Przełączniki i przyciski to grupa prostych i nieskomplikowanych elementów, jeśli chodzi o zasadę działania, które konstruktorzy traktują jako coś oczywistego, rzadko interesując się budową i właściwościami. Ale szczęśliwie coraz więcej osób przywiązuje wagę do jakości wykonania tych podzespołów.
To samo dotyczy estetyki, szczegółów, jak również oferty dodatkowych akcesoriów montażowych i dostępnych opcji wykonania. Na rynku elementów przełączających sporo się zmienia, zarówno od strony technologii, jak i biznesu, dlatego po blisko trzech latach przerwy powracamy w ramach raportu "Elektronika" do tej tematyki, analizując zmiany, jakie zaszły w tym okresie i przyglądając się aktualnym zjawiskom.
Technologia dotykowa zmienia rynek
Już od ponad pięciu lat na rynku dostępne są rozwiązania technologii dotykowych, które zastępują elementy elektromechaniczne i pozwalają na wyeliminowanie najbardziej dotkliwych ich wad - ograniczonej trwałości i odporności na wpływ środowiska. Początkowo elementy dotykowe pojawiły się w elektronice konsumenckiej jako dotykowe ekrany rezystancyjne nakładane na wyświetlacze. Niemniej wówczas nie nastąpił jeszcze przełom, bo były to technologie rezystancyjne, też pełne wad i ograniczeń.
Zmianę przyniosło opanowanie technologii dotyku pojemnościowego, która nie bazuje na elementach i materiałach o ograniczonej trwałości i pozwala na umieszczenie sensora dotykowego nawet za grubą warstwą ochronną, na przykład za kilkumilimetrowej grubości taflą szkła lub poliwęglanu. Co więcej, sensory dotykowe nie są związane tylko z wyświetlaczami graficznymi, za ich pomocą można tworzyć punktowe przyciski na płytach czołowych, suwaki regulacyjne złożone z wielu małych punktów dotykowych, czyli także w postaci rozwiązań dyskretnych jak klasyczne przełączniki.
Dotykowy przycisk pojemnościowy, jako wydzielony, pojedynczy element stanowiący odrębną całość, którego można użyć praktycznie tak samo, jak tradycyjnego, został zbudowany już ładnych parę lat temu. Wydawać się mogło, że po tym kroku droga do całkowitej przebudowy technologicznej branży elektromechanicznej stoi otworem.
Pierwsze przymiarki implementacji technologii dotykowej do rynku przycisków pojawiły się w branży dość szybko i to na wymagającym obszarze, np. w pojazdach komunikacji miejskiej w roli przycisku do otwierania drzwi, przy sygnalizatorach świetlnych na skrzyżowaniach do włączania zielonego światła, a nawet w windach.
Konstruktorom i inwestorom chodziło niewątpliwie o zapewnienie dużej trwałości, ale szybko okazało się, że pojawiły się kłopoty. Konieczność ściągania rękawiczki zimą przed dotknięciem, brak natychmiastowego i jednoznacznego potwierdzenia zadziałania to chyba te najbardziej dotkliwe problemy i z pewnością niejedyne związane z technologią dotykową.
W praktyce przyciski pojemnościowe przeznaczone są przede wszystkim do realizacji interfejsu użytkownika. Nie nadają się do przełączania napięć zasilających, bo same wymagają zasilania, wysokich napięć ani też czułych sygnałów z sensorów. Nie da się ich używać w aplikacjach wymagających absolutnej pewności działania (tzw. aplikacje bezpieczeństwa), w warunkach silnych zaburzeń elektromagnetycznych, na przykład blisko pracujących urządzeń do zgrzewania indukcyjnego, suszarek mikrofalowych lub w sąsiedztwie działających nadajników radiowych.
W takich warunkach elementy pojemnościowe tracą czułość i mogą po prostu słabiej lub z opóźnieniem reagować na dotykający palec. Oczywiście jest to stan na dzień dzisiejszy. Technologia dotyku pojemnościowego stale jest poprawiana i być może z czasem większość jej wad zostanie w końcu całkowicie wyeliminowania. Ale droga do tego, aby trwale i całkowicie zmienić branżę elektromechaniczną, jest jeszcze bardzo daleka.
