Droga do Przemysłu 4.0 prowadzi przez IIoT
Według firmy Siemens rewolucję przemysłową można podzielić na trzy etapy. Pierwsza rewolucja przemysłowa polegała na zastosowaniu do produkcji mechanicznej napędu wodnego i parowego. Druga rozpoczęła się od wprowadzenia w tym celu energii elektrycznej. Trzecia nastała wraz z automatyzacją, gdy w fabrykach pojawiły się pierwsze programowalne sterowniki logiczne (PLC, Programmable Logic Controllers).
A teraz Siemens i inne duże firmy sądzą, że nadeszła kolejna rewolucja, określana jako Przemysł 4.0, gdzie wytwarzanie będzie procesem całkowicie zautomatyzowanym (rys. 1). Produkcja w Przemyśle 4.0 będzie się opierać na komunikowaniu się tworzonych wyrobów z maszynami linii montażowej, na której powstają.
W Niemczech wdrażanie koncepcji Przemysłu 4.0 służy już do poprawy produkcji oraz oprogramowania przemysłowego. Podobną inicjatywę, zwaną "Internetem Przemysłowym" (Industrial IoT) wdrożono w USA m.in. w zakładach General Electric.
Produkcja jest dobrze przez IIoT wspieraną dziedziną, ponieważ w jej trakcie jest gromadzona i przetwarzana wielka liczba danych. A to właśnie analiza i wizualizacja danych służy do optymalizacji działania oraz kosztów. Spoiwem tej nowej rewolucji w wytwarzaniu są inteligentne czujniki, sterowanie rozproszone i skomplikowane, oraz zaawansowane i bezpieczne oprogramowanie.
Różnice między IIoT a Przemysłem 4.0 nie są duże i wiele osób uważa te koncepcje za równoważne. Niemniej można pokusić się o opinię, że droga do Przemysłu 4.0 prowadzi przez IIoT, czyli że IIoT grupuje aplikacje liczniejsze i działające w mniejszej skali (czujnikowe), które stają się infrastrukturalną bazą dla większych aplikacji (systemów automatyki) związanych z Przemysłem 4.0. Niemniej granice są tu bardzo nieostre.
Co to właściwie jest IIoT?
IIoT jest tak definiowany przez ekspertów przemysłowych i analityków rynku:
- Przemysłowy Internet Rzeczy jest kolejną falą innowacji kształtujących sposób, w jaki maszyny się łączy i optymalizuje. Korzystając z czujników, zawansowanych analiz i inteligentnie podejmowanych decyzji IIoT głęboko zmieni sposób, w jaki aktywy w terenie łączą się i komunikują z przedsiębiorstwem.
- Największe naftowo-gazowe przedsiębiorstwa rozwijają infrastrukturę, w której czujniki, obróbka danych, zaawansowana analityka i automatyka są wykorzystywane do ułatwienia produkcji, redukcji kosztów działania, zapobiegania awariom i optymalizacji aktywów.
- Internet Przemysłowy, sieć połączonych inteligentnych maszyn, działających w zamierzony sposób, tak głęboko zmieni przedsiębiorstwa, jak IoT konsumencki zmienia nasze życie.
Inną definicją IIoT jest przedstawienie sieci przemysłowej w formie jak na pokazano na rysunku 2.
U dołu są urządzenia (systemy) procesowe. Mogą to być czujniki polowe, sterowniki, czy komputery, a wszystko to może obejmować (lub nie) bezpieczeństwo sprzętowe. Takie urządzenia końcowe muszą dysponować użytecznymi danymi, a są zwykle połączone z hubami komunikacyjnymi, bramami i przełącznikami, wysyłającymi dane w postaci Big Data do chmury (albo intranetu).
Gdy te dane już są "tam", można za pomocą różnych programów analitycznych i optymalizacyjnych wykorzystywać je do analizy i optymalizacji produkcji dla mnóstwa rodzajów zadań składających się na wytwarzanie i serwis i lepszego wykorzystywania zasobów.
