestawu jest pokazany na rysunku 5.
Zakończenie
Techniki montażu bez lutowania od dawna były używane do łączenia urządzeń elektronicznych. Szkodliwe skutki temperaturowe procesu lutowniczego ciążą wspólnocie produkcyjnej, przyczyniając się do licznych defektów. Rodzi się przekonanie, że elektronika bez lutowania (SAFE, solder alloy free electronics), jak podany jako przykład proces Ockham, stanie się z biegiem czasu normą. Można się spodziewać, że zapewni zwiększenie niezawodności i obniżenie kosztów, a producenci obwodów drukowanych przystosują do tego wkrótce proces wytwarzania zgodnie z europejskimi ograniczeniami RoHS.
KKP