Z pewnością zjawiska charakterystyczne w największym stopniu dla rynku elektroniki konsumenckiej, w tym ekspansja ekranów dotykowych, miniaturyzacja, nowoczesne wzornictwo, które często wyklucza tradycyjną płytę czołową i podobne czynniki związane z wzornictwem sprzyjają technologiom dotykowym.
Istotne jest też widoczne cały czas ograniczanie liczby rozwiązań mechanicznych w nowoczesnej elektronice, co wiąże się z chęcią zapewnienia lepszej jakości urządzeń oraz z tego, że po prostu konstruktorzy mają obecnie alternatywne rozwiązania dla tych elementów. Z takich powodów elementy elektromechaniczne będą znikać z płyt czołowych, niemniej nie z każdej i nie błyskawicznie, czasem też wcale.
Największe oddziaływanie na rynek, pomijając elektronikę konsumencką, a więc tablety, telefony i podobne, technologia dotykowa niesie obecnie w możliwości schowania części przełączającej pod osłoną i możliwością dowolnej kompozycji płyty czołowej bez wiercenia dziur. Technologie dotykowe pojawiają się więc w dość dużym obszarze rynku oddzielającym elektronikę profesjonalną i przemysłową od całej reszty. Sprzęt AGD, komponenty automatyki domowej, automaty sprzedaży i systemy POS, sprzęt informacyjno-rozrywkowy, wydają się na razie tworzyć pewnego rodzaju niszę, gdzie systemy te mogą pokazać wiele zalet, a opisane wady nie są dokuczliwe.
Ważnym aspektem wpływającym na tempo rynkowej ekspansji ekranów dotykowych jest to, że zapewniają one konstruktorom największy stopień elastyczności projektu, dają możliwość wypływania na kształt interfejsu użytkownika w trakcie eksploatacji urządzenia poprzez wymianę oprogramowania oraz pozwalają na tworzenie indywidualnych projektów interfejsu użytkownika bez konieczności inwestowania w przygotowanie produkcji. Jest to silny argument za, nawet gdy na przeciwnej szali położy się technologię druku cyfrowego dla paneli czołowych pozwalającą wykonywać pojedyncze sztuki.
O to czy technologie dotykowe są zagrożeniem dla sektora rozwiązań, pytaliśmy w naszych ankietach, a zebrane tam opinie pokazujemy na wykresie 1. Specjaliści najczęściej byli zdania, że technologie dotykowe mają silny wpływ na rynek rozwiązań elektromechanicznych, ale jedynie w wybranych sektorach i aplikacjach. Potwierdza to nasze powyższe rozważania na ten temat.
Paweł BanaśHorizon Technologies
Klient dziś to partner wymagający, motywujący dostawcę do wytężonej i kreatywnej pracy, często świadomy wizji rozwiązania, które zamierza wprowadzić na rynek. Oczekuje on oczywiście najlepszej jakości w najniższej cenie przy możliwie najkrótszym terminie realizacji. Ale przede wszystkim zależy mu, aby produkt, nad którym właśnie pracuje, odniósł sukces rynkowy i przyczynił się do rozwoju jego firmy. Żeby taki scenariusz był możliwy, klient potrzebuje rzetelnego i fachowego wsparcia w zakresie realizacji projektu od jego początkowej fazy. Pomoc w zakresie właściwego doboru technologii, odpowiednich materiałów zapewniających prawidłową oraz bezawaryjną pracę urządzenia w określonych warunkach środowiskowych, dopasowane do aktualnych trendów rynkowych wzornictwo przemysłowe to tylko część z bardzo istotnych elementów, na których dziś skupia swoją uwagę klient. Reasumując, można zatem powiedzieć, że klient oczekuje przede wszystkim szeroko rozumianego wsparcia i zrozumienia jego potrzeb przez dostawcę, a jakość, cena oraz termin realizacji muszą iść w parze z profesjonalnie przygotowanym i prowadzonym projektem wdrożeniowym.