Ale to nie wszystko. IIoT zapewnia, że te dane mogą zostać zintegrowane z oprogramowaniem produkcyjnym do ERP (Enterprise Resource Planning, do planowania zasobów przedsiębiorstwa) i CRM (Customer Relationship Management, obsługa relacji z odbiorcami). Działalność produkcyjna może nie tylko być wykorzystywana w skuteczniejszym planowaniu i ocenie kosztów procesów produkcyjnych, ale także w użytkowaniu informacji od odbiorców do dokonywaniu w czasie rzeczywistym zmian w liniach montażowych i parametrach procesów.
Dolne warstwy stosu na rysunku 2 wpływają na projektowanie sprzętu systemowego, a warstwy wyższe wpływają na rozwój i integrację oprogramowania.
Istotna rola czujników w IIoT
IIoT to nie tylko modne hasło. W wytwórniach zaczęto korzystać z sygnałów pochodzących z wielkiej liczby przyłączonych czujników, łącząc je z silnymi komputerami, co rozpoczęło tworzenie podstaw nowej generacji inteligentnych fabryk. Gdy już wszystkie dane przemysłowe (czyli pośrednio liczba "rzeczy", liczba "T" w IIoT), zostaną ostatecznie połączone online (czyli do Internetu, "I" w IIoT), kompleksowe oprogramowanie będzie mogło być używane do optymalizacji dokładnie wszystkiego.
Dobrym przykładem aktualnego IIoT jest najnowsza fabryka GE, powstała przed rokiem na w stanie Nowy Jork. Produkuje się tam zaawansowane akumulatory sodowo-niklowe, służące między innymi do zasilania stacji przekaźnikowych telefonii komórkowych. W tych zakładach umieszczono 10 000 czujników rozmieszczonych na 17 000 m2 powierzchni produkcyjnej.
Wszystkie te czujniki są przyłączone do bardzo szybkiej wewnętrznej sieci Ethernet i monitorują one procesy decydujące, które partie proszku zostaną użyte do formowania ceramicznych rdzeni ogniw, jaka jest temperatura ich spiekania, ile energii potrzeba do utworzenia jednego akumulatora, a nawet, jakie jest lokalne ciśnienie atmosferyczne. Pracownicy z rozmieszczonych w fabryce węzłów komunikacyjnych z Wi-Fi mogą wszystkie te dane pobierać na tablety i na bieżąco analizować.
Także Airbus z centralą w Tuluzie we Francji poinformował o znacznym zaawansowaniu IIoT w mającej powstać "Fabryce Przyszłości". Airbus pokazał znakowanie podzespołów samolotu, a także narzędzi, etykietami RFID, dającymi się odczytywać z odległości do 100 m za pośrednictwem specjalnych okularów (podobnych do okularów Google Glass z wyświetlaczem), pozwalających śledzić i obserwować proces produkcyjny w czasie rzeczywistym. Według Airbusa ta technika wizualizacji została już wprowadzona do linii montażowych A330 i A350 w Tuluzie oraz montażu ich skrzydeł w Wielkiej Brytanii.
Chociaż, jak się obecnie wydaje, proces ten w Airbusie ogranicza się do cyfrowego śledzenia i monitorowania etykiet RFID w celu poprawy sprawności działania produkcji, idea ta może zostać rozszerzona również na inne rodzaje analiz.
Czy IIoT jest nam potrzebne?
