Klasyczny ekran LCD ma wbudowany moduł podświetlenia, który równomiernie rozprowadza światło z emiterów LED po całej powierzchni matrycy. Aby pełnił on swoją funkcję prawidłowo, musi dobrze przylegać do ekranu. W typowych konstrukcjach jest to wymaganie proste do spełnienia w produkcji, natomiast uzyskanie takiej samej funkcjonalności w przypadku wyświetlaczy elastycznych jest zdecydowanie trudniejsze.
Wyświetlacze AMOLED są pozbawione tej wady. Komórki OLED-owe znajdujące się na matrycy wyświetlacza stanowią źródło światła, dzięki czemu pomijany jest problem z przyleganiem modułu podświetlenia. Właśnie ta cecha technologii OLED sprawia, że możliwa jest produkcja wyświetlaczy elastycznych.
Najwięksi producenci wyświetlaczy (tacy, jak Samsung, AUO czy LG) nieustannie rozwijają i ulepszają tę właściwość, aby po opanowaniu produkcji wyświetlaczy zakrzywionych (curved) rozwinąć ofertę jednostek elastycznych (bendable), a docelowo także wyświetlaczy składanych (foldable).
Materiały wykorzystywane do produkcji wyświetlaczy elastycznych
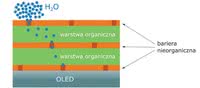
Rys. 2. Schemat poglądowy konstrukcji wielowarstwowej uszczelnienia matrycy organicznej przed wpływem wilgoci atmosferycznej w wyświetlaczu elastycznym OLED
W przypadku płaskich lub zakrzywionych AMOLED-ów podstawę wyświetlacza stanowi szkło, na którym znajduje się matryca OLED. Jest to konstrukcja prosta w produkcji, która dostatecznie zabezpiecza komórki OLED przed czynnikami zewnętrznymi.
Podstawę wyświetlaczy elastycznych stanowi plastik, na którym znajduje się matryca OLED. Niestety tutaj problematyczne staje się zapewnienie szczelności komórek AMOLED. Nie można dopuścić, aby powietrze atmosferyczne i wilgoć przedostały się do wyświetlacza, gdyż wtedy komórki ulegają szybkiej degradacji, znacznie skracając czas życia wyświetlacza.
Aby uchronić wyświetlacz przed działaniem czynników zewnętrznych, stosowana jest cienka warstwa pokrycia uszczelniająca matrycę AMOLED. Stanowi ona ochronę dla komórek i jest na tyle elastyczna, że umożliwia swobodną pracę wyświetlacza z dowolnym zgięciem. Wymagane jest, aby taka warstwa uszczelniająca miała WVTR (Water-vapour Transmission Rate - współczynnik przepuszczania pary wodnej) o wartości ~10-6 g/m² na dzień, który zapewni 5-letnią żywotność. Porównanie konstrukcji wyświetlacza AMOLED na podstawie szklanej i na podstawie plastikowej jest przedstawione na rysunku 1.
Dalszą poprawę żywotności uzyskuje się przez utworzenie warstwy uszczelniającej dzięki kilkukrotnemu naprzemiennemu nałożeniu na siebie warstw organicznych i nieorganicznych pokryć ochronnych w tzw. strukturze Vitexa (nazwa pochodzi od firmy, która przedstawiła i udoskonaliła tę metodę). Badania potwierdzają możliwość uzyskania WVTR na poziomie ~10-6 g/m² na dzień przy wykorzystaniu warstw tlenku glinu AL2O3 oraz poliakrylanu.
Warstwy nieorganiczne są barierą dla wilgoci, natomiast elastyczne warstwy organiczne oddzielają je od siebie i spajają całą strukturę w całość. Dzięki takiemu podejściu odległość pomiędzy otoczeniem a matrycą jest wydłużona i tym samym niepożądane czynniki środowiskowe zostają absorbowane przez film uszczelniający, jak na rysunku 2. Ta metoda umożliwia zredukowanie WVTR z poziomu ~10-3 g/m² do ~10-6 g/m² na dzień.
Struktura Vitexa, choć skuteczna, jest zarazem droga i trudna w produkcji. Z tego powodu starano się wypracować inne tańsze metody wytwarzania uszczelnienia. Jednym z rozwiązań jest zastosowanie HMDSO (Hexamethyldisiloxane). Potrafion przyjmować cechy i właściwości cienkiej powłoki (tzw. filmu) zarówno organicznego, jak i nieorganicznego, w zależności od stężenia tlenu podczas procesu osadzania warstw chemicznych z plazmy PECVD (Plasma-enhanced Chemicalvapor Deposition).
Związek HMDSO jest nie tylko tańsze w produkcji, ale też skutecznie chroni matrycę OLEDową przed szkodliwym działaniem powietrza. Co więcej, zachowując elastyczność, nie wpływa on w żaden sposób na parametry optyczne wyświetlacza. Ostatnie badania wykazują, że żywotność wyświetlacza może sięgać 500 godzin i więcej przy temperaturze 60°C i wilgotności względnej 90%.
Kiedy będą dostępne?
Technologia wytwarzania elastycznych OLED-ów jest rozwijana nie tylko przez największych producentów wyświetlaczy do aplikacji konsumenckich, ale również przez producentów rozwiązań przemysłowych, takich jak Winstar. Aktualnie producenci mają jedynie prototypy wyświetlaczy elastycznych (jak na fot. 3) o grubości zaledwie 0,2 mm. Winstar przewiduje rozpoczęcie masowej produkcji takich jednostek do końca 2017 r.
Można śmiało stwierdzić, że przyszłość wyświetlaczy należy do OLED-ów. Obecnie jesteśmy na etapie wyświetlaczy krzywych, ale wejście do produkcji monitorów elastycznych oraz zwijanych jest tylko kwestią czasu i z pewnością zaowocuje rozwojem wielu innowacyjnych wynalazków i urządzeń.
Piotr Ryżyński
Unisystem
www.unisystem.pl