W przypadku produkcji urządzeń elektronicznych na lokalnym rynku, trudno jest mówić w tej chwili o ofensywie ekranów dotykowych. Faktycznie zauważalny jest wzrost zainteresowania rozwiązaniami dotykowymi ze strony klientów. Zdecydowanie jednak sytuacji tej nie należy postrzegać, a raczej my jej nie postrzegamy jako zagrożenia dla pozycji klawiatur membranowych. Pozycja klawiatur membranowych jest nadal bardzo mocna, a nasz lokalny rynek charakteryzuje się dużym potencjałem wzrostu. Przewrotnie rzecz ujmując, rozwiązania oparte na ekranach dotykowych to szansa na jeszcze bardziej komplementarną ofertę dla klienta. Dzięki dostępowi do nowych technologii jesteśmy w stanie zaoferować więcej alternatywnych sposobów zmierzających do realizacji celów biznesowych naszych klientów. Wielu z nich nadal będzie wykorzystywało w swoich urządzeniach standardowe klawiatury membranowe, kolejni zaczną wdrażać urządzenia oparte na panelu dotykowym, który zapewni im dodatkowe funkcjonalności, trudne do zrealizowania za pomocą klawiatury membranowej. Znajdą się jeszcze tacy klienci, dla których wdrożymy rozwiązanie, które łączy ze sobą panel dotykowy z klawiaturą membranową. |
Producenci przełączników bronią się jakością i wzornictwem
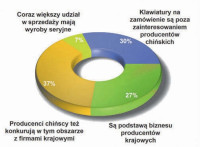
Rys. 4. Ocena, jakie znaczenie na rynku klawiatur ma produkcja na zamówienie i w jakim stopniu jest ona odporna na konkurencję azjatycką
W ostatniej dekadzie trwałość tradycyjnych przełączników i przycisków znacznie się poprawiła. Oczywiście nie tych najtańszych, które są robione byle jak i z kiepskich materiałów, ale wyroby markowe zwykle mają żywotność niebędącą problemem w większości ich zastosowań. Producenci udoskonalili technologię, poprawili precyzję działania tych elementów i sięgnęli po nowe lepsze materiały, aby zdjąć z elementów elektromechanicznych piętno najsłabszego ogniwa.
Wystarczy przejrzeć pobieżnie karty katalogowe renomowanych producentów, aby dojść do wniosku, że to nie jest już problem spędzający sen z powiek. Ponieważ w wielu aplikacjach przełączniki i przyciski pracują z niskimi napięciami i prądami, coraz częściej w kartach katalogowych rozgranicza się wytrzymałość mechaniczną od elektrycznej, co pozwala lepiej dobrać konkretny element do aplikacji.
Producenci starają się też ograniczać liczbę wytwarzanych wersji i wykonań za pomocą systemów modułowych, gdzie w ramach jednego rdzenia i pola przełączającego można zmieniać fronty, kształty klawiszów, podświetlenie, kolor, a także spinać kilka oddzielnych przycisków w bloki. To samo dotyczy zgodności akcesoriów, które zwykle są wspólne dla wielu różnych elementów.
Wytwórcy przełączników przemysłowych i rozwiązań przeznaczonych do pracy w trudnych warunkach otoczenia, a więc obszarach ściśle profesjonalnych jak przemysł, wojsko, transport, telekomunikacja, są praktycznie wolni od oddziaływania ze strony technologii dotykowych. Największy wpływ notują z pewnością producenci koncentrujący się na obsłudze aplikacji półprofesjonalnych (sprzęt audio, AGD) lub też na aplikacjach, gdzie liczy się wygląd i dobre parametry, jak chociażby medycyna. Wytwórcy ci stawiają dzisiaj na modułowość konstrukcji, pozwalającą na kompozycję elementów przełączających dobrze dopasowanych do aplikacji, na ciekawe wzornictwo oraz wprowadzają także własne projekty przycisków dotykowych.
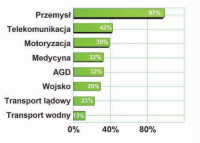
Rys. 5. W rankingu najważniejszych odbiorców dla sektora przełączników i klawiatur zdecydowanie dominuje przemysł
Producenci klawiatur mocno inwestują w technologię: nowe trwałe materiały, zapewniające odporność środowiskową i długotrwałe działanie, wykorzystują druk cyfrowy po to, aby dać możliwość pełnej indywidualizacji projektów i łączą w ramach jednej oferty wiele technologii przełączających, podświetleń i całego know-how, aby mieć ofertę dla każdego klienta.