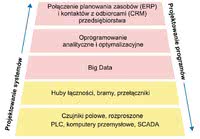
Rys. 3. Korzyści z IIoT. Wszystkie dane fabryk i procesów są online (w chmurze), więc analiza programowa jest pomocna do optymalizacji zasobów i procesów, a także zadań
Trzeba jasno przedstawić, dlaczego wszyscy dążą do realizacji IIoT. Narzuca się odpowiedź, że jest to optymalizowanie systemów wraz z wszystkimi korzyściami, jakie ta optymalizacja przynosi. Korzyści z IIoT można podzielić na trzy grupy: aktywa, proces i optymalizacja zadań, w tej właśnie kolejności. Łatwiej jest optymalizować silnik wiertarki niż cały proces wiercenia, a ten z kolei łatwiej niż optymalizować liczne linie produkcyjne dużego przedsiębiorstwa. A optymalizacja tego wszystkiego jest głównym celem Przemysłowego IoT (rys. 3).
Optymalizacja aktywów
Na początku jest pierwszy stopień analizy i interakcji. Dane są pobierane z czujnika, na przykład z czujnika turbiny wiatrowej, kodera silnika, albo sygnalizatora drgań. Są one przetwarzane lokalnie, aby operatorzy rozumieli, jak dobrać parametry dla najwyższej sprawności albo wcześnie zasygnalizować możliwość awarii.
Optymalizacja procesów
Miejscem drugiego stopnia analizy jest centrum sterowania. Tu są gromadzone dane z czujników zamontowanych w urządzeniach produkcyjnych, czy licznych liniach montażowych, umożliwiając podejmowanie przemyślanych decyzji, mających pozytywny wpływ na sprawność poszczególnych procesów i całej fabryki. Na przykład w sterowni na podstawie dokładniejszych danych z czujników można decydować o tym, kiedy urządzenia mogą zostać wprowadzone w stan jałowy, czy uśpione. Dzięki temu polepsza się eksploatacja urządzeń, a zużycie energii jest obniżane.
Optymalizacja zadań
Wspólnym mianownikiem tych rozważań jest zwiększanie liczby danych i przemyślane ich użycie. Dobrze wiadomo, jak dane mogą pozytywnie wpływać na użytkowanie zasobów i funkcjonowanie procesów. Ale IIoT nie tylko sugeruje zwiększenie liczby zbieranych danych i analizę dwóch pierwszych stopni. Zapewnia zintegrowanie danych procesowych z danymi przedsiębiorstwa, umożliwiając w ten sposób podejmowanie rzeczywiście inteligentniejszych decyzji, jakich dotąd podejmować nie się dawało.
Można wziąć za przykład linię montażową, którą można teraz zaprogramować do produkowania liczniejszych produktów na nowy rynek, albo do pomijania wyrobów, na które popyt maleje. Nawet powiązanie danych operacyjnych z finansowymi może dać lepszy ze strony księgowości wgląd w działanie przedsiębiorstwa.
IIoT ciągle jeszcze jest w powijakach i nie ma znormalizowanej dominującej platformy. Jest to faza "dzikiego zachodu" w IIoT i teraz jest właściwy czas, aby pokierować rozwojem standardu tej platformy. I to właśnie w przedsiębiorstwach z branży automatyki się odbywa.
Firmy z branży automatyki przemysłowej oferują urządzenia generujące wszystkie rodzaje danych przemysłowych i mają najwięcej doświadczenia w ich interpretacji. Muszą tylko opracować oprogramowanie zdolne do ich przetwarzania, analizy i prezentacji. Te przedsiębiorstwa są najlepiej przygotowane do automatyzacji przemysłu i są gotowe do przejęcia dominacji w powstającym IIoT.
IIoT pobudza wymagania systemów
W rozpowszechnianiu czujników i rozproszonego systemu przetwarzania istotną rolę grają dwa kreowane przez IIoT kluczowe trendy systemowe:
- rozprzestrzeniające się korzystanie z czujników. Koszt czujników i ich interfejsów stale się zmniejsza, co umożliwia śledzenie coraz większej liczby zmiennych oraz liczby różnych rodzajów danych.
