Korozja warstw metalicznych w obwodach drukowanych staje się coraz większym problemem producentów elektroniki. Jej występowaniu sprzyja m.in. duża różnorodność metali używanych do budowy urządzeń elektronicznych oraz postępująca miniaturyzacja. To ostatnie sprawia, że komponenty obwodów drukowanych są coraz mniejsze.
W rezultacie nawet minimalny ubytek materiału w wyniku korozji może być na tyle duży w stosunku do wymiarów elementu, na przykład szerokości ścieżki sygnałowej, że uniemożliwi jego prawidłowe działanie - na przykład zablokuje przepływ prądu. Zwiększa się też gęstość upakowania PCB. Przez to ich komponenty są umieszczane coraz bliżej siebie, w rezultacie czego silniej na siebie oddziałują.
Ponieważ czynniki środowiskowe, przede wszystkim wahania temperatury, duża wilgotność powietrza oraz zanieczyszczenia przyspieszają korozję, nie powinno się elektroniki używać w takich warunkach. Niestety w niektórych zastosowaniach, na przykład w elektronice użytkowej oraz w przemyśle czynniki takie występują często, a na dodatek zwykle są całkowicie nieprzewidywalne.
Dlatego celem producentów powinno być przygotowanie komponentów urządzenia do bezawaryjnej pracy bez względu na warunki otoczenia. W związku z dużą konkurencją na tym rynku gwarancja niezawodności pozwala się wyróżnić na tle innych dostawców.
Korozja chemiczna
Korozja chemiczna to zjawisko znane z życia codziennego. Powszechnie wiadomo, jakie są jego skutki, a intuicyjnie jako czynnik ją przyspieszający każdy wskaże wilgoć. Potrzebne są też gazy korozyjne. Te, które powodują to zjawisko w przypadku metali najczęściej używanych do konstrukcji PCB (miedzi, srebra, aluminium), to m.in. gazy kwasotwórcze, takie jak różne związki siarki i chloru, tlenki azotu, fluorowodór oraz amoniak (szczególnie miedź jest podatna na korozję pod wpływem tej substancji) oraz utleniacze (na przykład ozon).
Nawet niewielka ilość wymienionych gazów o stężeniu na poziomie niewyczuwalnym lub nieszkodliwym dla człowieka może powodować korozję komponentów elektronicznych. W wyniku reakcji chemicznej powstają wówczas nowe związki. Na przykład produktem reakcji żelaza z wodą lub wilgotnym powietrzem są różne tlenki oraz wodorotlenki, czyli rdza.
Z kolei na siarkowodór wrażliwe jest m.in. srebro. Pod wpływem tego gazu na jego powierzchni formują się kryształki siarczku srebra (fot. 1). Zjawisko to występuje nawet przy bardzo małych stężeniach tego gazu (poniżej 50 ppb), znacznie poniżej poziomu stężenia siarkowodoru, który człowiek może wyczuć węchem.
Samozahamowanie i korozja pełzająca
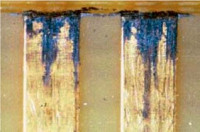
Fot. 2. Korozja może się rozpocząć na niezabezpieczonym brzegu platerowanego styku i stopniowo przenieść się na całą jego powierzchnię
Szybkość korozji chemicznej niezabezpieczonych metali zależy od wielu czynników. Można je podzielić na kilka grup. Do pierwszej zalicza się właściwości metalu - na przykład jego chropowatość oraz cechy podłoża - na przykład rodzaj jego struktury oraz stopień absorpcji wilgoci. Wpływ mają również parametry środowiskowe (temperatura, wilgotność).
Trzecią grupą czynników są właściwości gazów korozyjnych, tzn. ich rodzaj oraz na przykład stężenie. Na szybkość, z jaką postępuje degradacja struktury metalu, wpływają również właściwości produktu korozji. Jeżeli jest to materiał nierozpuszczalny, który formuje na powierzchni metalu nieprzepuszczalną oraz trwałą powłokę izolującą, korozja może ulec samozahamowaniu.