W ich przypadku zagrożenie dotykiem jest też szansą na rozwój biznesu - producenci klawiatur mają technologię i potencjał do tego, aby stać się integratorami technologii dotykowych. Same sensory to przecież nie wszystko, potrzebne są płyty frontowe, okna dla wyświetlaczy, uszczelnienia, osłony itd. Początki takiego procesu już są widoczne - Qwerty zaczęła współpracować z Unisystemem w zakresie produkcji i integracji paneli dotykowych do urządzeń elektronicznych z wyświetlaczami.
Marcin RzechonekIrga
Obserwujemy w firmie wzrost zainteresowania konstrukcjami klawiatur z podświetlanymi klawiszami. Olbrzymi postęp w technologii LED i spadek cen elementów pozwalają na dużą elastyczność w projektowaniu. Konstrukcje takie zaczynają być atrakcyjne nawet dla klientów z branż tradycyjnie przywiązanych do rozwiązań opartych na typowych przyciskach pulpitowych.
Jak w każdym przypadku kluczowe jest znalezienie kompromisu między wymaganiami technicznymi a ekonomicznymi. Technologia membranowa pozwala na produkcję klawiatur zarówno bardzo tanich, o ograniczonej żywotności, jak również konstrukcji bardzo trwałych i odpornych. Istotne jest określenie środowiska, w jakim klawiatura ma działać i kto ma jej używać, w zależności od odpowiedzi na te pytania nasza firma jest w stanie doradzić rozwiązanie najbliższe oczekiwaniom klienta. Możliwości wykonania grafiki frontowej również są bardzo szerokie - jest to olbrzymia zaleta wyróżniająca tę technologię na rynku, ale komplikująca decyzję klienta: czy wybrać wersję ekonomiczną, czy droższą w produkcji, ale bardzo efektowną wizualnie. O ile nasi projektanci mogą pomóc w opracowaniu designu, o tyle wybór jego stylu i odpowiedź, co jest optymalne marketingowo, zawsze jest po stronie klienta.
Wydawać by się mogło, że te technologie zawojują świat wszelkiego typu sterowników - jest taki trend w segmencie HMI. Technologie dotykowe wciąż jednak mają wady ograniczające ich przydatność w przemyśle. Są nimi niska wytrzymałość mechaniczna dla technologii rezystancyjnej, wciąż niewystarczająca niezawodność, wrażliwość na zakłócenia oraz konieczność obsługi gołymi palcami w technologii pojemnościowej albo z kolei wysokie koszty dla ekranów z falą powierzchniową. Tam gdzie pewność zadziałania ma kluczowe znaczenie, a więc w sterownikach przemysłowych, aparaturze medycznej itp., pozycja klawiatur membranowych wydaje się na razie niezagrożona. Podobnie we wspomnianym segmencie paneli HMI obserwujemy raczej integrację klawiatur z panelami dotykowymi niż ich wypieranie. |
Czynników sprzyjających rozwojowi rynku jest wiele
W dużej mierze czynnikiem napędowym dla rynku elementów elektromechanicznych we wszystkich sektorach produktowych jest ogólny rozwój rynku elektroniki, automatyki i wzrost liczby rozwiązań opartych na urządzeniach elektrycznych i elektronicznych. W każdym z takich miejsc, gdzieś pojawia się przełącznik, nierzadko jest ich wiele.
Ogólny rozwój rynku napędzają także inwestycje, modernizacje starych linii produkcyjnych, urządzeń infrastruktury, obowiązki prawne związane z zapewnieniem bezpieczeństwa użytkowania oraz rozwój usług montażu kontraktowego. Trwa dobra koniunktura na rynku profesjonalnym: wojskowym, kolejowym, komunikacji bezprzewodowej, co zawsze przekłada się w pewnym stopniu na sprzedaż.
Z przełączników nie rezygnuje się bez powodu ani też nie szuka na siłę zastępczych technologii, bo z każdą kolejną generacją poprawiają się ich parametry: trwałość mechaniczna i elektryczna, a następnie odporność środowiskowa. Poprawia się wzornictwo, rośnie liczba dostępnych wykonań, kolorystyki i opcji oraz akcesoriów. Innymi słowy, producenci pracują nad tym, aby kwestia wyboru od strony technicznej (mechaniczny czy elektroniczny) oraz jakościowej była jak najbardziej neutralna.