- system rozproszonego przetwarzania. Umieszczanie PLC (Process Loop Control, sterowników pętli procesowych) bliżej maszyn, które kontrolują, eliminuje zatory oraz usprawnia wydajność i elastyczność produkcji.
Czujniki są wszędzie
Pojawiają się raporty oceniające wzrost rynku czujników w kontekście IoT. Na przykład BCC Research przedstawia globalny rynek czujników w różnych aplikacjach, takich jak bioczujniki, czujniki chemiczne, wizyjne, przepływów, czy poziomu. Inna firma, Emerson, przedstawia szeroki wachlarz terenowych czujników procesorowych. Przykłady to m.in.:
- "Rynek czujników ma wartość około 80 mld USD i oczekuje się, że w 2015 wzrośnie do 95,3 mld USD. Ocenia się, że w 2020 osiągnie poziom 154,3 mld USD przy rocznym wzroście 10,1% od 2015 do 2020 roku, wg raportu BCC Research.
- Oczekuje się, że rozprzestrzeniające się korzystanie z czujników podwoi obecną wartość 16 mld USD rynku pomiarów w nowy sposób wspomagając produkcję urządzeń i podnosząc bezpieczeństwo, niezawodność i sprawność energetyczną, wg Emerson Process Management.
Analitycy w różny sposób oceniają wzrost rynku czujników. Jasne jest jednak, że wzrasta zapotrzebowanie na dane analityczne, jak również na sensory, które je gromadzą. Ocenia się, że roczny wzrost szerokiego rynku tych produktów, zwłaszcza w wersjach przemysłowych, będzie dwucyfrowy.
Ukute przez Emersona określenie "rozpowszechnianie się korzystania z czujników" sugeruje, że znajdą się one wszędzie. Oznacza to także, że czujniki umożliwiają, lub umożliwią wkrótce, fabrykom, rafineriom, wytwórniom chemicznym, oraz innym zakładom przemysłowym, uzyskiwanie rosnącej liczby danych z monitorowanych procesów. Ich gromadzenie poszerza wgląd w ich działania, które stają się bardziej bezpieczne, niezawodne i opłacalne.
Ubocznym produktem niezwykłego wzrostu zapotrzebowania na czujniki jest oczekiwanie, że powinny one dostarczać więcej informacji niż prosty sygnał włącz/wyłącz. Zarządzanie w przemyśle wymaga danych operacyjnych w czasie rzeczywistym... a to zmienia trendy projektowe poziomu systemowego.
Wyłania się standard połączeń IO
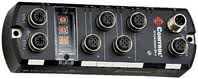
Rys. 4. Brama IO-Link Master firmy Comtrol jest interfejsem pomiędzy IO-Link a protokołami EtherNet/IP oraz Modbus TCP
W przemyśle rozwijają się standardy dla cyfrowych łączy komunikacyjnych niezbędnych do zapewnienia łączności. Taką przykładową otwartą i relatywnie tanią normą szeregowej łączności punkt-punkt, opartą na normie IEC 61131-9 jest protokół IO-Link. Stosuje się go do komunikacji pomiędzy PLC a umieszczonymi w dowolnym miejscu czujnikami, albo sterownikami. Ten protokół typu punkt-punkt opiera się na połączeniu 3-przewodowym. Jest jakby rodzajem interfejsu analogicznego do USB w wersji przemysłowej dla czujników, zapewniającym prostą instalację i użycie, nadając się do przesyłania danych z inteligentnych czujników.
Użycie protokołu IO-Link rośnie gwałtownie wraz ze wzrostem liczby takich sensorów. Quest TechnoMarketing Survey dla niemal dwustu przedsiębiorstw produkujących maszyny podaje, że do 2016 roku 47% producentów maszyn zamierza używać do komunikacji w omawianym zakresie znormalizowanego protokołów o takich właściwościach!