Dzieje się tak, gdy czynniki korozyjne nie reagują z produktami wcześniejszej reakcji. W ten sposób przebiega przykładowo proces utleniania aluminium, w wyniku którego na powierzchni metalu tworzy się cienka warstwa ochronna z tlenku. Jeżeli z kolei produkty korozji są rozpuszczalne lub mają postać porowatej powłoki, zjawisko to przebiega bez przeszkód do momentu, gdy osiągnięte zostaną granice materiału i reakcje chemicznie nie będą mogły dalej zachodzić. Przykładem jest proces rdzewienia żelaza.
Ponieważ produkty reakcji mają w tym przypadku strukturę inną niż metal bazowy, tworzą porowatą oraz słabo związaną z podłożem powłokę. Nie chroni ona zatem żelaza przed korozją jego kolejnych warstw oraz powierzchni dookoła. Zachodzi wówczas tzw. korozja pełzająca. Przykładowo może się ona rozpocząć na odsłoniętym brzegu platerowanego styku i stopniowo przenieść się na całą jego powierzchnię, zwiększając rezystancję kontaktu (fot. 2).
Niedoskonałości powłok ochronnych
Korozja może się też rozwinąć, jeżeli w powłoce platerowanej występują niedoskonałości. Są to przykładowo pory, które odsłaniają powierzchnię metalu. Stopień porowatości zależy m.in. od grubości powłoki, technologii jej nanoszenia, chropowatości metalu bazowego oraz stopnia jego czystości - zabrudzenia na powierzchni sprzyjają bowiem powstawaniu porów w powłoce.
Im grubsza jest powłoka, tym mniejsze jest prawdopodobieństwo, że w związku z jej porowatością zostanie odsłonięty metal. W przypadku bardzo cienkich powłok możliwe jest jednak, że zanieczyszczenia korozyjne będą miały bezpośredni kontakt z materiałem bazowym przez większą liczbę porów.
Jeżeli korozja metalu rozwinie się tą drogą, może pozostać przez jakiś czas niewidoczna. Produkty reakcji mogą też, podobnie jak w przypadku korozji pełzającej, rozprzestrzenić się na całej powierzchni metalu (fot. 3).
Elektromigracja
W obwodach drukowanych problemem jest także elektrochemiczny proces, tzw. elektromigracja. Zachodzi on w przypadku metali o różnych potencjałach umieszczonych na izolacyjnym podłożu, między którymi występuje warstwa wody. Sytuacja taka ma miejsce, jeżeli na przykład na powierzchni PCB między dwoma ścieżkami lub wyprowadzeniami układu scalonego uformuje się kropla lub warstwa wilgoci.
Tworzy się wówczas mikroogniwo galwaniczne. Jony metalu z anody przemieszczają się w kierunku katody, z czasem osiadając na tej elektrodzie. W miarę jak się nawarstwiają, odległość między metalami maleje. Ostatecznie tworzą się struktury, które łączą obie elektrody (fot. 4). Dochodzi wówczas do zwarcia. Przeważnie efekt ten zachodzi powierzchniowo, jednak pionowa migracja również może wystąpić, jeżeli wilgoć wniknie w głąb porów w materiale.
Co wpływa na elektromigrację?
Zjawisko elektromigracji nasila się przy wzroście różnicy potencjałów. Zwarcie elektrod nastąpi też szybciej przy mniejszej odległości między nimi. Ilość wilgoci wymaganej do zaistnienia tego zjawiska jest wciąż przedmiotem badań. Ogólnie to, czy wystarczy tylko kilka, czy może kilkaset monowarstw wody, zależy m.in. od struktury oraz porowatości powierzchni.
Znaczenie ma również stopień absorpcji wody przez podłoże. Przykładowo laminaty z żywicy fenolowej charakteryzują się większą higroskopijnością niż podłoża ceramiczne, co sprzyja elektromigracji. Struktury zwierające elektrody formują się też łatwiej, jeżeli powierzchnia laminatu jest chropowata. Metalem najbardziej podatnym na migrację jonów jest srebro.
Miedź, cynk oraz ołów z kolei wymagają bardziej niesprzyjających warunków, by zjawisko to zaszło. Natomiast w przypadku takich materiałów jak żelazo, nikiel oraz cyna elektromigracja praktycznie nie występuje. Wynika to z ich małej rozpuszczalności w wodzie. Zjawisko to nie zachodzi też w wypadku złota, platyny oraz palladu. Dlatego z materiałów tych wykonuje się powłoki zabezpieczające elementy wykonane ze srebra.
Zanieczyszczenia
Zjawisku elektromigacji sprzyja obecność zanieczyszczeń, zwłaszcza jonowych, która gromadzą się na powierzchni PCB. Pochodzą one z różnych źródeł i nawarstwiają się stopniowo podczas kolejnych etapów produkcji oraz obróbki obwodów drukowanych, w tym podczas montażu komponentów, ich lutowania oraz czyszczenia.
Są to przykładowo pozostałości chemikaliów, m.in. topników, środków do trawienia płytek oraz tych używanych w procesie galwanizacji. Oprócz tego na powierzchni PCB pozostawiane są tłuste ślady palców, resztki kosmetyków (kremów, mydeł), wytracają się osady soli z potu, przywierają fragmenty naskórka, tkanin, na przykład rękawic, a także okruchy, kurz oraz pył.
Źródłem zanieczyszczeń PCB jest także zjawisko tzw. korozji ściernej. Problem ten dotyczy zwłaszcza złączy i wszystkich tych komponentów, których elementy się stykają. W czasie wibracji o małej amplitudzie przemieszczają się one względem siebie, a w wyniku tego ruchu ściera się ich powłoka ochronna.
Jeżeli odsłonięta powierzchnia zacznie reagować z otoczeniem, utworzy się na niej nowa warstwa. Podczas kolejnych wstrząsów zostanie ona ponownie zniszczona. Jeżeli sytuacja ta powtórzy się wielokrotnie, wytworzyć się może duża ilość okruchów.
Zapobieganie korozji PCB
Aby ograniczyć ilość zanieczyszczeń, które zbierają się na powierzchni PCB, należy przestrzegać pewnych zasad na etapie montażu, inspekcji i przechowywania płytek. Przykładem jest zakaz wnoszenia jedzenia do pomieszczeń produkcyjnych oraz używania kosmetyków do rąk. Trzeba także dbać o czystość rękawiczek oraz regularnie wymieniać te zużyte.
Ponadto warto stosować lakiernicze powłoki ochronne hamujące rozwój korozji oraz uszczelnienia zapobiegające wnikaniu zanieczyszczeń do wnętrza komponentu lub części PCB. Ważne jest też, aby mieć pewność, że materiały, z jakich wykonano obudowy komponentów obwodu, nie zawierają siarki (sprzyja ona korozji miedzi, cyny, niklu oraz srebra).
Jeżeli płytki na etapie na przykład montażu nie są w danym momencie używane należy je schować do oryginalnego opakowania. Jeżeli będą w ten sposób przechowywane przez dłuższy czas, należy to opakowanie zamknąć próżniowo. By z kolei uniknąć korozji ściernej, najlepiej używać złączy oraz styków wykonanych z materiałów o jak najwyższej jakości, na przykład miedź pokrytą cyną zastąpić złotem.
Tańszą alternatywą jest używanie komponentów, w konstrukcji których wykorzystano rozwiązania zwiększające ich mechaniczną stabilność. Korozja rozwija się też szybciej przy dużej wilgotności. By ją zmniejszyć, warto stosować różnego typu osuszacze powietrza. Niekorzystne są również gwałtowne zmiany temperatury.
Takie warunki sprzyjają bowiem skraplaniu się wilgoci z powietrza na powierzchni PCB. Jeżeli takie czynniki mogą wystąpić (na przykład w centrach danych, w których w jednym miejscu zgromadzona jest duża ilość sprzętu lub w przemyśle), parametry środowiskowe należy monitorować. Mierzyć trzeba nie tylko temperaturę i wilgotność, ale również stężenie gazów korozyjnych.
Monika Jaworowska