Oczywiście nie wszystkie czujniki łączy się bezpośrednio ze sterownikami PLC i komputerami. Komunikacja dotyczy setek tysięcy czujników, szeroko rozmieszczonych w fabryce, a także na zewnątrz. Do łączności z tak zróżnicowanymi układami czujników wykorzystywane są też inne urządzenia infrastrukturalne jak bramy, huby i punkty dostępowe.
Na rysunku 4 pokazano IO-Link Master, bramkę łączącą urządzenia standardu IO-Link z sieciami bazującymi na protokołach TCP EtherNet/IP i Modbus. Taki sprzęt upraszcza budowę sieci, a czas opracowywania systemu i jego instalacji ulega skróceniu.
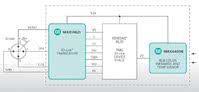
Rys. 5. Najmniejszy przemysłowy czujnik światła IO-Link zawiera sześć czujników: światła otoczenia (białego), światła czerwonego, zielonego, niebieskiego, podczerwieni oraz temperatury. Posługuje się układem transceivera IO-Link firmy Maxim, zawierającego liniowe stabilizatory 3,3 i 5 V, konfigurowalne wyjścia (przeciwsobne, pnp lub npn), ochronę przed odwróceniem polaryzacji i przed zwarciami, a także rozbudowane monitorowanie uszkodzeń. Wszystko to mieści się w małej obudowie WLP 2,5x2,5 mm. Czujnik zawiera także programowalną pamięć flash on-chip 64 kB i pamięć danych Flash on-chip 4 kB. Działa poczynając od 1,8 V
Współczesne czujniki przemysłowe stają się też mniejsze. Rysunek 5 pokazuje uważany przez nas za najmniejszy na świecie czujnik IO-Link światła otaczającego. Wykrywa on wartość koloru, którą przesyła przez łącze cyfrowe. Jego rozmiar jest porównywalny z wielkością spinacza do papieru.
W tym rozwiązaniu czujnik światła jest złożony z sześciu czujników, każdy z własnym wzmacniaczem PGA i z 14-bitowym ADC w miniaturowej obudowie OTDFN 2×2 mm. Systemem tym steruje ultra niskiej mocy mikrokontroler Renesasa, o poborze prądu 66 mA/MHz. Wszystkie komponenty tego czujnika z wyjściem w standardzie IO-Link zostały dobrane starannie i spełniają ostre wymagania przemysłowe w zakresie warunków środowiskowych.
Sterowanie rozłożone z czujnikami bezprzewodowymi
Projektowanie systemu szeroko rozmieszczonymi czujnikami bezprzewodowymi w obszarze IIoT napotyka na wiele trudności, związanych z sprzecznymi w stosunku do siebie normami, trudnościami we współdziałaniu urządzeń, bezpieczeństwem urządzeń przemysłowych, dostępnością pasm częstotliwości do komunikacji bezprzewodowej i koniecznością ochrony oprogramowania przed zagrożeniami.
Obecnie czujniki bezprzewodowe zajmują nikłą część rynku przemysłowego. Technika ta ciągle jest w znacznym stopniu skoncentrowana przez duże firmy z branży automatyki, które produkują przetwarzające dane sensory dla przemysłu naft owego, gazowego i wydobywczego. Przystosowanie czujników bezprzewodowych na większym obszarze automatyzacji przemysłu rozwinie się zapewne, jeśli zostaną pokonane problemy sterowania rozłożonego. Wiadomo, że nie wszystkie normy łączności bezprzewodowej są ze sobą zgodne. Może to doprowadzić do nowej wojny standardów Fieldbus/przemysłowy Ethernet, o utworzenie jednej wspólnej normy.
Sterowanie rozłożone z MicroPLC

Rys. 6. 32-kanałowy moduł wej/wyj PLC zawiera zespół wejściowego serializera cyfrowego 8 do 1 (MAX 31911) ze scalonym izolatorem cyfrowym (MAX14932) zmniejszający liczbę elementów o 70%, a rozmiary o 63%
IIoT wymaga lokalnego sterowania rozłożonego. Wobec liczby czujników w fabryce/procesie, wiązanie każdego z nich z centralnym komputerem lub sterownikiem PLC nie jest wykonalne. Zatem wiele rozłożonych mikroPLC umieszcza się bliżej kontrolowanych linii i sterują one każdym z podzespołów. Stąd się bierze potrzeba silnych, ale bardzo małych i sprawnych energetycznie systemów sterowania.
Największym problemem współczesnych sterowników kierowanych pod rynek IoT, z którego mało kto zdaje sobie sprawę, jest optymalne wykorzystywanie przestrzeni na płytce drukowanej. Większość projektantów ciągle wierzy, że technologia cyfrowa zapewnia najlepszą oszczędność miejsca na płytce. Ale cyfrowe chipy nie zajmują zwykle urządzeniach automatyki nie więcej niż 15 do 20% miejsca.
Elementy analogowe zajmują aż 85% powierzchni płytki drukowanej, ale nie dorównują w skali chipom cyfrowym. Zatem dla oszczędzania powierzchni płytek potrzebny jest wyższy poziom integracji elementów analogowych przy zachowaniu wymaganej funkcjonalności. Jednym ze sposobów osiągnięcia tego jest zastosowanie scalonych elementów analogowych zamiast bardzo czasem licznych komponentów dyskretnych. Uzyskuje się dzięki temu zmniejszenie powierzchni, zmniejszenie poboru mocy i poprawę niezawodności.
Przykład? Moduły we-wy tworzą podstawowe połączenia pomiędzy sterownikami a niezliczonymi czujnikami i układami wykonawczymi, rozmieszczonymi w zakładowych sieciach IIoT nowej generacji. Gdy wytwórcy dodadzą więcej czujników na obszarze fabryki, projektanci urządzeń będą musieli zwiększyć gęstość upakowania i jeszcze bardziej zmniejszyć płytki oraz wykorzystywać lepsze, efektywniejsze chipy po to, aby te sygnały podłączyć.
Obecnie wielokanałowe serializery, jak MAX31911, mogą przekazywać, kondycjonować i serializować 24-woltowe sygnały cyfrowe czujników i przełączników do kompatybilnego z CMOS poziomu 5 V, wymaganego przez sterowniki PLC. Takie rozwiązanie redukuje liczbę osobnych kanałów wejściowych i prowadzi do ogromnych oszczędności rozpraszanej mocy, liczby elementów i powierzchni całkowitej płytek drukowanych.
Ocenia się, że w 32-kanałowym module z wejściem cyfrowym takie nowoczesne chipy obniżają liczbę komponentów o 70%, a całkowite rozmiary o 63% (rys. 6).
Zakończenie
Dwa kluczowe wymagania systemowe nowej generacji IIoT można zreasumować jako:
- Rozpowszechnienie mniejszych, inteligentnych i lepiej połączonych czujników. Wymaganie to prowadzi do rozwoju bezprzewodowych protokołów komunikacyjnych, a także rozpowszechnienia bramek zbierających obszerne dane licznych czujników bazujących na komunikacji Fieldbus i przemysłowym Ethernecie.
- Rozproszona kontrola produkcyjnych linii montażowych pozwala na mało zwłoczną elastyczną kontrolę systemową. Prowadzi to do zwiększenia gęstości we-wy, umieszczania kompaktowych (lub mikro) PLC bliżej kontrolowanej linii produkcyjnej. Systemy te wiążą się ze specyficznymi trudnościami w projektowaniu, związanymi z współczynnikiem kształtu, odprowadzaniem ciepła i scalaniem komponentów o sygnałach analogowych i mieszanych. Te systemowe potrzeby wymagają innowacji zarówno na poziomie urządzeń (IC) jak i w architektury. Nowe takie systemy są podstawą dla zrealizowania obietnic IIoT.